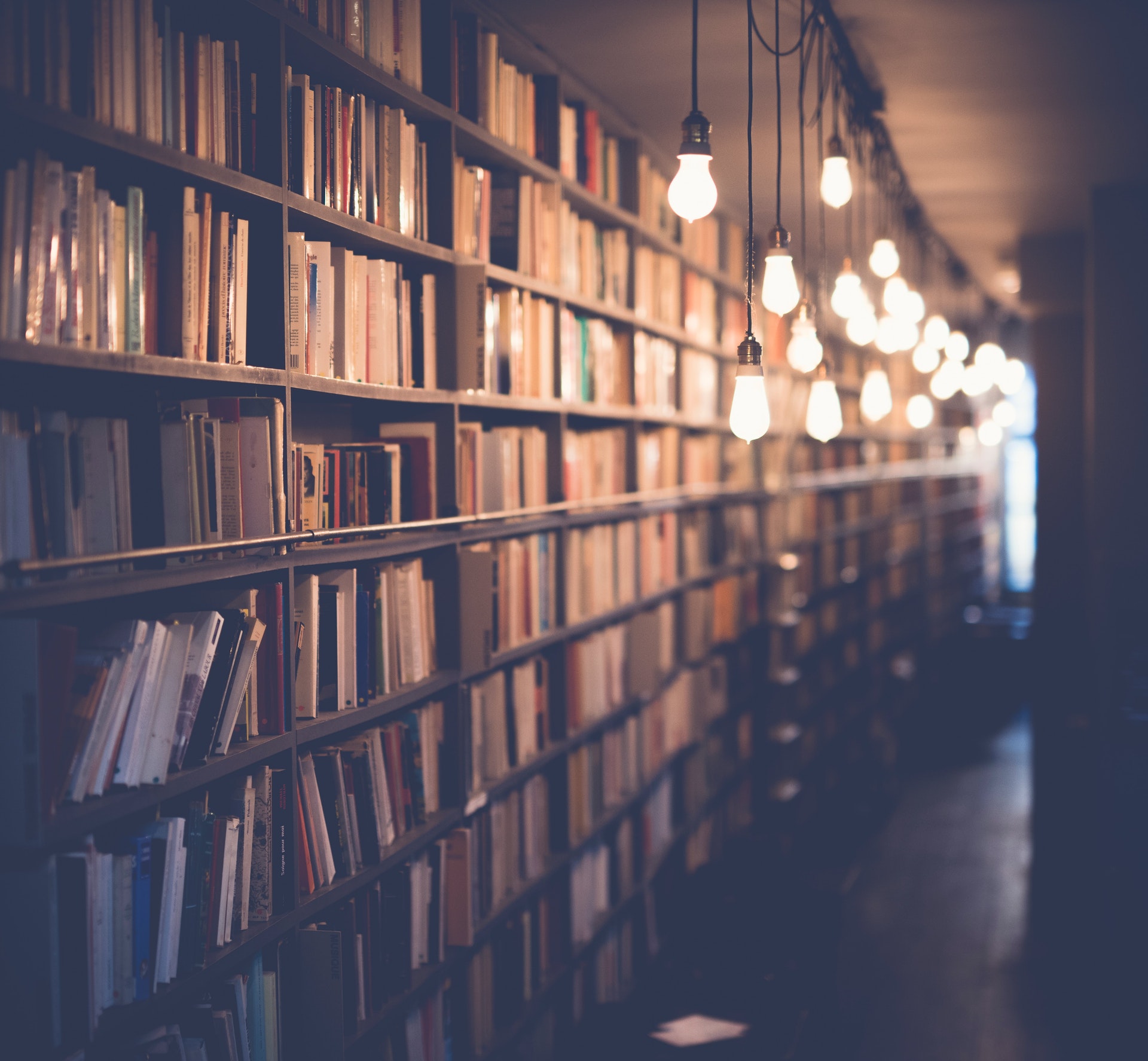
The type of device used to move materials around a workplace depends on the size of the workplace, the amount of material to move, and the purpose. In smaller workplaces manually operated machines such as a pallet jacks and trolleys can be used to move materials quickly and efficiently. For large warehouses and production facilities, powered industrial vehicles such as forklifts are commonly employed.
Forklifts come in a variety of models that are designed for a particular application. Electric forklifts are suitable for indoor use while diesel or petrol engine based models can power heavy loads outdoors. They can be tailored with attachments that help with specific tasks such as paper roll clampers, upenders, bin trippers, dual-tire systems, magnets and more. In addition to being able to lift loads, some models come with side tilt allowing for easier placement of delicate items into tight places.
In today’s modern production plants automated guided vehicles (AGVs) provide an efficient way to transport materials quickly, safely and accurately. These self-driving robots are programmed with a vehicle controller connected to onboard navigation sensors that allow it to navigate around obstacles while following predetermined routes autonomously. AGVs typically excel at tasks that require continuous material transport over short distances in places where safety is paramount such as medical equipment manufacturing plants.
Regardless of the type of device chosen one thing remains true; materials must always be moved safely for maximum efficiency both indoors or out. By selecting the right type of machine for each particular application you can ensure quick, uneventful transportation throughout your workplace every time!
You might like: Which of the following Is Not a Type of Influencer?
What is the most common type of powered equipment used in material handling?
Material handling is a critical element in any efficient operation. Without proper material handling, organizations can struggle with productivity as well as safety issues. The type of equipment used in material handling depends largely on the application, but one type of powered equipment is common across many industries: forklifts.
Forklifts are hugely versatile pieces of powered equipment and they’re capable of tackling a variety of tasks. They can move heavy and bulky objects quickly and safely, allowing personnel to store and retrieve items with ease. In warehouses and factories, forklifts are typically used to transfer cargo between shelves, loading docks and storage containers. This greatly simplifies the task of transporting materials between different areas while also keeping employees safe by minimizing physical manipulation efforts.
Thanks to modern technology advancements such as load sensors, 3D cameras and geo-fencing, forklifts are becoming increasingly safer and efficient with each passing year. These technological innovations allow employers to better control their workflows and analyze performance data, providing them with valuable insights for further process optimization. The majority of bigger companies that rely heavily on material handling also resort to automation solutions such as robotic arms or automated guided vehicles (AGVs) to further improve productivity rates for particular applications that require more precise operations or higher speeds than human operators can provide.
In conclusion, it’s safe to say that forklifts are the most widely deployed powered equipment used in material handling scenarios due to their practicality, versatility and overall cost effectiveness. As such, many companies turn automate their processes with modern technologies such as machine learning algorithms or robotic arms in order to reduce costs while still maintaining efficiency standards at their facilities.
Take a look at this: Which of the following Is Not a Type of Galaxy?
What equipment is used to increase efficiency when loading and unloading materials?
In the modern world, efficiency is the name of the game. With workflows and processes constantly scrutinized for opportunities to do things better and faster, it’s important to have the right equipment on hand during loading and unloading operations. The right equipment helps speed things up, and many available materials-handling tools can improve efficiency.
One of the most common pieces of equipment used for loading and unloading is a forklift. These are great for handling both light and heavy loads in almost any environment, like warehouses, factories, distribution centers, and more. Not only do they load materials easier than with human muscle alone but they also increase safety by moving material faster and with less risk of worker injury. Forklifts can also feature attachments like booms that extend their reach for added flexibility, sacrificing some speed for increased potential reach.
Materials-handling conveyors are another common tool that makes loading tasks simpler and faster. What used to take multiple people or teams using wheeled carts now can be accomplished by one or two workers driving empty pallets down a conveyor to be filled in one area then sent to a separate area that needs them—all with little manual effort required beyond getting the pallet onto the initial lift. Conveyors can be integrated into more complex automation systems too, like digital-controlled lifts that can elevate items up to multiple stories high if needed.
When it comes to increased efficiency while loading or unloading materials, there are plenty of options available! From simple tools like forklifts to more advanced automation systems, having efficient material-handling equipment on hand makes life along the supply chain much easier.
Intriguing read: Silicone Impression Material
How can motorized material handling devices improve productivity?
Motorized material handling devices are incredibly important tools for improving productivity in the workplace. These devices take different forms, but all of them have one common goal—they help to simplify and streamline the movement of materials from one part of a facility to another, saving staff time and energy in the process.
One of the most popular motorized material handling devices is pallet jacks. These jacks feature a motor, controls and platform to help move heavy and wide loads over long distances quickly and with ease. They also feature self-propelled motors that can be easily operated quickly with minimal effort, which increases speed and accuracy when transporting materials between locations. For example, you could use a pallet jack to move items like ready-to-ship items around your storage area, allowing for quick order turnaround times for customers.
Apart from pallet jacks, automated guided vehicles (AGVs) can also improve productivity in facilities by routing material from a starting point to their desired destination without having to manually drive it there by personnel or a forklift. Also featuring self-propelled motors, AGVs have advanced obstacle avoidance capabilities that help prevent any potential collisions along the route, ensuring materials arrive without any delays or damage—a task difficult by staff or manually driven forklifts. Plus, AGVs can also serve multiple functions in larger facilities by providing physical and mathematical processing capabilities beyond just simple transportation tasks alone—greatly speeding up operations times when combined with other automated processes.
Overall, motorized material handling devices offer essential solutions to improve productivity in workplaces through reducing labor intensive efforts installed with automated solutions that remove production hiccups along their journey and ensure materials are delivered on schedule while still being reliable enough to sustain operational integrity throughout its life span.
Expand your knowledge: Which One of the following Is Correct?
What are the advantages of using motorized material handling devices?
Material handling is an important process in any industry, and motorized material handling devices are used to help streamline the process. They reduce labor costs, help eliminate manual processes, and improve safety. There are several advantages of using motorized material handling devices, including increased efficiency, improved accuracy, reduced fatigue, and improved worker safety.
Increased Efficiency: Motorized material handling devices enable you to move more goods in less time. With automated systems that can optimize shipment size and container consolidation, throughput can be increased to accommodate larger orders with fewer labor costs. Motorized equipment also helps reduce inventory by providing accurate and real-time data about product flow. This means that labor resources no longer need to be devoted solely to numbers crunching or moving paperwork – instead these resources can focus on other tasks that contribute more directly to higher productivity levels.
Improved accuracy: Manual material handling processes rely on paper-driven processes which increase the chances of errors associated with manual processes that can occur due to human error such as incorrect counting or forgetting steps in a system process. Motorized material handling devices greatly increase accuracy by allowing for automated processes such as scanning barcodes for improved precision over hand-scanning or manually counting products. Throughput is also increased thanks to scanning capability which eliminates the need for personnel involvement during order fulfillment cycles – enabling orders broken down by item level detail to be prepared faster than what would traditionally be possible at a manual scale operation.
Reduce fatigue: Motorized material handling systems reduce the amount of physical exertion and stress placed on workers due to manual dexterity requirements when completing tasks such as lifting heavy materials or transferring goods from one area to another. Automated systems are designed with ergonomic principles in mind to ensure that they are friendly towards operator well being while still working efficiently and effectively at the same time. This reduces the amount of strain placed on human muscles which can facilitate more workplace comfort ensuring a better environment for personnel working long shifts with heavily physical requirements associated with machine operation of materials transfer needs.
Improved Safety: As previously mentioned when addressing ergascripttual ergonomic improvements within assembly handlings machines also improve safety through their use as well due to reliance upon specifically designed systems for completion of specific task sets or movements required personally by individuals engaging within those climates such accidents or resource shortages like slips trips falls tool breakage etc can sometimes be prevented most definitely assisted through proper motors capable of transferring necessary items from one location 2 another via mechanisms meant exactly 4the above purpose avoiding any pain probability moreover additionally locking mechanisms employed either thru hardware implementation software make sure additional working hazards states excluded as these unfortunate occurances get reduced if/when machines replace properties human-personnel relied upon thus preventing endangerment regarding living staff present upon premises needing intervention if anything were 2 transpire instead mechanical attributes brought inside through robotic assistance handle it quite carefully w/o potential loss of either life property both immediately or afront confrontational confrontation scenarios without fail 10 times outa 10 bettering safety overall 4 everyone.
For more insights, see: What Material Can You Sublimate On?
What safety measures should be taken when operating motorized material handling equipment?
There is no doubt that operating motorized material handling equipment requires a high degree of safety to be observed by the operator. It is important for workers to adhere to all safety and operational protocols before, during, and after every shift. The following steps should be taken for maximum safety when operating motorized material handling equipment:
To begin, operators must receive the proper training on how to properly use the specific machine being operated. This involves being aware of overhead obstacles, clearance from other obstacles in the area, and recognizing that the machine has blind spots where other workers or pedestrians may be in harm’s way. Before any machinery is used, all appropriate warnings must be observed and all necessary guards in place, as well as making sure personal protective equipment (PPE) is worn.
Next, pre-start inspections should be conducted routinely to check on controls and instruments that are associated with the equipment’s functionality. This includes ensuring that switches and alarms are in working condition and checking oil levels, any fluids or parts that need servicing. A practice of spot checking these components during shifts will help create a secure work environment.
Finally, it is important to never operate a motorized piece of machinery while under the influence of drugs or alcohol — this can easily lead to dangerous situations for yourself or those around you. Additionally, it must never be used outside its rated capacity or for purposes beyond its capability as outlined by its manufacture (e.g., using a forklift for other applications). By simply keeping up with daily maintenance activities on all machines it will ensure safer operation because malfunctions will be less likely occur without warning.
By adhering to these safety precautions while operating material handlingequipment, both employers and employees can help create a safe workenvironment and reduce avoidable accidents within their facility that could havebeen caused by negligence or carelessness on behalf of an operator who might not have been properly trained in the safe operation of their equipment.
Take a look at this: Material Participation
Featured Images: pexels.com