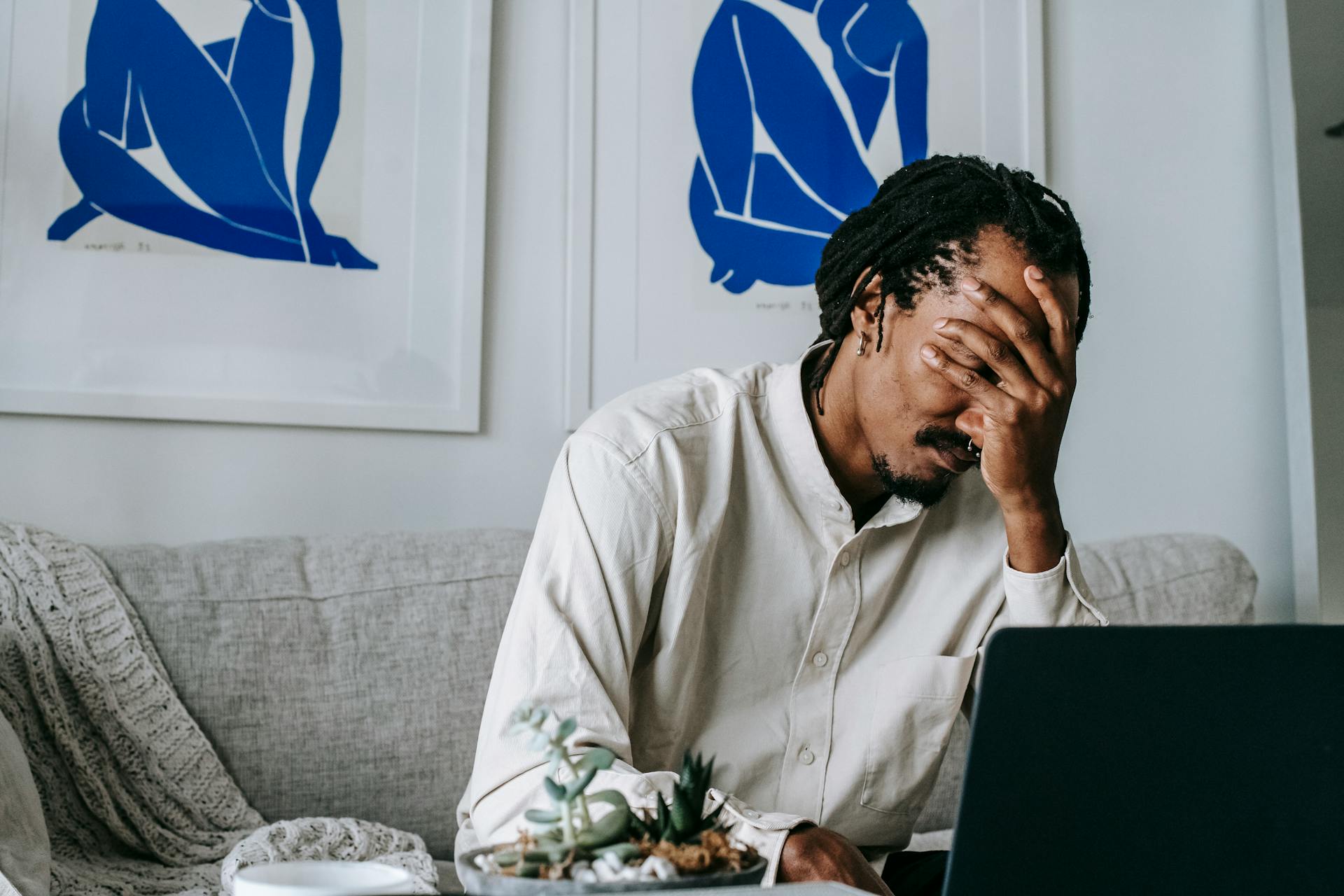
Costs associated with external failures can be significant and far-reaching.
In many cases, these costs can be directly attributed to the end user, such as the cost of repairing or replacing a defective product.
External failure costs can also include the cost of warranty claims, which can be a substantial burden on a company's bottom line.
These costs can be unpredictable and difficult to anticipate, making them a major concern for businesses.
If this caught your attention, see: Direct Costs
What are External Failure Costs?
External failure costs are expenses incurred by a company due to product or service defects discovered after delivery to customers. These costs can be substantial and have a significant impact on customer satisfaction, brand reputation, and financial stability.
Examples of external failure costs include complaints, repairing goods, warranties, customers' bad will, losses due to sales reductions, and environmental costs. These costs can arise from various issues, such as defects in the product or service, inadequate customer support, or failure to meet customer expectations.
For more insights, see: Average Refi Closing Costs
External failure costs are often considered a reactive measure, as they respond to problems that have already occurred. However, they can also serve as a catalyst for improvement, prompting companies to reassess their quality control processes and production methods.
Businesses can use external failure costs to identify areas for improvement and develop proactive measures to prevent similar issues in the future. By analyzing these costs, companies can gain valuable insights into their operations and make informed decisions about product recalls, re-engineering processes, or discontinuing items prone to quality issues.
To illustrate the various types of external failure costs, consider the following breakdown:
By understanding and addressing external failure costs, companies can reduce their financial losses, improve customer satisfaction, and enhance their brand reputation.
Examples of External Failure Costs
External failure costs are a significant concern for businesses, and understanding what they are can help you identify areas for improvement.
Complaints are a type of external failure cost, as they indicate that a product or service has failed to meet customer expectations.
Here's an interesting read: Transmission Failure Cost
Repairing goods and redoing services are also external failure costs, as they are a direct result of defects or issues that arise after delivery.
Warranties can be a costly external failure cost, as they often involve replacing or repairing defective products.
Customers' bad will is a consequence of external failure costs, leading to a loss of trust and potential brand reputation damage.
Losses due to sales reductions can also be a result of external failure costs, as dissatisfied customers may choose to take their business elsewhere.
Environmental costs can be incurred due to external failure costs, particularly if a product or service is found to have a negative impact on the environment.
Here are some examples of external failure costs:
- Complaints
- Repairing goods and redoing services
- Warranties
- Customers’ bad will
- Losses due to sales reductions
- Environmental costs
What is Not an External Failure Cost?
An internal failure cost is not an external failure cost. This is a critical distinction, as internal failure costs are incurred before the product or service reaches the customer.
Internal failure costs include expenses such as scrap materials, rework, and repair of defective products. These costs are typically incurred during the production process, not after the product has been delivered to the customer.
Companies often have different metrics for measuring internal and external failure costs, as they require distinct approaches to analysis and improvement. By understanding the difference between these two types of costs, businesses can develop targeted strategies for reducing waste and improving quality.
Internal failure costs can be minimized through process improvements, such as implementing quality control checks and reducing defects during production. This can help companies save resources and improve overall efficiency.
Sources
- https://www.studocu.com/en-us/messages/question/2845817/which-of-the-following-is-not-an-external-failure-costa-scrapb-lost-goodwillc-costs
- https://en.tigosolutions.com/blogstory/4337
- https://www.isixsigma.com/financial-analysis/cost-quality-not-only-failure-costs/
- https://sixsigmastudyguide.com/cost-of-poor-quality/
- https://www.wallstreetmojo.com/external-failure-cost/
Featured Images: pexels.com