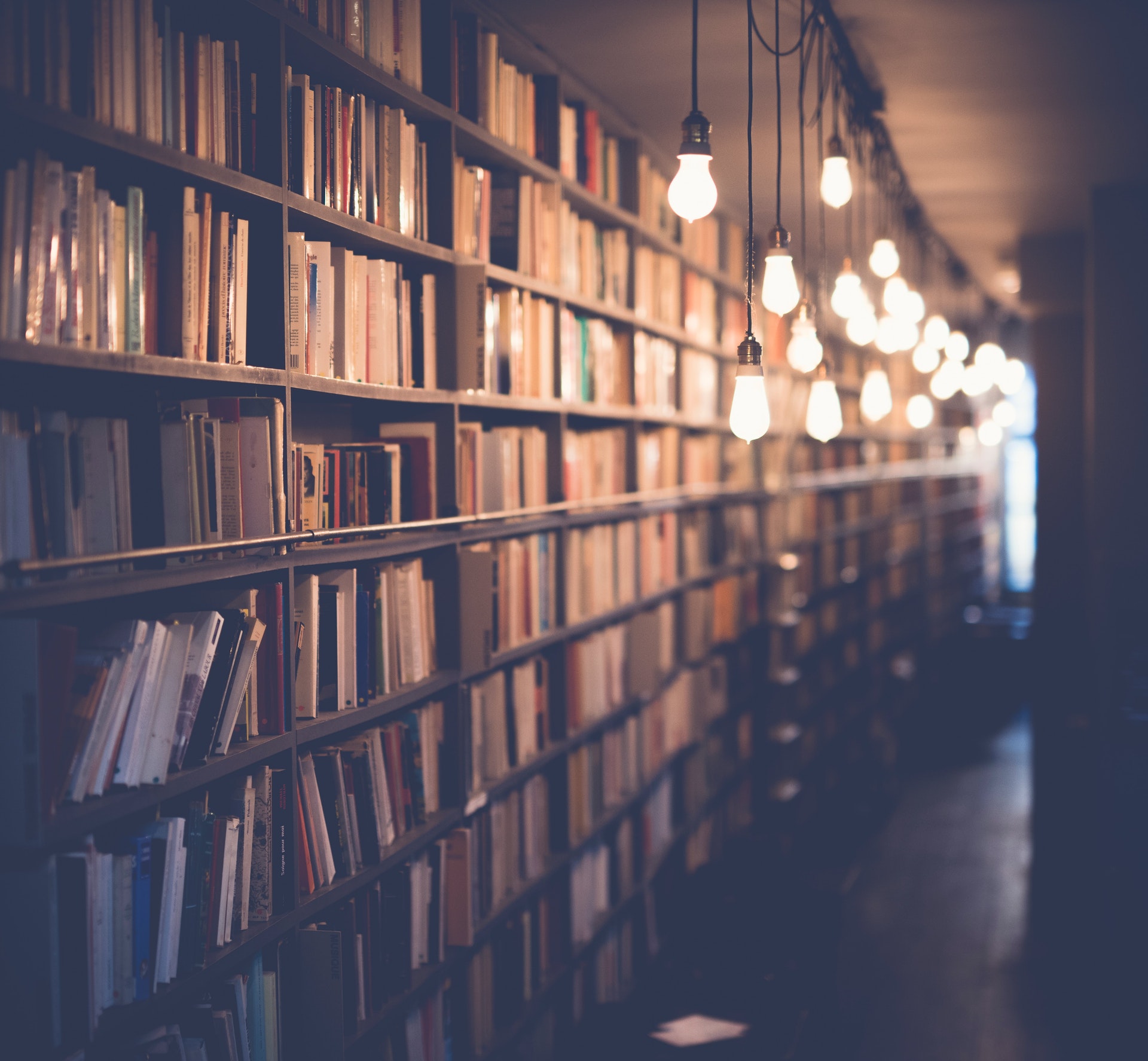
Removing moisture from air compressors is essential to keeping the equipment in good condition and your air supply pure. Fortunately, there are a few easy steps you can take to ensure that your air compressor does not become damaged due to excess moisture.
1. Install a desiccant system for use with the compressed air supply: Most desiccant systems are connected directly to the discharge service line from an air compressor and work by drawing out moisture from the compressed air as it passes through their filtering media or beads. This can drastically reduce both overall humidity and condensation levels in an enclosed environment such as a workshop or garage where an excessive amount of moisture may already be present. Desiccants should be replaced regularly in order to keep them efficient, so make sure that you check the manufacturer’s recommendations on how often this needs done.
2. Invest in an oil/air separator with drain valve: An oil/air separator is designed specifically for removing water vapor and oil residue created by an internal combustion engine before leaving into atmosphere as exhaust gas, but these devices also have application when used on an independent compressed air system too – especially those using reciprocating compressors – helping keep maintenance down and ensuring no unneeded buildup of contaminants occurs on valves and other wear surfaces within the compressor itself like pistons or connecting rods where serious mechanical damage could occur otherwise over time due to corrosion. The separators continuously trap any condensed liquid matter within its reservoir chamber, making disposal of this material much easier than if it were allowed free flow back into ambient environment
3. Manually drain excess accumulations of water after every use & maintain proper operating temperature settings: To keep things safe even further adequate amounts maybe regularly need manually drained out between uses regardless whenever possible given most models feature either some form type external valve that rotates ball downwards during operation allowing liquids slowly drip down below its safety point until nothing more finds left inside; while also adhering closely any recommended temperature settings given these help dissipate heat faster more efficiently rather than merely running cold cycle setting throughout entire day which may result high buildups build up shortly after long hours continuous running cycles cause lack appropriate ventilation within enclosure around unit itself.. Just remember make sure try open tank area where possible let extra pressure usually built release too along draining off everything else there just directly away safe place far enough nearby avoid contamination aspects too!
By taking all these steps together, you will find yourself with a much dryer storage space for your compressed equipment – ensuring both cleanliness and longevity alike throughout its operational use!
Discover more: Identify Moisture Ants
What is the best way to dehumidify an air compressor?
If your air compressor is suffering from high levels of humidity, it can cause a lot of damage to your tools and equipment. Fortunately, there are several ways you can effectively dehumidify an air compressor to prevent this.
Firstly, you want to avoid increasing the temperature in the room where the air compressor is located. While warmer temperatures typically reduce humidity levels quicker than colder temperatures, this can also lead to an increase in condensation forming inside the machine – leading to more corrosion damage. As such, we suggest keeping temperature steady by using fans or other ventilation solutions instead.
Secondly, you may want to consider investing in a commercial-grade dehumidifying unit for your air compressor. These units come with systems for both cooling down and dehumidifying incoming airflow before releasing it back into the environment. This ensures that wherever possible any moisture is removed from the area before being released – helping keep everything dry and free from rusting or corroding over time.
Finally, some companies now also offer dehumidifying oil – specially designed lubricants that contain silicates which absorb atmospheric moisture within a closed system as they circulate inside an air compressor’s motor and/or cylinder head components; helping promote a drier internal environment overall which further guards against corrosion damage wreaking havoc internally within a machine’s components over time due accumulated moisture build-up..
By following these simple steps in addition with regular cleaning routine maintenance; owners of an air compressors will be able benefit from improved longevity and overall reduced wear & tear through better management of its operating environment via smarter preventative measures when combatting any issues caused by unwanted additional moisture creeping into its work areas..
For your interest: Ac Compressor Turning
How can I reduce moisture levels in my air compressor?
If you are finding that the moisture levels of your air compressor are too high, it is important to take steps to reduce them. Here are 5 tips for reducing the moisture levels in an air compressor.
1. Dryer: A dryer can be used to reduce moisture levels by removing water vapor prior to entering the air compressor system. Using one of these can help keep your moisture level low and prevent your system from becoming too wet and filled with water droplets that could damage its parts over time.
2. Drain Valve: Regularly draining any excess condensate (water) from your air compressor's drain valve can help remove a substantial amount of moisture and keep it away from working parts located inside the machine, thus helping you maintain a lower level overall than would otherwise be present without doing this regularly.
3. Separator: Installing a separator after drainage can also help keep some of the dirt particles or oils in suspension out of the compressed air stream, thus helping you maintain an even drier environment for your machine parts during operation and continuing maintenance schedules.
4. Control Air Leaks: You should make sure all hoses, fittings and gaskets on all types of equipment connected to or attached near your air compressor system have no unnecessary lead holes or other gaps so as not to allow outside moist environments enter into it while running– ultimately this will affect residuals in both pressures circulation rate performance due improper adjustment seals such as rods packing fit-up check valves failing when combinations occur– either on output lines reservoir tanks chemical purgers etc., causing serious effects if not settled quickly being tightly sealed!
5 Filtration: Investing in a filtration unit that uses specialty cartridges designed specifically for oil & water vapor removal can go a long way towards keeping things properly contained within compressors while they run– while this separate device comes at additional cost upfront when selecting good variety with single coalescing filters sizes up their fingertips change outs highly contribute prolonged life systems dealt experiences gradually gain investor maintenance controls useful information gather toward making better decisions those related professional upkeep!
Worth a look: Install Water Separator
What is the most effective method to remove excess humidity from an air compressor?
When using an air compressor to power pneumatic tools, one of the challenges can be controlling the amount of humidity in the air. Excess humidity builds up inside your compressor's tank and can lead to adhesion problems, corrosion and even inadequate power delivery. Fortunately, with a few simple solutions, you can remove excess humidity from your air compressor quickly and effectively.
The first step is to make sure you’re using an oil-free portable air compressor that has either built-in or optional features designed to prevent condensation build-up. Your manual should tell you which options are available for your machine – many provide automatic drain valves which open periodically to release any water collected in the tank. Alternatively, if specifically available for your model, a refrigerated dryer removes moisture from compressed air by cooling it enough so condensation forms; this moisture is then easily collected in a separate container or released back into the ambient environment once cooled below dewpoint temperature.
If those solutions aren’t available on your machine, regular maintenance of activity becomes even more important: Before each use check for moisture inside both hoses leading from and back into the unit as well as check what is draining out (at least once every 8 hours when running 24/7). Fit quality ‘anti-corrosion’ filters at start/end point of system – aftermarket units often fit designed specifically with anti-condensation capabilities OR installing a ‘grain adjuster’ (desiccant type) filter before compressing will help adsorb any airborne moisture before it has chance to reach compressor's tank during charge phase = procedure should assist slow down accumulation phase without drying out incoming too much! Lastly don't forget your safety procedures too - regularly inspect pressure relief valve and replace if need be due2excessive corrosion buildup not detectable by sight only!
By taking these steps ahead and addressing issues directly related with protection against excess humidity into account when choosing an effective method for removing this issue from an air compressor system; regardless whether purchasing new or retrofitting existing one - operators should achieve longer lasting performance & efficiency gains form their compressed work routine activities undertaken throughout day 2day operations.
On a similar theme: Remove System Ui
What steps can be taken to reduce condensation in an air compressor?
Condensation in an air compressor can be a headache to deal with and can reduce the longevity and efficiency of your equipment. Fortunately, there are steps that you can take in order to reduce the condensation and prolong the life of your compressor.
One easy step you can take is to install an air filter or oil separator. This will help filter out any moisture or oil buildup before it reaches your compressor, potentially reducing condensation down the line. A more expensive solution would be to invest in an after-market desiccant dryer system. This attaches to the exit port on your air compressor, acting like a sponge by absorbing any remaining moisture within your compressed air before it exits out into other parts of your equipment.
Another way you could reduce condensation is by keeping an eye on those temperature levels. By running a cooler temperature within specified parameters from manufacturer guidelines, you'll avoid overheating which helps decrease moist environments forming inside of your unit. You could even invest in cooling fans for additional assurance on maintaining those temperatures as best as possible throughout operation hours.
Lastly, another strategy worth utilizing would be purchasing corrosion inhibitors either separately or included with lubrication solutions from suppliers such as Grainger parts. Corrosion inhibitors soak into metal surfaces inside of these units and prevent damaging rusting due to long-term humidity exposure without interfering with their mechanics themselves.. In turn, this extends their shelf-life substantially allowing for that extra bit of longevity every owner desires!
Expand your knowledge: Remove Rotoscope Filter
Are there any measures I can take to reduce moisture levels in my air compressor?
If you're dealing with high moisture levels in your air compressor, don't worry! This is a common problem and it can often be solved by taking the right preventative measures. Here are some tips to help reduce the moisture content in your air compressor:
1. Install an Air Filter - An air filter will trap any airborne debris entering the system, which can help keep moisture levels down. Make sure to regularly check and clean or replace your filter as needed for maximum efficiency.
2. Drain Your Compressor Regularly - Another great way to reduce moisture buildup is to regularly drain your compressor's tank and discharge pipes at least once every few days. Be sure to properly dispose of the water that comes out so that it doesn't end up inside the compressor again!
3. Use an Air Dryer - An air-dryer helps remove residual humidity from compressed air before it enters your machinery or tools, providing a much drier working environment with lower operating costs and helping lower maintenance costs too! Many dryers can be piped directly into your existing compressor's lines for easy installation and use.
4. Use Oil Separators - If you find that oil is contaminating your air piping, an oil separator could be a good solutionby separating particles from liquids before they enter into any type of machine using compressed gas or vapors, such as auto engines.. It's important know how many gallons per minute (gpm) or liters per minute (lpm) of oil-containing liquid needs to separate from incoming airflow prior specifying proper oil separation technology for installation between compressors and other related parts of equipment within a network of systems requiring clean filtered compressed gases/vapors/air emissions within a workplace environment. Keep both cleaning intervals in mind here; either monthly or quarterly checks depending on how intensively system is used.
By following these tips you should notice immediate improvement in both air quality output form the compressed gas delivery system as well as energy efficiency improvements when considering reduced maintenance requirements due lower fluid contamination risks posed by increased presence of lubricants introduced by broken seals at different screws located around all sides off valve cover containing individual valves inside hose connections between all machines along assembly line setup where ever large volumes off mass process occurs overtime day after day involving numerous equipment being operated continuously without any breaks during production process while aiming optimal performance metrics during manufacturing processes such industrial operations require special monitoring protocol where regular audits take place frequently like every 2-3 weeks when possible. Hope this helps anyone struggling with excessive moisture buildup problems caused due lack off preventative measures being taken on regular basis – happy compressing!!
Consider reading: Clean Idle Air Control Valve
What type of maintenance is necessary to control the humidity in an air compressor?
Maintaining the humidity in an air compressor is vital in keeping it running smoothly and efficiently. Too much moisture entering into the system can cause a number of problems, such as increased wear on components, decreased performance, and shorter lifespan of your air compressor. Here are five easy steps you can take to maintain and control the humidity inside your air compressor:
1. Change the air filter regularly - A dirty air intake filter can greatly impede proper airflow and increase moisture buildup inside your tank. Make sure to check it monthly and change it when you notice any dirt buildup or clogging.
2. Opt for sealed tanks associated with wet-armature type compressors - On these types of compressors, compressed gas is contained within tanks that feature rubber membranes that help to trap moisture as well as dust particles during operation. This helps keep them from entering your system thereby reducing corrosion and allowing for greater efficiency levels within your system as well as better overall output from pumps/engines utilized by some compressors today
3. Install humidifiers - If you find yourself dealing with particularly humid weather patterns in either residence or workplace, investing in a humidifier could be beneficial in both controlling/adjusting levels within moist environments more effectively along with removing possible hazards involving condensation-related issues connected with airborne gas etc.. This will also reduce instances where piping may begin rusting due to consistently high amounts of water vapor present at any given time leading towards potential operational issues if left unchecked
4. Consider purchasing an atmospheric regulator – Restricting environment temperature often goes hand in hand when trying specifically control water vapor levels especially without spending too much on either equipment upgrades or personnel because these things work together quite nicely 5. Adjust temperature settings appropriately – Just being mindful about what each setting does has its advantages when trying reduce instances where residual moisture might remain behind after use which results not only potential hazardous situations but wear on components as well
Suggestion: Makes Napa Air Compressors
Sources
- https://fluidairedynamics.com/blogs/articles/get-rid-water-compressed-air-system
- https://www.youtube.com/watch
- https://www.compresstech.com.ph/2020/08/28/ways-remove-moisture-from-compressed-air/
- https://compressorservices.net/5-ways-remove-moisture-compressed-air/
- https://toolbeltguru.com/how-to-clean-an-air-compressor/
- https://blog.airlinehyd.com/air-line-moisture-removal
- https://toolsideas.com/how-to-prevent-moisture-in-air-compressor/
- https://www.youtube.com/watch
- https://bjbeneair.com/dry-compressed-air/
- https://www.youtube.com/watch
- https://indoair.com/blog/removal-process-of-moisture-from-compressed-air-system/
- https://www.sunbeltsales.co.uk/news-2/a-guide-to-compressor-and-desiccant-dehumidifiers-2
- https://bestdehumidifierchoice.com/blog/how-does-a-compressor-dehumidifier-work/
- https://toolsideas.com/how-to-remove-water-from-air-compressor/
- https://compressors.matteicomp.com/blog/how-to-fight-condensation-in-your-air-compressor
Featured Images: pexels.com