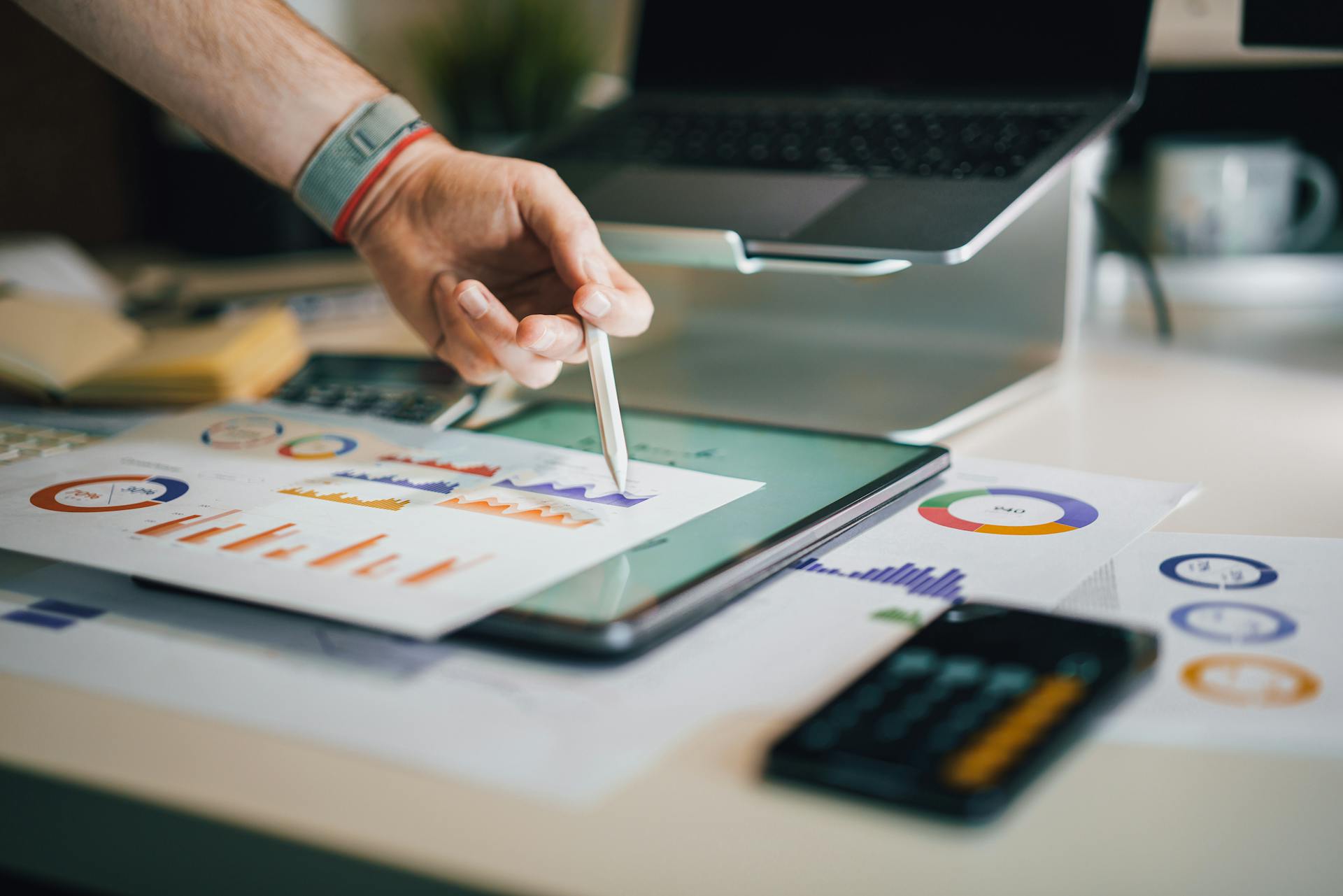
External failure cost is a crucial aspect of quality improvement. It's the cost of fixing defects after they've been shipped to customers.
According to studies, external failure cost can be as high as 80% of the total cost of quality. This is a staggering number that highlights the importance of catching defects early.
Companies that focus on quality improvement can significantly reduce their external failure cost. By implementing quality control measures, they can catch defects before they reach customers.
For example, a company that produces electronic components can reduce its external failure cost by implementing a rigorous testing process. This ensures that defective components are caught and fixed before they're shipped out.
For more insights, see: External Risk
What is External Failure Cost
External failure costs are expenses incurred by a company due to product or service defects discovered after delivery to customers.
These costs are a direct result of poor quality after delivery, which can lead to customer dissatisfaction, damage to brand reputation, and financial instability.
External failure costs include expenses such as warranty claims and customer support expenses, which can be a significant burden on a company's finances.
Some examples of external failure costs include complaints, repairing goods and redoing services, warranties, customers' bad will, losses due to sales reductions, and environmental costs.
These costs serve as a tangible indicator of the expenses incurred due to post-delivery quality issues, making them an important metric for businesses to track and improve upon.
A company can reduce external failure costs by improving production processes, customer service, and overall product and service quality, which can lead to enhanced customer loyalty and trust.
A fresh viewpoint: External Debt Collectors
Types of External Failure Cost
External failure costs are a significant concern for businesses, and understanding the different types can help you identify areas for improvement. External failure costs are costs that occur after a product or service has been delivered to a customer.
Customer complaints handling is one of the most common external failure costs. This includes the resources used to address and resolve customer complaints. You can expect to see a significant increase in call center activity and support team workload.
If this caught your attention, see: Which of the following Is Not an External Failure Cost
Product returns are another common external failure cost. This includes the costs of processing and handling returned goods. If you're not careful, product returns can quickly add up and become a significant burden on your business.
Warranty claims are also a major external failure cost. This includes repairs or replacements under warranty agreements. A well-designed warranty program can help minimize these costs, but it's essential to have a clear understanding of what's covered and what's not.
Product recalls are a costly and time-consuming external failure cost. This includes the costs of identifying and retrieving defective products. Product recalls can have a significant impact on your brand reputation and customer loyalty.
Liabilities and legal costs are also a type of external failure cost. This includes the costs of settlements or judgments for product liability claims, attorney fees, and regulatory fines and penalties. These costs can be devastating to a business, so it's essential to take proactive steps to prevent them.
Loss of reputation is a long-term external failure cost. This includes the negative impact on brand image and customer loyalty, as well as the costs of marketing and public relations to rebuild trust. A damaged reputation can be difficult to recover from, so it's essential to prioritize customer satisfaction.
Discover more: Business Insurance for Llc Cost
Loss of sales is another external failure cost. This includes the cost of decreases in future sales due to negative word-of-mouth, as well as lost revenue from dissatisfied customers switching to competitors. A single unhappy customer can quickly spread the word and impact your business.
Customer compensation is a significant external failure cost. This includes the cost of compensation for damages caused by defective products. It's essential to have a clear process in place for handling customer complaints and providing compensation when necessary.
Investigation costs are also a type of external failure cost. This includes the costs incurred to analyze the root causes of external failures. Understanding the root cause of a failure can help you prevent similar failures in the future.
Here are the most common types of external failure costs:
- Customer complaints handling
- Product returns
- Warranty claims
- Product recalls
- Liabilities and legal costs
- Loss of reputation
- Loss of sales
- Customer compensation
- Customer support costs
- Investigation costs
Understanding External Failure Cost
External failure costs are expenses incurred by a company due to product or service defects discovered after delivery to customers. These costs can range from warranty claims and customer support expenses to potential legal fees arising from dissatisfaction.
External failure costs serve as a tangible indicator of the expenses incurred due to post-delivery quality issues. They highlight the financial impact of poor quality after delivery, prompting improvements in production processes, customer service, and overall product and service quality.
These costs include handling customer complaints, providing customer support, issuing refunds or replacements, managing warranty claims, and potentially dealing with legal issues or fines due to non-compliance. The intangible cost associated with damage to the brand's reputation and customer trust can also be significant.
Explained
External failure costs are expenses incurred by a company due to product or service defects discovered after delivery to customers. These costs can be significant and have a direct impact on customer satisfaction, brand reputation, and financial stability.
Examples of external failure costs include complaints, repairing goods and redoing services, warranties, customers' bad will, losses due to sales reductions, and environmental costs. These costs can be substantial and may include direct expenses such as labor, materials, and logistics, as well as intangible costs like damage to a company's reputation and customer trust.
Broaden your view: Direct Costs
Businesses can use external failure costs to identify quality issues and prioritize process improvements. By tracking and analyzing these costs, companies can make informed decisions about product recalls, re-engineering processes, or discontinuing items prone to quality issues.
Here are some key factors to consider when understanding external failure costs:
- Direct expenses incurred in addressing the problem, such as labor, materials, and logistics
- Intangible costs associated with damage to a company's reputation and customer trust
- Damage to a company's reputation and customer trust can lead to negative word-of-mouth, social media backlash, and decreased customer loyalty
By understanding external failure costs, businesses can take proactive steps to minimize these costs and improve overall quality and customer satisfaction.
Internal Cost
Internal failure costs are incurred during the production process or before the product reaches the customer. These costs arise from detecting defects internally within the organization.
Internal failure costs are associated with identifying and correcting defects within the company's production or operational processes before the product is shipped or delivered. This can include costs such as the cost of correcting defects and liability.
Mitigating internal failure costs involves proactive measures such as stringent quality checks throughout production. This can help reduce the likelihood of defects being shipped to customers.
Some examples of internal failure costs include the cost of quality, production externality, and warranty expense.
A unique perspective: Internal Engine Failure Cost
Calculating External Failure Cost
Calculating External Failure Cost is a crucial step in understanding the financial impact of post-delivery quality issues. External failure costs in business are expenses incurred by a company due to product or service defects discovered after delivery to customers.
To calculate external failure cost, consider the expenses incurred due to warranty claims and customer support expenses. These costs can range from simple repairs to complex replacements, and even potential legal fees arising from dissatisfaction.
The key is to identify the tangible indicators of external failure cost, such as warranty claims and customer support expenses. This will give you a clear picture of the expenses incurred due to post-delivery quality issues.
Here are some examples of external failure costs to consider:
- Warranty claims
- Customer support expenses
- Potential legal fees arising from dissatisfaction
By calculating external failure cost, you can gauge the repercussions of poor quality after delivery and prompt improvements in production processes, customer service, and overall product and service quality.
Managing External Failure Cost
External failure costs are a significant concern for manufacturers, and it's essential to understand how to manage them effectively.
The 1:10:100 rule suggests that the costs of dealing with defects rise exponentially as products near shipment, with inspection costs $1 per unit, rectifying nonconformance rising to $10, managing CAPA to $100, resolving complaints to $1,000, and dealing with recalls to $10,000.
Investing in prevention is the most effective way to ensure that nonconforming output never reaches the customer and incurs external failure costs.
According to Gartner's 2022 Total Cost of Quality Survey, manufacturers are putting 52% of their total cost of quality into appraisals and internal failure costs, such as rework and scrap.
This allocation may seem sensible, but it's essential to prioritize customer satisfaction and focus on rectifying issues that directly impact customers.
The 1:10:100 rule highlights the importance of investing in prevention to avoid costly external failure costs.
Here's a breakdown of the 1:10:100 rule:
Frequently Asked Questions
What does the external failure cost not include?
External failure cost does not include expenditures incurred before the sale of products, such as inspection costs. It only covers costs that arise after the sale.
Sources
- https://www.accountingtools.com/articles/external-failure-costs
- https://www.wallstreetmojo.com/external-failure-cost/
- https://www.alisqi.com/en/guides/cost-of-quality/external-failure-costs-paying-the-price-of-customer-dissatisfaction
- https://www.isixsigma.com/financial-analysis/cost-quality-not-only-failure-costs/
- https://www.accountingtools.com/articles/failure-costs
Featured Images: pexels.com