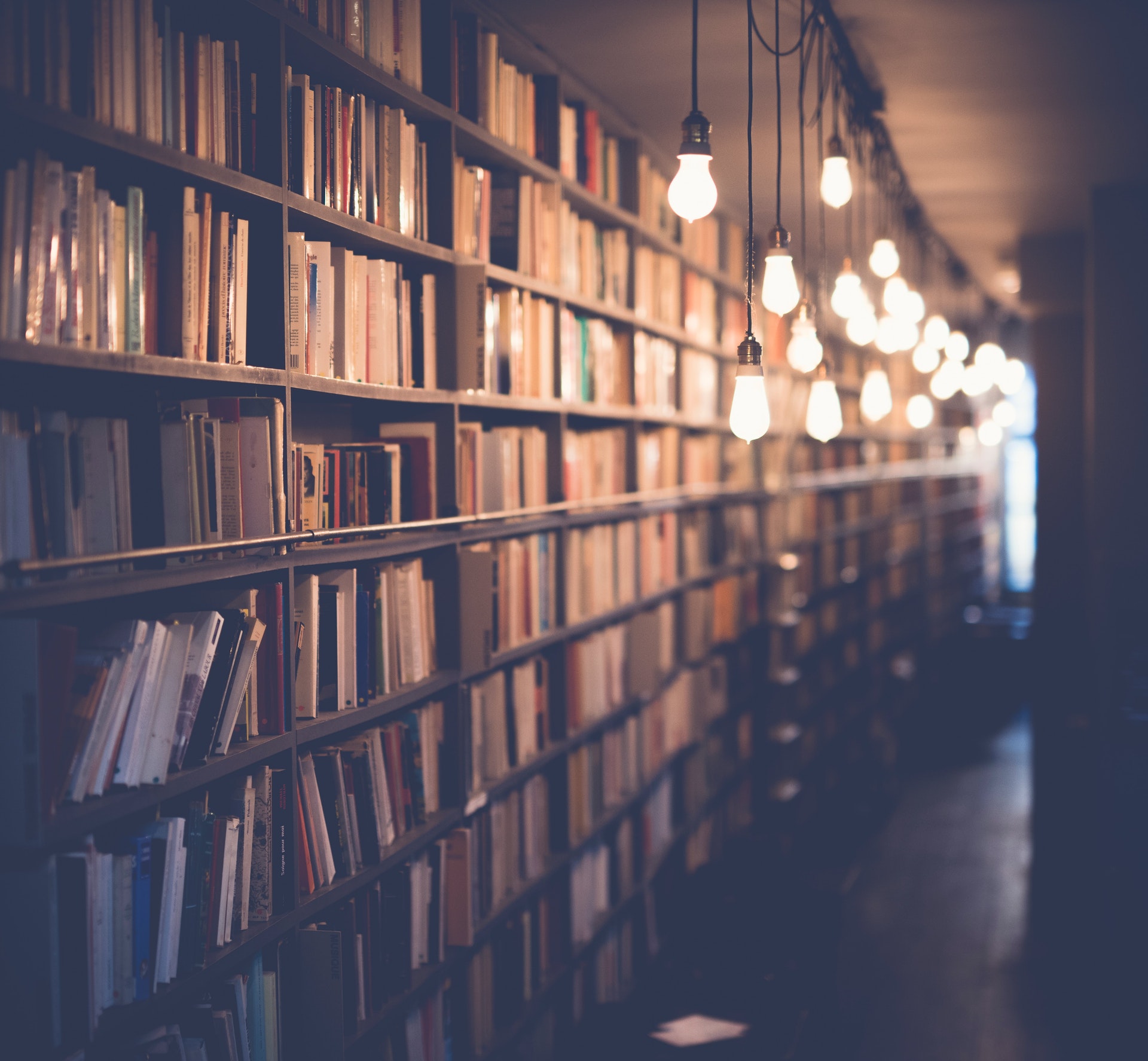
Abrasive wheels are a type of cutting tool that are commonly used in a variety of industries. They are often used to cut or grind metals, but can also be used on other materials such as wood or concrete. There are a variety of different types of abrasive wheels, each designed for specific applications.
When selecting an abrasive wheel for a particular application, it is important to consider the type of material that will be cut or ground, the speed at which the wheel will be operating, and the amount of force that will be applied to the material. For example, a softer abrasive wheel is typically used for cutting metals, while a harder wheel is better suited for grinding.
In addition to considering the type of material that will be cut or ground, it is also important to select the appropriate safety equipment. Abrasive wheels can generate a lot of heat and sparks, so it is important to wear protective clothing, gloves, and eye protection. It is also important to have a fire extinguisher on hand in case of an accident.
Once the appropriate safety precautions have been taken, the next step is to select the right abrasive wheel for the job. There are a variety of different types of abrasive wheels on the market, so it is important to do some research to find the best option for the specific application.
After the right abrasive wheel has been selected, it is important to test it before using it on the job. This can be done by running the wheel against a piece of scrap material to see how it performs. If the wheel leaves a smooth, even finish, it is likely that it will work well for the intended application. If the wheel leaves a jagged or uneven finish, it may need to be adjusted or replaced before being used on the job.
Abrasive wheels are a type of cutting tool that are commonly used in a variety of industries. They are often used to cut or grind metals, but can also be used on other materials such as wood or concrete. There are a variety of different types of abrasive wheels, each designed for specific applications.
When selecting an abrasive wheel for a particular application, it is important to consider the type of material that will be cut or ground, the speed at which the wheel will be operating, and the amount of force that will be applied to the material. For example, a softer abrasive wheel is typically used for cutting metals, while
A fresh viewpoint: What Are the Best Places to Elope in California?
What is the maximum speed rating for the abrasive wheel?
There is no definitive answer to this question as the maximum speed rating for an abrasive wheel can vary based on a number of factors, including the type of abrasive material, the Wheel's diameter, and the rotational speed of the Wheel itself. However, as a general rule of thumb, the maximum speed rating for an abrasive wheel should not exceed the speed at which the Wheel can rotate without causing the abrasive material to break down or disintegrate.
Worth a look: Can You Use Bleach on Your Areola?
What is the maximum operating speed of the machine on which the abrasive wheel will be used?
The maximum operating speed of the machine on which the abrasive wheel will be used is determined by the type of abrasive wheel and the size of the machine. The machine size is classified by the diameter of the largest abrasive wheel that can be used on it. The type of abrasive wheel is determined by the abrasive material and the bond that holds the abrasive particles together.
There are four types of abrasive wheels: grinding wheels, cutoff wheels, abrasive flaps, and abrasive belts. Grinding wheels are classified according to the type of abrasive material and the size of the wheel. Some of the most common abrasive materials used in grinding wheels are aluminum oxide and silicon carbide. The bond that holds the abrasive particles together can be vitrified, resin, or metal.
The majority of grinding wheels have a maximum operating speed of approximately 6,000 feet per minute. Cutoff wheels have a maximum operating speed of approximately 10,000 feet per minute. Abrasive flaps have a maximum operating speed of approximately 8,000 feet per minute. Abrasive belts have a maximum operating speed of approximately 4,500 feet per minute.
The maximum operating speed of the machine on which the abrasive wheel will be used is determined by the type of abrasive wheel and the size of the machine. The machine size is classified by the diameter of the largest abrasive wheel that can be used on it. The type of abrasive wheel is determined by the abrasive material and the bond that holds the abrasive particles together.
Additional reading: Subatomic Particles
What is the minimum diameter of the abrasive wheel?
The abrasive wheel is the component of the grinder that does the actual grinding. It is composed of abrasive grains held together in a binder. The size, hardness, and composition of the abrasive grains determine the aggressiveness of the wheel and the material removal rate. The abrasive wheel is made up of abrasive grains that are held together in a binder. The size, hardness, and composition of the abrasive grains determine the aggressiveness of the wheel and the material removal rate. The minimum diameter of the abrasive wheel is 3 inches.
A different take: Composition Roof
What is the maximum diameter of the abrasive wheel?
Abrasive wheels are tools that are used for grinding, polishing, and cutting. They are made from a variety of materials, including diamond, aluminum oxide, silicon carbide, and zirconia. The abrasive particles are bonded together with resin, metal, or vitrified bonds. The bond is what determines the strength of the wheel and the abrasiveness of the particles. The type of abrasive wheel you use will depend on the material you are working with and the desired outcome.
The diameter of the abrasive wheel is determined by the size of the arbor hole. The arbor hole is the hole in the center of the wheel that is used to attach it to the grinder. The diameter of the arbor hole is usually 1/2 inch, but can be larger or smaller depending on the manufacturer. The maximum diameter of the abrasive wheel is 12 inches.
You might like: Diamond Knockout Arbor
What is the maximum width of the abrasive wheel?
There is no definitive answer to this question as it depends on a number of factors, including the type of abrasive wheel, the material it is made from, and the application it is being used for. However, as a general rule of thumb, the maximum width of an abrasive wheel should be no more than twice the diameter of the wheel. This ensures that the wheel is strong enough to withstand the forces exerted on it during use and that it will not overheat and cause damage to the workpiece.
A fresh viewpoint: What Is Friction?
What is the maximum depth of cut for the abrasive wheel?
The maximum depth of cut for an abrasive wheel is determined by the composition of the wheel and the speed at which it is rotated. The deeper the cut, the more material is removed from the workpiece.
Abrasive wheels are made of a hard abrasive material, such as diamond, and are used to grind or cut a variety of materials. The size and shape of the wheel determine the depth of the cut. The speed of the wheel also affects the depth of the cut.
The depth of cut is usually expressed in micrometers (µm) or thousandths of an inch. The maximum depth of cut for an abrasive wheel is typically about 1.5 mm (0.060").
Abrasive wheels are used in a variety of applications, including grinding, cutting, and polishing. Grinding wheels are used to remove material from a workpiece, while cutting wheels are used to make cuts in a workpiece. Polishing wheels are used to polish a workpiece.
The speed at which an abrasive wheel is rotated affects the depth of the cut. The faster the wheel is rotated, the deeper the cut. For example, a grinding wheel rotated at 8,000 rpm will produce a deeper cut than a wheel rotated at 4,000 rpm.
The depth of cut also depends on the type of abrasive material. For example, a diamond wheel will cut deeper than a silicon carbide wheel.
Abrasive wheels are available in a variety of sizes and shapes. The size of the wheel is expressed in inches or millimeters. The shape of the wheel is expressed in terms of the diameter and width of the wheel.
The most common abrasive wheel shapes are:
1. Straight: A straight wheel has a cylindrical shape with a flat face.
2. Tapered: A tapered wheel has a cone-shaped profile.
3. Flared: A flared wheel has a wide face and a narrow base.
4. Recessed: A recessed wheel has a depressed center.
5. Dish: A dish wheel has a rounded face.
Abrasive wheels are usually mounted on a spindle and rotated at a high speed. The spindle is powered by an electric motor.
Abrasive wheels can be used to grind, cut, or polish a variety of materials, including metals, plastics
For your interest: X3 Rpm Exhaust
What is the maximum operating temperature of the abrasive wheel?
The abrasive wheel is a critical component in many industrial applications. Its purpose is to remove material from a workpiece through the process of grinding or abrasive machining. In order to function properly, the abrasive wheel must be able to withstand extreme temperatures. Depending on the specific type of abrasive wheel, the maximum operating temperature can range from 325 degrees Fahrenheit to over 1000 degrees Fahrenheit.
There are several factors that can affect the maximum operating temperature of an abrasive wheel. The type of abrasive material that makes up the wheel is one of the most important. For example, wheels made with diamond or silicon carbide abrasives can withstand significantly higher temperatures than those made with aluminum oxide or other less durable materials. In addition, the design of the wheel can also impact its maximum operating temperature. For instance, wheels with a thicker body can typically handle higher temperatures than those with a thinner body.
Another factor to consider is the speed at which the abrasive wheel is operated. Higher speeds can generate more heat, which can in turn lead to a higher maximum operating temperature. Additionally, the environment in which the abrasive wheel is used can also play a role. If the surrounding air is very hot, this can raise the temperature of the wheel and potentially reduce its lifespan.
Ultimately, the maximum operating temperature of an abrasive wheel is largely dependent on its specific design and intended use. It is important to consult with the manufacturer or a knowledgeable specialist to ensure that the wheel can withstand the temperatures that it will be subjected to during use.
A different take: Mobile Operating System
What is the maximum exposure time for the abrasive wheel?
There is no definitive answer to this question as it depends on a number of factors, including the type of abrasive wheel being used, the material it is made from, the speed at which it is rotating, and the degree of pressure being applied. However, as a general rule of thumb, the maximum exposure time for an abrasive wheel should not exceed five minutes.
When using an abrasive wheel, it is important to follow all safety guidelines and procedures to minimize the risk of injury. Always wear appropriate personal protective equipment, including gloves, safety glasses, and a dust mask, and be sure to work in a well-ventilated area. Inspect the abrasive wheel before use to ensure that it is not damaged and that all mounting Hardware is securely in place. Never use an abrasive wheel that is broken, cracked, or otherwise damaged.
To avoid excessive heat build-up, use the abrasive wheel only for the recommended time frame and take frequent breaks. Use light pressure and make sure the contact area is well lubricated with water or cutting oil. Keep the contact area cool by frequently dipping it in water. If the abrasive wheel begins to smoke or emit sparks, discontinue use immediately and replace the wheel.
Abrasive wheels are a necessary part of many industrial and construction applications but they must be used with caution and care. By following the proper safety procedures and using the abrasive wheel only as recommended, you can help to ensure a safe working environment.
Take a look at this: How Can You Be Sure Chords?
What is the minimum safety guard width for the abrasive wheel?
There is no definitive answer to this question as the minimum safety guard width for an abrasive wheel will depend on a number of factors, including the type of abrasive wheel being used, the speed at which it is operated, the material being cut, and the operator's experience and training. However, as a general rule of thumb, the minimum safety guard width for an abrasive wheel should be at least twice the diameter of the wheel. This will help to ensure that the operator has enough time to react if something goes wrong and to prevent the abrasive wheel from causing serious injury if it comes into contact with the operator.
A unique perspective: Find Minimum
Frequently Asked Questions
What is the internal quality inspection of abrasive wheels?
There are four items that directly determine the intrinsic properties of the abrasive wheels, such as safety and serviceability. These items are hardness, static balance, slewing strength, and organization number. Because these items have a direct impact on the quality of the abrasive wheel, it is often referred to as the internal quality inspection of the abrasive wheels.
What are the quality technical standards of abrasive tools?
The quality technical standards of abrasive tools are the main basis for product quality inspection. The inspection items of ordinary grinding wheels include the following seven items: basic dimensions, row tolerances, appearance defects, hardness, static balance, rotation strength, and organization number.
Who is responsible for visually inspecting hand tools such as abrasive wheels?
The operator should visually inspect hand tools before each use. The site supervisor should visually inspect hand tools before each use. The user should visually inspect hand tools once a week.
What is the best way to PAT test tools?
You should periodically (every 6 months) perform a "Patching and Bonding" test on your site tools. This can be done by using the standard drop methodology or by combining it with the use of an Agitator Plate.
When are abrasive wheels used for Internal grinding?
When wheels 2 inches or less in diameter which are securely mounted on the end of a steel mandrel are used.
Sources
- http://www.andreabrasive.com/technical-description/speed-conversion-table-for-various-diameters-of-abrasive-wheels
- https://www.highspeedtraining.co.uk/hub/grinding-wheel-marking-system/
- https://quizlet.com/555287886/osha-30-hazropeforktools-flash-cards/
- https://binictools.com/tag/what-test-should-be-performed-on-abrasive-wheels-quizlet/
- https://brainly.com/question/19147904
- https://www.hsewebsite.com/abrasive-wheel-safety/
- https://www.commodious.co.uk/knowledge-bank/abrasive-wheels/abrasive-wheel-marking
- https://quizlet.com/512340804/osha-flash-cards/
- https://wheelsrun.com/performed-on-abrasive-wheels/
- https://teacherscollegesj.org/what-is-the-max-rpm-of-a-grinding-wheel/
- https://www.revolutionreport.net/what-test-should-be-performed-on-abrasive-wheels/
- https://quizlet.com/416306257/quiz-8-tools-flash-cards/
- https://www.courtley.com/abrasive-wheels-quiz/
- https://cpdonline.co.uk/knowledge-base/health-and-safety/abrasive-wheel/
Featured Images: pexels.com