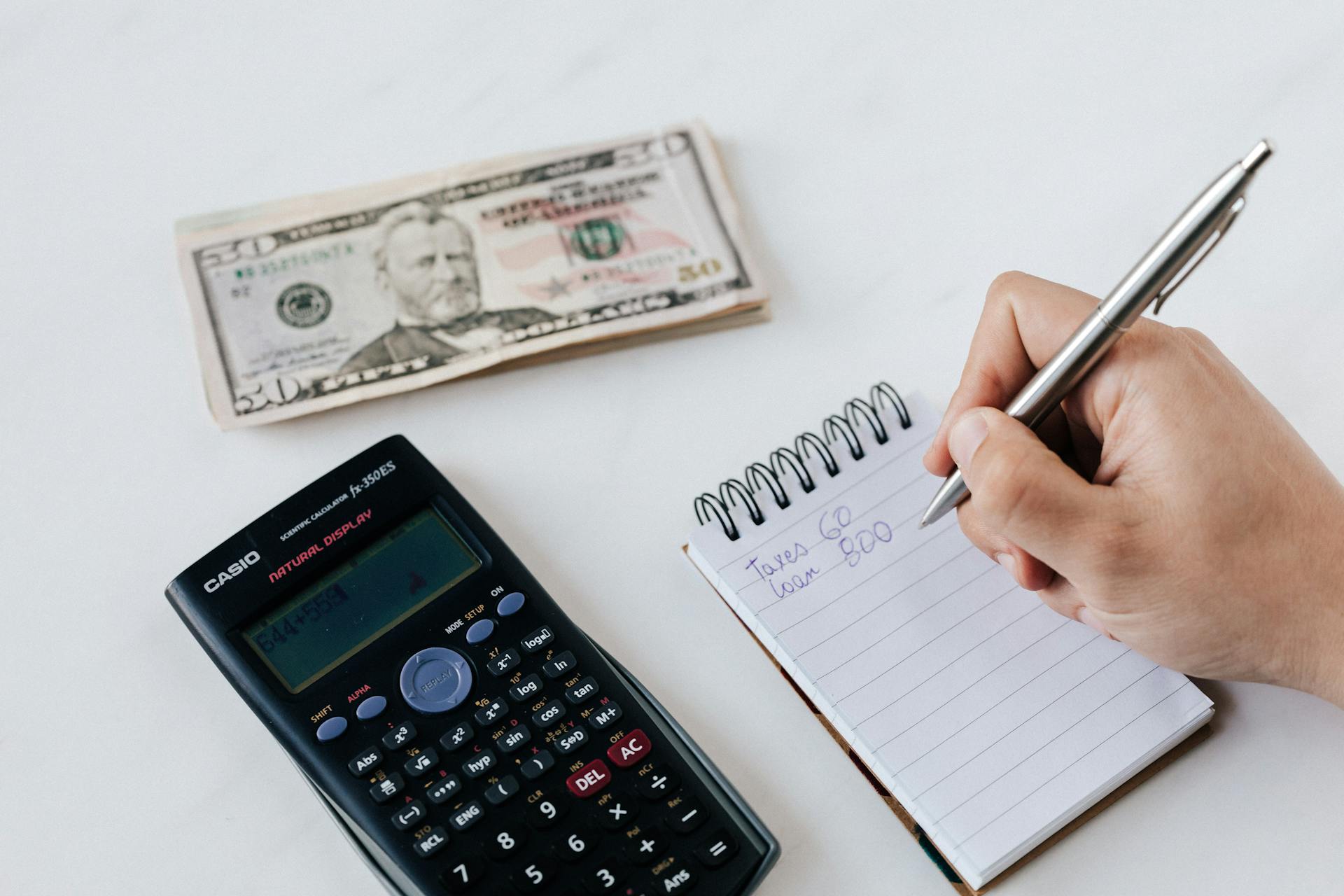
Direct materials budgeting is a crucial step in managing production costs. It helps businesses accurately estimate and control the costs of direct materials used in the production process.
A direct materials budget is typically prepared for a specific period, such as a month or a year, and is based on the company's production plan. This plan outlines the expected production volume and the types of materials needed.
The direct materials budget should include all direct materials, including raw materials, components, and supplies. This ensures that the company has sufficient funds to purchase the necessary materials and avoid stockouts or overstocking.
A well-prepared direct materials budget helps businesses avoid cost overruns and ensures that production costs are accurately estimated.
Here's an interesting read: Move Materials
Calculating Direct Materials Budget
To calculate your direct materials budget, you'll need to know your production level, which can be found in your production budget. This is the foundation of your direct materials budget.
Your direct materials inventory at the beginning of an accounting period is found in the preceding accounting period's production budget. You'll also need to know your ending direct material inventory to ensure you have enough materials for the next production period.
If this caught your attention, see: Integrate Study Materials
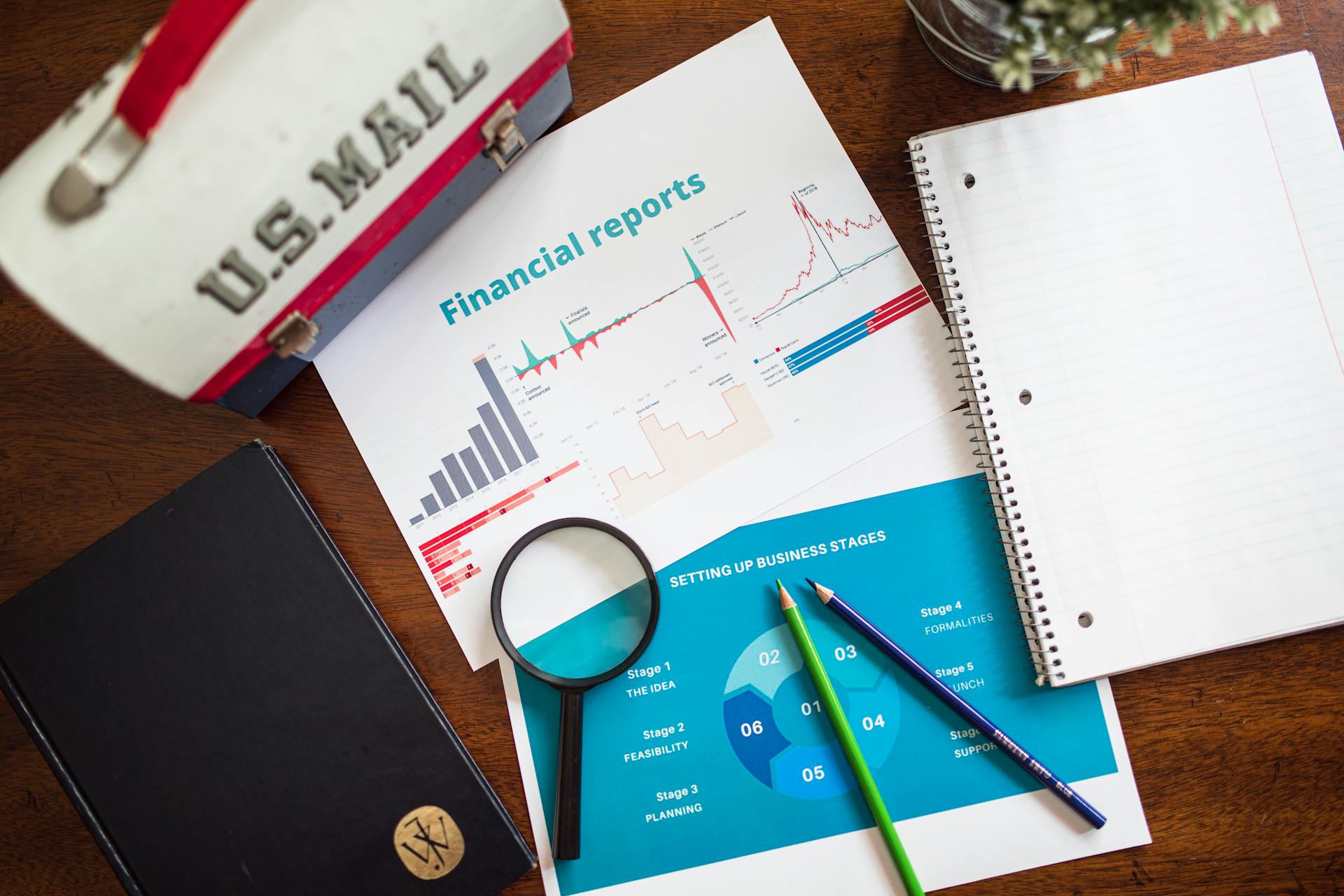
The formula for direct material budgeting is simple: Budgeted direct material purchases in units = Budgeted beginning direct material in units + Direct material in units necessary for production - Budgeted ending direct material in units. To work out the direct material necessary for production, you'll need to know the units of direct material required per unit, which can be calculated by multiplying the budgeted production level during the period by the units of direct material required per unit.
Here's a quick rundown of the variables you'll need to calculate your direct materials budget:
By having these variables, you'll be able to accurately calculate your direct materials budget and make informed decisions about your production costs.
What Are Purchases?
Purchases are a crucial aspect of direct materials budgeting. Direct material is the raw material directly used to produce an item, and it's essential to track its cost to ascertain the cost of manufacturing a product.
Direct material used is tracked to calculate the point of reordering, which means more raw material needs to be bought for production at this level. Direct material is a recipe for the manufactured item as listed under the bill of materials.
To calculate the cost of direct material used, you need to consider the opening direct material inventory, direct material purchased, and closing direct material inventory. The common inventory costing method is First-In-First-Out (FIFO), which is the most standard in the beverage and food industry.
Here's a breakdown of the direct material used formula:
- Opening direct material inventory: This is the stock of raw materials at the beginning of an accounting period.
- Direct material purchased: This includes the shipping cost incurred by the company.
- Closing direct material inventory: This is the inventory left in the store at the end of the trading period.
The direct material used formula is used to calculate both the quantity and cost of material used in production.
Calculating Direct Materials Budget
To calculate your direct materials budget, you'll need to know your production level, which can be found in your production budget. This is a crucial piece of information as it determines how much material you'll need to purchase.
Your beginning direct materials inventory is also essential, and you can find this in the production budget of the most recent period that was completed. This will help you understand how much material you already have on hand.
You'll also need to consider your ending direct materials inventory, which will ensure you have enough materials for the next production period. Direct materials that go into production and their cost are also important factors to consider.
To calculate the direct materials budget, you can use the following formula: Budgeted direct material purchases in units = Budgeted beginning direct material in units + Direct material in units necessary for production - Budgeted ending direct material in units.
To determine the direct material necessary for production, you can use the formula: Direct material in units necessary for production = Budgeted production level during the period x Units of direct material required per unit.
Here's a breakdown of the information you'll need to calculate your direct materials budget:
- Production level
- Beginning direct materials inventory
- Ending direct materials inventory
- Direct materials that go into production and their cost
- Units of direct material required per unit
With this information, you'll be able to accurately calculate your direct materials budget and ensure you have enough materials on hand to meet your production needs.
Related reading: Building Materials
Inventory and Costing Methods
Inventory and Costing Methods are crucial for accurate direct materials budgeting. The most standard inventory costing method is First-In-First-Out (FIFO), commonly used in the beverage and food industry.
Direct material inventory goes through three stages: direct material stock, work-in-progress stock, and finished goods inventory. The direct material used formula helps calculate both the quantity and cost of material used in production.
To calculate the direct material used, you need to know the opening direct material inventory, direct material purchased, and closing direct material inventory. The direct material used formula is: Cost of Direct Material Used = Opening Direct Material Inventory + Direct Material Purchased – Closing Direct Material Inventory.
Opening direct material inventory is the stock of raw materials at the beginning of an accounting period. Closing direct material inventory is the inventory left in the store at the end of the accounting period.
Here's a simple formula to calculate the direct material used:
By using the FIFO method, you can accurately calculate the cost of direct material used and make informed decisions for your direct materials budget.
Cost Calculation and Formulas
To calculate the direct materials purchases budget, you'll need to know your production level, which can be found in your production budget. This will help you determine how much material you need to purchase.
The formula for calculating direct materials used is: Cost of Direct Material Used = Opening Direct Material Inventory + Direct Material Purchased – Closing Direct Material Inventory. This formula takes into account the beginning inventory, direct materials purchased, and ending inventory.
Here's a breakdown of the costs involved in direct material used:
- Opening Direct Material Inventory: This is the stock of raw materials at the beginning of an accounting period.
- Direct Material Purchased: This is the amount of direct material purchased during the trading period, including shipping costs.
- Closing Direct Material Inventory: This is the inventory left in the store at the end of the trading period.
By using this formula, you can accurately calculate the direct materials used in production and make informed decisions about your business.
Calculating Used Production Costs
Calculating used production costs is a crucial step in understanding the financial health of your business. This involves tracking the cost of direct materials used in production, which is the raw material directly used to produce an item.
Direct material used is tracked to ascertain the cost of manufacturing a product. Direct materials fall under variable costs.
Take a look at this: Direct Costs
To calculate the cost of direct materials used, you'll need to consider the opening direct material inventory, direct material purchased, and closing direct material inventory. The formula for this is: Cost of Direct Material Used = Opening Direct Material Inventory + Direct Material Purchased – Closing Direct Material Inventory.
The cost of direct materials used is a key component of the production cost, which also includes manufacturing overhead and direct labor. The production cost formula is: Production Cost = Direct Materials + manufacturing Overhead + Direct Labor.
To get the opening direct material inventory, you'll need to use the FIFO method, which is the most standard method in the beverage and food industry. This will give you the stock of raw materials at the beginning of an accounting period.
Direct material purchased during the trading period is added to the opening inventory, along with the shipping cost incurred by the company. At the end of the trading period, count the inventory left in the store and use the FIFO method for the ending direct materials total cost formula.
Here's a summary of the steps to calculate the cost of direct materials used:
- Calculate opening direct material inventory using the FIFO method
- Add direct material purchased during the trading period
- Include shipping cost incurred by the company
- Calculate closing direct material inventory using the FIFO method
- Use the formula: Cost of Direct Material Used = Opening Direct Material Inventory + Direct Material Purchased – Closing Direct Material Inventory
Linearity Assumption for Cost Calculation
Calculating costs in a linear relationship is a straightforward process. In a perfectly linear relationship, a change in one variable directly affects another, such as the cost of materials and the price of a product.
To calculate costs in a linear relationship, you need to develop an equation based on related variables. This equation helps project future costs of production under various scenarios.
The cost of materials and labor influences the cost of production. An equation for calculating the cost of production using specified values for materials and labor costs is derived.
The equation is used to estimate future costs, but keep in mind that perfectly linear cost-variable relationships are rare. When the relationship is approximately linear, the least-squares regression line is calculated.
A linear function for estimating costs can give incorrect values, so businesses use approximation methods for accurate estimates in financial decisions.
There are no Generally Accepted Accounting Principles for doing a cost report for a process. Various ways of presenting the information with similar results are used.
To illustrate the concept, consider the following example:
By using the equation derived from the linear relationship, you can estimate the production cost based on the materials and labor costs.
Sources
- https://courses.lumenlearning.com/wm-managerialaccounting/chapter/performance-report/
- https://www.thebalancemoney.com/how-to-prepare-a-direct-materials-purchases-budget-393023
- https://gocardless.com/en-us/guides/posts/how-to-create-a-direct-material-purchasing-budget/
- https://emergeapp.net/inventory-reports/how-to-calculate-direct-materials-used/
- https://www.centage.com/blog/developing-an-accurate-direct-materials-budget
Featured Images: pexels.com