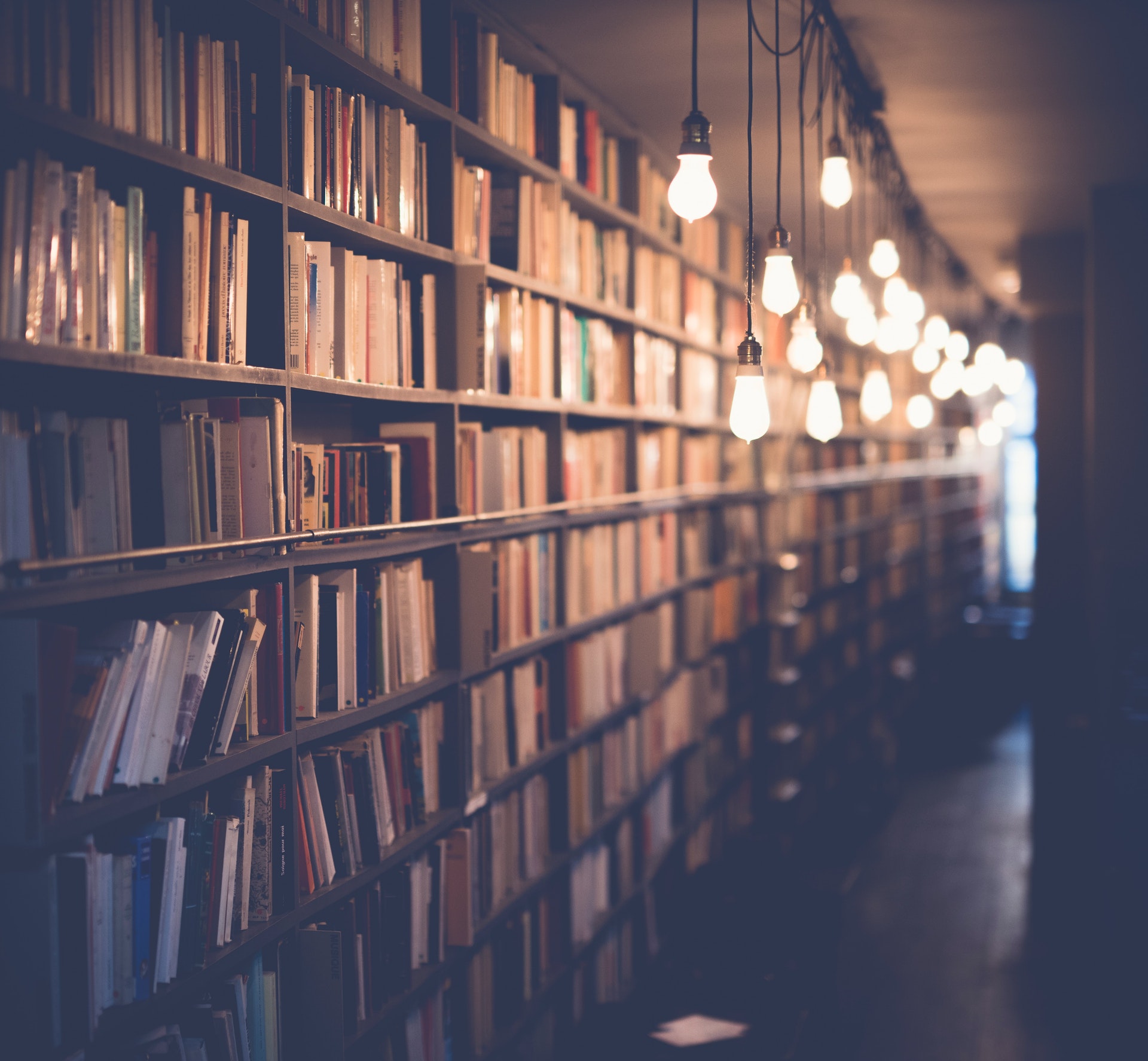
There is no one answer to this question as six sigma is a complex and multi-faceted business strategy. However, some people may incorrectly believe that six sigma is only about improving efficiency and quality control in manufacturing processes. However, six sigma encompasses much more than this – it is a holistic approach to business that takes into account all aspects of the company in order to create a more streamlined, efficient and effective operation. In addition, six sigma is not just a short-term solution or a once-off project – it is a long-term business strategy that should be continually adapted and updated in order to keep up with the ever-changing business landscape.
Suggestion: Sigma Projects
What is six sigma?
While there are many definitions of Six Sigma, it is commonly accepted to be a business improvement methodology that seeks to identify and remove causes of errors and defects in any process, whether in manufacturing or service delivery.
The key to Six Sigma is in its focus on process improvement. This means that rather than simply seeking to fix individual problems as they occur, the Six Sigma methodology seeks to identify and address the root causes of errors and defects, in order to prevent them from occurring in the first place.
To do this, Six Sigma employs a number of tools and techniques, including statistical analysis, process mapping, and quality control. By using these tools to identify and understand the causes of errors and defects, businesses can then take steps to eliminate them.
The ultimate goal of Six Sigma is to achieve near-perfection in any process, whether it is manufacturing a product or delivering a service. This goal is often expressed as a goal of reducing defects to less than 3.4 defects per million opportunities.
While this may seem like an impossible goal, businesses that have adopted the Six Sigma methodology have been able to achieve it. In fact, many businesses have reported defect rates of well below 1 per million, and some have even achieved rates of less than 0.1 per million.
There are a number of reasons why Six Sigma has been so successful in improving quality and reducing defects. One of the most important is that it provides a structured and systematic approach to problem-solving.
Another key reason is that it makes use of data and statistical analysis to drive decision-making. This means that businesses are able to make informed decisions about where to focus their efforts, based on a rigorous understanding of the causes of errors and defects.
Finally, Six Sigma is successful because it recognizes that human beings are fallible and that errors are inevitable. Rather than seeking to achieve perfection, which is impossible, it instead seeks to minimize the occurrence of errors and defects. This acknowledgement of humanity's fallibility is what sets Six Sigma apart from other quality improvement methodologies, and is one of the key reasons for its success.
What are the benefits of six sigma?
There are benefits to a Six Sigma certification. Six Sigma is a business improvement methodology that is used to streamline processes and eliminate defects. A Six Sigma certified individual has a system in place to measure, analyze, and improve processes. This certification can lead to increased job opportunities, earnings potential, and career advancement. Six Sigma is also beneficial to organizations, as it can help to improve quality, reduce costs, and increase customer satisfaction.
What are the key elements of six sigma?
There are a few key elements of six sigma that help organizations to achieve higher levels of quality and efficiency. The first key element is a strong commitment from leadership. Without this commitment, it is difficult to implement and sustain the necessary changes. Leaders need to be actively involved in setting the direction for six sigma and ensuring that everyone is aware of and understands the goals.
The second key element is a clear understanding of what six sigma is and how it can help the organization. There needs to be buy-in from all levels of the organization in order to successfully implement six sigma.
The third key element is having the right people in place to lead and support the change. This includes having trained and certified black belt and green belt Six Sigma practitioners. It is also important to have mentors and coaches available to those who are new to the Six Sigma methodology.
The fourth key element is having robust processes in place. This means that there is a systematic and standardized approach to the way work is done. It also includes having adequate resources available to support the changes being made.
The fifth key element is effective communication. This is vital to ensuring that everyone is on the same page and understands the changes that are taking place. Communication needs to be clear and concise, and it should flow freely between all levels of the organization.
The sixth and final key element is continuous improvement. Once Six Sigma has been implemented, it is important to continually monitor and strive to improve upon the process. This includes making modifications and adjustments as needed to ensure that the process is as efficient and effective as possible.
By following these six key elements, organizations can experience significant improvements in quality and efficiency. Six Sigma has been proven to work time and time again, and it can be an invaluable tool for any organization looking to take their performance to the next level.
Additional reading: Nonverbal Communication
What is the difference between six sigma and other quality improvement initiatives?
In the business world, the term “quality” can mean many different things. For some businesses, quality is a measure of how well a product or service meets the customer’s expectations. For others, quality is a measure of how well a product or service meets the company’s own internal standards.
Regardless of how a business defines quality, there are always opportunities for improvement. That’s where quality initiatives like Six Sigma come in. Six Sigma is a data-driven approach to quality improvement that focuses on reducing defects and increasing customer satisfaction.
Comparing Six Sigma to other quality initiatives is difficult because there are so many different types of quality initiatives out there. Some initiatives, like ISO 9000, are focused on developing and maintaining a quality management system. Others, like Lean, are focused on streamlining processes and eliminating waste.
Still, there are some key ways in which Six Sigma differs from other quality initiatives:
1. Six Sigma is heavily reliant on data and statistical analysis. This allows businesses to identify root causes of problems and target their improvement efforts accordingly.
2. Six Sigma focuses on reducing defects, rather than simply meeting customer expectations or internal standards. This makes Six Sigma an ideal approach for businesses that have a high volume of customers or products.
3. Six Sigma is a structured and systematic approach to quality improvement. This makes it easy to implement and track progress.
4. Six Sigma is designed to be sustainable over the long term. This means that businesses can continue to reap the benefits of Six Sigma even after the initial investment has been made.
Overall, Six Sigma is a powerful quality improvement initiative that can bring significant benefits to businesses. It is important to note, however, that Six Sigma is not the only quality improvement initiative out there. Lean, ISO 9000, and other quality initiatives all have their own strengths and weaknesses. The key is to select the right quality improvement initiative for your business based on your specific needs and goals.
Broaden your view: Internal Control
How is six sigma different from traditional quality control methods?
It is important to note that quality control and Six Sigma are not synonymous. Quality control is a generic term that could apply to any number of quality improvement initiatives, whereas Six Sigma is a specific methodology that has its own set of tools and techniques.
Traditional quality control methods tend to be reactive, meaning that they are only implemented after a problem has already been identified. Six Sigma, on the other hand, is a proactive approach that seeks to prevent problems from occurring in the first place.
One of the key differences between Six Sigma and traditional quality control is the role of statistics. Traditional quality control methods tend to rely on intuition and experience, while Six Sigma relies heavily on statistical data and analysis. This allows Six Sigma to be more objectively data-driven and to target specific problem areas more effectively.
Another key difference is the focus on process improvement. Traditional quality control methods tend to focus on individual products or services, while Six Sigma takes a holistic view of the entire process. This allows Six Sigma to identify and address systemic issues that may be causing defects, rather than just treating the symptoms.
Finally, Six Sigma also has a built-in mechanism for continuous improvement. The Six Sigma DMAIC (Define, Measure, Analyze, Improve, Control) methodology includes a feedback loop in which the results of each project are used to improve the process for future projects. This means that the gains made through Six Sigma are sustainable over the long term.
Overall, Six Sigma represents a significant improvement over traditional quality control methods. It is more effective, more data-driven, and more focused on continuous improvement.
Suggestion: Medical Control
What are the steps in a six sigma project?
There are many steps in a six sigma project, but the most important steps are as follows:
1. Define the problem or opportunity.
2. Measure the current state of the process.
3. Analyze the data to identify root causes of variation.
4. Improve the process by eliminating or reducing the root causes of variation.
5. Control the process to maintain the improvements.
The first step in any six sigma project is to define the problem or opportunity that is to be addressed. This step is important because it helps to ensure that the project is focused on the right issue and that all stakeholders are clear about what the project is trying to achieve.
The second step is to measure the current state of the process. This step is important because it provides a baseline against which the improvements made during the project can be measured.
The third step is to analyze the data to identify root causes of variation. This step is important because it helps to ensure that the project is aimed at addressing the real causes of the problem or opportunity.
The fourth step is to improve the process by eliminating or reducing the root causes of variation. This step is important because it is the heart of the six sigma improvement process.
The fifth step is to control the process to maintain the improvements. This step is important because it helps to ensure that the improvements made during the project are sustainable over the long term.
How is a six sigma project structured?
A Six Sigma project is typically structured around the DMAIC process, which consists of the following steps: Define, Measure, Analyze, Improve, Control.
The first step, Define, is all about clearly identifying the problem that needs to be solved. This step also involves setting customer requirements and Key Performance Indicators (KPIs), which will be used to measure the success of the project.
The second step, Measure, is focused on data collection. This data will be used to understand the current state of the process and identify opportunities for improvement.
The third step, Analyze, is where cause-and-effect analyses are performed to identify the root causes of process problems.
The fourth step, Improve, is focused on finding and implementing solutions to the problems identified in the previous steps. This step also involves developing and implementing process controls to prevent the problems from recurring.
The fifth and final step, Control, is all about monitoring the process to ensure that the improvements made in the previous steps are sustained over time. This step also includes establishing procedures for responding quickly to any problems that do occur.
What are the roles of the different participants in a six sigma project?
There are typically four participants in a Six Sigma project. They are the Six Sigma project sponsor, the Six Sigma project leader, the Six Sigma team members, and the organizational leadership.
The Six Sigma project sponsor is typically a senior executive in the organization who provides the funding and resources for the project. The sponsor also provides the overall direction for the project and ensures that it aligns with the organization's strategic objectives.
The Six Sigma project leader is responsible for leading the team and ensuring that the project is completed on time, within budget, and to the required level of quality. The leader also works with the sponsor to ensure that the project objectives are met.
The Six Sigma team members are the individuals who actually carry out the work of the project. They are responsible for completing the tasks assigned to them and for providing accurate and timely reports to the project leader.
The organizational leadership is responsible for supporting the Six Sigma project and for providing the necessary resources. The leadership also provides guidance and direction to the project team and ensures that the project is aligned with the organization's strategic objectives.
If this caught your attention, see: Organizational Culture
How is a six sigma project implemented?
There is no one answer to this question as every organization is different and will have different needs for their six sigma project. However, there are some basics that are typically followed in order to ensure success.
First, a six sigma project should be led by a team of highly skilled and trained individuals. This team should be able to identify opportunities for improvement, and then develop and implement plans to address those opportunities.
Once the team has been assembled, the next step is to select a project manager. The project manager will be responsible for ensuring that the project stays on track and meets all deadlines. He or she will also be the point of contact for the team and will be responsible for communicating updates and project results to upper management.
After the project manager has been selected, the team will need to establish clear objectives for the project. These objectives should be specific, measurable, achievable, relevant, and time-bound. Once the objectives have been established, the team can then begin to develop a plan of action for how they will be achieved.
One of the most important aspects of any six sigma project is data collection and analysis. The team must collect accurate data in order to identify problem areas and areas of opportunity. This data should then be analyzed in order to determine the root cause of any problems.
Once the root cause has been identified, the team can then begin to develop and implement solutions. These solutions should be designed to address the root cause of the problem in order to prevent it from happening again in the future.
After the solutions have been put in place, the team will need to monitor the results to ensure that the desired outcome has been achieved. If the results are not as expected, the team can then make necessary adjustments to the solutions.
It is important to keep in mind that there is no one right way to implement a six sigma project. Every organization is different and will have different needs. The key is to tailor the project to the specific needs of the organization in order to ensure its success.
Frequently Asked Questions
What is Six Sigma in simple words?
Six Sigma is a data-driven approach used to improve business by reducing the likelihood of error. This methodology uses a statistical methodology for eliminating defects.
What is Six Sigma in quality management?
Six Sigma is a method that provides organizations tools to improve the capability of their business processes. This increase in performance and decrease in process variation helps lead to defect reduction and improvement in profits, employee morale, and quality of products or services.
What is Six Sigma DMAIC?
The Six Sigma DMAIC methodology uses a three-step process to improve processes: Monitoring, Defining, and Advocating for Change. This process allows the Six Sigma team to collect data in order to identify performance deficiencies, quantify the potential impact of changes, and make recommendations to improve the process.
What are six sigma levels?
Six Sigma is a quality management system (QMS) with six levels of quality. Level 1 is the basic level of quality, and 6 Sigma delivers products and services that are within specification. Levels 2-5 refer to specific types of quality control processes that help ensure products and services meet customer expectations. Levels 6 and 7 account for reducing defects or errors to the point where they cannot be detected by the customer or conducted without impacting the product’s usability.
What are the Six Sigma techniques?
Six Sigma Techniques are a problem solving approach that focuses on reducing defects and variability in products.
Sources
- https://6sigma.com/what-is-six-sigma/
- https://www.chegg.com/homework-help/questions-and-answers/following-true-six-sigma--utilizes-five-step-improvement-model-dmaic-b-developed-motorola--q42705718
- https://www.simplilearn.com/what-is-six-sigma-a-complete-overview-article
- https://answerdata.org/which-of-the-following-statements-regarding-six-sigma-is-true/
- https://cvdragon.com/blog/know-the-6-elements-of-six-sigma-certification/
- https://brainly.com/question/15186728
- http://www.sixsigma.in/advantages-and-disadvantages-of-six-sigma.html
- https://quizlet.com/145391880/six-sigma-flash-cards/
- https://quizlet.com/602807550/lean-six-sigma-flash-cards/
- https://www.leansixsigma.school/what-are-the-benefits-of-lean-six-sigma/
- https://corporatefinanceinstitute.com/resources/management/six-sigma/
- https://www.quesba.com/questions/following-true-six-sigma-lofty-goal-statistical-six-sigma-used-723171
- https://quizlet.com/111502704/six-sigma-final-exam-notes-flash-cards/
- https://www.chegg.com/homework-help/questions-and-answers/6-following-true-six-sigma-process-focuses-end-product-employee-satisfaction-b-terminates--q43871741
- https://qualite.ooreka.fr/comprendre/six-sigma
Featured Images: pexels.com