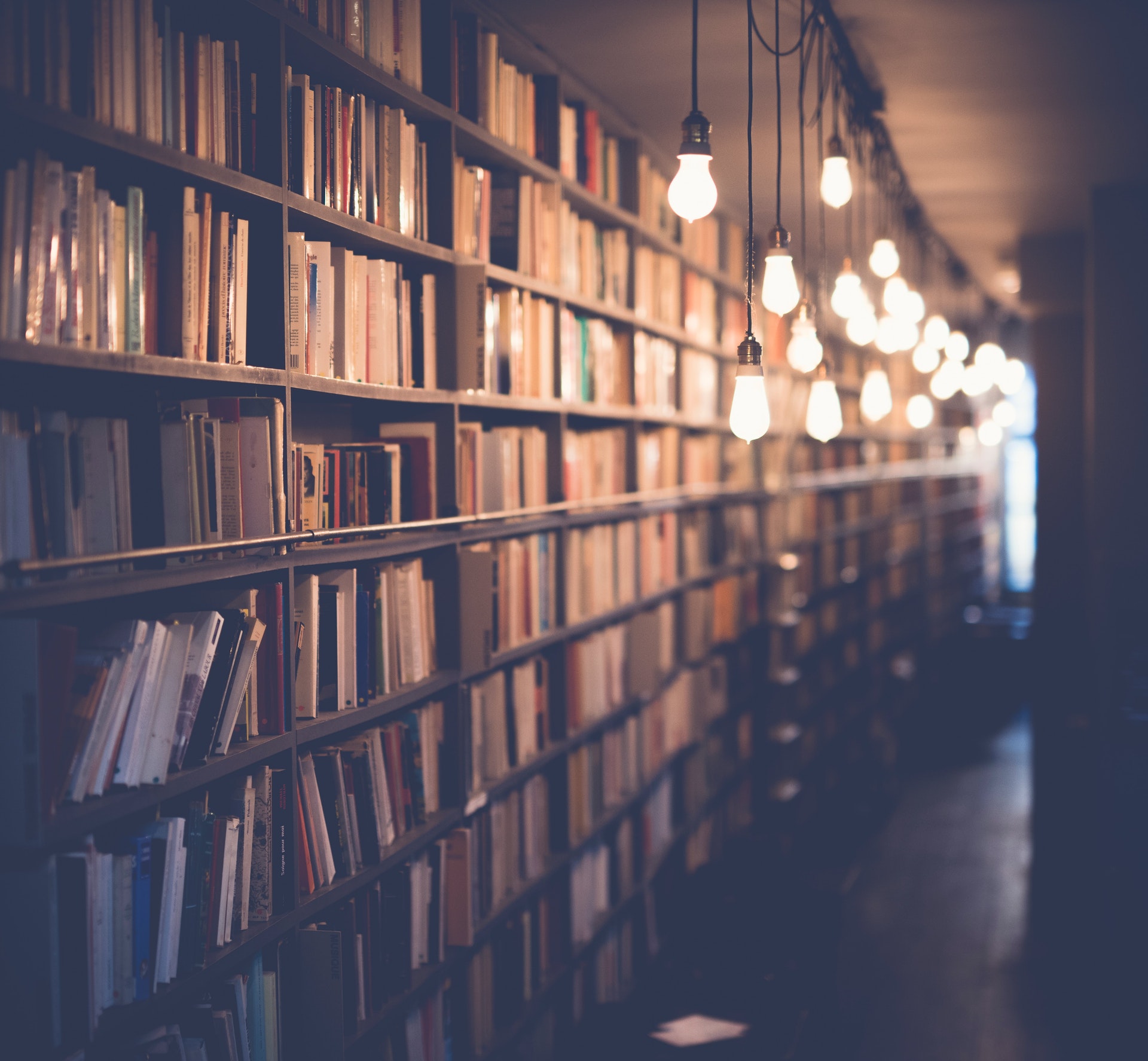
Punching machines are a type of machinery used for punching holes in various materials. The most common type of punching machine is the turret punch press, which is used to create holes in sheet metal. Turret punch presses work by holding a sheet of metal in a clamp, and then using a punching tool to punch holes through the metal. The punching tool is typically a cylindrical tool that is rotated at high speeds, and it has a sharp point that punches through the metal.
Punching machines can also be used to create holes in other materials, such as plastics and wood. There are different types of punching machines that are designed for different materials. For example, there are plastic injection molding machines that are used to create holes in plastics. These machines work by injection hot plastic into a mold, and then using a punch to create a hole in the plastic.
Punching machines are used in a variety of industries, such as the automotive industry, the electronics industry, and the construction industry. Punching machines can be used to create a variety of products, such as car parts, electrical components, and construction materials.
You might like: Frozen Yogurt Machines Work
How do you choose the right punching machine for your application?
There are many different types of punching machines on the market and choosing the right one for your application can be a difficult task. Here are a few factors to consider when selecting a punching machine:
1. The type of material you will be punching.
2. The thickness of the material you will be punching.
3. The size of the punches you will need.
4. The amount of force required to punch the material.
5. The speed at which the punching machine will operate.
6. The size and weight of the punching machine.
7. The power source for the punching machine.
8. The warranty and service agreement offered by the manufacturer.
9. The price of the punching machine.
10. The reviews and ratings of the punching machine.
11. The lead time for the punching machine.
12. The shipping and return policy of the punching machine.
13. The customer service of the punching machine.
14. The support offered by the manufacturer.
15. The accessories included with the punching machine.
16. The available options for the punching machine.
17. The compatibility of the punching machine with your existing equipment.
18. The training and support offered by the manufacturer.
19. The ease of use of the punching machine.
20. The safety features of the punching machine.
When considering these factors, it is important to consult with an expert in the field of punched-machine selection. An experienced professional can help you understand the features and benefits of each type of machine and help you choose the one that is best suited for your specific application.
What are the benefits of using a punching machine?
Punching machines are devices that are used to create holes in materials such as paper, cloth, metal, and leather. They come in a variety of shapes and sizes, and can be hand-held or mounted on a table or stand.
Punching machines offer several benefits over other methods of creating holes in materials. They are faster, more precise, and can create multiple holes in a single pass. Additionally, they can be used to create patterns of holes, such as those used for buttonholes or eyelets.
Punching machines can be used for a variety of purposes, such as creating buttonholes in clothing, holes for eyelets in shoes or belts, or even for decorative purposes such as punching patterns in paper. Their versatility makes them a valuable tool for anyone who often needs to create holes in materials.
You might like: Bread Machines Worth
How do you operate a punching machine?
A punching machine is a specialized machine used to punch holes in materials such as metal, paper, or plastic. There are many different types of punching machines, each designed for a specific type of punching. The most common type of punching machine is the turret punch, which is used to punch holes in sheet metal.
Turret punches are classified by the size of their throat, which is the distance from the center of the punch to the edge of the die. The throat size of a turret punch determines the maximum size of the punch that can be used with that machine. The most common throat sizes are 6 inches (15 cm), 9 inches (23 cm), and 12 inches (30 cm).
To operate a turret punch, the operator first sets the desired punch size and die size on the punch control panel. The operator then loads the sheet metal into the machine, making sure that the sheet is properly aligned with the die. Once the sheet is in place, the operator activates the machine by pressing the start button.
The turret punch will then move the sheet metal into the die and punch the desired hole. Once the hole is punched, the turret punch will eject the sheet metal and return to the home position. The operator can then remove the sheet metal and load another sheet into the machine.
You might enjoy: Counter Drain Punch
What are the safety precautions you need to take when using a punching machine?
In order to use a punching machine safely, there are a few key safety precautions that you need to take. First and foremost, always make sure that the machine is properly secured and anchored before using it. Secondly, never put your hand or fingers near the moving parts of the machine while it is in operation. Finally, always wear appropriate safety gear, including gloves and eye protection, when using a punching machine.
When setting up the machine, always make sure that it is properly secured and anchored. The best way to do this is to use the bolts that come with the machine to anchor it down. If you are using the machine on a table, make sure that the table is also properly secured. Once the machine is properly secured, you can then proceed to the next safety precaution.
Never put your hand or fingers near the moving parts of the machine while it is in operation. This includes the area around the die, the area where the punch comes down, and the area where the material is being ejected. If you must reach into any of these areas while the machine is running, make sure that you shut off the power to the machine first.
Always wear appropriate safety gear, including gloves and eye protection, when using a punching machine. Gloves will protect your hands from the sharp edges of the material being punched, and eye protection will defend your eyes from debris that could be ejected from the machine. Wearing both gloves and eye protection is the best way to stay safe while using a punching machine.
By following these safety precautions, you can safely use a punching machine without putting yourself or others at risk. Always remember to secure the machine before use, keep your hands and fingers away from moving parts, and wear proper safety gear. With these precautions in mind, you can enjoy the benefits of using a punching machine without worry.
What are the different types of punches that can be used with a punching machine?
A punching machine is a mechanical device that can be used to apply force to a workpiece. The machine may be classified according to the type of punch that is used. The four most common types of punches are:
1. Flat punch: This punch has a flat, slightly radiused face. It is used to punch through material, such as a piece of sheet metal.
2. Round punch: This punch has a cylindrical face with a sharp edge. It is used to make round holes in material, such as for mounting a knob or for wire termination.
3. Diamond punch: This punch has a conical face with a diamond-shaped tip. It is used to make precise, clean holes in material, such as for electronic connectors or for display screen mounting.
4. Form punch: This punch has a custom-shaped face that is used to make a specific shape in material, such as a keyhole or a slot.
What are the different types of materials that can be punched with a punching machine?
When it comes to punching machines, there are two types of materials that can be used: ferrous and non-ferrous. Each type of material has its own unique set of characteristics that make it ideal for certain applications. Here is a closer look at the two types of materials:
Ferrous materials are those that contain iron. This includes metals like steel and cast iron. Ferrous materials are known for their strength and durability. They are often used in applications where strength and wear resistance are important, such as in the automotive and construction industries.
Non-ferrous materials are those that do not contain iron. This includes metals like aluminum, brass, and copper. Non-ferrous materials are known for their corrosion resistance. They are often used in applications where corrosion resistance is important, such as in the chemical and food processing industries.
Both ferrous and non-ferrous materials have their own unique set of advantages and disadvantages. The type of material that is best for a particular application will depend on the specific requirements of that application.
How do you troubleshoot a punching machine?
When troubleshooting a punching machine, there are a few things to keep in mind. First, check the machine for any visible damage. Next, check to see if the machine is properly plugged in and that all the connections are secure. Finally, check the Settings menu to ensure that the machine is set to the correct mode and that all the settings are correct. If the machine is still not working properly, reset it by turning it off and then on again.
How do you maintain a punching machine?
A punching machine is a type of machinery used to perforate materials such as paper, leather, or fabric. There are various types of punching machines, each with its own specific set of features and capabilities. However, all punching machines share some common elements that must be maintained in order for the machine to function properly.
The first and most important element of a punching machine is the die. The die is the metal plate with the desired shape cut out of it. This is what actually does the cutting or punching. The die must be kept sharp and clean in order to function properly. If the die becomes dull or dirty, it will not cut as cleanly and may even tear the material it is trying to cut.
Another important element of a punching machine is the anvil. The anvil is the metal plate that the die cuts into. It is important to keep the anvil clean and free of debris so that the die can cut properly. If the anvil is dirty or damaged, it can cause the die to chip or break.
The third important element of a punching machine is the press. The press is the portion of the machine that actually applies pressure to the die to make it cut through the anvil. The press must be kept in good working condition so that it can apply the proper amount of pressure to the die. If the press is not working properly, the die may not cut properly or may not cut at all.
In order to maintain a punching machine, it is important to perform regular maintenance on all of its elements. This includes sharpening the die, cleaning the anvil, and oiling the press. Additionally, it is important to keep the machine itself clean and free of debris. Doing so will help to prolong the life of the machine and keep it running smoothly.
Related reading: Press Machine
Frequently Asked Questions
How does the punching work?
The punching works by pushing the sheet against the matrix. This causes the punching machine to create holes in the sheet according to the programmed lengths of the bars.
Does the arcade punching machine work?
Yes, the arcade punching machine is a functional tool that can be used to administer acceleration to the punching bag.
How does a CNC punch press work?
A CNC punch press is a machine that uses high-speed rotational movements to create pre-shaped holes in a workpiece. The punch ram is mounted on an arm that is suspended from the ceiling or movable slide. As the punches move down the ram, they push the workpiece through the die, creating a hole in the workpiece.
What are the parts of a punching machine?
There are two main parts to a punching machine: the tool holders and the punches. The tool holders are large, rigid frames that house all of the quick change tools for the punching machine. The punches are the smallest pieces of equipment in a punching machine, and they travel along the length of the tool holder in order to create holes in the metal.
How does metal punching work?
The principle is relatively simple: The sheet metal being punched is sandwiched between the punch and a die. The punch moves downward and into the die.
Sources
- https://themechanicalengineering.com/punch-press-machine/
- https://www.youtube.com/watch
- https://www.machinemfg.com/how-to-choose-punch-press/
- https://www.youtube.com/watch
- https://stamping.wiki/advantages-of-using-cnc-punching-machine/
- https://machinetools.bhavyamachinetools.com/benefits-of-an-aluminium-busbar-punching-machine/
- https://www.youtube.com/watch
- https://www.wmtmetal.com/do-you-know-the-safety-operation-procedures-of-punching-machines/
- https://www.skical.org/how-to-choose-the-perfect-punching-bag-for-your-needs/
- https://ventilengineers.com/benefits-of-hydraulic-punching-machine/
- https://www.machinemfg.com/punching-machine/
- https://www.youtube.com/watch
- https://www.platmekano.se/en/faq/punching/what-are-the-benefits-of-sheet-metal-punching/
- https://kingreal.org/industry-news/what-are-the-advantages-of-a-fully-automatic-punching-machine.html
- https://coil-slitting.com/faq/how-to-choose-the-right-automatic-pipe-punching-machine.html
Featured Images: pexels.com