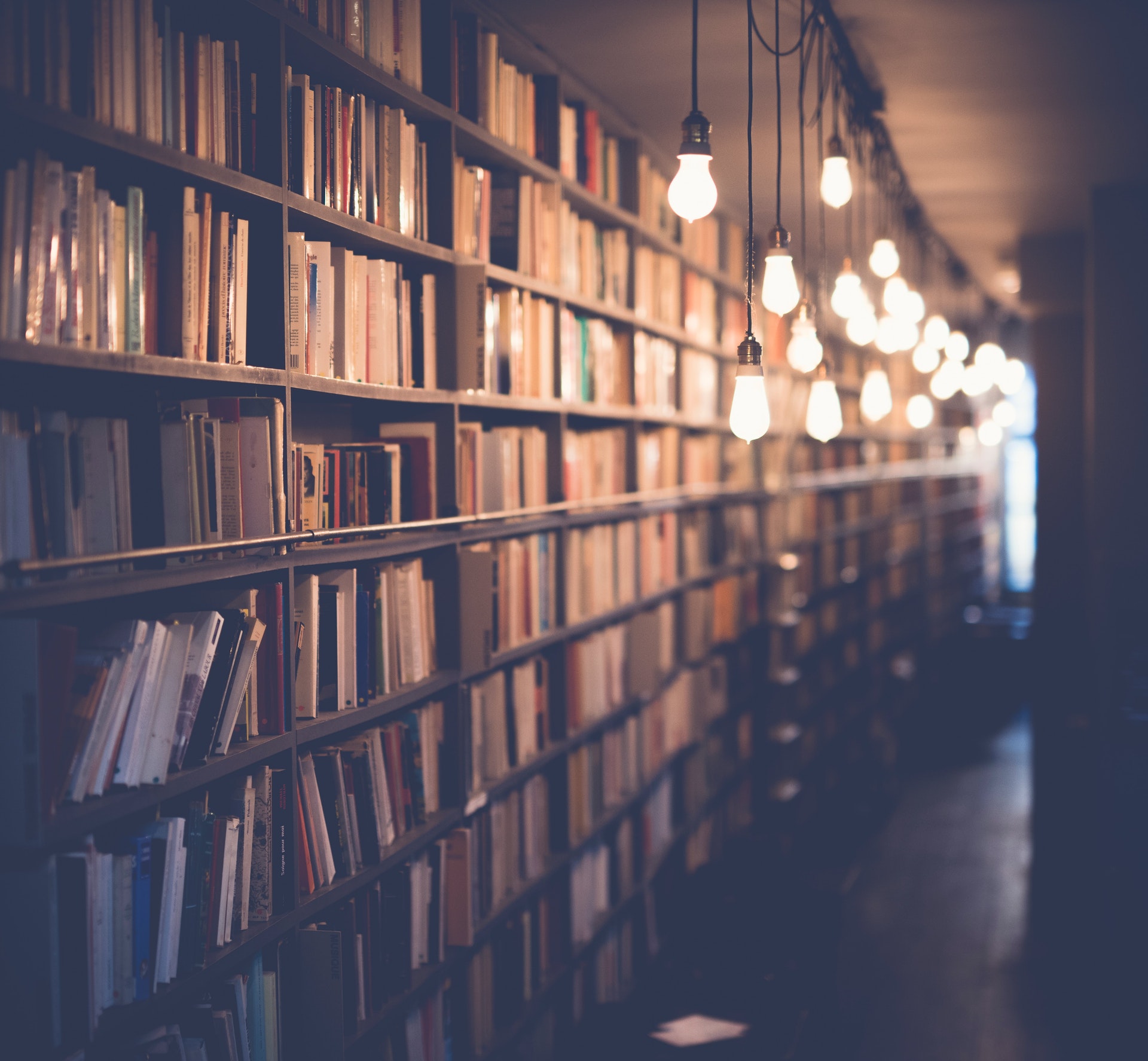
One type of machine safeguarding is a barrier guard. Barrier guards are physical barriers that are placed between the operator and the moving parts of the machine. They are used to keep the operator from coming into contact with the moving parts of the machine. Another type of machine safeguarding is a point of operation guard. Point of operation guards are used to protect the operator from coming into contact with the moving parts of the machine while the machine is in operation.
You might enjoy: Primary Safeguarding Methods
What is a type of machine safeguarding?
A type of machine safeguarding is any mechanical, electronic, or procedural measure that stops or slows down the action of a machine in order to protect users from injury. There are three main types of machine safeguarding: physical barriers, mechanical guards, and electronic guards.
Physical barriers are the simplest and most common type of machine safeguarding. They work by either completely stopping access to a dangerous part of the machine, or by slowing down the movement of a person or object so that they can’t reach the danger zone. Common examples of physical barriers include fences, covers, and enclosures.
Mechanical guards are devices that are attached to the machine itself and move with it. They work by either blocking access to the danger zone, or by absorbing energy from a collision so that the person or object doesn’t have to. Common examples of mechanical guards include shield guards, barrier guards, and presence-sensing devices.
Electronic guards are devices that use sensors to detect when someone or something is getting too close to the danger zone. When the sensor is triggered, the electronic guard will either stop the machine or slow it down. Common examples of electronic guards include light curtains, photoeyes, and pressure mats.
What are the different types of machine safeguarding?
There are several different types of machine safeguarding that are available, and each type has its own advantages and disadvantages. The most common types of machine safeguarding are mechanical guards, interlocking devices, and electrical controls.
Mechanical guards are the most basic type of machine safeguard and are usually the least expensive. They work by physically blocking access to dangerous parts of the machine. Some examples of mechanical guards include barrier guards, enclosures, and covers.
Interlocking devices are another type of machine safeguard. They work by preventing the machine from being turned on or used unless the proper safety procedures are followed. For example, a common interlocking device is a switch that can only be turned on when the guard is in place.
Electrical controls are the most complex type of machine safeguard. They work by monitoring the machine and its surroundings and automatically shutting off the power if a dangerous situation is detected. For example, an electrical control might be a light that turns on when a machine is overloaded.
Each type of machine safeguard has its own advantages and disadvantages. Some advantages of using machine safeguards include increased safety, reduced liability, and increased productivity. Some disadvantages of using machine safeguards include increased cost, reduced flexibility, and reduced efficiency.
The best type of machine safeguard depends on the specific needs of the workplace. In some cases, a combination of different types of machine safeguarding might be used. For example, a mechanical guard might be used to block access to the machine, while an electrical control monitors the machine and shuts off the power if a dangerous situation is detected.
For more insights, see: What Is Insurance and Its Types
What are the benefits of machine safeguarding?
There are many benefits to machine safeguarding. By protecting workers from injuries, machine safeguarding can improve job satisfaction and morale, reduce workers’ compensation costs, increase productivity, and improve product quality. In addition, safeguarding can help to protect equipment from damage and downtime.
When workers are injured on the job, it can lead to physical and psychological pain, suffering, and financial hardships. In addition to the obvious human costs, workplace injuries also cost businesses money in the form of workers’ compensation claims, lost productivity, and damaged equipment. Machine safeguarding can help to prevent these costly accidents and injuries.
Safeguarded machinery is often more productive than unguarded machines. This is because workers are able to work more quickly and efficiently when they feel safe and comfortable. In addition, when workers know that their safety is a priority, they are more likely to take care of the equipment they are using. This can lead to less equipment downtime and damage.
Finally, machine safeguarding can improve product quality. When workers feel safe, they are able to focus on their work and are less likely to make mistakes. In addition, well-maintained equipment is less likely to break down, resulting in fewer defects.
Machine safeguarding is an important part of any workplace safety program. By protecting workers and equipment, safeguarding can help to improve job satisfaction, productivity, and product quality.
What are the best practices for machine safeguarding?
Workplace injuries due to machines are preventable. Machine safeguarding is the best way to prevent these injuries.
There are four main types of machine safeguarding:
1. Machine Guards
2. Warning Devices
3. Safe Work Procedures
4. Training
1. Machine Guards
Machine guards are physical barriers that protect workers from exposure to moving parts. They can be purchased commercially or custom-made for a specific machine.
2. Warning Devices
Warning devices, such as horns or lights, warn workers of potential hazards. They are typically used in conjunction with machine guards.
3. Safe Work Procedures
Safe work procedures are written instructions that outline how to safely operate a machine. They should be specific to the make and model of the machine and should be followed by all employees who use the machine.
4. Training
All workers who use or come in contact with machines should be properly trained on machine safety. Training should include information on how to identify hazards, how to use machine guards and warning devices, and what to do in case of an emergency.
See what others are reading: Exercise Machines
How can machine safeguarding improve safety in the workplace?
There are many ways in which machine safeguarding can improve safety in the workplace. Safeguarding devices can prevent workers from coming into contact with moving parts of machinery, and they can also help to prevent dangerous debris from being ejected from the machinery. dust and other debris.
Installation of physical barriers such as fences, enclosures, and guards can help to keep workers away from moving parts of machinery. Fences and enclosures can also help to contain debris that may be ejected from the machinery.
Safeguarding devices can also be used to control the speed of moving parts of machinery. By reducing the speed of moving parts, the likelihood of injuries caused by contact with those parts is reduced.
In addition to the installation of physical barriers and the use of safeguarding devices, proper training of workers is essential to improve safety in the workplace. Workers should be trained in the proper use of machinery, and they should be made aware of the hazards associated with the machinery.
What are the most common injuries associated with machines?
There are a variety of injuries that can be associated with machines in the workplace. The most common injuries include:
-Cuts and lacerations from sharp edges
-Bruising and contusions from being hit by moving parts
-Crushing injuries from being caught in between moving parts
-Fractures and broken bones from being hit by heavy or moving parts
-Sprains and strains from repetitive motions
-Injuries to the eyes, ears, and fingers from flying debris or moving parts
How can machine safeguarding help to prevent injuries?
Machine safeguarding is the practice of using physical and mechanical devices to protect workers from potentially hazardous moving parts in machinery. Safeguarding can help to prevent injuries by reducing the likelihood of workers coming into contact with moving parts, and by providing a barrier between workers and the machinery.
There are a variety of machine safeguarding devices that can be used, depending on the type of machinery and the potential hazards present. Common safeguards include guards that physically block access to moving parts, devices that Slow down or stop the machinery if a worker is present, and emergency stop buttons that can be used to shut down the machinery in an emergency.
When used correctly, machine safeguarding devices can be effective in preventing injuries. However, it is important to remember that safeguarding is only one part of a comprehensive safety program. Other important elements of a safety program include employee training, machine maintenance, and proper workstation design.
What are some of the most common machine hazards?
There are many potential machine hazards that could harm workers in various industries. The most common machine hazards include:
1. Unsafe Guards: Guards are designed to protect workers from being injured by moving parts of a machine. However, if a guard is not properly installed or maintained, it can actually create a hazard. For example, a loose guard on a power saw can become caught in the blade, causing the saw to kick back and injure the operator.
2. Unsafe Wiring: Improperly wired machines can pose an electrocution hazard to workers.
3. Unsafe Operating Procedures: If workers are not properly trained on how to safely operate a machine, they can be injured by the machine.
4. Unsafe Maintenance Procedures: Improperly maintained machines can break down and cause injuries to workers. For example, a power saw that is not properly lubricated can bind and kick back, causing serious injuries to the operator.
5. Improperly Guarded Moving Parts: Moving parts on a machine can cause serious injuries if they are not properly guarded. For example, a power saw blade that is not properly guarded can cause serious cuts to the operator.
6. Unsafe Machine Design: Some machine designs can create hazards for workers. For example, a power saw with a defective guard can cause the operator to be cut by the blade.
7. Unsafe Workplace Conditions: Unsafe workplace conditions can increase the likelihood of a worker being injured by a machine. For example, if a power saw is being used in an area with poor lighting, the operator may not be able to see the blade and can be injured.
8. Improper Personal Protective Equipment: If workers are not using the proper personal protective equipment, they can be seriously injured by a machine. For example, if an operator is not wearing gloves while using a power saw, he or she can be cut by the blade.
9. Unsafe Machine Modifications: Unsafe machine modifications can create hazards for workers. For example, if a power saw is modified so that the guard does not work properly, the operator can be cut by the blade.
10. Other Unsafe Conditions: There are many other potential unsafe conditions that can lead to workers being injured by machines. For example, if a power saw is being used in an area with flammable materials, the operator could be killed if the saw sparks
For another approach, see: Which of the following Is an Example of A?
How can machine safeguarding help to reduce machine hazards?
Machine safeguarding can help reduce machine hazards in a few ways. First, if a machine is properly safeguarded, it is less likely to cause an accident. Second, safeguarding can help to prevent machine operators from being injured while working. And third, machine safeguarding can help to improve the quality of the products produced by the machine.
Let's take a look at each of these in turn.
1. Machine safeguarding can help reduce machine hazards by making the machine less likely to cause an accident.
There are many ways to safeguard a machine, but one of the most effective is to keep the machine clean and well-maintained. A clean machine is less likely to have loose parts or to be improperly operated.
2. Safeguarding can help to prevent machine operators from being injured while working.
One of the best ways to safeguard a machine is to make sure that the operator is properly trained in how to use it. Operator error is one of the leading causes of machine accidents, so it is important that operators know how to properly use the controls and understand the hazards of the machine.
3. Machine safeguarding can help to improve the quality of the products produced by the machine.
If a machine is not properly safeguarded, it is more likely to produce defective products. This is because the machine is more likely to be improperly operated, which can cause the production of defective products.
In summary, machine safeguarding can help to reduce machine hazards in a number of ways. By keeping the machine clean and well-maintained, by training the operator in how to properly use the machine, and by ensuring that the machine is properly safeguarded, you can help to reduce the likelihood of a machine accident and improve the quality of the products produced by the machine.
Frequently Asked Questions
What are the three areas of a machine that require safeguarding?
The three areas of a machine that require safeguarding are the point of operation, power transmission apparatus, and other moving parts. If a machine's point of operation exposes an employee to injury, it must be guarded.
What are the hazards of machine safeguarding?
Machine safeguarding is the practice of taking every possible measure to keep people and machines safe while they are in use. This includes everything from properly installing and adjusting equipment to implementing safety policies and procedures. If you or someone you know has been injured as a result of being in contact with a moving machine part, professional help may be needed. The first step is always to seek medical attention, no matter how minor the injury may seem at first. Depending on the type and severity of the injury, further treatment may also be necessary, such as surgery for crushed hands and arms.
What must be safeguarded when working with mechanical motion?
Typically, when working with mechanical motion, the operator and those in the vicinity must be safeguarded. Hazards that may occur include: Intentional misuse or abuse of machines Injury to persons as a result of contact with machinery or parts thereof Injury as a result of material spilling or flying from the machine
What are the rules of safety in the operation of machines?
There are several rules of safety in the operation of machines. The first rule is that any part of the body may be placed in the danger area, as long as it is safe to do so. Second, the worker must use both hands when operating the machine, to keep them out of the danger area. Third, if an operator's hands are required to be restrained or removed from the danger area, they must be positioned so that they are not touching any moving parts of the machine.
What are the three basic areas where safeguarding is required?
The three basic areas where safeguarding is required include the point of operation, power transmission apparatus, and the work area.
Sources
- https://securityboulevard.com/2022/09/safeguarding-memory-in-higher-level-programming-languages/
- https://www.iqsdirectory.com/articles/shredder/shredding-machine.html
- https://en.wikipedia.org/wiki/Individual_psychology
- https://machinerysafety101.com/2018/08/28/emergency-stop-pull-cords/
- https://en.wikipedia.org/wiki/Education_in_Malaysia
- https://www.osha.gov/enforcement/directives/std-01-12-002
- https://wawf.eb.mil/
- https://www.techtarget.com/searchsecurity/definition/challenge-response-system
- https://auth0.com/blog/the-complete-guide-to-deploying-javascript-applications-part-1/
- https://www.grainger.com/know-how/safety/machine-safeguarding/people-protection/kh-osha-requirements-machine-guarding
- https://www.csagroup.org/store/product/Z432-16/
- https://www.dmp.wa.gov.au/Documents/Safety/MSH_COP_SafeguardingOfMachineryAndPlant2009.pdf
- https://en.wikipedia.org/wiki/Icemaker
- https://www.cbn.co.za/industry-news/health-safety/safeguarding-you-your-loved-ones-and-possessions-during-loadshedding/
- https://www.bannerengineering.com/us/en/products/sensors.html
Featured Images: pexels.com