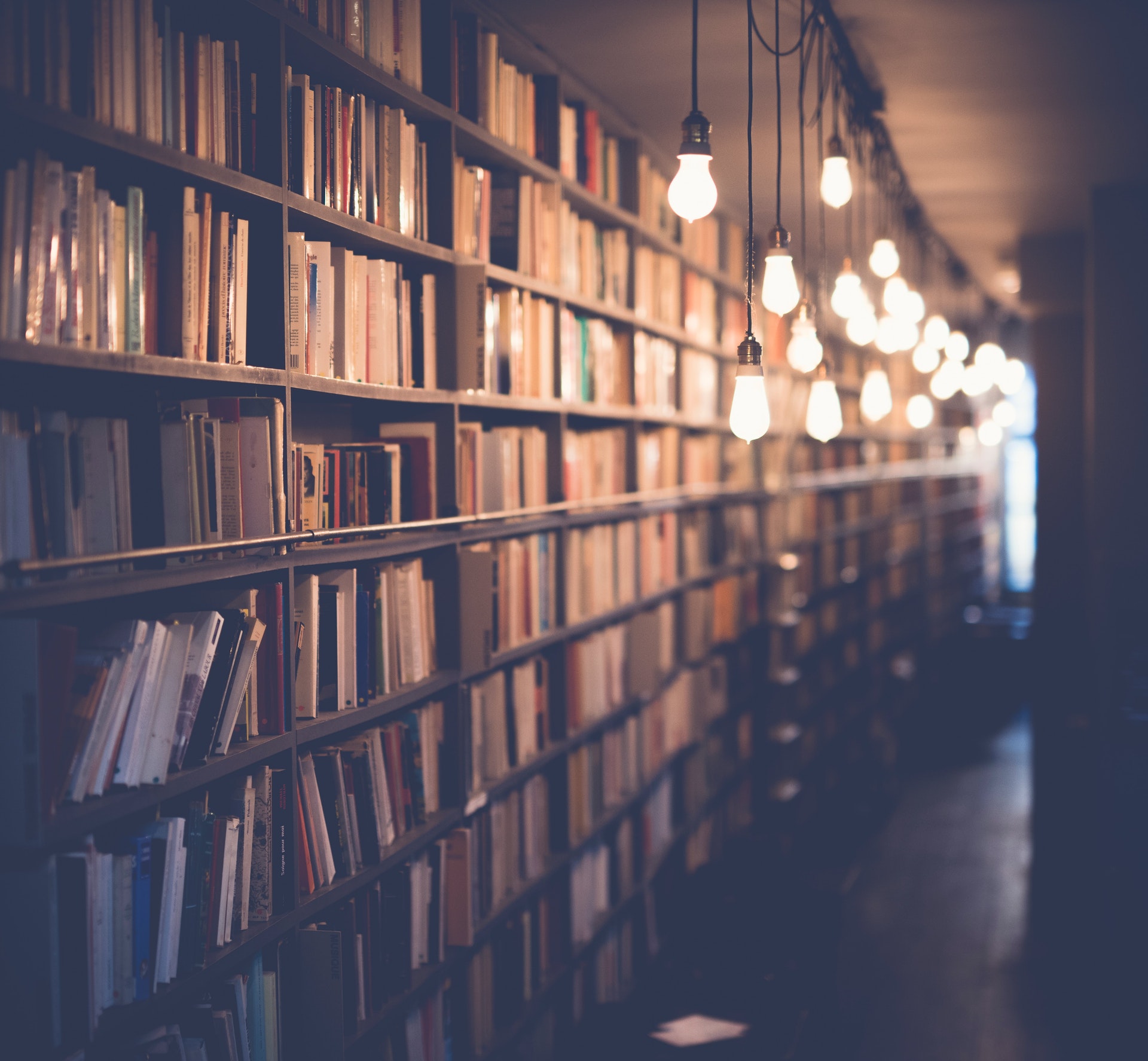
In the automation industry, the term "totally integrated automation" (TIA) has come to mean a holistic and integrated approach to manufacturing process and control design and implementation. The TIA approach encompasses end-to-end visibility and control of the manufacturing process, from the raw material stage through to the finished product. It also includes the ability to fully integrate the manufacturing process with the company's business processes and systems.
In a sense, TIA can be thought of as a next-generation manufacturing execution system (MES). Unlike traditional MES solutions, TIA provides complete process and manufacturing visibility and control in a single software platform. This allows for much greater efficiency and coordination across the entire manufacturing process.
The TIA approach is built on the concept of the "digital twin." The digital twin is a digital representation of the physical manufacturing process, which can be used to optimize and manage that process. The TIA platform provides a complete digital model of the manufacturing process, including all equipment, materials, and processes. This digital model can be used to simulate different process scenarios and to identify potential problems and inefficiencies.
The TIA platform also includes a number of powerful analytical tools. These tools can be used to understand and optimize the manufacturing process. For example, the platform can be used to identify process bottlenecks and to assess the impact of different changes to the process.
The TIA platform is also designed to be highly scalable. It can be used in manufacturing plants of all sizes, from small facilities to large, multi-site operations. The platform can also be used in a variety of industries, including automotive, aerospace, electronics, and medical devices.
In summary, TIA is a holistic and integrated approach to manufacturing process and control. It is built on the concept of the digital twin and includes a number of powerful analytical tools. The TIA platform is scalable and can be used in a variety of industries.
You might like: Authorized Common Stock Refers to the Total Number of Shares
What are the challenges of totally integrated automation?
The challenges of totally integrated automation are many and varied. They include the need to integrate all of the disparate systems and processes within an organization, the need to manage and monitor the constantly changing and expanding data sets, the need to ensure data quality and integrity, the need to develop and maintain custom applications, the need to keep pace with advances in technology, and the need to minimize the risk of disruptions to business operations.
Organizations that have not yet adopted totally integrated automation often find themselves at a competitive disadvantage. Many of the benefits of automation, such as increased efficiency and accuracy, can only be realized when all of the organization's systems and processes are integrated. In addition, the data sets that need to be managed and monitored in order to support totally integrated automation can be extremely large and complex.
Data quality and integrity is another critical challenge associated with totally integrated automation. The data sets that are used to support automated systems and processes must be accurate and complete in order to avoid errors and disruptions. To ensure data quality and integrity, organizations need to implement comprehensive data management processes and procedures.
custom applications are another important challenge associated with totally integrated automation. In order to realize the full benefits of automation, organizations need to develop custom applications that are specific to their business operations. These custom applications need to be able to interface with the organization's existing systems and processes.
keeping pace with advances in technology is another challenge associated with totally integrated automation. As new technologies are developed, organizations need to evaluate whether or not they can be used to support their automated systems and processes. If new technologies are adopted, organizations need to ensure that their custom applications are compatible with the new technologies.
minimizing the risk of disruptions to business operations is another challenge associated with totally integrated automation. disruptions can occur when changes are made to automated systems and processes, when data sets are modified, or when new technologies are introduced. To minimize the risk of disruptions, organizations need to carefully plan and test all changes to their automated systems and processes.
If this caught your attention, see: Which Describes the Benefits of Automation?
How does totally integrated automation work?
The term "totally integrated automation" (TIA) was first used in the early 1990s to describe the integration of all factory processes and systems within a company. TIA aims to create a single, integrated system that can manage all aspects of production, from product design and development to manufacturing, packaging, and distribution.
TIA is often accomplished through the use of computerized manufacturing execution systems (MES), which can provide real-time data on all aspects of the manufacturing process. This data can be used to optimize production and improve quality control. In addition, MES can also be used to monitor and control the supply chain, ensuring that raw materials and finished products are available as needed.
In order to be truly effective, TIA must be supported by an enterprise resource planning (ERP) system. ERP provides the necessary data and tools for managing all aspects of the business, from financials to inventory. With ERP, businesses can have a complete view of their operations, which is essential for making the best decisions about production.
The benefits of TIA are many, but perhaps the most important is the ability to improve quality control. By having all processes and systems integrated, businesses can more easily identify problems and correct them in real-time. This can lead to significant reductions in waste and rework, as well as improve overall product quality.
TIA can also improve operational efficiency by reducing the need for manual data entry and paperwork. By automating all processes, businesses can eliminate the need for duplicate data entry and reduce the opportunity for errors. This can free up employees to focus on other tasks, such as product development or customer service.
In addition, TIA can help businesses to better meet customer demands. By having a complete view of the manufacturing process, businesses can more easily adjust production to meet changing customer needs. This can lead to increased sales and customer satisfaction.
While TIA can offer many benefits, there are also some challenges that must be addressed. One of the biggest challenges is the initial investment required to implement a TIA system. This investment can be significant, but the payoff can be worth it if the benefits are fully realized.
Another challenge is integrating all of the different systems and processes within a company. This can be a complex and time-consuming undertaking, but it is essential for achieving the full benefits of TIA.
Finally, it is important to note that TIA
A different take: FXBO Integrates Brokeree to Offer Integrated CRM to Retail Brokers
What are the applications of totally integrated automation?
In industrial applications, TIA is used to increase productivity and quality while reducing downtime, waste, and energy consumption. When all components of a production line are integrated and controlled by a single system, it can respond quickly to changes in demand or product mix. This enables manufacturers to achieve greater flexibility and agility in their operations.
TIA can also be used to optimize maintenance schedules and improve safety by reducing the need for operators to work in close proximity to machinery. In addition, TIA systems can provide real-time data and visibility into production processes, enabling operators to make informed decisions that can improve efficiency and quality.
Over the past decade, TIA has been gaining momentum in the marketplace as manufacturers seek to increase competitiveness and improve operating margins. The continued advancement of TIA technology, along with the increasing adoption of Industry 4.0 concepts, is expected to drive further growth in the use of TIA in industrial applications.
What are the advantages of totally integrated automation over other automation technologies?
There are many advantages of totally integrated automation over other automation technologies. With totally integrated automation, all processes and functions are automated seamlessly and easily monitored and controlled from a central location. This allows for better efficiency and coordination of resources, as well as improved quality control. Additionally, it reduces the need for human intervention in the production process, thereby reducing the potential for errors.
Additional reading: Integrated Master Schedule
What are the disadvantages of totally integrated automation?
As the world progresses, more and more businesses and organizations are looking to adopt automation in order to increase efficiency and effectiveness. However, there are a number of disadvantages that come with totally integrated automation.
First, when everything is automated, it can lead to a loss of flexibility. For example, if a company designs its process around a certain piece of equipment and that equipment breaks down, the company may not be able to continue its process without that piece of equipment. This can lead to disruptions in the production process and can cause delays.
Another disadvantage of totally integrated automation is that it can lead to a loss of jobs. As machines and automation take over more tasks that were traditionally done by human workers, there will be a decrease in the need for human workers. This can lead to mass layoffs and can increase unemployment.
Finally, totally integrated automation can also lead to a loss of control. When everything is automated, it can be difficult for people to understand how the process works and to make changes to the process if necessary. This can lead to frustration and can make it difficult to make improvements to the process.
What is the future of totally integrated automation?
The future of totally integrated automation is very promising. With the advancement of technology, there is no doubt that many aspects of our lives will be automated. We will see more and more devices that are controlled by our thoughts or voice commands. We will see cars that drive themselves and homes that run themselves.
As technology continues to advance, the future of totally integrated automation looks even more promising. We can expect to see even more amazing inventions that make our lives easier and more efficient.
For more insights, see: Does Insurance Cover Totaled Car
How can totally integrated automation be used in manufacturing?
The notion of totally integrated automation (TIA) has been around for decades but only recently has become a reality in manufacturing. TIA is the integration of all machine, device, and software interfaces in a factory or other production environment so that one operator can control the entire process from a single console. This level of integration requires a high degree of standardization and coordination among equipment suppliers, but the benefits can be substantial.
In a totally automated environment, a single operator can oversee the entire production process, from start to finish. This eliminates the need for multiple operators to manage different aspects of the production process, which can lead to errors and inefficiencies. By reducing the number of operators needed, TIA can also help to reduce labor costs.
In addition, TIA can improve the consistency and quality of products by reducing the potential for human error. When an operator is responsible for multiple tasks, there is a greater potential for mistakes to be made. By consolidating all operator functions into a single interface, the chance for errors is greatly reduced.
TIA can also improve safety in the workplace by reducing the number of people who are exposed to potential hazards. In a traditional production environment, multiple operators may be working in close proximity to one another, increasing the risk of accidents. By consolidating all operator functions into a single console, the risk ofoperator exposure to potential hazards is greatly reduced.
Despite the many potential benefits of TIA, there are also some challenges that must be addressed. First, TIA requires a high degree of coordination and communication among equipment suppliers. In order to achieve total integration, all equipment must be compatible with each other and able to communicate with the operator console. This can be a challenge, as different suppliers may use different technologies.
Second, TIA can require a significant investment in new equipment and software. In order to achieve total integration, factories may need to replace older equipment with new, compatible equipment. This can be a costly investment, and may not be feasible for all factories.
Third, TIA can lead to a certain degree of inflexibility in the production process. Once the Factory is set up for TIA, it can be difficult to make changes to the production process. This can be a problem if the product being produced changes frequently, or if the production process needs to be adjusted for different products.
Fourth, TIA can make it difficult to add new products to the manufacturing
A unique perspective: Ai Automated Altcoin Investment
What are some benefits of using totally integrated automation in manufacturing?
Totally integrated automation (TIA) is defined as an automation technology that covers the entire process chain of a manufacturing system. TIA incorporates all levels of automation, from individual production cells to the overall factory process control. Development and utilization of TIA is a key success factor in Industry 4.0 or the fourth industrial revolution.
The benefits of using TIA in manufacturing are many and varied. Perhaps the most important benefit is the ability to achieve a much higher degree of process control and consistency than is possible with traditional discrete manufacturing methods. With TIA, operators have real-time visibility into the status of the production process and can proactively intervene to correct problems as they arise. This results in significant reductions in down time and waste, and increases in productivity and product quality.
Another key benefit of TIA is its ability to provide perfect traceability of products throughout the manufacturing process. This is essential for meeting the requirements of today's highly regulated marketplace and for ensuring product safety and quality.
TIA also enables manufacturers to take advantage of the latest advances in big data and data analytics to optimize their processes and further improve performance. By collecting and analyzing data throughout the manufacturing process, TIA makes it possible to identify inefficiencies and problems that would otherwise go undetected. This information can then be used to make adjustments to the process to eliminate these issues and improve overall performance.
Finally, TIA provides a platform for the integration of robotic and human workers in the manufacturing process. This can lead to the development of so-called "cobots" or collaborative robots that work side-by-side with human operators to enhance productivity and safety.
The benefits of TIA are numerous and impactful. TIA is poised to revolutionize manufacturing and make it more efficient, productive, and safe.
Check this out: S&p Total Return Index Historical Data
Frequently Asked Questions
What is totally integrated automation (TIA)?
Totally integrated automation (TIA) is an open system architecture and has been enabling the seamless interaction of all automation components, the software involved, and higher-level systems and services since 1996. TIA helps companies automate their business processes in a more efficient and effective way by integrating all automation components, including operating systems, middleware, and applications from different vendors. This allows enterprise managers to manage their automated business processes through a single management platform with consistency across all automation platforms. In addition, TIA provides an extensible architecture that can be customized to meet the specific needs of your organization.
Who is using the totally integrated automation solutions?
The totally integrated automation solutions from Siemens are used in many industries such as automotive, infrastructure and logistics, telecommunications, industrial production and more.
What is continuous integration with Tia portal?
Continuous integration (CI) is a well-known software development methodology that helps to optimize the development process and improve quality of the results. CI can also be used in automation projects with TIA Portal. With CI, developers integrate their changes into the source code repository on a regular basis to ensure that the latest code is always available. This helps to improve reliability and quality of the final product. How does continuous integration work with TIA Portal? TIA Portal can assist you with automating your workflow using CI. By using TIA Portal, you can automatically run your tests and deploy your updated applications to specific environments. Additionally, TIA Portal provides integrations with various version control systems (VCSs), including Git, which makes it easy for developers to manage and track their changes. This means that you can effectively monitor and manage your software development process from one central location.
What really holds back progress in digital transformation initiatives?
There are a few key things that typically hinder progress in digital transformation initiatives. The first is the lack of integration across all layers of technology, including hardware, software, and services. This can be due to a number of reasons, such as different platforms, application domains, architectures, or deployment models. Second is the complexity of integrating new technologies into an already operational system. Third is embracing change and learning how to work together in a new environment. Finally, teams need to develop skills in collaboration and communication; without these abilities, it is difficult to achieve success in building an innovative digital platform.
What is the totally integrated automation portal?
The totally integrated automation portal is a centralised online resource where Siemens offers its customers an overview of all its automation and information technology services in one place. It allows users to quickly and easily find the information they need, wherever they are in the world. What kind of resources is available on the TIA Portal? The TIA Portal provides access to a range of resources, including: - Digital planning tools: Use these tools to create automated business processes, reduce complexity and speed up decision-making. - Integrated engineering solutions: Add value to your operations with our range of innovative engineering solutions that help you increase efficiency and improve process reliability. - Automation news and information: Stay current with the latest automation news and insights from across the Siemens network. - Service support: Connect with our global service network for technical assistance, advice and troubleshooting when things go wrong.
Sources
- https://in.mitsubishielectric.com/en/feature/partneringindia/insights/challenges-in-the-industrial-automation.html
- https://www.thinkautomation.com/productivity/ten-benefits-of-automation/
- https://www.linkedin.com/pulse/totally-integrated-automation-future-proof-frame-work-anup-abhyankar
- https://www.youtube.com/watch
- https://de.wikipedia.org/wiki/Totally_Integrated_Automation
- https://blog.attuneiot.com/building-automation-system-bas-integration-challenges-for-commercial-and-industrial-hvac
- https://theecmconsultant.com/business-process-automation-challenges/
- https://www.qaoncloud.com/test-automation-challenges/
- https://new.siemens.com/global/en/products/automation/topic-areas/tia.html
- https://automationprimer.com/2014/02/16/advantages-and-disadvantages-of-automation/
- https://penaltyandpunishment.com/qa/what-is-the-advantages-and-disadvantages-of-automation.html
- https://new.siemens.com/uk/en/products/automation/industry-software/automation-software/tia-portal/tia-portal-v18.html
- https://integrateautomation.com/
- https://cbselibrary.com/automation-advantages-and-disadvantages/
Featured Images: pexels.com