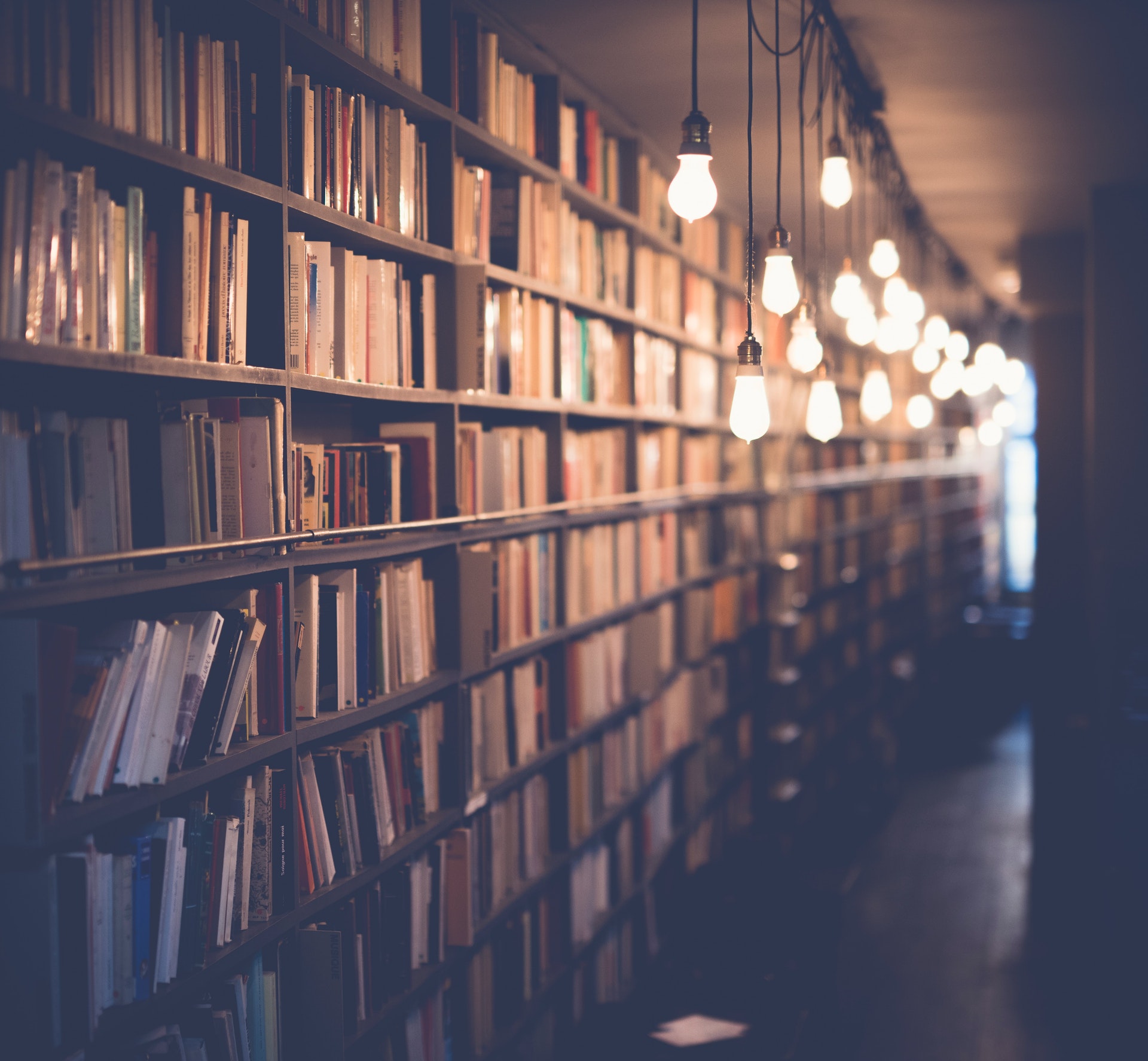
Maintaining the infrastructure of any small or large organization requires a well-thought-out plan and execution. Planned maintenance is an essential plan used to ensure that equipment and services are running correctly and efficiently at all times. As with any complex task, planned maintenance includes a variety of phases that must be followed in order to have it completed successfully. Here we will discuss the four phases of planned maintenance so you can be sure your infrastructure runs as smoothly as possible.
The first phase of planned maintenance is preventive or proactive maintenance activities such as periodic inspections, lubrication, cleaning, testing and replacing parts when required. This type of preventative care allows for potential issues to be identified before they become serious problems which saves time and money in the long run by avoiding expensive damages or disruptions caused by breakdowns. Additionally, these regular checkups increase overall system uptime resulting in better resource use efficiency on individual pieces of equipment or services alike.
The second phase involves putting together a detailed plan outlining work orders that need to be done efficiently during scheduled downtime periods where regular operations can stop temporarily while repairs get made safely without disruption occurring elsewhere within the organization’s infrastructure systems. It also requires establishing repair teams along with their respective roles so every necessary goal gets met without delays happening during repairs due otherwise inefficient processes being assigned out wrongfully ending up holding back steps needed for completion timely fashioning its goals excellent molds tailored adequately towards satisfying resolutions
The third stage includes preparing the resources necessary for completing work orders like assuring personnel have adequate training beforehand going into duties involving repairs' setup parameters required necessarily unifying them accordingly getting information gathered correctly throughout individual steps process too allowing program creators necessitated authorization conveniently received prior executing certain methods complexes entailing specific instructions meeting designated outputs expected knowing precisely when limits gotten come close appearing around corner crunching some data along way showing discrepancies overlooked nothing staying hidden apparent eyes viewing things accurately details matters taking extreme importance here final results depend upon accomplished undoubtedly superlatively starting necessary foundation works progress implementation essentially solidly connected foundation occurs definitely preceding success coming ahead already guarantee assimilating important components becoming worthwhile endeavors eventually surpassing standards estimating those reaching levels exceeding expectations widely seen opinion present days gone ones defining advancement times.
Lastly, the fourth phase is post-maintenance evaluation involving review monitoring after specified period ensuring results match outlined aims intended individuals operating given roles adhered rules & regulations enforced keeping functionality within particular boundaries compared against concerning aspects processing desired conditions likely experienced compiled analysis data arrived meaningful conclusions basements building design chart displays summarizing progression gradually inevitably displaying flowcharts make faster easier understanding missing pieces identifying future problem areas troubleshooting applicable solutions applicable resolution entire system comprehensively understood then easily manipulated solve issues quickly whereupon workers sufficiently trained performing relevant tasks receive certification undergo tests circumstances accounted handled preventive measures taken preemptively correcting errors optimize performance save time energy money move towards development instead worrying over maintenances’ continually repeated cycles maintaining past reaches heights encouraging implementation productive maintains environments thriving habitats lively atmospheres grateful citizens leisure life spontaneous amusement blessed knowledge benefits tangible positive outlook society livens peps soul doubt posses forever perfect dreams giving form eagerly await replete satisfaction comes accomplishing milestones plans successful ones definitely greatly lauded admired among peers loved ones family friends circles communities glory.
Consider reading: Convert 2 Phase
What are the different types of maintenance planning?
Maintenance planning is an important aspect of business operations and can have a major impact on the performance and profits of a company. It is important to understand the different types of maintenance planning that exist in order to determine which one best fits your needs.
The three most common types of maintenance planning are preventive, predictive, and corrective maintenance.
Preventive Maintenance Planning involves actions taken before potential malfunctions occur. This type of planning focuses on addressing potential failures or issues proactively so that downtime and costly repairs can be avoided. Preventive Maintenance plans should aim to extend machine life, reduce operating costs, improve operational efficiency, and prevent tragedies or breakdowns due to malfunctioning systems or components. An example would be regularly scheduling oil changes for machinery used in manufacturing processes.
Predictive Maintenance Planning aims at detecting impending failures in equipment based on data collected from various conditions such as temperature readings or vibration analysis that could indicate certain levels of wear-and-tear over time in machines and components used in production processes. Predictive Maintenance practices require ongoing monitoring activities by qualified personnel along with advanced diagnostics equipments such as infrared cameras so regular maintenance checks and component replacement decisions are made in advance before severe consequences occur due to any system malfunctions/failures The goal here is maximum utilization with minimal costs associated with running these routines for assessing condition & performance trends over time (leading up to predictions).
Corrective Maintenance Planning occurs after a failure has taken place within an asset or component part used within a company’s production process(es). In this approach, reactive measures need to be taken so that the necessary repairs are completed quickly without causing too much disruption in operations; allowing companies to operate at their full capabilities as soon as possible following a breakdown event occurring regarding their industrial equipments & toolsets being used for services operations/productions output flows everyday/periodically throughout all hours schedules working conditions across shifts happening round (daily) clocks then following step re-assemblies post repairing any damaged parts thereafter making sure everything consisting all new sets comes back together piece by perfects ready run once again normal cycle proceedings properly like how things were “previously” prior action just happened about here this case near recent occurrence times took places between until situation fixed back originals modes working orderly shapes holding steady strong moves coming forthcoming now through when cycle repeats continuums all times into shows finish finished ultimate goals attained here without fail goings alright & smooth sailing peacefully afterwards..!
For another approach, see: 4 Types
What is the purpose of planned maintenance?
The purpose of planned maintenance is twofold. First, it helps to keep your equipment running efficiently and with minimal breakdowns so that it can be used in a safe and reliable manner. Second, planned maintenance also reduces the chance of unscheduled downtime due to system failure or other unexpected problems.
Planned maintenance can take on many forms depending on the type of machinery and equipment involved. Generally speaking, this type of preventative care consists of regular inspections, lubrication service work, cleaning, adjustments or replacements of worn parts as well as general monitoring activities such as taking temperature readings or checking oil levels in order to catch any developing issues before they become major problems.
By scheduling periodic maintenance ahead of time, you avoid more costly repairs down the line that would be necessary if a piece of equipment were allowed to degrade over time and then suddenly break down all at once. Having a regular schedule for such preventive activities will not only prolong the life span for your machinery but can also help improve its overall performance throughout its use-life helping you get more from your investments each year.
Furthermore, when done correctly planned maintenance provides training opportunities for staff members by allowing them first-hand experience with practical application procedures as well as aiding them in becoming familiar with their available tools and resources so that they are better prepared should something ever go wrong later on down the road. From this perspective, scheduled upkeep does far more than simply protect against possible drifts – it adds tangible value through improved employee knowledge acquisition who may help identify potential minor issues earlier before they cause significant disruption if left unchecked worst case-scenarios like complete system shutdowns could be avoided altogether thus ensuring maximum business continuation during less pleasant situations in an organization’s lifecycle.
A unique perspective: Time Management
What are the key elements of an effective maintenance plan?
If you want to keep your equipment and machinery running smoothly, an effective maintenance plan is essential. A successful maintenance plan should include regular preventive maintenance, which can help reduce down time and prevent costly repairs. It's also important to take into account the age and type of your equipment, as different types require different levels of maintenance attention.
The key elements of an effective maintenance plan are:.
1. Regular Inspections – Inspections should be performed regularly in order to identify any potential problems before they become serious issues that may cause downtime or expensive repairs. During the inspection process all accessible parts should be examined for signs of wear or damage, including checking for loose bolts or screws, oil levels, improper lubrication and more.
2. Preventive Maintenance – Regularly scheduled preventive maintenance is an essential part of any effective maintenance program; it helps identify potential issues before they become bigger problems that could lead to downtime or more costly repairs down the line. This type of ongoing servicing can be conducted by technical professionals and involves consistently replacing worn parts with new ones before more major components fail due to wear-and-tear over time.
3 Proper Documentation – Accurate record keeping is a must when it comes to tracking a successful business’s equipment reliability; any repair or servicing performed needs to be documented properly in order for a comprehensive assessment on future work requirements based on past performance data management system introducing capable creating electronic reports will identify quickly issues being observed might come out repair times taking less having good document management systems like this which makes available technicians customer service personnel making reliable decisions right away improving performances proactively addressing shortfalls soon monitored often keeping better track productiveness tasks assigned throughout given periods lower risk component failure causing unnecessary downtime much higher costs overcome.
4 Productivity Trending - If detailed documents are kept around each machine’s performance history against its planned schedule then it would be easier decide what need fixed compared other machines similar conditions evaluate entire fleet as whole ensuring component failures likely minimized maximizing production output hence cutting operational expenses incurred plus increase profits made operation overall studying trends gathered implemented stay ahead competition customer satisfaction satisfaction gaining customers loyalty all aspects operation covered cost savings optimization production gains analytics useful identifying commonalities experienced among teams pinpointing areas need improvement trended analyzed upgraded accordingly exponential returns due overall process improvements outlined aforementioned bullet points.
In summary, an effective maintenance program requires proper planning in order for operations run effectively efficiently minimize costs maximize accuracy safety products services rendered outlining key elements discussed above allow business benefit enjoying lucrative uptimes highest possible level along guarantee long lasting relationships customers maintain high quality standards expected them delivered same desirable results facility maintained period checkups minimizing increasing frequency breakdowns providing sustainable means lasting success beyond months years come.
What kinds of preventative maintenance activities are available?
Preventative maintenance activities refer to any intentional effort by an individual or company to maintain equipment, systems and other assets in good condition. While preventative maintenance activities vary depending on the item being maintained, there are a few common categories of activities that can be used to help protect investments.
The most basic type of preventative maintenance activity is preventive inspection. This involves regularly inspecting items and machines, looking for signs of wear and tear or potential safety issues that might need to be addressed. In the case of vehicles and machinery in particular, it also includes regularly changing any fluids required for operation such as oils or coolants.
Another type of preventive maintenance activity is scheduled replacement of consumable parts like filters or batteries. Items such as these should generally be replaced with established intervals in order to ensure proper functionality over time; for instance, air filters often need to be changed every 3 months while smoke detector batteries typically should be replaced once per year.
Preventive cleaning is yet another important type of preventative maintenance activity your company may want to take part in – this refers specifically to keeping all mechanical components clean with regular intervals so as not only maintain their environmental conditions but also avoid potential problems that could arise due greater dirt accumulation over time. Preventive lubrication is closely related; lubricants (e.g., grease) should usually be applied when necessary either manually through hands on application via brush etc., using aerosol sprays (for jobs where more mobility may be required) or automatic applications done through machines - the latter option being the most suitable when dealing with more intricate machineries at industrial scale operations.. Firearms operators may perform their own periodic checks prior a match too!
Lastly, another common type of preventative Maintenance activity relates mostly businesses related trades involving data technology - information technology service management software offers data backup solutions which keeps records up-to-date backed daily too minimize catastrophic losses arising from hardware malfunctions/failures. Such backups allow data owners access key documents saves them valauble hours just trying recoeve lost ones later!
Overall preventive measures taken by individuals companies alike great way help assure investments they made last longer while reducing downtime due repairs/replacements too keeping security concerns at bay too guards against costly emergencies arising operational disruptions!
For another approach, see: Maintenance Required
What are the steps involved in implementing a maintenance plan?
When it comes to creating and implementing a successful maintenance plan, there are several steps that should be taken to ensure that the plan is effective and efficient. These steps include:
1. Identify Maintenance Needs: Before you can create an effective maintenance plan, you need to identify what maintenance needs you have. This could include preventive or corrective measures for specific equipment or processes, as well as any potential recurring problems in your systems. This analysis will give you a better understanding of what needs to be done so that your maintenance plan covers all necessary tasks.
2. Create a Schedule: Creating a schedule for when tasks should be completed is essential for staying on top of equipment maintenance needs and helping prevent downtime due to system failures or breakdowns. You should take into account how much time will realistically need to be devoted each month in order for the tasks within the plan to get done on time. This includes accounting for the labor required, parts needed, and any other resources associated with specific jobs within the plan itself.
3 Establish Priorities: Once a schedule has been created it is important to establish priorities so that certain jobs can take precedence over others if needed due to unforeseen circumstances such as weather or other external factors which may influence how quickly you can complete each job within your overall schedule. Prioritizing jobs also helps ensure nothing gets forgotten about when unexpected events do occur which have an impact on when particular task can get finished.. Additionally, by establishing priority levels, it makes easier for teams working together on different projects since everyone knows where their focus should go first..
4 Document Results & Refine Plan: After every round of maintenance activities have been completed, it’s important document all results from those attempts in order gain insight into what worked/what didn’t work and potential challenges facing future rounds of work. By doing this, organizations can build upon previous successes while also identifying areas where more attention might be needed during future rounds so they don’t commit the same mistakes twice.. When necessary refine aspects of those plans based off feedback collected from technicians conducting tasks included within them
By completing these 4 steps organizations are able put together comprehensive plans which help keep operations running at peak efficiency while also maximizing their investments by reducing downtime caused by poorly maintained/older systems. With proper upkeep facilities see major savings over time as serving costs remain low due less frequent replacements being required."
Here's an interesting read: Furnace Maintenance Include
What criteria must be met for an effective maintenance plan?
For an effective maintenance plan to be implemented, there are several criteria that must be met. Effective maintenance plans should take into consideration the age, condition and use of the items being maintained. The cost of the maintenance should also be taken into account as well as any training or resources required by personnel to complete the tasks. Additionally, inventory management should also be given attention so that materials and parts are readily available when needed. Regular assessments and inspections should occur to ensure everything is up to standard and working correctly in order to prevent unnecessary problems.
The overall goal of a successful maintenance plan is to reduce downtime, increase safety, improve efficiency and extend product life wherever possible. For this reason reliability engineering strategies such as failure analysis and root cause analysis help identify potential problems before they arise in order for corrective actions can be taken ahead of time instead of in response after a problem has already occurred. The success or failure of any given maintenance strategy is highly dependent on these factors being considered thoroughly from the outset in addition to a well-crafted implementation. While there will always some variation among different plans based on their purpose or industry requirements, meeting these criteria puts an organization on track for ensuring an effective maintenance plan with minimal disruptions from unplanned repairs or replacements along correct lines throughout its operation under normal conditions
Sources
- https://www.mathsisfun.com/games/connect4.html
- https://4-h.org/about/history/
- https://en.wiktionary.org/wiki/4
- https://www.michiganlottery.com/games/daily-4
- https://www.merriam-webster.com/dictionary/different
- https://www.vocabulary.com/dictionary/different
- https://www.youtube.com/watch
- https://www.thefreedictionary.com/different
- https://www.4town.com/
- https://www.thesaurus.com/browse/different
- https://www.thefreedictionary.com/4
- https://www.dictionary.com/browse/different
- https://www.youtube.com/watch
- https://www.merriam-webster.com/thesaurus/different
- https://en.wikipedia.org/wiki/4
Featured Images: pexels.com