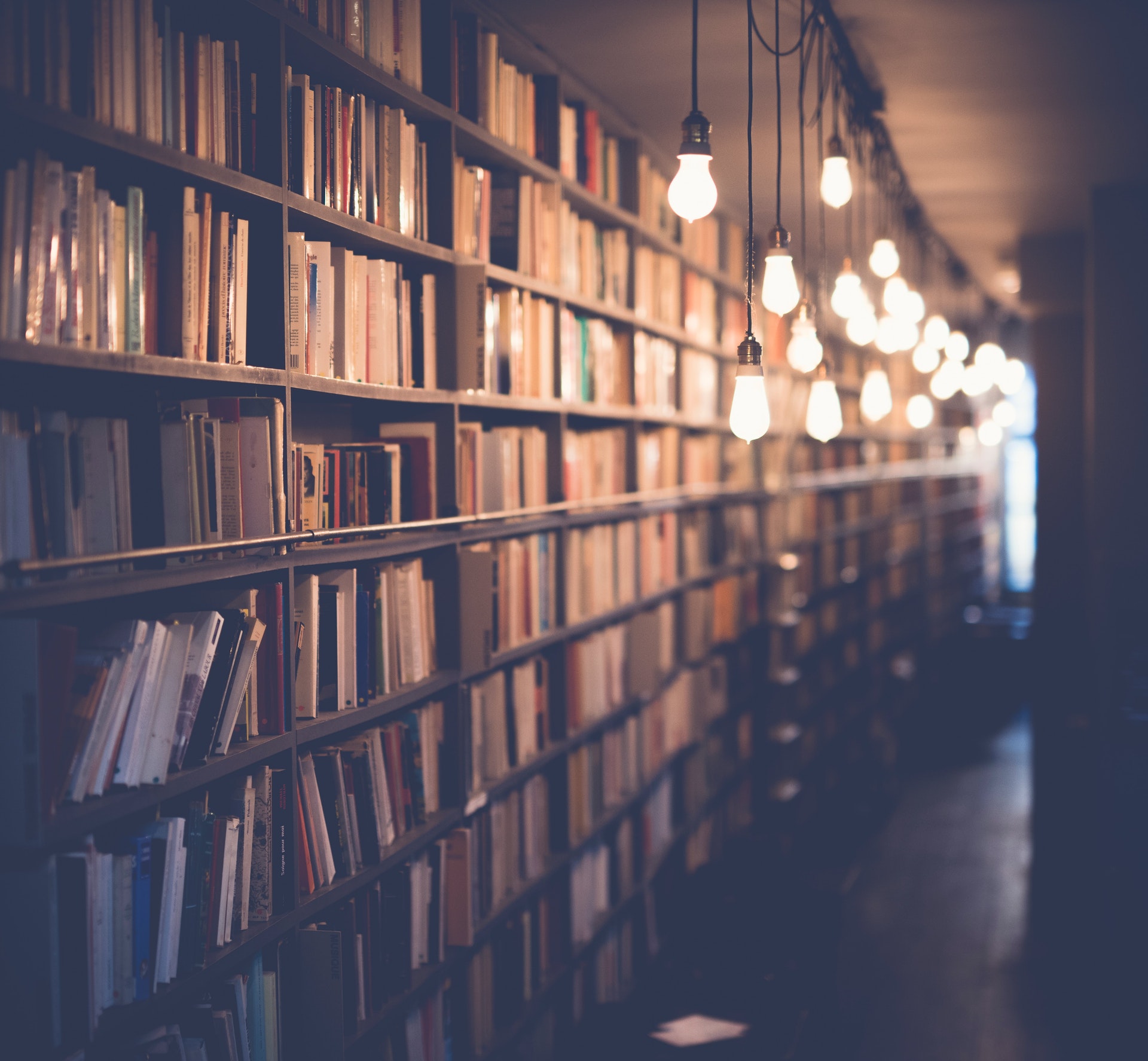
Information systems for managing manufacturing resources come in many shapes and sizes. These systems can range from providing a comprehensive overview of operations to much more specific information about production, supply chain management, inventory control, employees and other important aspects of the manufacturing process.
For an overall resource planning solution, an Enterprise Resource Planning (ERP) system is the ideal choice. ERP solutions provide companies with a single source of data to easily collect and view information related to accounting, inventory control, sales, reporting, business intelligence and other key areas. ERP solutions are also highly flexible and can be scaled to fit any size organization or industry.
What if a company needs something more specific than an ERP? In this case a Manufacturing Execution System (MES) could be the answer. An MES provides companies with detailed information on processes such as maintenance and scheduling, quality assurance checks, traceability of components from start to finish in production lines as well as tracking costs associated with individual products in the production cycle. This level of detail ensures that quality is consistently maintained across production processes and allows for streamlined workflow optimization for maximum efficiency in operations.
For those organizations that need a level of immediacy in operations management, a Manufacturing Operations Management (MOM) system might be the way to go. MOM enables companies to integrate both real-time data from sensors throughout their assembly lines as well as historical information in order to provide an efficient way to monitor their performance while gaining valuable insights into their operations.
Ultimately selecting the right information system depends on each company's specific needs – but no matter what the choice is the right system will help ensure efficient manufacturing processes and increased profits for any business.
You might enjoy: Restraint System
What software is used to organize and track manufacturing control data?
Organizing and tracking manufacturing control data can be one of the most daunting tasks for manufacturers with large budgets. After all, ensuring efficiency in production output requires a close eye on resources, material and labor costs, as well as production timelines. To simplify this highly intensive task, various software programs have been developed to accurately track and organize all aspects of manufacturing control data.
One of the most widely used software programs for tracking manufacturing data is Manufacturing Execution System (MES). This program allows manufacturers to connect all machinery, instrument systems and networks for efficient production performance supervision. It also can quickly convert information from sales orders into production orders with real-time updates that provide accurate cost-benefit analysis.
Enterprises Resource Planning (ERP) is another popular software program used to manage manufacturing control data. It helps manufacturers plan their materials inventory more efficiently by automating supplier communication. Also, this system has the capability to generate reports that measure efficiency in machine usage time and labor costs compared to customer demand projections.
For companies looking for a more streamlined solution, much of today’s control systems integrate updated plans with existing scopes and financial details related to purchasing raw materials. With these systems, real-time updates are transmitted directly from departments that consolidate current market knowledge with inventory analysis tools.
All these programs help make the daunting task of organizing and tracking manufacturing control data much more manageable. Thanks to their capabilities -- collecting data on different levels of production accuracy, detecting bottlenecks before they arise and improving overall productivity levels -- they are an invaluable asset in making sure companies remain competitive in the fast-changing industrial landscape.
A fresh viewpoint: Septic System
How does a company optimize its manufacturing process via technology?
The use of technology in manufacturing processes has had a revolutionary disruptive effect in recent years, and it can be seen as the heart of many industrial operations. Technology-driven optimization yields increased production speed, improved safety and quality control, real-time tracking of inventory levels, cash flow observation and coordination of complex tasks. It is no surprise that today's savvy businesses are keen to leverage this potential for cost savings and aggressive competitive positioning.
The most efficient way to begin optimizing is to fully understand the production process before investing in technology tools. Companies should carefully analyze their existing processes to identify timesaving opportunities specific to their goals. A comprehensive overview would include an exploration of digitalized infrastructure such as intranet systems or automated data exchange functions, as well as any current workplace practices that could be replaced with automated, more time and resource efficient solutions.
Technology tools best suited for the task will differ depending on the type of industry involved, but once the needed technologies have been identified companies should implement solutions in phases - starting with basic functions like targeted customer ordering or automated warehouse tracking before raising the bar with more intricate systems no matter how advanced they may seem. If coupled with comprehensive training for all relevant staff and ongoing technical support after installation, optimal adaptations can be expected from almost every system available today.
Of course proper planning is crucial for any successful optimization project but it can bring awesome advantages if done correctly. High profits from higher outputs at lower costs are only a few potential benefits, not to mention improved job satisfaction and morale due to worker empowerment. Clear ongoing planning for maintenance is essential for long term system stability, but once the basics are in place you can look forward to your new optimized manufacturing process paving the path towards success!
A unique perspective: Physical Systems
What tools are available to help automate the manufacturing process?
Automation has become increasingly important in the world of manufacturing, enabling makers to maximize production and ensure that products are made with quality and safety in mind. The good news is that there is a plethora of tools now available to facilitate this process.
At the most basic level, hardware automation tools are used to replace or augment manual labor. Examples include robots that can move items around production lines, specialized welding machines and even complex 3D printed components. Advanced software solutions also automate a range of tasks such as data analysis, testing, quality assurance and even customer ordering processes. It’s also worth noting that these tools don’t need to be expensive or overly complex – incredibly helpful manufacturing tools such as “flow charts” or “production checklists” are available to small businesses free of charge via online resources.
For manufacturers looking to improve the efficiency of their operations, automation solutions should be one of the first ports of call. Fortunately there is a wide range of options on the market for both large and smaller companies, from high end robotic arms to simple flow diagrams - so makers can easily find something suited to their needs. Indeed, with some planning and research it should be possible for most companies which invest in automation solutions to see an improved return on investment almost straight away.
Check this out: Manufacturing Equipment Financing
What type of information systems are used to monitor quality in the manufacturing process?
Information systems are critical to help streamline production, increase efficiency and monitor the quality of goods produced in any manufacturing process. Quality control isn’t a one and done kind of process, it requires multiple steps and continual monitoring of key performance indicators to ensure that safety standards and quality assurance protocols are met.
To keep track of these indicators, there must be an information system that can measure quality over time. Quality monitoring systems typically consist of two components: process automation through programmable logic controllers (PLCs) to take readings from sensors in the production lines and data management software to store, analyze, and visualize large amounts of data collected from the machines throughout production. PLCs can identify anomalies in the production line that indicate when manual adjustments or interventions are needed. The software allows for efficient data analysis and serves as a dashboard for management, saving time manually curating data sheets.
Cloud-based enterprise resource planning (ERP) suites have also become increasingly useful for manufacturing process control as they help connect different systems from various departments within a single consortium connected by a shared infrastructure allowing for improved interdepartmental communication. ERP suites offer real-time tracking capabilities as well as central collection points helping visualise all relevant metrics across departments linking out materials moved at each phase in the supply chain further increasing visibility into operational performance.
Overall, automation technologies such as PLCs combined with cloud based ERP's are commonly used in manufacturing processes to easily capture powerful insights about product quality and efficiency at all stages of production. These information systems provide valuable support for improving the quality control process and resolving issues that arise quickly with little expenditure needed from manual labour or other resources.
If this caught your attention, see: Reliable Information
What technologies are used to store and analyze manufacturing data?
Manufacturing data storage and analysis has become increasingly important as a means to reduce costs across production chains and optimize performance. Companies are turning towards technology to assist them in achieving this goal, deploying specialized services that can store, track, manage and organize vast amounts of data. Here is a breakdown of some of the technologies used to store and analyze manufacturing data.
Data Warehousing is a system that stores large amounts of data, which makes it easier for those working with the data to perform retrieval tasks and analyses. This process involves collecting production data from multiple sources into one central repository of digital information in order for an organization to use for reporting and analysis purposes. Warehousing allows for business leaders to better understand their production systems, analyze performance metrics and identify areas for improvement more quickly.
Analytic Software are software systems designed specifically for analyzing datasets from manufacturing operations. They involve the use of predictive analytics tools to identify short-term trends in operations as well as long-term forecasting based on collected historical data, providing an extensive overview into how production processes are running in real-time. Such tools provide detailed insights about parts usage and failures, staff productivity levels, assembly line throughputs or any other relevant attributes related to production or inventory levels.
Industrial Internet of Things (IIoT) is a network comprising connected sensors that transmit live information back to plants through a dedicated server, providing companies with up-to-date insights into their real-time operations. Companies can also take advantage of predictive analytics capabilities within IIoT solutions to detect potential problems before they happen by collecting continuous streams of feedback from machines and analyzing them against suggested standards before alerting engineers by automation if any issues arise that need attention.
These technologies constitute some of the most popular tools used for storing and analyzing manufacturing data today; however, there are many more available out on the market depending on specific needs (e.g., Artificial Intelligence). Thus it’s important that companies evaluate all factors when deciding which path they should take when considering a solution for processing their manufacturing data needs.
Consider reading: When Would You Decide to Use Rpa?
How do businesses ensure inventory and production levels remain accurate and up-to-date?
Businesses must stay on top of inventory and production levels in order to properly provide customers with timely service and products. Ensuring that accuracy and up-to-date information is maintained is crucial for a successful business model.
The simplest way of achieving this is investing in proper inventory management systems. Modern systems are available for businesses of all sizes, including relatively small startups. These systems incorporate tracking, monitoring, and tracking technology to automate inventory-level data collection from multiple sources in real-time. With accurate data available, managers can make well-informed decisions about ordering resources and adjusting production to avoid costly delays or overages.
In addition to using an inventory management system, businesses should also implement a layered process control system as part of their operations plan. These systems focus on making sure each layer within a production line remains in sync with the others by examining the quality of the raw materials at each step and inspecting finished products before delivery. Layered process control systems can detect any errors that occur during the manufacturing process and ensure they are addressed quickly so production operations remain uninterrupted.
With smart investments in modern inventory management systems and layered process controls, businesses can be sure reordering processes are efficiently managed and quality is maintained with current production levels. As long as these tools remain regularly updated with accurate information, business owners have peace of mind that their inventory and production levels remain up-to-date and aligned with customer demand.
Intriguing read: Information Literacy
Sources
- https://roboticsbiz.com/8-ways-to-automate-your-manufacturing-processes/
- https://pletheonconsulting.com/how-to-automate-manufacturing-process/
- https://cogsy.com/backordering/inventory-levels/
- https://katanamrp.com/blog/manufacturing-process-automation/
- https://www.themanufacturer.com/articles/using-technology-improve-manufacturing-processes/
- https://katanamrp.com/raw-materials-inventory-management-guide/
- https://www.netsuite.com/portal/resource/articles/inventory-management/inventory-forecasting.shtml
- https://theecmconsultant.com/data-quality-monitoring/
- https://www.ahg.com/qr-mobile-data/business-solutions/mobile-data-collection-production-process-management.htm
- https://letstranzact.com/blogs/the-importance-of-keeping-an-accurate-inventory
- https://katanamrp.com/batch-tracking-guide/
- https://aimpointdigital.com/data-manufacturing/
- https://www.assemblymag.com/articles/95162-powerful-industry-40-manufacturing-software-organize-control-enforce-every-detail-of-your-processes
- https://deljoosoft.com/data-analytics-in-manufacturing/
- https://invergehq.com/how-to-do-inventory-count-9-steps-for-accurate-results/
Featured Images: pexels.com