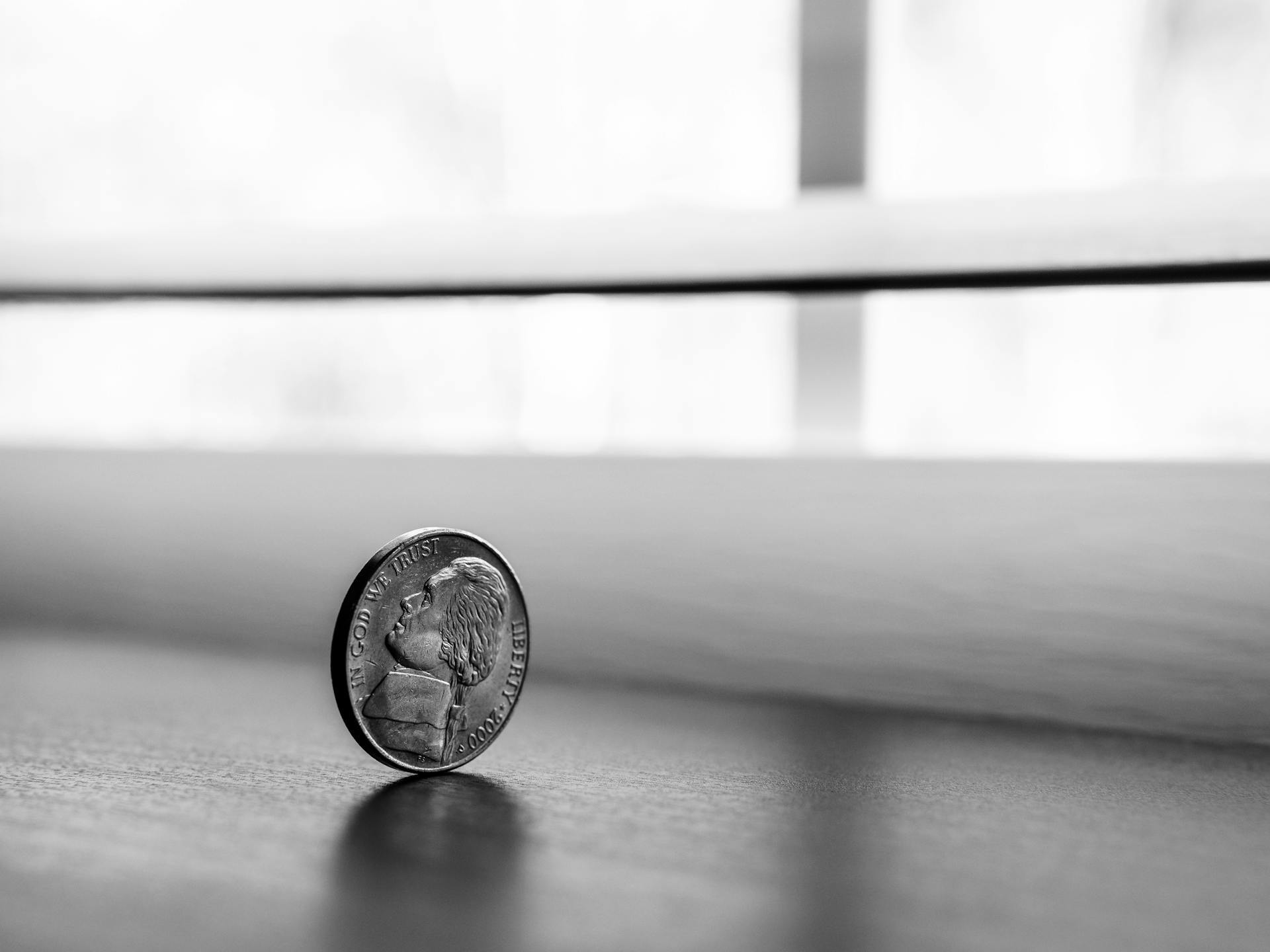
The art of minting coins has come a long way from its ancient roots. In the early days, coins were made by hand, with skilled craftsmen hammering and shaping metal into various forms.
The first coins were minted around 700 BCE in ancient Lydia, with the famous Lydian lion coins being a notable example. These early coins were made from electrum, a naturally occurring alloy of gold and silver.
One of the most significant advancements in minting coins was the introduction of the screw press in the 13th century. This innovation allowed for mass production of coins, making them more accessible to the general population.
The Industrial Revolution brought about even more significant changes, with the development of mechanized minting machines in the 19th century.
You might enjoy: Minting Coins Meaning
History of Money
Coins were first minted over 2,000 years ago in the ancient kingdom of Lydia, modern-day Turkey. The ancient coins were minted by hand through striking blank pieces of metal using hammers.
Check this out: What Is a Minted Coin
The first mint was likely established in Lydia in the 7th century BC, for coining gold, silver, and electrum. This marks the beginning of coin minting.
Medieval coin minting improved on the ancient methods by using pre-formed round discs of metal and a screw press. This process produced more consistent quality coins.
Aegina, an island in Europe, produced the first coins minted on European soil, dating back to the 7th century BC. These early coins featured an electron stater bearing the image of a turtle.
The manufacture of coins in the Roman Republic, dating from about the 4th century BCE, significantly influenced the later development of coin minting in Europe. This had a lasting impact on the way coins were made.
The origin of the word "mint" is ascribed to the manufacture of silver coin at the temple of Juno Moneta in 269 BCE Rome. This temple became a place of great importance for money and its production.
Modern coins are minted with hydraulic coining machines that mechanically load blanks inside them, stamping 100 to 300 tons of coins within a short time. This substantial minting capacity is crucial for large minting houses like the U.S. Mint.
Coin Production
Coin production is a complex process that involves several stages, starting from the creation of a plaster model of the coin. The plaster model is then coated with rubber to create a mold, which is used to make an epoxy galvano.
The process of making dies is crucial in coin production. A master hub is created by reducing the image from the plaster model onto a steel master hub, which is then heat-treated to make it hard. This master hub is used to make a limited number of master dies via hubbing.
The working dies, which are used to strike coins, are created by pressing the master hub into a steel blank to impress the image into the die. The working dies are then put through the same process to form the actual dies that will strike coins. To prolong the life of the hubs and dies, a lower amount of pressure is used in the hubbing press, and the die is subjected to an annealing procedure to soften the steel.
The minting process starts with the mining of metals used for minting coins, including iron, gold, silver, nickel, and copper. These metals are mined as ore before being refined to remove impurities.
Recommended read: Mining Hub Pool
Reduction Dies
The coin design is inputted into steel using a coin engraving machine that employs specialist software applications, creating a reduction punch, also known as a reduction die, which contains the complete coin design.
This process finishes the coin delineations and fillet work, and the reduction die is then loaded onto the hydraulic press.
Between 100 tons and 400 tons of pressure is applied to transform the design into softened steel, a process known as hobbing, resulting in a master die with a negative impression of the coin design.
The reduction die is hardened through a series of pressing steps, where a copy of the coin image is shifted from the hardened steel to the mild steel through pressing.
A pair of minting dies can reproduce up to one million coins before they need to be replaced.
Mining and Recycling
The process of mining and recycling is a crucial step in coin production.
Metals used for minting coins include iron, gold, silver, nickel, and copper.
These metals are mined as ore before being refined to remove impurities.
Recycling old coins is another avenue to obtain raw materials.
Old coins may have been removed from circulation but once recycled, they are renewed and thrown back into circulation.
Consider reading: Coins in Uk Circulation
Modern Coin Production Methods
Modern coin production methods have undergone significant changes over the years, with the introduction of steam engines in the 1770s being a major turning point. This efficient power source allowed for the adoption of new technologies in the coin minting process.
The use of pantographs enabled the minting of standardized designs for every coin denomination, making it possible to manufacture and replicate coins identically to different scales. This was made possible by creating a plaster model of the proposed design, which was then used to make a mold, and an electrolyte copy was obtained in nickel and copper.
Die production involves a complex process of creating a master punch, which is used to punch in a matrix, raising a working punch used to sink a working die. The surface of the working die is then polished extremely hard before it is sunk.
The production of blanks is automated, and blanking presses are high speed, making the process more efficient. This is particularly evident in the use of a reducing machine, which takes several days to reduce the image onto a steel master hub.
Readers also liked: What Are Cryptocurrencies Used for
Modern
Modern coin production methods have come a long way, thanks to innovations like the steam engine.
The invention of the steam engine in the 1770s by Matthew Boulton and James Watt provided an efficient power source that was quickly adopted into the coin minting process.
New types of steel were produced that could handle much greater stresses, making it possible to manufacture coins with precision.
The pantograph allowed for the minting of standardized designs for every coin denomination, making mass production more efficient.
Coins could be manufactured and replicated identically to different scales, reducing errors and increasing consistency.
Die production uses a plaster model of the proposed design to create a mold, which is then used to obtain an electrolyte copy in nickel and copper.
The copy is mounted on the pantograph, which allows for the cutting of the design to a specific coin size in a block of steel called the master punch.
A fresh viewpoint: United States Mint Coin Production
The master punch is used to punch in a matrix, which raises a working punch used to sink a working die.
The surface of the working die is polished extremely hard before it is sunk, ensuring a high level of precision.
Blank production is also automated, with high-speed blanking presses that can produce coins quickly and efficiently.
Here's an interesting read: Whats Bitcoins All Time High
Production Methods
Modern coin production involves a range of techniques, from traditional methods to more modern and efficient processes.
The invention of steam engines in the 1770s brought about an efficient power source that was hastily adopted into the coin minting process. This led to the development of new types of steel that could handle much greater stresses, making it possible to produce coins with standardized designs.
In the modern process, a plaster model of the proposed design is used to create a mold, which is then used to produce a nickel and copper copy. This copy is mounted on a pantograph, which allows the cutting of the design to a specific coin size in a block of steel called the master punch.
Related reading: What Is Ethereum Used for
The master punch is used to punch in a matrix, which raises a working punch used to sink a working die. The surface of the working die is polished extremely hard before it is sunk. This process is a significant improvement over traditional methods, which involved hand-hammering and other labor-intensive techniques.
Die production involves several stages, including the creation of a plaster model, a rubber mold, and an epoxy galvano. This process can take several days to complete, and requires a high degree of precision to produce accurate and detailed designs.
The master die is then used to form as many working hubs as needed, which are then used to produce the working dies. These working dies are the actual dies that will strike the coins. The process of transferring the hub to the die can be repeated as many times as necessary to form the number of dies needed to make the number of coins required.
Using a lower amount of pressure in the hubbing press can prolong the life of the hubs and dies used. However, this requires the die being made to be subjected to an annealing procedure to soften the steel, making it easier to force the hub's image into the die.
Here's an overview of the production process:
- Plaster model creation
- Rubber mold creation
- Epoxy galvano production
- Reducing machine use
- Master die creation
- Working hub creation
- Working die creation
This process is a significant improvement over traditional methods, which involved hand-hammering and other labor-intensive techniques.
For your interest: Bitcoin Atm Milwaukee - Coinhub
Ancient and Medieval Coin Production
Ancient coin dies were manufactured individually by hand by artisans known as engravers. They were used even when worn or cracked, and the die on the hammer side tended to wear out first. The planchets were usually hot prior to striking.
In ancient times, a lower die could last for up to 10,000 strikes, depending on the level of wear deemed acceptable. Upper dies had a far greater range of lives, with usable lives ranging from just over 100 strikes to nearly 8,000 being reported. Ancient coin producers could get as many as 47,000 strikes out of an individual die.
Medieval coin dies were largely made of iron, and some had a small region at the face made of steel. The Venetian mint made an average of 20,000 coins per day, using dies that lasted around 17,000 to 36,000 strikes.
Explore further: How Are Cryptocurrencies Made
Ancient Dies
Ancient coin dies were manufactured individually by hand by artisans known as engravers. They were a crucial part of the coin production process.
Prior to the modern era, dies were made to last, with a lower die expected to last for up to 10,000 strikes depending on the level of wear deemed acceptable. This is a remarkable feat considering the technology available at the time.
Upper dies, on the other hand, had a far greater range of lives, with usable lives ranging from just over 100 strikes to nearly 8,000 being reported. This suggests that the quality of the die material and the striking process played a significant role in determining its lifespan.
In some cases, ancient coin producers were able to get as many as 47,000 strikes out of an individual die, a testament to the skill and craftsmanship of the engravers.
Medieval Dies
Medieval dies were made of iron, with some being made of steel for a small region at the face of the die.
The technique used to create medieval coin dies changed over time, with early medieval coinage dominated by dies created from punches that displaced metal instead of removing it.
Medieval die cutters used engraving tools to lay out designs and create detailed punches, but engraving on the face of the die didn't become common until the early Renaissance.
The Venetian mint had very detailed records of their die usage, showing that "hammer" dies lasted around 17,000 strikes, while "anvil" dies lasted 36,000 strikes.
The Venetian mint made an average of 20,000 coins per day, which meant they needed to create one "hammer" die a day and one "anvil" die every other day.
Suggestion: Create an Erc20 Token
The Third Side
The edge of a coin is often overlooked, but it can be just as interesting as the front and back.
Reeds, similar to knurling, are found on the edges of US coins like the dime, quarter, and half dollar, as well as many world coins.
These designs can be simple, like vines, or more complex, like bar patterns.
Some coins have phrases, like the United States dollar coin, which features the date, mintmark, and motto, E Pluribus Unum.
Explore further: Aus Dollar Coin
A special die called a collar die is used to impart these designs into the coin, and it's separated to allow the coin to be removed.
Broadstrikes occur when the collar is missing, resulting in a coin that's flatter and bigger around than usual.
The US Mint used an edge incusing machine to letter the edges of business strike presidential dollars, while using a collar for the proof versions of these coins.
Notable Mints
The Austrian Mint is one of the oldest mints in the world, established in 1397 and producing the iconic Vienna Philharmonic gold bullion.
Some other notable mints include the Barcelona Mint, which has a history dating back to 1067, and the Casa da Moeda do Brasil, which is one of the oldest mints in the Americas.
The Casa da Moeda de Portugal is another notable mint, and it's interesting to note that some of these mints have been producing coins for centuries.
Here's a list of some of the notable mints mentioned earlier:
- Austrian Mint
- Barcelona Mint
- Bundesdruckerei (Germany)
- Casa da Moeda do Brasil
- Casa da Moeda de Portugal
- Finland Mint
- Japan Mint
- Monnaie de Paris (France)
- Royal Canadian Mint
- Royal Dutch Mint
- Royal Mint (United Kingdom)
- Swissmint, Switzerland
The Royal Mint
The Royal Mint is a government-owned mint founded in AD 886.
It's a massive operation, producing 2-billion-pound sterling coins for circulation every year. That's a staggering number, and it's a testament to the mint's efficiency and expertise.
The Royal Mint mints coins for the United Kingdom, and it's also a leading export mint, producing coins for more than 60 countries around the world.
See what others are reading: Bitcoin Atm Tampa - Coinhub
Notable Mints
The Royal Canadian Mint is one of the most well-known mints in the world, but it's not the only notable one. The Austrian Mint, established in 1397, is a historic mint that produces the Vienna Philharmonic gold bullion. This mint has been around for over 600 years, making it one of the oldest in the world.
The Casa da Moeda do Brasil, established in 1536, is another notable mint that has been producing coins for centuries. It's also one of the oldest mints in the Americas, along with the Casa de Moneda de México, which was established in 1535.
Recommended read: Coin Mints Us
The United States Mint is a well-known mint that has been producing coins for over two centuries. It's responsible for producing coins such as the American Eagle and the American Buffalo. The Philadelphia Mint is one of the most famous mints in the United States, and it's been producing coins since 1792.
The Royal Australian Mint, the Royal Canadian Mint, and the Royal Dutch Mint are all notable mints that are known for producing high-quality coins. The Perth Mint in Australia is also a notable mint that produces gold and silver coins.
Here's a list of some of the most notable mints in the world:
- Austrian Mint (established in 1397)
- Casa da Moeda do Brasil (established in 1536)
- Casa de Moneda de México (established in 1535)
- United States Mint
- Philadelphia Mint
- Royal Australian Mint
- Royal Canadian Mint
- Royal Dutch Mint
- Perth Mint
The Monnaie de Paris in France is another notable mint that has been producing coins for centuries. The Monnaie de Navarre, established in 1351, is also a historic mint that's worth mentioning.
Represented in Other
The Austrian 700 Years City of Hall in Tyrol coin is a great example of a coin die being represented in another coin. The reverse side of this coin shows the Guldiner silver coin in a negative design, referencing Hall's history as a significant centre for minting coins.
This design choice is a nod to the city's rich minting history, which dates back centuries. The Guldiner silver coin is a significant part of that history, and its inclusion on the Austrian coin is a testament to the city's enduring legacy.
The Austrian coin is a notable example of how a coin die can be used as a design element in another coin.
Curious to learn more? Check out: Cryptocurrency History
Coin Production Process
The coin production process is a fascinating journey that transforms raw metal into a small work of art. The process begins with creating dies, which are essentially metal stamps that carry the image of the coin.
An artist carves two dies, the obverse and reverse, from a harder metal that can withstand the constant punching. The dies are then placed in an anvil and a punch die, respectively, to strike the coin.
The metal, usually silver, gold, or an alloy, is heated to a melting temperature and poured into a mold with circular indentations. The metal cools into small, circular, smooth pieces called flan or blanks.
The blanks are then weighed to ensure standardization and are ready to be struck. A blank is placed on the anvil die and the punch die is struck with a heavy mallet, resulting in a stamped coin.
The coining process depends on the type of coin being minted, with circulation coins being struck concurrently on both sides by dies, collector coins having automatic feeds and softly glazed images, and investment coins being manufactured using a single stamp method.
The process of creating dies can be repeated multiple times to form the number of dies needed to make the number of coins required. However, if the die is not lined up exactly with the hub, the result is a secondary image, or doubling, known as die doubling.
Design
The design of a coin is a crucial step in the production process. The design must be approved by the authorities before it is adopted.
In the U.S., the Secretary of the Treasury approves the coin design. This is a critical step to ensure the design meets the required standards.
A three-dimensional model is created using 3D modeling software and/or plaster modeling. This process allows for a detailed and precise design.
A milling model is used to create a synthetic model of the coin. This model is used to test and refine the design.
The diameter of the coin can range from 10 cm to 30 cm. This allows for a wide range of design possibilities.
The design process can take many months to ensure the coin has the highest quality design.
Coing
The coining process is a crucial step in making coins, and it depends on the type of coin being minted.
Circulation coins, used for everyday transactions, are made by loading blanks through a press where they're struck on both sides by dies, resulting in a sharper rim. This process spreads and stretches metal particles.
Collector coins, on the other hand, are specially minted for collectors and often have softly glazed detailed images.
Investment coins, made with precious metals, are manufactured using a single stamp method and usually have a heavy or light frost or a brilliant polish.
Melting and Blending
In the coin production process, melting and blending play a crucial role in creating alloys.
The U.S. Mint makes quarters and dimes with a unique alloy composition.
The outer layer of these coins is made up of 75% copper and 25% nickel, a blend of two metals.
The U.S. one-cent coin is made from a different material, with a copper-plated zinc core.
Intriguing read: Value of Copper Coins
The Process
The process of creating a coin involves several steps, each with its own unique challenges and requirements. The first step is to decide on the design and images to be featured on the coin, which is typically done by an issuer or a higher-ranking individual.
The artist then carves two dies, one for the obverse (front) side and one for the reverse (back) side of the coin. These dies are made from a harder metal that can withstand the constant punching it will endure.
The metal used for the coin is heated to a melting temperature and poured into a mold with circular indentations, creating small, circular pieces called flan or blanks. The blanks are then weighed to ensure standardization.
The blanks are then placed on the anvil die and struck with a heavy mallet, resulting in a stamped coin ready for circulation.
The coining process can vary depending on the type of coin being minted. For circulation coins, the blanks are loaded through a press and struck concurrently on both sides by dies, resulting in a sharper rim.
Collector coins, on the other hand, are minted using a press with an automatic feed and often have softly glazed detailed images. Investment coins are made with precious metals and are manufactured using a single stamp method.
The production of coins involves several steps, including creating a plaster model, coating it with rubber, and using it to make an epoxy galvano. This process is repeated several times to create the master die.
The master die is then used to form working hubs, which are used to create working dies. The working dies are the actual dies that will strike the coins.
A key factor in producing high-quality coins is the use of a lower amount of pressure in the hubbing press, which can prolong the life of the hubs and dies. However, if the die is not lined up exactly with the hub, it can result in die doubling, which can create spectacular coins.
Here's a summary of the different types of coins and their production methods:
Annealing
Annealing is a crucial step in the coin production process that involves heating the coin blanks to a high temperature to soften them.
The process changes the metal's physical properties, making it softer and more malleable. This allows for a smoother striking process.
The annealing furnace heats the blanks at temperatures above 800°C in an oxygen-free environment to prevent tarnishing. This ensures that the blanks are prepared for the next stage of the process.
Sources
- https://corporatefinanceinstitute.com/resources/wealth-management/money-minting/
- https://library.willamette.edu/hfma/omeka/exhibits/show/coinsofthegreekandromanworld/numismatichistory/mintingprocess
- https://money.com/coin-costs-us-mint-solutions/
- https://en.wikipedia.org/wiki/Coining_(mint)
- https://en.wikipedia.org/wiki/Mint_(facility)
Featured Images: pexels.com