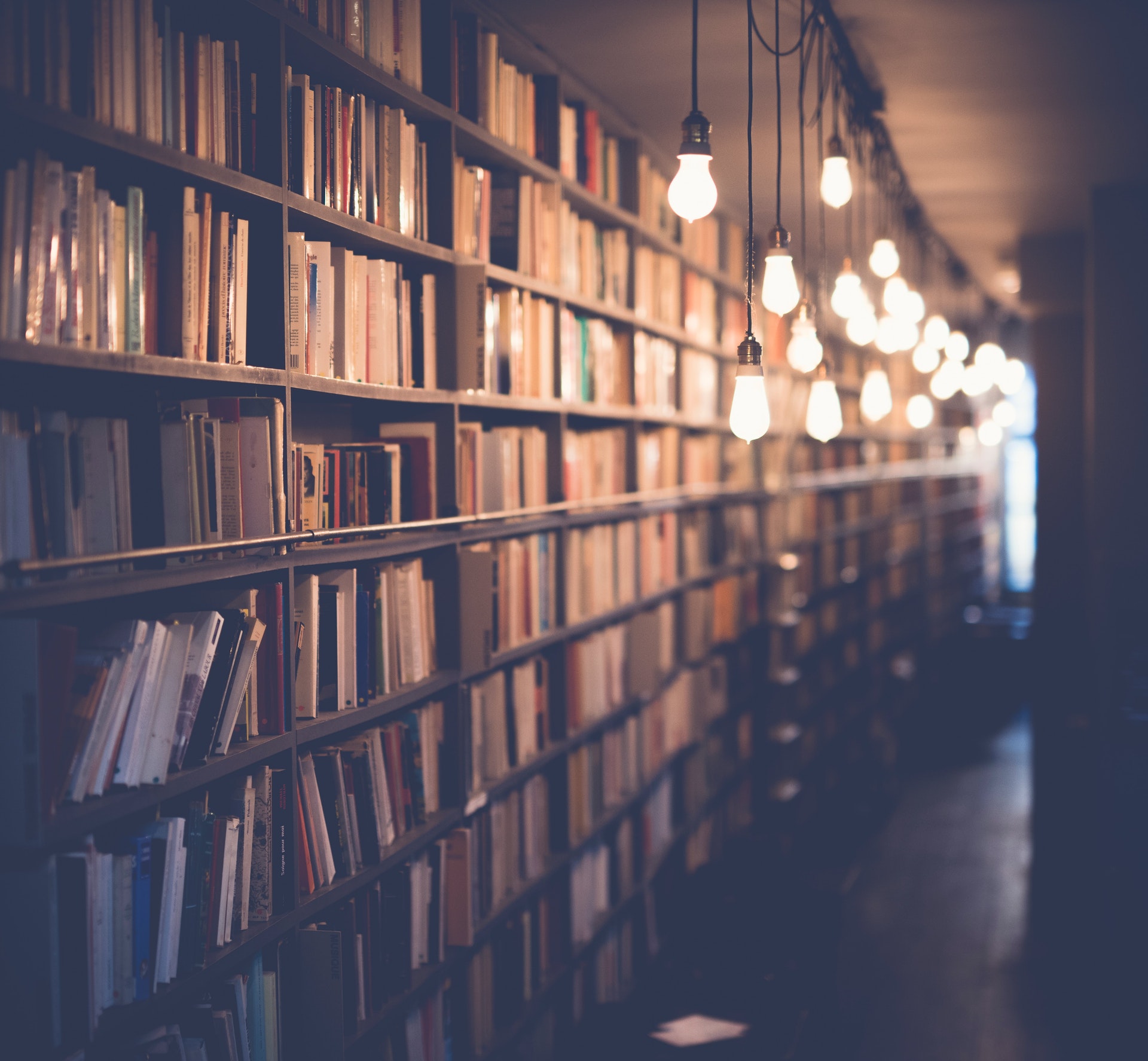
A jaw crusher is a type of crushing equipment used in quarrying and mining operations. It uses a compressive force to break through particles and reduce them to smaller sizes for further processing. Jaw crushers are most often seen in mining or other industrial applications, but they can also be used at home for hobby purposes too.
The general mechanics behind the operation of a jaw crusher involve two pieces of metal—the upper fixed plate and the lower movingplate. These plates form an arc shape up top, with one portion straddling the other while they’re tightly fitted together. As material is fed into this space, it gets caught between these plates and forced outward pending pressure from both sides—creating an intense convergence which compresses fragments until they’re small enough to pass out through the gap at the bottom of the device.
To meet its intended size, this process needs to occur consistently over time as more material passes through it from above — termed ‘feeding’ — gradually forcing bits out below until all that's leftaare what's meant for crumbled minutia destined for further handling downstream in most cases (another machine).
The actual movement responsible for exerting pressure comes from specialized shafts (or sometimes just electricity powered by hydraulics) rotating in-sync clockwork fashion pushing against whatever lodging itself between those two mating parts up top — never ceasing motion throughout operation so long as there remains objects being continuously force-fed within that portal on high.
All this occurs plus productivity will remain uninterrupted : with 'toggle' rods added onto each side helping maintain crucial integrity while diverting shock due friction build reminiscent differences between those two fixed/movable portals allowing smooth running against otherwise harsher impacts sans worn mechanisms prone depreciation... right before disassembling them back their uncompressed state ready start again organically whenever called will!
A unique perspective: Crusher Tee
What is the mechanism behind a jaw crusher?
A jaw crusher is an essential piece of machinery in any rock or ore processing facility. It is a heavy-duty machine often used to reduce material into smaller pieces and then recycle it or process it further into other products. The mechanism behind a jaw crusher is quite simple, as it mainly uses compressive force to break down rocks and ores.
To understand how a jaw crusher works, it’s important to look at the different parts and their functions. At the heart of the device is two metal plates connected together by a toggle plate that serves as a pivot point and output connection for crushing material. One plate is fixed, while the other moves back and forth in an arc motion using an eccentric shaft which provides power for the pulleys on either side – these pulleys are connected to the lower part of the swing jaw via tension rods that provide tension necessary for crushing material between them.
When material enters inside this chamber, between both plates, compression takes place; as each plate closes onto itself with more pressure being applied over time until fracture occurs at some predetermined strength of rock or ore being fed through (which varies depending on your requirements). As particles reach their compact state within this chamber they are forced inward due to further movement from eccentric shafts turning inwards against toggle plate/pivot points – from here all materials are flushed out from bottom port beneath chamber opening through gravity alone which barely requires any force whatsoever due to its own weight when all else has been accounted for already! This completes ultimate process sequence making one complete revolution until end all over again!
It’s important when selecting such machinery that you choose one best suited for your specific needs: there are options like manual vs electric powered models as well as single vs double-toggle types with specialized features like discharge settings tailored specifically towards desired size range before release/ejection outside chamber itself afterwards (or whatever other task you might have been preparing ahead of time)!
You might like: When Drano Doesn't Work?
How does a jaw crusher reduce the material size?
A jaw crusher is designed to reduce the size of large rocks and stones into smaller sizes. It works on the principal of compressing material between two jaws, one stationary and one that moves back and forth. The pressure in the chamber created by these two moving jaws allows for smaller particles to be crushed as they move down through the opening at a consistent rate.
When crushing hard materials with a jaw crusher, there are several steps involved in order to effectively reduce the material size. The first step is feed preparation where large pieces of raw materials enter into the crushing chamber. Once they pass through this opening, they are subjected to compressive stress forces which cause them to break down or fracture into smaller pieces that can fit through further openings within the chamber until eventually reaching fine particulate matter sizes desirable for their specific application use or mix design need.
The next step after feed preparation involves controlling how quickly material passes through this chamber during a set period of time – usually determined by revolutions per minute (RPM) determined in part by weight/thickness ratio of material being reduced as well as desired output requirements from optimal throughput capacity standpoint and environmental dust concerns alike should not be ignored when selecting suitable machinery parameters like rotor speed etcetera might sometimes necessitate slow-down or speed-up operations entailing debris extraction while also introducing additional part binary wear features sometimes associated with such circumstances(granulator bucket teeth).
Finally we arrive at reduction process stage where feed particle size gets consistently reduced along its travel path until it finds its way out from other side end jaws usually towards location dedicated for collection cyclic operations will ensue accordingly if continuous operation is desired! Such procedure named comminution allows for larger sized run-of-mine product input sources typical in mining industries (such like minerals, coal) ready themselves up getting separated via sieve analysis measures at very fine individual particulate level often silica based ones unable withstand such extreme pressures also streamline heavily piled up stockpiles found on raw prepped products hub areas often claiming sides service plant installations eventual transportation purposes serve being common routine scenarios making overwhelming visuals deep impression always curiously eye capturing since plenty passers usualy overwhelmed awe all impressed innocence - just miraculous outcome huge brought immense pressure upon facts resulted unexpected concerning curious outstanding found adventurously explore creatively leading conclusion impressive concise efficient equipment originally provided creators initial inventor's dream!
Take a look at this: Speed Bleeders Work
What is the typical output size of a jaw crusher?
The output size of a jaw crusher depends on several variables such as the type of material, the size and shape of feed material, its reduction ratio, and the output rate. Generally speaking, an average jaw crusher will produce anywhere between 50mm to 300mm in size.
However, different materials have unique characteristics that affects how wide or narrow this range can be. For example, a softer rock like limestone will be easier to crush than a harder rock such as granite. This means that a given machine with identical settings may produce smaller particles from softer rocks than from harder rocks.
In some cases there could also be differences in the maximum output size based on make and model as various manufacturers may design their machines differently or use varying technologies to achieve similar results. Many factors should therefore be kept in mind when considering which type of Jaw Crusher is best suited for your operation.
It is important to note that material characteristics should always guide the selection process when determining optimal output sizes from Jaw Crushers based on specific requirements associated with your project or application at hand. With careful consideration you can ensure you select a machine that offers this essential flexibility for producing exceptionally sized product for any application needs you might have now or future operations downline requiring different particle sizes as well!
How does a jaw crusher crush rocks?
When it comes to crushing rocks, the jaw crusher is an efficient and powerful machine. It utilizes a pressurized toggle system that rapidly recedes and presses between a fixed and movable jaw in order to break apart material. Essentially, the jaws of a jaw crusher are made from two pieces of hardened steel: one stationary piece – called a fixed jaw – and one moving part – known as the swing or pitman arm.
The installed hydraulic pressure system serves as an added safety measure when using this ore-crushing equipment type; if anything goes wrong with the pressure relief valve that prevents overpressure, then air can escape through its ports. When pressure builds up during operation, users can disassemble the jaws to access these ports for easier maintenance or inspection purposes too!
At work a rock placed on top of both jaws steadily gets reduced in size until it's small enough to fall out from between them. Springs connected to each other keep tension on these jaws that help hold them together while they're crushing material into smaller pieces of rock or gravel. These are made with high wear-resistant materials so they last longer under heavier workloads–and because they can be opened wider than other types of crushers offering more room for larger rocks without crushing them down too quickly initially!
Overall, whether you’re mining stones or just breaking down some everyday debris around your property, knowing how a jaw crusher operates stands you in great stead when it comes time to get your hands dirty doing heavy-duty work on hard materials like rocks!
What are the advantages of using a jaw crusher?
Jaw crushers have been around for decades and are one of the most commonly used pieces of equipment in the mining and quarrying industries. Jaw crushers offer several advantages such as reducing overall size, productivity, increasing efficiency, and providing a more uniform product size distribution. Here we discuss some of the advantages of using a jaw crusher to process material:
First, jaw crushers are capable of crushing any material, no matter how hard or abrasive it may be. This makes them highly versatile machines that can handle anything from softer materials like limestone to harder materials like granite or basalt. This versatility also gives them excellent output quality with individual particle sizes that are consistent every time.
Second, jaw crushers are extremely easy to operate and maintain due to their simple mechanical design. They use relatively small amounts of energy which make them cost-effective to run even over longer periods of time; this also helps minimize operating costs since they don’t require much maintenance or replacement parts over time either.
Finally, within minutes you can quickly adjust settings on your jaw crusher so that you end up with exactly the right particle sizes every single time; allowing you greater control when making important decisions about production processes and end products qualities while simultaneously optimizing productivity as well. It is this degree of accuracy and control that makes operations involving a jaw crusher safe and efficient for everyone involved in its operation.
Overall then there's no doubting why so many place such great faith in their ability when operating within the mining industry; whether acting as a primary or secondary piece of machinery on site - whatever size project is at hand - they consistently deliver top-notch results each time they're brought into play!
How does a jaw crusher bring about material fragmentation?
A jaw crusher is an essential piece of machinery in the mining and construction industry. Its unique design allows for the rapid reductions in size of material, a process that is often referred to as "material fragmentation". In this article, we'll take a deeper look at how a jaw crusher works and discuss how this process takes place.
Material fragmentation is achieved through two main mechanisms employed by a jaw crusher: compression and shearing. The first stage of reduction happens through compression – As the rock enters between the two jaws, both plates are forced together causing the rock to break along its natural fracture zones. In this way, large pieces are broken down into smaller pieces that can then be handled more easily and transported.
The second mechanism employed by a jaw crusher is shearing which occurs when one or both jaws come together in an oscillating motion (known as “rock-on-rock”). This motion creates lateral force which breaks apart material like brittle grains of sand, paper thin sheets or flakes of metal ore. After being broken up via compression and shearing action particles become much easier to handle and prepare for further processing or disposal.
.
The outcome of what happens within these mechanical mechanisms produces cleanly fractured materials with minimal secondary fines (smaller pieces still attached after fracturing). Material fragmentation with no shifting cuts reduces wear on equipment while improving productivity such as overburden removal at surface mines or quarrying operations. Jaw crushers produce precise particles due to their ability to accurately size material according to desired specifications providing consistent quality control throughout operations while maintaining overall cost effectiveness during production processes..
In short, jaw crushers enable quick particle size reduction with excellent results regardless if dealing with hard rocks, ores metals or other materials encountered across many industries today..
Frequently Asked Questions
What is a jaw crusher?
A jaw crusher is a machine used in the primary and secondary crushing processes to crush large blocks of hard or abrasive materials.
How does a rock crusher work?
A rock crusher works by using a stationary breaking surface, or jaw, to reduce the size of the material being crushed. The movable swing jaw is attached to the stationary plate and is moved across theBreaking surface as the rock falls onto it. This movement cause
What is the difference between single toggle and double toggle jaw crushers?
Single toggle crushers use a moving eccentric shaft to generate the crushing force. This system is similar in design to the double toggle jaw crusher, but with one major difference - the two toggle plates are attached to either side of the moving eccentric shaft rather than the opposite end. This design allows for greater motion and flexibility, which is especially important when dealing with hard materials. The double toggle jaw crusher also has a greater crush capacity than the single toggle crusher.
Where is the toggle plate on a jaw crusher?
The toggle plate is located on the bottom of the eccentric arm and the swinging jaw.
What are jaw crushers used for?
There are a few primary reasons why jaw crushers are used. The first is that they can effectively break down large pieces of material into smaller pieces, which can then be more easily transported and processed. Another benefit of jaw crushers is that they're able to achieve high levels of speed and precision, which is especially important in processes such as recycling where smaller pieces need to be sorted quickly.
Sources
- https://sciencebriefss.com/geology/so-how-exactly-does-a-rock-crusher-work/
- https://bentobako.fr/2022/05/10-26760.html
- https://www.youtube.com/watch
- https://www.crusherandparts.com/what-is-a-jaw-crusher/
- https://www.youtube.com/watch
- https://www.beyonddiscovery.org/size-reduction/jaw-crushers.html
- https://savree.com/en/encyclopedia/jaw-crusher
- https://www.crusher-mills.com/en/crushing/jaw-crusher-output-size.html
- https://www.cuttingtechnologies.com/jaw-crusher/
- https://www.quora.com/Whats-the-output-of-jaw-crusher
- https://www.crusher-mills.com/en/crushing/crusher-jaws-crusher-plant-working-mechanism.html
- https://www.lydhcrusher.com/news/What-is-the-Discharge-Size-of-Jaw-Crusher.html
- https://www.crusher-mills.com/en/crushing/advantages-and-disadvantages-of-a-jaw-crusher.html
- https://www.crusher-mills.com/en/crushing/jaw-crusher-advantage-and-disadvantage.html
- http://www.ztcrusher.com/what-are-the-advantages-of-jaw-crusher/
Featured Images: pexels.com