
The United States Mint has been producing coins for over two centuries, but its production process is not without challenges.
One of the main challenges facing the Mint is the increasing demand for coins, particularly for the penny and nickel, which are the most widely used coins in circulation.
The Mint has been struggling to keep up with this demand, leading to a shortage of these coins in many areas.
To address this issue, the Mint has implemented new production techniques, such as the use of high-speed presses, to increase its output.
These new presses have significantly improved the Mint's efficiency, allowing it to produce more coins in a shorter amount of time.
The Mint has also invested in new machinery and technology to improve the quality and accuracy of its coin production.
The Pandemic's Effect
The pandemic's effect on coin production was significant, with some people struggling to find quarters to use at the laundromat. Business closures and disruptions to normal circulation patterns were major contributors to the shortage.
The U.S. Mint increased production of circulating coins in response to the shortage, producing almost 3 billion more coins in 2020 compared to 2019.
Before the pandemic, the Federal Reserve Banks distributed an average of 70 billion coins to financial institutions. This highlights the massive scale of the coin circulation system in the United States.
The U.S. Coin Task Force was formed in July 2020 to help identify and promote strategies to address the country's coin circulation issues. This task force played a crucial role in mitigating the disruption to coin circulation.
To mitigate the disruption, the U.S. Mint and Federal Reserve Banks released 5 billion pieces of coin reserves. This move helped to replenish the coin supply and ease the shortage.
The U.S. Mint and the Federal Reserve have proposed several solutions to solve the circulation challenge, including increased transparency on coin inventories and flows.
If this caught your attention, see: Coin Pushers Legal 2020
Coin Production Issues
Coin production issues have been a significant challenge in the United States. The U.S. Mint increased its production of coins to mitigate the disruption of coin circulation during the Covid-19 pandemic.
A staggering 5 billion pieces of coin reserves were released by the U.S. Mint and Federal Reserve Banks to help alleviate the problem. This move aimed to get coins back into circulation.
The U.S. Coin Task Force launched the #GetCoinMoving campaign to encourage the public to spend their coins, deposit them at financial institutions, and redeem them at coin kiosks. This effort was crucial in getting coins moving again.
The U.S. Mint and the Federal Reserve proposed several solutions to the circulation challenge. They include increasing transparency by improving data on coin inventories, flows, and demand across the coin ecosystem.
Improvement Plans and Assessments
The United States Mint has been actively working to improve its coin production processes since 2006.
One of the ongoing improvement plans is to reduce maintenance downtime of coin manufacturing machinery, which began in 2006 but was not fully completed. The Mint shifted focus from solely manufacturing efficiency to overall operational efficiency in FY 2008.
The Mint aims to develop a measure for Enabling Commerce, a core responsibility, and track other metrics such as Seigniorage per $ issued and Mint Quality Index, which is a composite rating of samples of final coin products to standard visual and functional requirements.
Here are some key aspects of the ongoing improvement plans:
Reducing maintenance downtime of coin manufacturing machineryEstablishing a performance target to reduce the time required to process raw materials into finished goodsDeveloping a measure for Enabling CommerceTracking Seigniorage per $ issued and Mint Quality Index
You might like: Pipette Measure
Program Improvement Plans
Program Improvement Plans are a crucial aspect of any organization's growth and development. The United States Mint has been actively working on several improvement plans since 2006.
One of the plans started in 2006 aimed to reduce maintenance downtime of coin manufacturing machinery, but it's not yet completed. The Mint shifted its focus from solely manufacturing efficiency to overall operational efficiency in FY 2008.
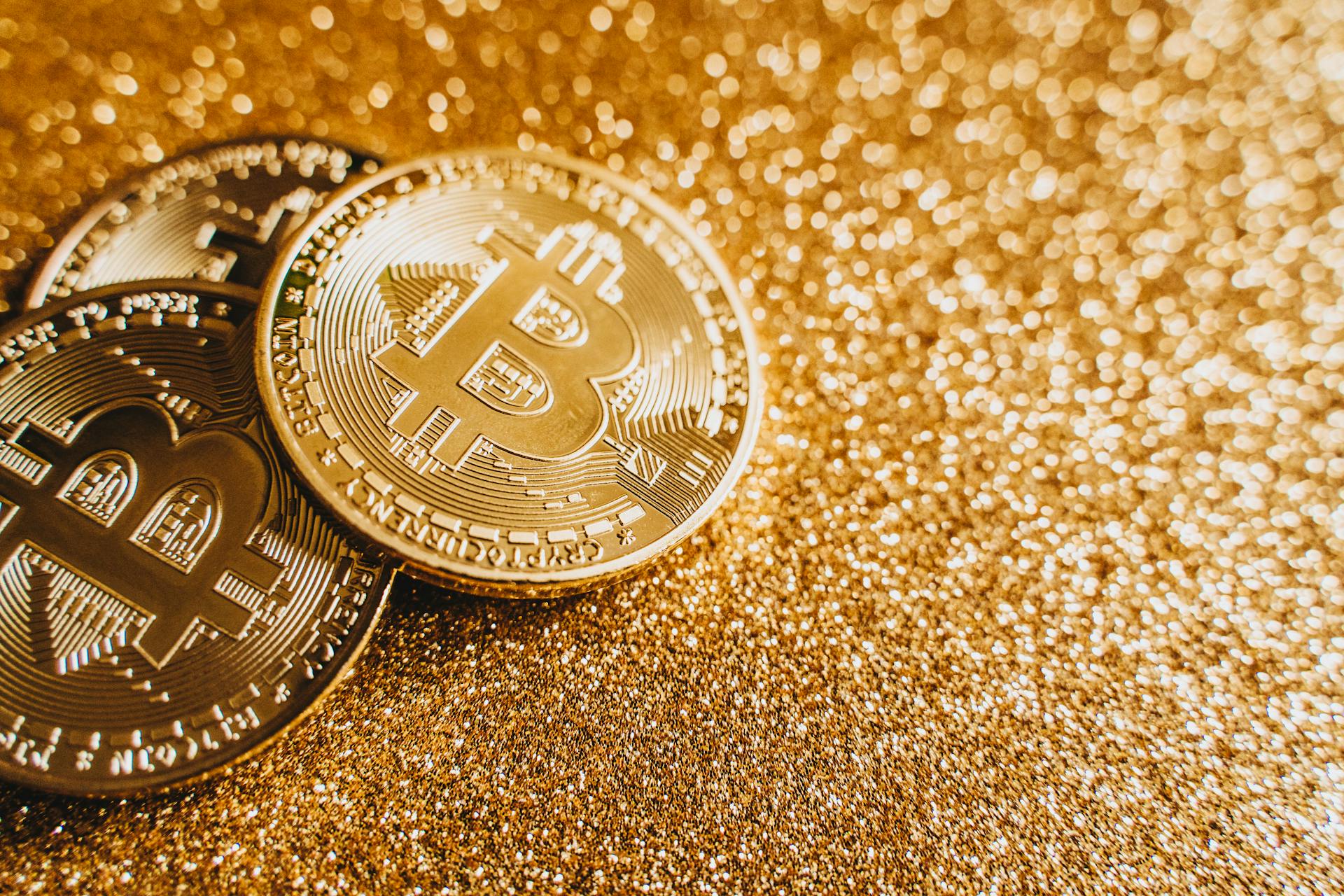
Another plan from 2006 targeted reducing the time required to process raw materials into finished goods. By improving forecasts and monitoring Federal Reserve Banks inventory data, the Mint aims to reduce production volatility and ensure adequate coinage for commercial needs.
The Mint has established a strategic stockpile of coinage to prepare for unexpected events. This plan is still in action but not yet completed.
Questions/Answers (Detailed Assessment)
A detailed assessment is a thorough evaluation of an individual's or organization's performance to identify areas for improvement. It's a crucial step in creating effective improvement plans.
The assessment should be based on specific, measurable goals and objectives, such as the ones outlined in the "Setting Goals and Objectives" section. These goals should be challenging yet achievable.
A detailed assessment should also involve gathering and analyzing data, as discussed in the "Data-Driven Decision Making" section. This data can come from various sources, including performance metrics and feedback from stakeholders.
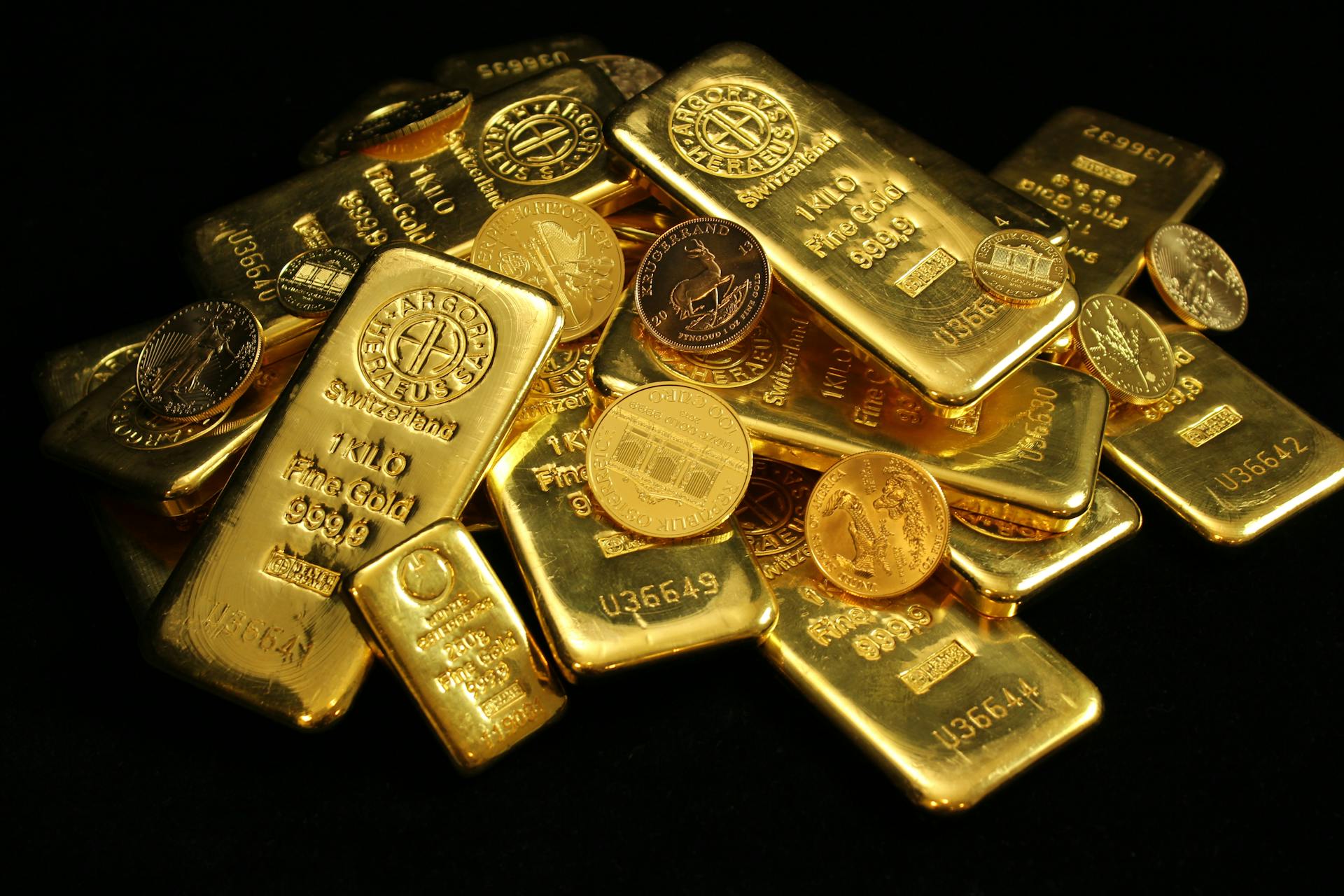
The assessment should be conducted regularly to ensure that progress is being made towards the goals. This helps to identify any issues early on and make adjustments as needed.
The results of the assessment should be used to create a clear and actionable improvement plan, as explained in the "Creating an Improvement Plan" section. This plan should include specific steps to be taken, timelines for completion, and responsible parties.
By following these steps, individuals and organizations can create effective improvement plans that lead to real change and progress.
Coin Production Process
The United States Mint coin production process is a complex and fascinating topic. The process begins with the creation of designs, which are then reviewed and approved by the Secretary of the Treasury.
The Mint uses a combination of machines and skilled craftsmen to produce coins. The Philadelphia Mint produces over 7 billion coins annually, making it one of the largest coin-producing facilities in the world.
The Mint's manufacturing process involves several key steps, including metal blanking, striking, and packaging.
Melting Common for All?
Not all coins were subject to the same melting rules as classic commemoratives. The commemoratives had special legislation allowing for the melting of unsold pieces.
Circulating coinage, on the other hand, underwent multiple tests for weight and purity during manufacture and delivery. These tests were so rigorous that a single Special Assay coin that was out of tolerance could condemn an entire delivery.
If a delivery was condemned, it meant that all of those coins were melted and recoined. This could happen quickly, but sometimes it took a year or more to recoin.
Where's the Evidence?
The coin production process was more complex than just following a request. Before the law changed in 1873, the Mint delivered as many coins as the owner's bullion would make.
The Mint used to handle gold and silver in Troy ounces and grains, which required conversions to calculate the required amount of coin.
Calculations had to be made by the Melter and Refiner (M&R) and Coiner to convert bullion into coin while allowing for normal wastage and defective pieces.
The Coiner would eventually deliver to the Superintendent the required amount of coins in the requested denomination, such as $1,000,000 in $20 gold double eagles.
Coin production was always requested in dollar amounts after the law changed in 1873, but the calculations were still made internally in Troy ounces and grains.
Standardization of Planchets and Blanks
In the early days of coin production, standardization of planchets and blanks was not a straightforward process.
Except for early coppers, blanks were cut from long strips, not standard sheets of metal.
The M&R was supplied with iron molds of different widths and thickness, each determined by the dimensions of the coins that would be produced.
Gold or silver was poured into these molds depending on the coin denomination that was to be made.
An ingot for making standard dollars was 12-1/2 inches long, 1-1/2 inches wide, and 7/16th inch thick.
An ingot for quarters was 12-1/2 inches long, 1-1/16th inch wide and 3/16th inch thick.
To produce long thin strips, ingots were run through compression rollers multiple times.
The number of blanks made from each strip depended on denomination and whether blanks were cut singly or in pairs.
How Coins Are Counted
Coins were counted using manually operated counting boards made of wood with metal dividers until the 1920s. These boards were preferred to mechanical counters because they caused little damage to coins.
The counting boards could hold up to 250 dollar coins at one time, and other board sizes accommodated various denominations. They were also easy to use and rarely broke down.
Gold coins were put in bags of $5,000 value, but each bag also had a weight tolerance of plus or minus nine grains.
Mintage and Circulation
Before the Covid-19 pandemic, the Federal Reserve Banks distributed an average of 70 billion coins to financial institutions each year. This helped meet most of the demand for coins.
The onset of the Covid-19 pandemic disrupted coin circulation in the United States, affecting both secular trends and pandemic-specific effects. The U.S. Mint increased its production of coins to mitigate the disruption.
The U.S. Mint and Federal Reserve Banks released 5 billion pieces of coin reserves to help address the issue. This move aimed to get coins back into circulation.
Here are some key proposals to solve the circulation challenge:
- Increased transparency by improving data on coin inventories, flows, and demand across the coin ecosystem.
- Inventory management by improving existing methodologies and practices to manage coin inventories.
- Denomination shifts, changing the U.S. Mint’s production from lower to higher-value coins.
- Reinforced consumer pathways by boosting consumer awareness and supporting options for depositing loose coins cheaply and conveniently.
Coin Circulation Challenges
The Covid-19 pandemic disrupted coin circulation in the United States, arising from secular trends and pandemic-specific effects.
Before the pandemic, the Federal Reserve Banks distributed an average of 70 billion coins to financial institutions, but recirculating coins couldn't meet the demand. The onset of the pandemic made it more difficult for retailers and small businesses to accept cash payments, especially for those who rely on cash transactions.
The U.S. Mint increased its production of coins to mitigate the disruption, releasing 5 billion pieces of coin reserves in collaboration with the Federal Reserve Banks.
The coin supply problem can be solved if we all do our part, as the U.S. Mint suggests. This can be achieved by spending coins, depositing them at financial institutions, and redeeming them at coin kiosks.
The U.S. Coin Task Force launched the #GetCoinMoving campaign to encourage the public to take action.
A unique perspective: What Is Bit Coin Cash
Here are some proposed solutions to the circulation challenge:
- Improved data on coin inventories, flows, and demand across the coin ecosystem.
- Inventory management by improving existing methodologies and practices to manage coin inventories.
- Denomination shifts, changing the U.S. Mint’s production from lower to higher-value coins.
- Reinforced consumer pathways by boosting consumer awareness and supporting options for depositing loose coins cheaply and conveniently.
Cost of Small Change
The cost of producing small change is surprisingly high. In the fiscal year 2022, the U.S. Mint faced costs of 2.72 cents to produce a 1-cent penny.
It's worth noting that this cost has remained above face value since 2005. The unit cost for pennies has been a concern for a while.
Many people are starting to question the value of producing new pennies. Data from a poll in August 2022 showed that 58% of U.S. voters agreed to stop producing new pennies.
Nickel production is also being scrutinized, with 33% of voters favoring a halt to new nickel production. The cost to produce a nickel is even higher, at 10.41 cents.
Expand your knowledge: Canada Coins Value
Determinants of Mintage Size
The U.S. Treasury Department and the Mint operated on the Federal Government's fiscal year, which is why there's inconsistency in coin production from one calendar year to another.
This fiscal year priority was so important that it even influenced the way coins were dated, making it an exception to normal accounting practices.
The demand for copper coins, made from 1793 through 1857, filtered through large banks and the United States Treasurer to the U.S. Mint at Philadelphia, determining how many coins were needed.
Gold and silver coins, on the other hand, were made to the demand of depositors rather than for Government account, leading to erratic production.
The process of making gold and silver coins was also affected by the delay between depositing specie and the Mint's delivery of coins made from that deposit.
Half dollars were a popular choice for large depositors because it took less time to deliver $100,000 in halves than in smaller denominations like half dimes.
The Act of 1873 changed the way the Government bought gold and silver for coinage, making coin production more closely related to commercial demand.
The Treasurer of the U.S., the Mint Director, the Comptroller of Currency, and informal conversations with bankers and Assistant Treasurers in various regions all played a role in determining mintage size.
Congress also got involved by ordering certain production quotas, such as for Morgan dollars made from required bullion purchases.
Curious to learn more? Check out: Gold Coins Canada
And Half Dollars
Half dollars were not typically melted for recoinage, except in one documented instance where 1877 half dollars were melted into dimes in 1886 due to high demand and a lack of bullion.
Only a small number of half dollars were involved, and this was done to meet a specific need for dimes.
The U.S. government did, however, melt older coins when changes were made to coin weights or precious metal content, classifying them as "obsolete" or "uncurrent".
Frequently Asked Questions
How many coins does the U.S. Mint produce every year?
The U.S. Mint produces over 10 billion circulating coins annually. This staggering number highlights the Mint's significant role in circulating currency across the country.
Sources
- https://en.wikipedia.org/wiki/United_States_Mint_coin_production
- https://www.marketplace.org/2022/01/27/how-does-the-u-s-mint-decide-how-many-coins-to-produce-each-year/
- https://cashessentials.org/united-states-coin-production-and-circulation/
- https://obamawhitehouse.archives.gov/sites/default/files/omb/assets/omb/expectmore/detail/10000420.2002.html
- https://coinweek.com/coin-production-united-states-mint-questions-answers-roger-burdette/
Featured Images: pexels.com