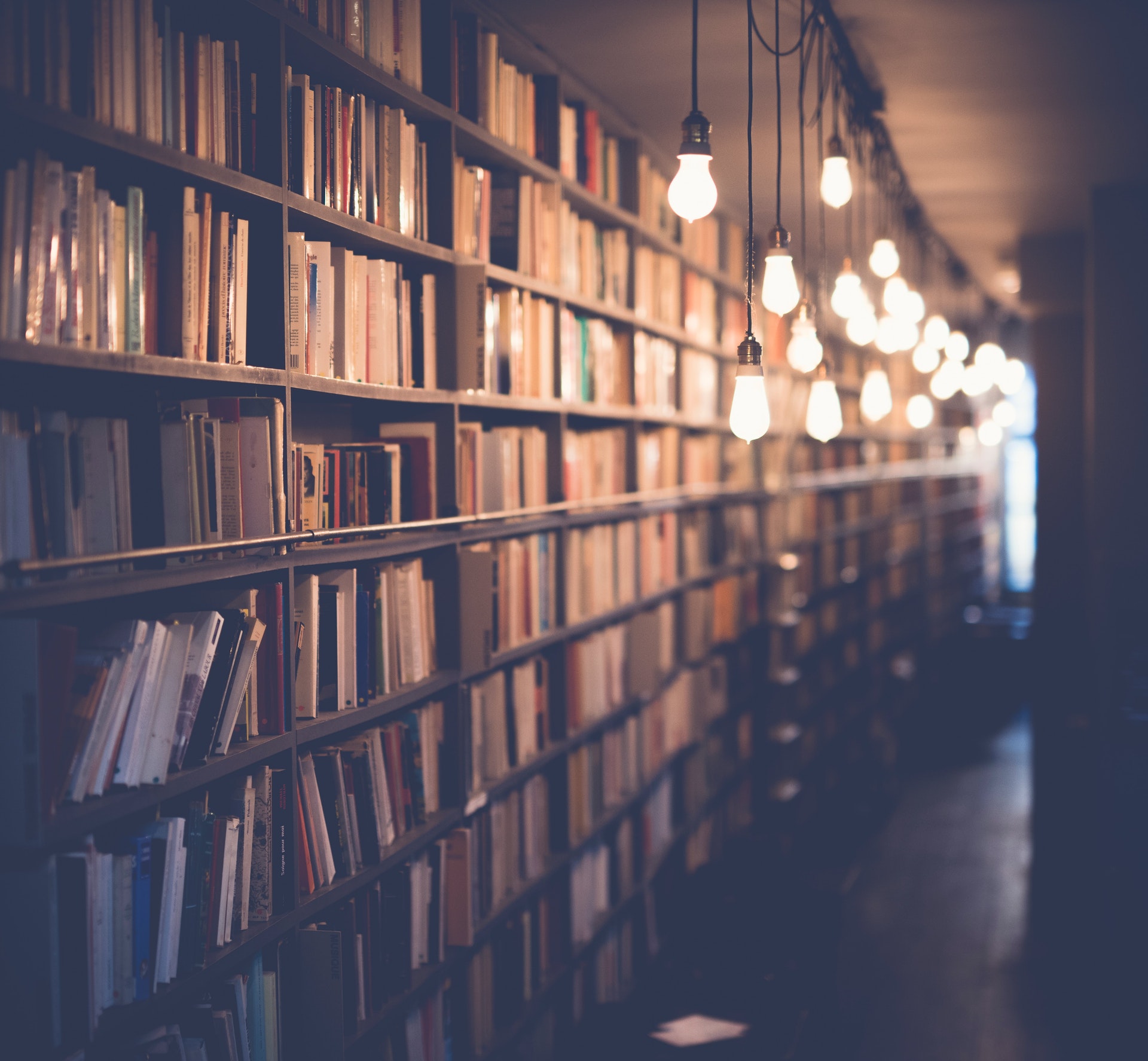
In the early 20th century, the quality control movement in manufacturing was born. This was in response to the need for products to be made consistently well, with as little variation as possible. The goal was to produce products that met the customer's expectations and were free of defects.
One of the key thinkers in this movement was Dr. W. Edwards Deming. Dr. Deming developed the concept of jidoka, which means "automation with a human touch." The idea behind jidoka is that if a machine detects a problem, it should stop and notify a human operator. The human operator can then fix the problem and restart the machine.
Jidoka is a fundamental quality control concept that is still used today. It is based on the idea of continuous improvement and catches problems early so that they can be fixed before they cause major defects. Jidoka can be applied to any process, not just manufacturing.
The jidoka concept is important because it is a proactive approach to quality control. Instead of waiting for the customer to find a problem, jidoka seeks to find and fix problems before they occur. This results in higher quality products and happier customers.
What is the jidoka concept?
Jidoka is a Japanese concept that can be translated to mean "automation with a human touch." It is a philosophy that is rooted in the idea of continuously improving quality and efficiency in manufacturing. Jidoka emphasizes the importance of using machines and other automated processes to their fullest potential, while also incorporating the "human touch" into the manufacturing process. This means that businesses should not rely solely on machines to do all the work, but should also utilize the knowledge and expertise of their employees.
The jidoka concept has its origins in the early 20th century, when the Toyota Motor Corporation was first established. One of the company's founding principles was to always be looking for ways to improve quality and efficiency. This principle was put into practice with the development of the jidoka system, which was designed to immediately stop the production line if a problem was detected. This way, problems could be quickly fixed, and quality control could be more effectively maintained.
The jidoka concept has since been adopted by businesses in a variety of industries, outside of just the automotive sector. The philosophy can be applied to any type of manufacturing or production process, and has been shown to be an effective way to improve quality and efficiency. In recent years, the jidoka concept has also been adopted by service-based businesses, as a way to improve the quality of their customer service.
At its core, the jidoka concept is about using machines and automation to their fullest potential, while also incorporating the "human touch" into the process. This philosophy can be applied in a variety of different ways, depending on the specific needs of a business. But, overall, the jidoka concept is a powerful tool that can be used to improve quality and efficiency in any type of manufacturing or production process.
What are the benefits of jidoka?
Jidoka, also known as the Andon Cord, is a simple but important part of the Toyota Production System. Its purpose is to stop the line when a problem occurs, so that it can be fixed quickly and efficiently. This way, problems are addressed immediately, before they have a chance to cause further issues down the line.
There are several advantages to using jidoka. First, it helps to ensure quality by catching problems early. Second, it saves time by allowing line workers to fix issues themselves, rather than having to wait for a supervisor or technician to come and do it. Third, it saves money by preventing defects from reaching the customer. Finally, it builds morale by empowering workers and giving them a sense of ownership over the production process.
Overall, jidoka is an essential tool for ensuring quality and efficiency in the production process. It is simple to use and understand, and its benefits are clear.
How can jidoka be used in manufacturing?
Jidoka, which can be translated as “automatic stopping” or “self-reliance,” is a principle of lean manufacturing that is based on the idea of giving machines the ability to stop themselves when an abnormal condition occurs. The purpose of jidoka is to prevent defects from being produced and to allow for quick detection and correction of problems.
Jidoka has its roots in the early days of the automotive industry. In the early 1900s, automobiles were handmade and all production was done by skilled workers. The introduction of mass production techniques led to the need for unskilled workers to perform repetitive tasks. As a result, quality control became more important, and jidoka was developed as a way to address these issues.
The principle of jidoka can be applied in many different ways. One common application is known as “ mistake-proofing” or “poka-yoke.” This is a method of designing processes and equipment so that it is impossible to make a mistake or produce a defect. For example, a simple mistake-proofing device is a plug with two prongs that can only be inserted into an outlet one way. This prevents the user from incorrectly wiring the plug and causing an electrical short.
Jidoka can also be used to create an automated stopping point in a process. This allows the operator to quickly identify and correct any problems that occur. For example, many assembly lines are equipped with sensors that detect when a part is missing or not properly oriented. When a problem is detected, the conveyor belt is automatically stopped so that the operator can fix the issue.
In addition to these direct applications, jidoka also has a number of indirect benefits. Perhaps the most important of these is that it helps to create a culture of continuous improvement. Jidoka is based on the idea of stopping the process when a problem occurs, and this requires a mindset shift for many workers. Instead of simply trying to produce as many parts as possible, workers must now focus on quality and on catching and correcting problems. This shift in mindset can lead to a more proactive and preventive approach to quality, which can have a positive impact on the overall production process.
Jidoka is a powerful lean manufacturing tool that can be used in many different ways. By understanding the principles of jidoka, manufacturers can find new and innovative ways to improve quality and efficiency in their
What are some of the challenges associated with implementing jidoka?
There are many potential challenges associated with implementing jidoka into a manufacturing process. One challenge is that jidoka can be difficult to define and implement in a consistent way across a manufacturing process. Another challenge is that jidoka can require significant investment in training and education for workers in order to be effective. Additionally, jidoka can require a higher level of coordination and communication between workers and managers in order to be successful. Finally, jidoka can be challenging to maintain over time as processes and production needs change.
How does jidoka differ from other lean manufacturing concepts?
Jidoka is a lean manufacturing concept that focuses on the quality of the product or service being produced. It is based on the principle of stopping the line when a problem is detected, in order to prevent defects from being passed on to the next process or stage. This allows for problems to be quickly identified and corrected, before they cause further issues downstream.
Jidoka is often seen as the foundation of lean manufacturing, as it sets the stage for other key concepts such as just-in-time (JIT) production and kaizen (continuous improvement). Unlike other methods which may sacrifice quality in the name of efficiency, jidoka ensures that quality is built into the product or service from the start. This not only saves time and money in the long run, but also helps to build customer trust and loyalty.
While jidoka is an important lean manufacturing concept, it is not the only one. Other important lean concepts include:
Just-in-time (JIT) production: This involves producing only what is needed, when it is needed, in order to minimize waste.
Kaizen: Kaizen is the principle of continuous improvement, which means always looking for ways to improve the quality and efficiency of the manufacturing process.
5S: The 5S principle is a tool for organizing the workplace in order to improve efficiency and quality. The 5S refers to the Japanese words for sort, straighten, shine, standardize, and sustain.
Value stream mapping: This is a tool used to understand and improve the flow of material and information throughout the manufacturing process.
These are just a few of the many lean manufacturing concepts that can be used to improve the quality and efficiency of the production process. Jidoka provides the foundation for these other concepts, by ensuring that quality is built into the product from the start. By using jidoka, along with other lean manufacturing concepts, companies can improve the quality of their products and services while also reducing waste and increasing efficiency.
You might like: Time Period Concept Accounting
What is the history of jidoka?
The history of jidoka is a long and complicated one. It is a history that is full of both triumph and tragedy.
Jidoka is a Japanese word that translates to "automatic device." It is a term that is used to refer to a machine or process that can operate without constant human intervention.
The concept of jidoka has its roots in the late 19th century. It was during this time that Japan was rapidly modernizing and industrializing. One of the key figures in this process was Sakichi Toyoda.
Toyoda was a gifted inventor and engineer. He developed a number of groundbreaking technologies, including the loom and the power loom. In 1924, he founded the Toyoda Automatic Loom Works.
The Toyoda Automatic Loom Works was the predecessor of the Toyota Motor Corporation. Toyota is now one of the largest and most successful automakers in the world.
The word "jidoka" was first coined by Toyoda in 1931. He used it to describe a new type of loom that he had developed. This loom was able to stop automatically if something went wrong. This was a revolutionary safety feature that prevented injuries and accidents.
The concept of jidoka quickly spread beyond the loom. It was soon applied to other types of machines and processes. In the years following World War II, jidoka became an important part of the Japanese economy.
Today, jidoka is still an important part of Japanese industry. It is used in a variety of sectors, including automotive, electronics, and food processing. Jidoka is also used in many other countries around the world.
How has jidoka been developed over time?
Jidoka, also known as the Andon Cord, was developed in the early 20th century by Japanese engineer Shigeo Shingo. Jidoka is a production control system that uses a visual signal to alert workers to a problem so that it can be fixed immediately. The Andon Cord is a physical cord that is pulled to stop the line when a problem is detected.
Jidoka has been further developed over time to include electronic and software-based solutions in addition to the physical cord. These solutions allow for more flexibility and faster response times to problems. Jidoka is now an important part of the lean manufacturing process and is used by many companies around the world.
Jidoka has been constantly evolving to meet the needs of modern manufacturing. The latest development is Andon 2.0, which is a cloud-based solution that integrates with existing manufacturing systems. Andon 2.0 provides real-time visibility into production line status and can be used to quickly identify and resolve problems.
Jidoka has come a long way since its inception over a century ago. It has evolved from a simple Andon Cord to a sophisticated cloud-based system that helps manufacturers operate more efficiently. Jidoka will continue to evolve to meet the ever-changing needs of the manufacturing industry.
A unique perspective: What Is the Concept of Time Value of Money
What are some of the key principles of jidoka?
There are several key principles of jidoka that can help businesses improve quality and efficiency. First, jidoka produces products with a higher quality by preventing defects from occurring in the first place. Second, jidoka saves time and money by reducing waste and increasing efficiency. Third, jidoka fosters a continuous improvement culture by encouraging employees to identify and solve problems. Finally, jidoka helps businesses adapt to changing conditions and demands by providing flexibility and agility. By implementing these principles, businesses can improve quality, save money, and increase efficiency.
What are some of the applications of jidoka?
Jidoka is a Japanese lean manufacturing principle that can be applied in many different ways to improve efficiency and quality in a manufacturing process. One way jidoka can be used is to stop the line immediately when an error is detected, preventing defective products from being made. This can be done through sensors or workers manually stopping the line. Another way jidoka can be used is to automate dirty or hazardous tasks so that workers are not exposed to potential risks. This could involve using robots to handle hazardous materials or using automated machines to clean dirty parts. Jidoka can also be used to create a streamlined production process by reducing or eliminating unneeded steps. This could involve using conveyor belts to move parts from one station to the next or using automated machines to perform tasks that would otherwise be done by workers.
Jidoka can be applied in many other ways to improve manufacturing efficiency and quality. By using jidoka to stop the line immediately when an error is detected, workers are able to fix the issue and prevent defective products from being made. Jidoka can also be used to automate tasks that are considered dirty or hazardous, protecting workers from potential risks. Additionally, jidoka can be used to streamline the production process by removing unneeded steps, which can help to improve efficiency.
Frequently Asked Questions
What is the difference between just-in-time and Jidoka?
Just-in-time is a manufacturing philosophy that is based on the assumption that products or materials should be delivered to the production line just in time, with no additional inventory. Jidoka is a Japanese term that refers to quality control and manufacturing practices aimed at reducing waste and improving production efficiency.
What is lean manufacturing and how does it work?
Lean manufacturing is a manufacturing technique that involves continuously reducing the amount of waste and improving the quality of products. It emphasizes on the use of proper tools, machines, and processes to help achieve efficiency in the production process. Jidokalean manufacturing is an important part of lean manufacturing as it helps identify potential problems and deficiencies in the flow of work before they become major issues.
What is Jidoka and how does it work?
The Japanese word "jidoka" is translated as "self-control" or "automatic inspection." Jidoka is a manufacturing process management tool that helps supervisors detect and correct abnormalities in the production process before they cause quality defects. Jidoka methods use variation monitoring, visual inspections, and feedback to identify deviations from normal conditions and make corrections before they lead to quality problems. How does Jidoka work? From the very beginning of the production process, jidoka tools keep track of all the steps involved. They then study those steps in detail to look for any unusual or problematic behavior. If something seems fishy, you can trigger an on-the-spot inspection. In extreme cases, you may need to halt production altogether and investigate what went wrong. By letting jidoka take care of routine quality control tasks, you save valuable time and energy for more important matters.
What should I do if the Jidoka process stops?
If the Jidoka process stops, there should be a focus on starting up again once the immediate issue has been resolved. In most cases, restarting the process will resolve the issue.
Who has the authority to stop the process in lean manufacturing?
In a lean manufacturing environment, each individual has the authority and responsibility to stop the process in the event that they find an abnormality. This includes line workers, supervisors, and managers.
Sources
- https://mbsitem.co.uk/jidoka-definition-origins-and-benefits/
- https://chisellabs.com/blog/jidoka/
- https://www.jidoka.fi/wwc2022/
- https://datamyte.com/jidoka-the-lean-manufacturing-method/
- https://leanmanufacturing.online/jidoka/
- https://www.slideshare.net/HarshJoshi80/jidoka-lean-manufacturing
- http://www.aleanjourney.com/2017/03/the-consequences-of-not-doing-jidoka.html
- https://www.ame.org/sites/default/files/target_articles/88q1a1.pdf
- https://trainrocket.com/public/blog/what-is-lean-manufacturing-and-how-does-it-differ-from-other-types-of-manufacturing/
- https://prezi.com/nejtomb75c6t/jidoka-lean-manufacturing/
- https://www.novida.com/blog/jidoka/
- https://in.kaizen.com/blog/post/2013/08/09/the-evolution-towards-jidoka
- https://businesszeal.com/jidoka-process-explained-with-examples
Featured Images: pexels.com