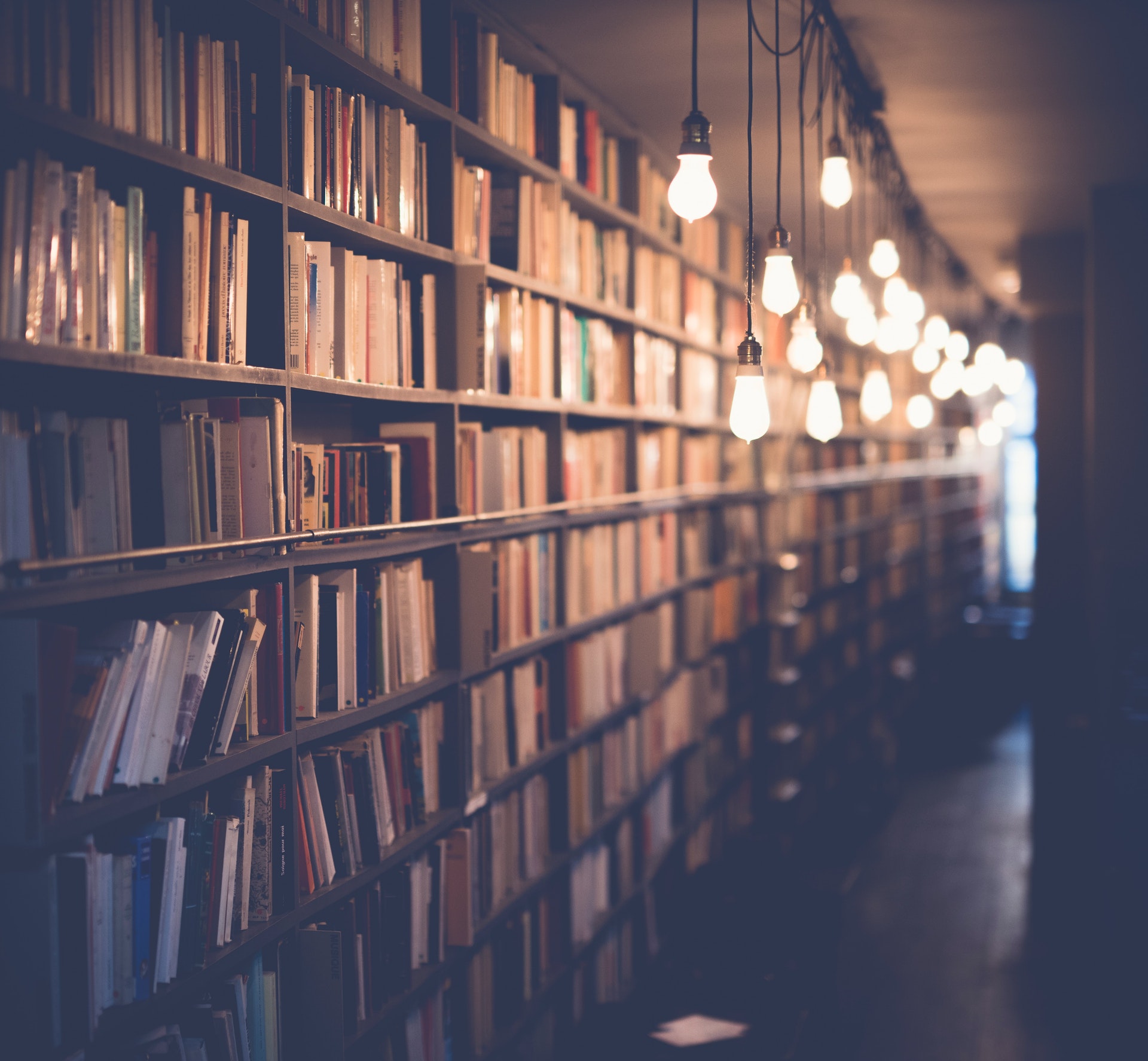
Moog parts are made in a variety of places around the world. In the United States, Moog has manufacturing facilities in New York, Pennsylvania, Ohio, Colorado, and California. Additionally, Moog has facilities in Mexico, Canada, Italy, China, and the United Kingdom. Moog also has a network of authorized distributors and service providers located in over 60 countries.
If this caught your attention, see: Can You Use Bleach on Your Areola?
Where are Moog parts manufactured?
Moog parts are manufactured in a number of places, but the majority of production takes place in the United States. The company has factories in North Carolina, Ohio, and Pennsylvania. Production in China is also a significant part of Moog's operations. The company has two factories there, one in Shanghai and one in Shenzhen. In total, Moog employs over 14,000 people in more than 30 countries.
Despite its global reach, Moog remains headquartered in the town of Elma, New York, where the company was founded in 1951. The company's founder, Robert Moog, developed the first commercial synthesizer in the 1960s. Moog's synthesizers were used by a number of influential musicians, including the Beatles, the Beach Boys, and Kraftwerk. Today, Moog continues to manufacture a variety of electronic musical instruments, as well as parts for a range of other industries, including aerospace and defense.
So where are Moog parts manufactured? The vast majority of production takes place in the United States, but the company also has a significant presence in China. In total, Moog employs over 14,000 people in more than 30 countries around the world.
Expand your knowledge: Watch Atlanta United
How are Moog parts manufactured?
How are Moog parts manufactured?
In Moog's state-of-the-art manufacturing facility, advanced computer-controlled machines quickly and accurately create parts that meet or exceed the company's stringent quality standards.
After a customer order is received, it is reviewed by Moog's engineering team to determine the best way to produce the required parts. The team then creates a manufacturing plan that details the specific processes and sequence of operations that will be used.
Once the manufacturing plan is finalized, the required raw materials and components are sourced from Moog's global supplier network. The parts are then delivered to Moog's manufacturing facility, where they are stored in a controlled environment until they are needed.
When it is time to produce the parts, they are machined to the precise specifications detailed in the engineering drawings. A variety of advanced machining technologies are used, including computer-controlled milling, turning, and grinding.
After the parts are machined, they undergo a rigorous inspection process to ensure that they meet Moog's high standards for quality and performance. Once they have passed inspection, the parts are packaged and shipped to the customer.
The entire process, from customer order to delivery, is managed by Moog's ERP system, which ensures that every part is produced quickly, accurately, and to the highest quality standards.
Check this out: Local Courier Facility
What materials are used to manufacture Moog parts?
Moog Inc. is a designer and manufacturer of motion control products, systems and services. The company operates in four segments: aircraft actuation, space and defense, industrial equipment and aftermarket services. Moog’s products include hydraulic and electric motion control actuators, motion control components, motion control systems, aircraft flight control systems and aftermarket services.
Moog was founded in 1951 by Bill Moog. The company started as a manufacturer of servo valves. In the 1960s, Moog expanded its product line to include control systems for the space program. In the 1970s, the company introduced products for the industrial market. In the 1980s, Moog expanded into the aircraft actuation market. In 2001, the company acquired the aerospace division of Clevite Corporation.
Moog’s products are manufactured at facilities in the United States, China, Germany, Canada and the United Kingdom. The company’s products are used in a variety of applications, including aerospace, defense, industrial, medical and commercial.
Aircraft Actuation
Moog’s aircraft actuation products include hydraulic and electric actuators, control cables and related components. Moog’s products are used on commercial, military, business and general aviation aircraft. Products in this segment are designed to meet the requirements of the major aircraft manufacturers.
Space and Defense
Moog’s space and defense products include satellite control systems, optical payloads, aircraft control systems and related components. Moog’s products are used on commercial, military and scientific spacecraft.
Industrial Equipment
Moog’s industrial equipment products includeservo valves, motion controllers, rotary actuators, linear actuators, gears, motors and motor controllers. Moog’s products are used in a variety of industries, including oil and gas, machine tools, medical equipment, printing presses and semiconductor manufacturing.
Aftermarket Services
Moog’s aftermarket services includerepair and overhaul, field services, technical support and spare parts.
Consider reading: Pronounce Including
What is the process of manufacturing Moog parts?
In 1955, Robert Moog created the first Moog synthesizer, which would go on to change the face of music forever. Since then, the Moog company has been responsible for some of the most iconic synthesizers and electronic instruments in the world. From the early days of the Moog synthesizer to the present day, the company has always been at the forefront of innovation, pushing the boundaries of what is possible with sound.
The Moog company is based in Asheville, North Carolina, where all of its products are designed and manufactured. The Moog factory is a state-of-the-art facility that uses the latest technology to produce the highest quality instruments. Every Moog product is handmade by a team of skilled craftspeople who take pride in their work.
The manufacturing process for Moog instruments begins with the design phase. The Moog team works closely with artists and musicians to create products that meet their specific needs. Once the design is complete, the team moves on to the prototyping phase. In this phase, the design is translated into a working prototype that can be tested and refined.
After the prototyping phase is complete, the production phase begins. In this phase, the Moog team uses the latest manufacturing technologies to produce the final product. Every Moog instrument undergoes a rigorous quality control process to ensure that it meets the company's high standards.
The Moog company takes great pride in its products and the people who make them. The company is constantly striving to improve its manufacturing process to ensure that its products are the best they can be. Moog is a true pioneer in the world of sound, and its commitment to innovation is evident in everything it does.
A unique perspective: Which Phase of Mitosis Is Shown in the Diagram?
What are the quality control measures in place for Moog parts?
The Moog company has been in business since 1954, and has been providing quality parts for a variety of industries ever since. They design and manufacture parts for everything from spacecraft to automobiles, and are always working to improve the quality of their products. The Moog company is committed to providing their customers with the best possible products, and they have a number of quality control measures in place to ensure that their parts meet or exceed customer expectations.
One of the ways that Moog ensures quality control is by testing their products before they are sent out to customers. Moog has a state-of-the-art testing facility where they can test parts under a variety of conditions to make sure that they will perform as expected. Moog also has a strict quality control process in place for their manufacturing process. They have a team of quality control inspectors who monitor every step of the manufacturing process to ensure that each part meets their high standards.
In addition to their internal quality control measures, Moog also participates in external quality assurance programs. These programs provide independent testing of Moog products to ensure that they meet the highest standards of quality. Moog is also ISO 9001 certified, which is an internationally recognized standard for quality management systems.
The Moog company takes quality control seriously, and has a number of measures in place to ensure that their parts meet or exceed customer expectations. Their commitment to quality control helps to ensure that their products are of the highest possible quality, and that their customers are satisfied with their purchase.
Intriguing read: Customers Find
How are Moog parts tested for quality?
The answer to this question depends on the particular Moog part in question. In general, Moog parts are subjected to a series of tests meant to assess their quality and performance. These tests may be conducted internally by Moog employees, or they may be outsourced to third-party testing laboratories.
The specific tests that a Moog part undergoes will depend on its intended purpose and desired level of performance. For example, a Moog part designed for use in an aircraft engine will need to undergo significantly more strenuous testing than a Moog part designed for use in a child's toy. In general, however, all Moog parts are put through a series of tests meant to assess their durability, strength, and accuracy.
One of the most important tests that Moog parts undergo is the vibration test. This test is designed to assess a Moog part's ability to withstand the rigors of vibration and shock. Vibration testing is conducted using a specialized piece of equipment known as a shaker table. A Moog part is attached to the shaker table and then subjected to a variety of different vibration profiles. These profiles help to simulate the types of vibration and shock that the Moog part might experience in the real world.
After the vibration test, Moog parts are typically assessed for their dimensional accuracy. This is done using a variety of different measuring tools, such as calipers and micrometers. The measurements taken during this testing help to ensure that the Moog part will fit correctly into its intended application.
In addition to the above tests, Moog parts may also undergo a variety of other tests, such as thermal testing, salt spray testing, and leak testing. The specific tests that a Moog part undergoes will depend on its end use. Moog parts are designed to meet the specific needs of their intended applications, and as such, the testing that they undergo is designed to ensure that they will perform as intended.
Here's an interesting read: What Starts with S and Ends with X?
What is the warranty on Moog parts?
The Moog company offers a limited warranty on all of its parts. The warranty period is one year from the date of purchase. This warranty covers defects in materials and workmanship. It does not cover damage caused by normal wear and tear, accidents, or use of the product in a way that it was not intended. If a Moog product fails during the warranty period, the company will repair or replace it at no cost to the customer. Moog also offers a satisfaction guarantee. If a customer is not satisfied with a Moog product, they can return it within 30 days for a full refund.
Related reading: What Are the Best Places to Elope in California?
How often do Moog parts need to be replaced?
Just like any other type of electronic equipment, Moog parts will eventually need to be replaced. However, Moog parts are built to last and can typically handle a lot of wear and tear before they need to be replaced. With proper care and maintenance, your Moog parts should last for several years before needing to be replaced.
If you use your Moog equipment regularly, you may need to replace parts more often than if you only use it occasionally. Parts that see a lot of use, such as faders and switches, may need to be replaced sooner than other parts. If you use your Moog equipment in a studio environment, it is important to keep an eye on all of the parts and perform regular maintenance to ensure that everything is in working order.
If you take care of your Moog equipment and regularly replace worn parts, you will be able to enjoy it for many years to come.
Broaden your view: Dermatologist Regularly
What are the most common problems with Moog parts?
The most common problems with Moog parts are typically related to the quality of the parts themselves. There have been reports of parts breaking down or malfunctioning after only a short period of use, which can be frustrating for customers. There have also been issues with customer service, with some customers reporting that it is difficult to get in touch with someone from the company when they have a problem. Overall, the most common problems with Moog parts seem to be related to the quality of the parts and the customer service.
Suggestion: What Is Friction?
Frequently Asked Questions
Does Moog make hydraulic systems?
Yes, Moog's hydraulic systems can be used for both manual and electronic control modes. Our systems are designed for a variety of applications, including: transportation, mining, industrial processes, and specialty applications.
What are some applications of Moog products?
One example of an application for Moog products is in the automotive industry. Moog's steering and propulsion controls are used on many different types of vehicles, from small cars to large trucks. Moog also manufactures actuators and valves for use in automotive applications, including hydraulic systems, traction control, emergency braking and more.
Are Moog parts better than OEM?
There is no definitive answer. Sometimes, Moog parts may be better quality than OEM parts, but other times it may not be the case. Ultimately, it comes down to personal preference and what kind of experience you are looking for with your car or bike.
Why choose Moog?
There are a lot of great options when it comes to choosing a parts supplier, so it’s important to do your homework. Moog is a well-respected organization that has been providing problem-solving parts and materials to the automotive industry for decades. Plus, their technical support is top-notch – you can be sure that if you need help with your installation or use of their products, they’ll be there to help you.
What are the different types of manufacturing processes?
There are many types of manufacturing processes but they can be broadly divide them into four parts. Casting process is one of the liquid state manufacturing process. In casting process we put molten metal into a die of desired shape and obtain our product when the metal become solid.
Sources
- https://www.moogparts.com/parts/driveline/universal-joints.html
- https://www.amazon.com/Moog-ES3493T-Tie-Rod-End/dp/B000C59WHA
- https://www.amazon.com/Moog-369-Universal-Joint/dp/B009HQJCYS
- https://www.moog-suspension-parts.com/universal-joints-ujoints.asp
- https://www.google.com/doodles/robert-moogs-78th-birthday
- https://www.amazon.com/MOOG-513179-Wheel-Bearing-Assembly/dp/B000BZJVA4
- https://www.moogparts.eu/
- https://www.ebay.ca/b/Car-Truck-Parts-Accessories/6030/bn_562630
- https://www.suspension.com/blog/where-are-moog-parts-made/
- https://www.fcpeuro.com/Mercedes~Benz-parts/
- https://www.moogparts.com/parts.html
- https://www.carparts.com/wheel-hub
- https://www.carid.com/suspension-parts.html
- https://www.moog.com/
- https://www.suspension.com/blog/how-to-grease-ball-joints/
Featured Images: pexels.com