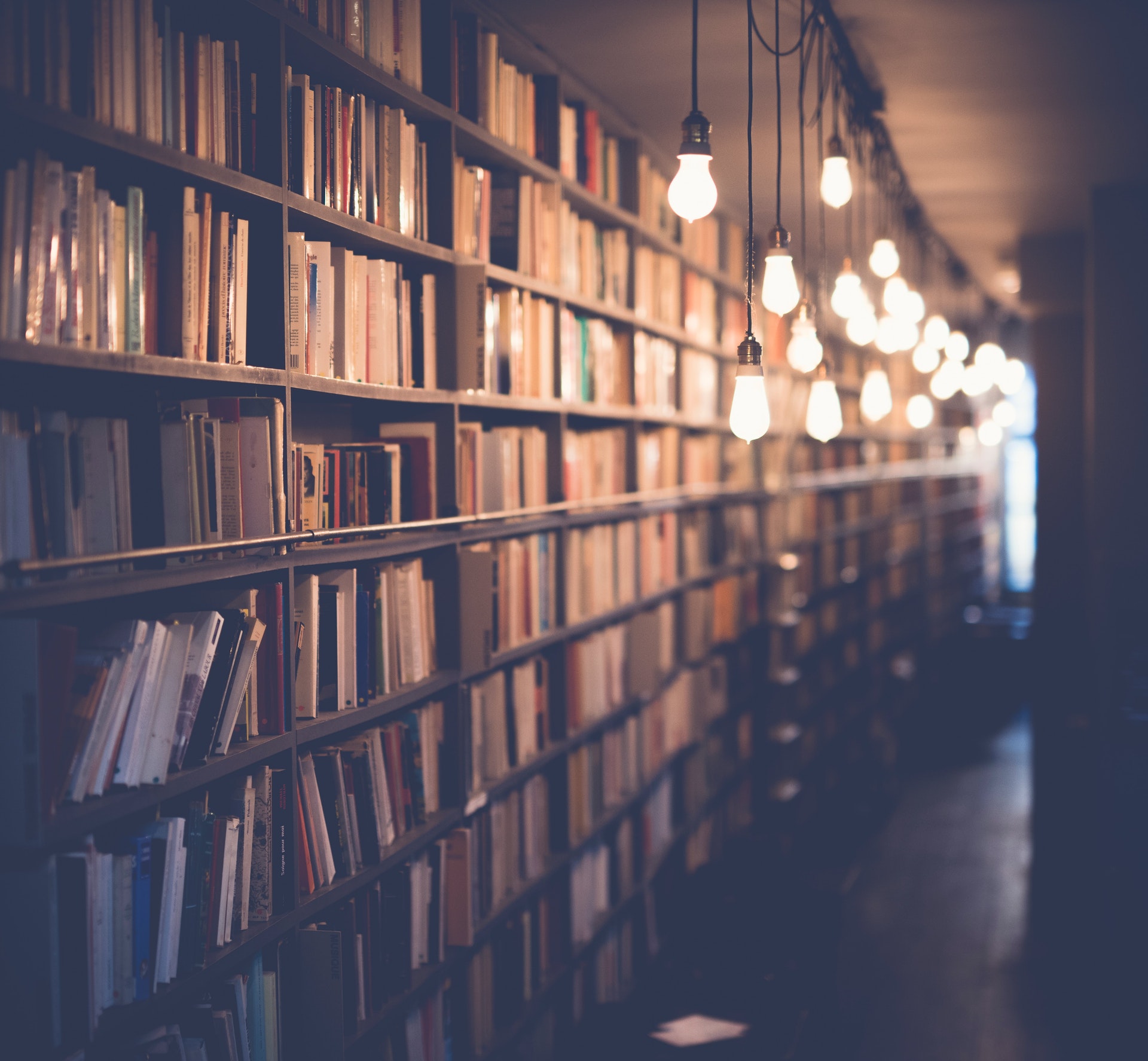
Dip coating is a process in which a fluid is applied to a substrate and then allowed to cure or dry. The substrate can be of any material, but is typically a metal or a plastic. The fluid can be of any type, but is typically an organic polymer such as a paint, a lacquer, or a resin. Dip coating is used to protect the substrate from corrosion, to provide a protective coating, or to give the substrate a desired appearance.
The dip coating process begins with the substrate being placed into a fluid-filled container. The substrate is then immersed in the fluid and allowed to soak for a period of time. The length of time will vary depending on the type of fluid and the desired result. After the soaking period, the substrate is removed from the container and allowed to air dry. The drying process can be accelerated by the use of heat lamps or fans.
Once the substrate is dry, it can be inspected for defects. If no defects are found, the substrate can be used as-is. If defects are found, the substrate can be re-immersed in the fluid and the process can be repeated.
Dip coating is a simple and efficient way to apply a variety of fluids to a substrate. The process is quick and easy to set up, and can be performed with minimal equipment. The process is also relatively forgiving, and defects can be easily corrected. Dip coating is an ideal solution for a wide range of applications.
What are the steps involved in dip coating process?
Dip coating is a process of applying a liquid film to the surface of a substrate. The substrate is dipped into a bath of the coating material, and the excess is then wiped off. This leaves a thin, even coating on the substrate.
Dip coating is used to protect the surface of the substrate from corrosion, wear, and other forms of damage. It can also be used to improve the appearance of the substrate, or to provide a base for further coating or finishing operations.
The first step in dip coating is to clean the surface of the substrate. This is important in order to ensure that the coating will adhere properly. Any dirt, grease, or other contaminants on the surface could prevent the coating from bonding properly.
Next, the substrate is dipped into the coating material. The coating material is typically a liquid, but it can also be a gel or even a powder. The substrate is left in the coating material for a period of time, which allows the material to wet the surface and start to form a film.
After the desired amount of time has elapsed, the substrate is removed from the coating material and any excess is wiped off. The excess coating material is typically removed with a cloth or paper towel.
The last step is to cure the coating. This is typically done by heating the coated substrate. The specific curing conditions will depend on the type of coating material used.
Dip coating is a simple and versatile process that can be used to protect or improve the appearance of a wide variety of substrates.
Recommended read: The First Step in the Capital Budgeting Process Is
What are the factors to consider while selecting a dip coating process?
When it comes to dip coating, there are a few key factors that you will need to consider in order to ensure that you select the best possible process for your needs. Perhaps the most important factor to consider is the type of substrate that you will be using. Dip coating is typically used on metal substrates, so if you are looking to coat a different type of substrate, you may need to look into alternative methods. Once you have determined that dip coating is suitable for your substrate, you will need to decide on the type of coating material that you will be using. There are a variety of different coating materials available, each of which has its own set of benefits and drawbacks. You will need to select a coating material that is compatible with your substrate and that will provide the desired level of protection. Another important factor to consider is the cure temperature. The cure temperature is the temperature at which the coating material will harden or cure. If the cure temperature is too low, the coating may not harden properly and may be susceptible to damage. If the cure temperature is too high, the coating may become brittle and may not provide the desired level of protection. You will need to select a cure temperature that is appropriate for your coating material and for your substrate. Finally, you will need to consider the cure time. The cure time is the amount of time that the coating material will need to harden or cure. If the cure time is too short, the coating may not harden properly and may be susceptible to damage. If the cure time is too long, the coating may become brittle and may not provide the desired level of protection. You will need to select a cure time that is appropriate for your coating material and for your substrate.
What are the types of dip coating process?
Dip coating is a process in which a liquid coating material is applied to a substrate by immersing it into the coating material. The substrate can be a variety of materials, including metals, plastics, glass, and even paper. The coating material can also be a variety of materials, including paints, varnishes, adhesives, and even metals. The most common type of dip coating is probably paint coating, in which a paint is applied to a substrate to protect it from the environment or to improve its appearance.
There are two main types of dip coating process: Immersion Coating and spraying. Immersion coating is the most commonly used dip coating process. In this process, the substrate is immersed in the coating material, and the coating material is then allowed to dry on the substrate. This type of coating is often used for thicker coatings, such as paint coatings. Spraying is the other type of dip coating process. In this process, the coating material is sprayed onto the substrate. This type of coating is often used for thinner coatings, such as varnishes and adhesives.
The choice of dip coating process depends on the type of coating material and the substrate. Some coatings, such as paint coatings, can be applied using either process. Other coatings, such as metal coatings, can only be applied using the immersion process. The substrate also influences the choice of process. Some substrates, such as metals, can be coated using either process. Other substrates, such as plastics and glass, can only be coated using the spraying process.
There are several advantages to using the dip coating process. One advantage is that the process is relatively simple and does not require special equipment. Another advantage is that the process can be used to coat a wide variety of substrates. Finally, the process can be used to coat a wide variety of coating materials.
Consider reading: Hard Coated Windshield
What are the applications of dip coating process?
Dip coating is a process where a metal or plastic object is dipped into a vat of molten metal or plastic. The object is then removed from the vat and allowed to cool. This process can be used to coat the object with a thin layer of metal or plastic. Dip coating can be used to protect the object from corrosion or to improve its appearance.
Broaden your view: Powder Coat Plastic
What are the advantages of dip coating process over other coating processes?
Dip coating can be used to coating process that is faster and more efficient than many other methods. It can produce a smooth and even coating on the substrate and can be used to coat large areas quickly. The disadvantages of dip coating include the potential for runs and drips, and the need for a well-ventilated area to avoid fumes.
What are the disadvantages of dip coating process?
Dip coating is a process where a piece of metal is dipped into a vat of liquid metal, typically zinc, to coat the piece. The disadvantage of this process is that it can be quite messy, and the piece being dipped must be cleaned thoroughly before it is coated. The process can also be time-consuming, and if the piece is not properly cleaned before being dipped, the coating may not adhere properly.
Discover more: Metal Coat
How can the dip coating process be improved?
Dip coating is a relatively simple process that can be used to coat a wide range of materials. It is often used to protect metal surfaces from corrosion, but can also be used to apply other coatings, such as paint or insulation. Dip coating is a relatively quick and easy way to coat a large surface area, but there are several ways that the process can be improved.
One way to improve the dip coating process is to increase the number of coats that are applied. This will help to improve the coverage of the coating and also make it more durable. It is also important to make sure that the coats are applied evenly and that there are no gaps or areas that are not properly coated.
Another way to improve the dip coating process is to use a better quality of coating material. This can be done by using a higher quality paint or by using a different type of coating altogether. There are a wide variety of coatings that can be used for dip coating, so it is important to experiment with different types to find the best one for the job.
Finally, the dip coating process can be improved by increasing the temperature at which the coating is applied. This will help to improve the adhesion of the coating and also make it harder and more durable. It is important to make sure that the temperature is not too high, as this can damage the material that is being coated.
Improving the dip coating process is important in order to coat materials more effectively and to make the process more durable. By increasing the number of coats, using a higher quality coating material, and increasing the temperature, the dip coating process can be improved to provide better results.
A different take: Lg Stainless Steel Refrigerators Coated
What are the future trends in dip coating process?
The future trends in dip coating process can be broken down into two areas: process advancements and process monitoring. In terms of process advancements, there is a trend towards automated systems that can control multiple parameters and optimize the process. This will lead to more consistent and repeatable results. In terms of process monitoring, there is a trend towards using real-time monitoring to understand the process and identify areas for improvement. This will lead to a better understanding of the process and how to optimize it.
Frequently Asked Questions
What is plastic dip coating and how does it work?
The plastic dip coating process involves immersing a preheated part into liquid Plastisol to form a polymerized or cured coating that can add protection and aesthetics to most metal parts. Depending on the coatings used, it can enhance the appearance of the part, provide a soft grip, or protect the part from chemicals and abrasion.
What is Plastisol dip coating and how does it work?
Plastisol dip coating is a process that involves immersing a preheated part into liquid plastic to form a plastic coating that can add protection and aesthetics to most metal parts.
What is dip coating?
What are the usages for dip coating? Dip coating is commonly used to finish products such as metal, plastic, and composites. It is also frequently used in manufacturing processes, such as the production of electrical components and medical devices. Dip coating provides a durable finish that can resist wear and tear.
Can Plasti Dip be used on plastic?
Yes, Plasti Dip can be used on almost all surfaces, plastic inclusive.
What are the different parts of dip coating?
There are three essential parts in the dip coating process: immersion, dip time, and removal. Immersion is the first step and is exactly what it sounds like: immersing the substrate material in the conformal coating. What are the different types of dip coating? There are three general types of dip coating: wet end printing (WEP), dry end printing (DEP), and inline coating.
Sources
- https://www.3ds.com/make/guide/finishing/dip-coating
- https://www.jessupmfg.com/blog/dip-coating-processes.html
- https://www.dipseal.com/plastic-dipped-parts-tools-and-corner/what-are-dip-coated-products-and-how-are-they-protected
- https://www.ossila.com/pages/dip-coating
- https://brinkerlab.unm.edu/assets/publications/2013-publications/dip-coating-brinkerdipcoating2013.pdf
- http://www.apexicindia.com/technologies/dip-coating-technology
- https://www.advancedcoating.com/blog/what-is-dip-coating
- https://www.mechdiploma.com/what-are-factors-be-considered-selection-materials-design-machine-elements
- https://www.cambridge.org/core/journals/mrs-online-proceedings-library-archive/article/physics-and-applications-of-dip-coating-and-spin-coating/CDF5D7C6BF44B3F923D6E2B6719D512F
- https://www.integrativemedcongress.com/advantages-and-disadvantages-of-plasti-dip/
- https://pubs.rsc.org/en/content/articlelanding/2011/jm/c1jm12837j
- https://www.researchgate.net/publication/286061999_Dip_Coating
- https://pubmed.ncbi.nlm.nih.gov/28591980/
- https://eoncoat.com/future-coatings/
Featured Images: pexels.com