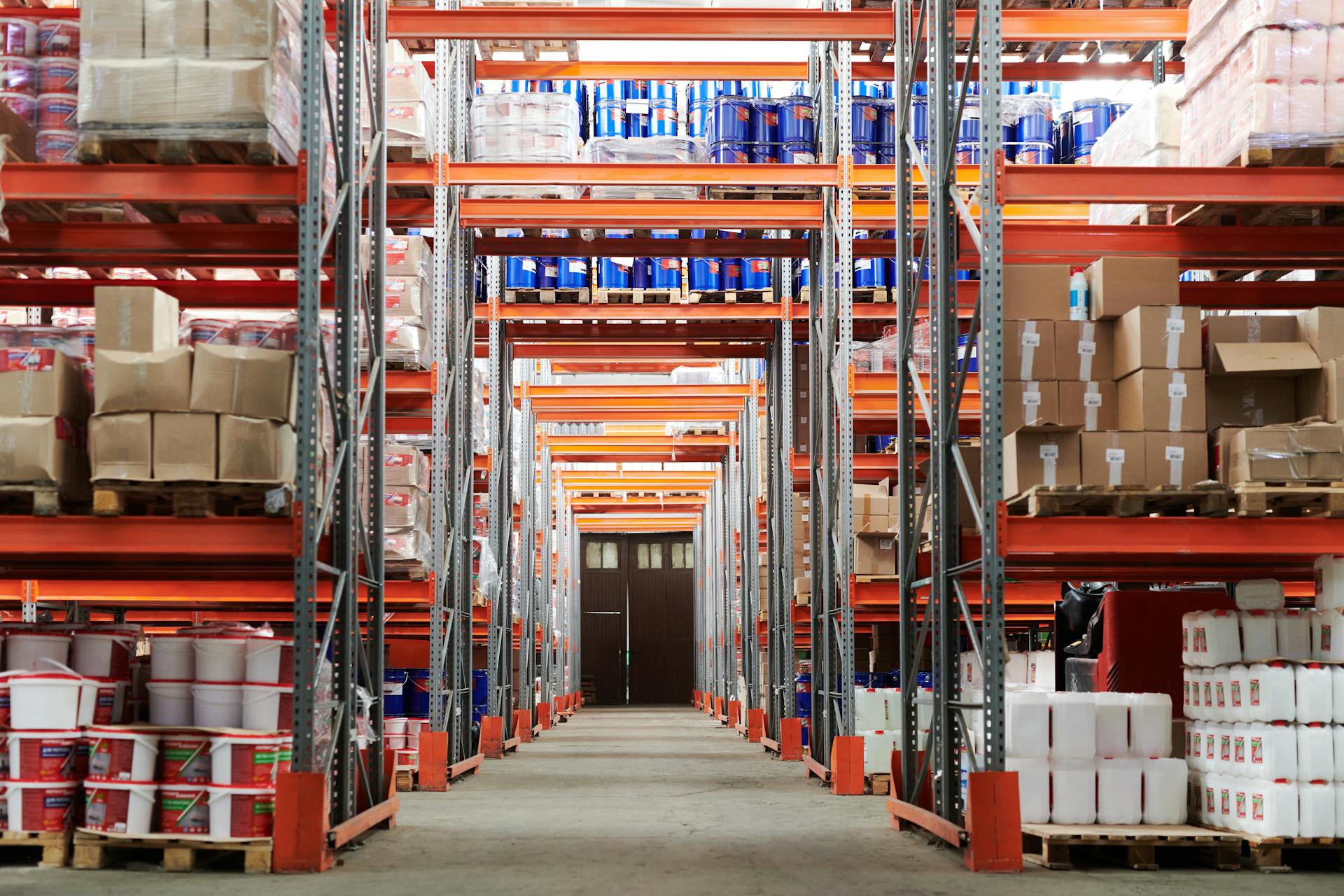
Risk pooling in supply chain management is a strategy that helps companies share risks and costs with partners or suppliers. This approach can significantly reduce the financial impact of supply chain disruptions.
By pooling resources, companies can create a safety net to protect against risks such as natural disasters, supplier insolvency, or equipment failures. This can be especially beneficial for small businesses or those with limited resources.
According to research, companies that implement risk pooling strategies can reduce their risk exposure by up to 30%. This is because the risk is spread across multiple partners or suppliers, making it more manageable.
Effective risk pooling requires careful planning and communication among all parties involved. It's essential to establish clear agreements and protocols for sharing risks and costs.
Additional reading: Correspondent Banking Relationship Risks Include:
What is Risk Pooling
Risk pooling is a strategy of combining several risks within a portfolio to reduce the possibility of significant loss arising from any one risk occurring.
This approach is essential for managing uncertainty in various sectors, including insurance, finance, and logistics. By spreading the potential impact of any singular risk event across a larger group, risk pooling often leads to more stable outcomes.
The risk pooling technique is used to efficiently manage uncertainty and minimize potential losses in business contexts such as insurance and supply chains. By combining diverse risks into a consolidated group, organizations can smooth out volatility and stabilize outcomes for more predictable financial performance.
Risk pooling in supply chain management refers to a centralized distribution system that caters to the requirements of all markets in a given region from a single warehouse. This allows for aggregation of demand across locations, making demand easier to forecast and reducing variability.
A centralized distribution system can lower inventory levels and costs by decreasing safety stock and average inventory requirements. For example, a company serving two markets can use a centralized system with a single warehouse instead of separate warehouses for each market.
By analyzing historical demand data, companies can compare the performance of decentralized and centralized distribution systems. For instance, a document highlights the benefits of centralization by comparing a decentralized system with two warehouses to a centralized system with a single warehouse.
Check this out: Single Car Accident Insurance Claim
Risk Pooling Techniques
Risk pooling in supply chain management is a technique that involves a centralized distribution system catering to the requirements of all markets in a given region from a single warehouse.
By aggregating demand across locations, demand becomes easier to forecast and variability is reduced, allowing for lower inventory levels and costs.
A centralized distribution system can make demand easier to forecast by aggregating it from multiple locations, which can be especially beneficial for companies with diverse markets.
This approach also reduces variability, making it easier to manage and predict inventory levels and costs.
For example, a company serving two markets can reduce variability by centralizing its distribution system, as shown in an analysis of historical demand data.
Calculations of reorder points, order quantities, and inventory levels indicate that the centralized approach can lead to decreased safety stock and average inventory requirements.
By minimizing variability, companies can stabilize outcomes and achieve more predictable financial performance, which is essential for efficient risk management.
Broaden your view: Levels of Operational Risk Management
Implementing Risk Pooling
Implementing risk pooling is a crucial step in supply chain management. By combining diverse risks into a consolidated group, organizations can smooth out volatility and stabilize outcomes for more predictable financial performance.
There are different pooling mechanisms to consider, including centralized control, decentralized control, or hybrid control. Centralized control can achieve higher efficiency and coordination if information is transparent and accurate across the supply chain.
To determine the best pooling mechanism, you need to assess the information availability, decision authority, and incentive alignment in your supply chain.
Intriguing read: Risk Control Report
Implement Mechanism
Implementing a suitable pooling mechanism is crucial for effective risk pooling. There are different pooling mechanisms, such as centralized control, decentralized control, or hybrid control.
Centralized control is ideal when information is transparent and accurate across the supply chain, allowing for higher efficiency and coordination. On the other hand, decentralized control is better suited when information is incomplete or distorted, enabling higher flexibility and autonomy.
Worth a look: Loss Control Consultant
Decentralized control can also be beneficial when dealing with lowly correlated demand, allowing for more localized decision-making. In contrast, centralized control is more suitable for highly correlated demand, enabling more efficient resource sharing.
The level of pooling also plays a significant role in risk pooling. The higher the level of pooling, the more resources are shared, but the more difficult it is to meet specific customer needs. This balance is critical, especially when dealing with high-value items like large appliances.
A good example of this is the strategy implemented by Zepto, where larger quantities of common models were pooled in central warehouses, while fast-moving or region-specific products were kept at micro DCs. This approach allowed them to meet customer expectations without incurring excessive storage costs.
Check this out: When Can an Insurance Company Refuse a Claim
Monitor and Adjust
Implementing risk pooling requires ongoing monitoring and adjustment to ensure optimal performance. This means tracking key performance indicators (KPIs) such as inventory turnover, fill rate, backorder rate, or total cost.
Discover more: Dogs of the Dow Performance History
Monitoring the performance of micro DCs handling large appliances is crucial, given the space constraints and high-value nature of the products. Gijo Kochuparambil John, a Delivery Hub Manager at Zepto, tracked metrics like delivery lead times, customer feedback, and inventory turnover.
To adjust the pooling strategy, you need to consider the feedback effects and dynamic interactions between different echelons in the supply chain. This includes the bullwhip effect, inventory inaccuracy, or order batching.
Gijo's team faced issues with stockouts due to misaligned forecasts during peak seasons. To address this, they adjusted their pooling strategy by increasing safety stock for certain models during high-demand periods.
Fine-tuning the pooling strategy can improve service levels and reduce the instances of delayed deliveries. For example, increasing safety stock for certain models during high-demand periods can help prevent stockouts.
Expand your knowledge: Cincinnati Insurance Stock
Identify Sources
Demand variability is a significant source of uncertainty in a supply chain, as it can be affected by various factors such as seasonality, promotions, trends, and customer preferences. This can lead to fluctuations in customer orders, making it challenging to manage inventory levels.
You might enjoy: Bcbs Customer Service Alabama
Supply variability is another major source of uncertainty, caused by disruptions or delays in the supply of raw materials, components, or finished goods. Quality issues, capacity constraints, natural disasters, or strikes can all impact supply chains.
Lead time variability is also a significant concern, as it can be influenced by factors such as transportation modes, congestion, weather, or customs. This can result in delays in moving inventory from one echelon to another.
In the context of managing demand variability, historical sales data can be a valuable tool for forecasting demand surges more accurately. By leveraging this data, supply chain managers can better anticipate and prepare for changes in demand.
Here are the main sources of uncertainty in a supply chain:
- Demand variability
- Supply variability
- Lead time variability
These sources of uncertainty can have a significant impact on inventory levels and service performance, making it essential to identify and quantify their effects on the supply chain.
Frequently Asked Questions
What are the four types of risk pooling methods?
There are four main types of risk pooling methods: no risk pool, unitary risk pool, fragmented risk pool, and integrated risk pool. These approaches vary in how they manage and distribute risk among individuals or groups.
Sources
- https://www.academia.edu/38382154/Supply_Chain_Management_Risk_pooling
- https://www.studysmarter.co.uk/explanations/business-studies/actuarial-science-in-business/risk-pooling/
- https://www.linkedin.com/advice/0/what-best-practices-risk-pooling-multi-echelon
- https://link.springer.com/article/10.1007/s10255-009-8830-x
- https://www.slideshare.net/SaurabhPratap18/1riskpoolingppt
Featured Images: pexels.com