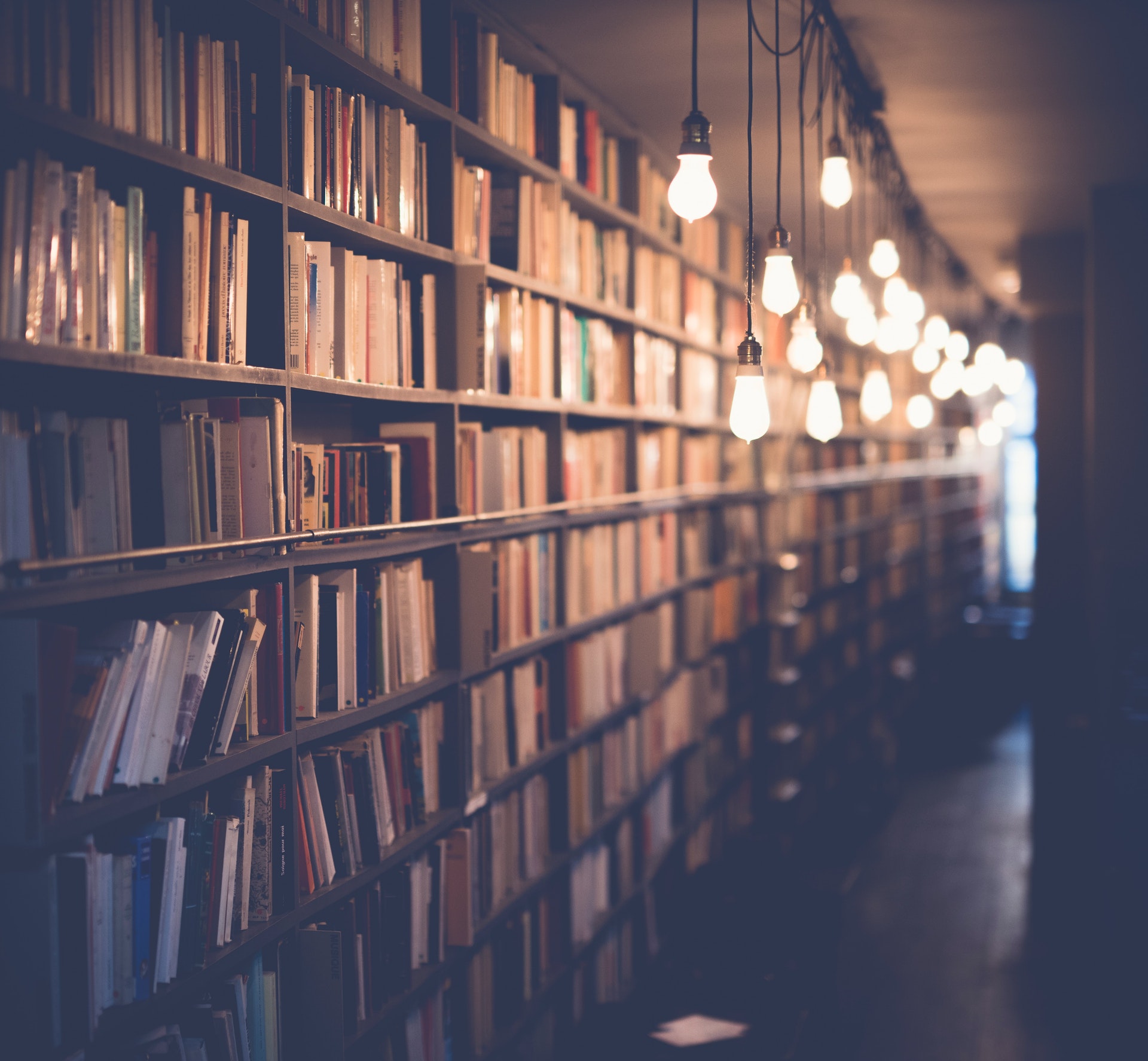
Copper rivets are most commonly used in the construction of boats and ships. They are also used in the construction of bridges, buildings, and other structures where steel or aluminum rivets would be less suitable. Copper rivets have excellent corrosion resistance and are not subject to galvanic corrosion.
What is the difference between copper and aluminum rivets?
There are a few key differences between copper and aluminum rivets. First, copper rivets are significantly stronger than aluminum rivets. This is due to the fact that copper is a stronger metal overall. Additionally, copper rivets are more resistant to corrosion than aluminum rivets. This is because aluminum is more prone to oxidation, which can cause it to break down over time. Finally, copper rivets are more expensive than aluminum rivets. This is because copper is a more expensive metal than aluminum.
Why are copper rivets used in some applications?
Copper rivets are most commonly used in leather working, where they are used to join two pieces of leather together. They are also used in canvas work and other applications where a strong, permanent joint is required. Copper rivets are less likely to corrode than other types of rivets, and their strength and durability make them ideal for use in high-stress applications.
How do copper rivets compare to other fasteners?
Copper rivets are a type of fastener used to join two or more pieces of metal together. They are preferred over other types of fasteners, such as steel or aluminum, because they are less likely to corrode or rust. Copper rivets are also stronger and more durable than other types of fasteners.
What are the benefits of using copper rivets?
There are many benefits of using copper rivets. Copper is an extremely strong and durable metal, which makes it ideal for use in construction and engineering applications. Copper rivets are less likely to rust or corrode than other types of rivets, and they can be used in a wide variety of environments. Copper rivets also have excellent electrical and thermal conductivity, which makes them ideal for use in electrical and heat-sensitive applications.
What are the drawbacks of using copper rivets?
The drawbacks of using copper rivets are many and varied. Copper rivets are softer than other metals, so they are more likely to deform under load. This can cause problems with the seal between the rivet and the material being joined, leading to leaks. Copper rivets are also more expensive than other metals, so their use may not be justified in some applications.
A fresh viewpoint: Why Are Used Teslas so Expensive?
How do I choose the right size copper rivet for my project?
Copper rivets are one of the most commonly used fasteners in a variety of industries. But how do you know what size rivet to choose for your project? Here are some factors to consider:
1. The thickness of the material you're joining. Heavier materials require larger rivets.
2. The number of layers you're joining. More layers require larger rivets.
3. The amount of force that will be exerted on the joint. Higher forces require larger rivets.
4. The type of joint you're creating. Some joints are more critical than others and require stronger rivets.
5. The environment the joint will be exposed to. Certain environments, such as salt water, require corrosion-resistant rivets.
Once you've considered all of these factors, you can select the size of rivet that will best suit your project.
Intriguing read: Joint Roller
How do I install copper rivets?
Installing copper rivets is a simple process that can be done at home with a few tools. Copper rivets are more durable and have a nicer appearance than other types of rivets.
First, drill a hole in the material where the rivet will be installed. The hole should be slightly smaller than the diameter of the rivet. Next, insert the copper rivet into the hole. Be sure that the head of the rivet is on the outside of the material.
Then, use a hammer to gently tap the other end of the rivet until it is flush with the material. Finally, use a file or wire brush to remove any sharp edges from the rivet.
What are some common uses for copper rivets?
Copper rivets are commonly used in construction, leather working, and carpentry. They are also used in some types of jewelry.
Construction: Copper rivets are often used to fasten together metal sheets or parts. This is because copper is a very strong metal that can withstand a lot of force.
Leather working: Rivets are commonly used in leather working to join two pieces of leather together. Copper rivets are often used because they are strong and they do not rust.
Carpentry: Rivets are also used in carpentry to join two pieces of wood together. Copper rivets are often used because they are strong and they will not rust.
Jewelry: Copper rivets are sometimes used in jewelry. They can add a nice decorative touch to a piece of jewelry.
Broaden your view: Which Suppliers Should Not Be Used Feasibility?
Frequently Asked Questions
What are the different types of rivets used in manufacturing?
There are several different types of rivets used in manufacturing, including the following: Round rivets: Round rivets are the most common type and feature a traditional design consisting of a shaft and head. Boxed rivets: Boxed rivets are commonly used to join metal sheets or plates together. They are made up of two pieces of metal that have been drill-pressed together to create a rectangular hole. Then, the rivet is inserted into this hole and “boxed” closed by hand or by using a machine. Flat rivets: Flat rivets are similar to boxed rivets, but their holes are lessened in size so that they can be put through harder materials more easily. They’re also used for joining pieces of metal that don’t need to be joined together tightly.
What is a tubular rivet?
Tubular rivets are semi-hollow rivets used to join materials. They have a manufactured head on one side and a hollow end that sticks through the pieces being joined. The hollow end is cold formed to a field head.
What are the different types of solid rivets?
There are three main types of solid rivets: round head rivets, hexagon head rivets, and octagon head rivets. Round head rivets are the most common type and have a round hole in the middle of their heads. Hexagon head rivets have a hexagonal hole in the middle of their heads. Octagon head rivets have an octagonal hole in the center of their heads.
How to install rivets on metal?
There are a few ways that rivets can be installed on metal, depending on the type of rivet and the material being used. Rivets can be placed using a traditional hammer and anvil, or they can be put in place with a CNC machine.
What are Almac® coated rivets?
Almac® coatings are used on rivets and fasteners to improve corrosion resistance, with the addition of copper making for a stronger joint.
Sources
- https://www.superwhat.org/are/are-copper-rivets-strong/
- https://prairierivet.com/10-common-uses-for-rivets/
- https://www.copperhealthsolutions.com/articles-studies/13-incredible-benefits-of-copper
- https://material-properties.org/uses-of-copper-and-copper-alloys-application-definition/
- https://www.appollobath.com/the-difference-between-copper-alloy-aluminum.html
- https://knowledgeburrow.com/why-are-rivets-popular/
- https://www.quora.com/What-is-the-difference-between-steel-and-aluminum-rivets
- https://www.ajreeves.com/copper-rivets.html
- https://alasscoonlinestore.com/our-products/fasteners/rivets/copper-rivets/
- https://allfasteners.com/products/rivets/copper-rivets.html
- https://www.creativefasteners.com/copper-rivets/
- https://www.linquip.com/blog/what-is-the-difference-between-a-blind-rivet-and-a-pop-rivet/
- https://www.multifixdirect.com/blog/post/rivets-and-their-uses-everything-you-need-to-know-about-rivets.html
- https://www.mechanicaleducation.com/2021/12/advantages-and-disadvantages-of-rivets.html
Featured Images: pexels.com