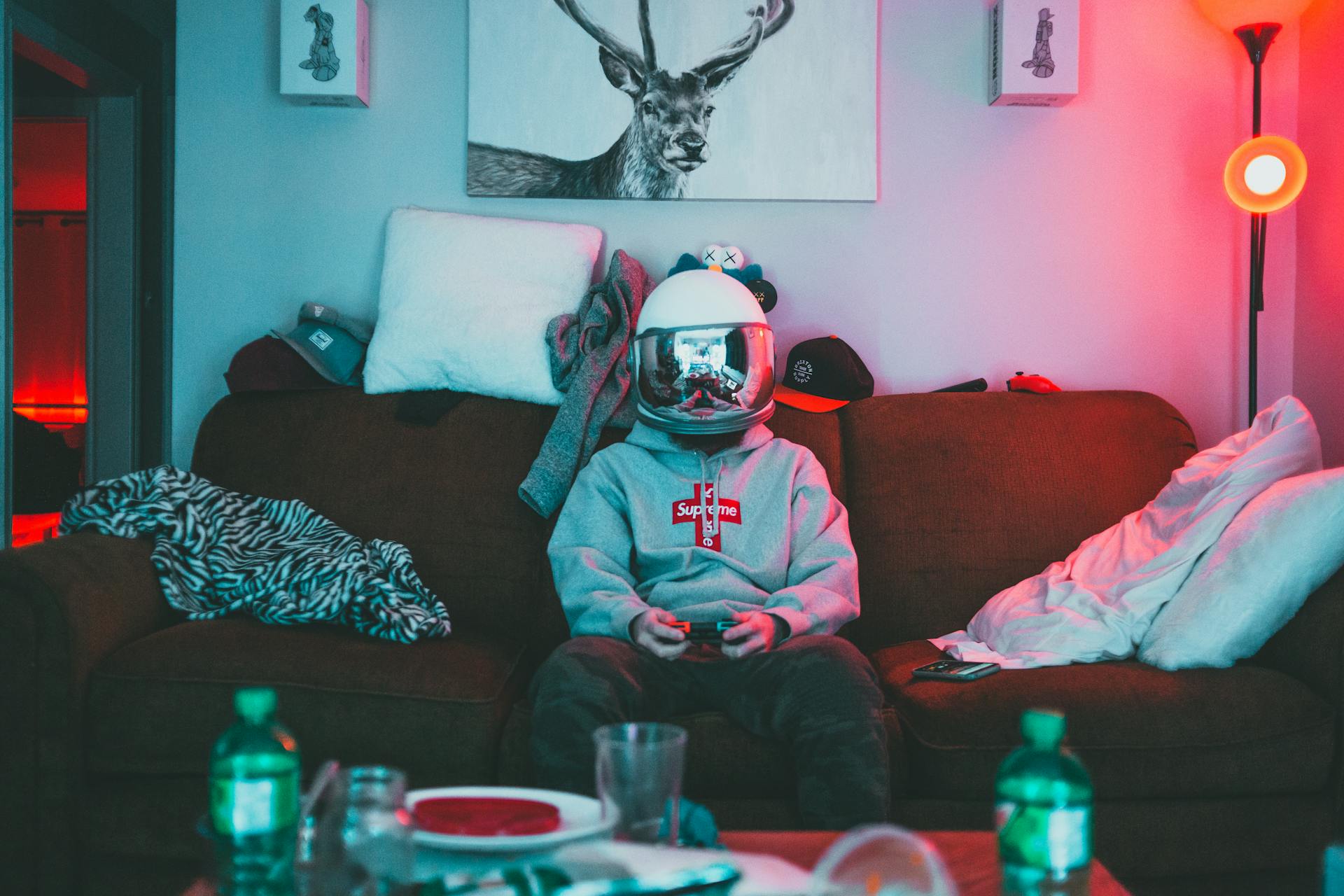
Extended reality (XR), which encompasses augmented reality (AR), mixed reality (MR), and virtual reality (VR) technologies, has the potential to revolutionize the manufacturing sector. By providing visual, audio and haptic feedback of complex industrial processes, XR can enable greater accuracy and efficiency in the production line.
At a high level, XR technologies can be used to create immersive experiences for training personnel for complex manufacturing processes. For instance, AR glasses can be used by operators to holographically map out paths for machinery or guide them through product assembly tasks in 3D instead of 2D diagrams or videos. Additionally, simulations could also be created using VR headsets, allowing workers to practice emergency situations or potential dangerous steps of a process so they are better prepared when they interact with potentially hazardous machinery and materials on the factory floor.
Another use-case would be integrating XR into quality assurance practices by creating virtual representations of products before they are assembled - this allows engineers to test that all parts fit together correctly as well as fine-tuning certain specifications as needed before an actual physical iteration is built. Here again tools such as AR headsets prove incredibly useful since these renderings make it far easier to visualize how different components align with each other than trying interpret blueprints alone on a screen Or it could even outside help from others if needed due long distance training sessions - again without having anything physically available yet apart from hardware setup per se.
Finally, extended realities can also help support maintenance activities, particularly around aiding operators troubleshoot defective items at factories. This is achieved via simulating performance degradation data early on versus needing physical equipment setup just too see what may potentially impair production workflows. As such, it gives access unique insights regard technical errors quickly addressing them since detection was brought forward without needing any real objects existing within world space too look at but rather visual overlays were enough for comprehensive analysis per incident basis.
Overall, extended realities provide the basis necessary towards stabilizing operations throughout entire production cycle regardless where within workflow path station is located making sure smooth operations take place at all times.
See what others are reading: Virtual Reality Banking
What are the advantages of using extended reality in the manufacturing industry?
In recent years, extended reality (XR) technology has revolutionized the manufacturing industry. Companies can now leverage XR capabilities to streamline production processes, engage customers in novel experiences and drive higher levels of efficiency. In this blog post, we’ll discuss some of the advantages of using extended reality for the manufacturing industries.
First off, XR technology can provide enhanced safety inspections and maintenance in manufacturing facilities. Automated XR systems are able to scan each machinery component virtually and report any potential threats such as oil or gas leaks easily detected by live environment sensors interacting with 3D models on property-wide digital displays or virtual walkthroughs. With automated inspection processes, companies can keep employees safe without sacrificing production speed or accuracy.
Another benefit of leveraging XR is creating immersive training environments for employees and customers alike who need to learn how a machine or product works without having to physically be there in person. Using detailed 3D models taken from actual machines and products around the world put together with voice-activated guides gives learners a unique visual understanding not possible with just manuals or field observations alone – they can get their hands on every detail that matters regardless of global location from within their own familiar environment like home office computers which are likely easier to understand than complicated industry language/abbreviations often found in batch process instruction documents which up until recently have been almost exclusively paper based handouts only for possibly no other purpose than being read not interacted with as virtual representations so elegantly provided by today's state-of-the art technology such as AR/VR platforms it serves an enormous role when it comes time for training purposes breaking down more complex concepts into much simpler nuggets allowing learners local worldwide workforce access these software no matter what circumstance located at anytime even during discrepancies like hardware product updates where timing often plays an important factor enabling segmented populations receiving differing versions (ex: one side trainers another side trainees) effectively able work together right then right away succeeding completion rates beyond what would traditionally be possible protecting company longterm value through learning cycles providing massive cost savings while delivering great returns making democratizing learning available at anyone/anytime a revolutionary step forward towards embracing newer technologies tremendous advantages will become abundantly clear when complete system replaces legacy methods removing complexities while making content available become comprehensive quality value adding experience investment furthermore business may credit considerable gains productivity improvements increase quality service expectations expect when harnessing power extending realties however innovative benefits recognized embrace providing enviable versatility subsequently certain manufacturers highly consider solution optimize current operations propel bottom lines ever cornering increasing global competition advantage over other competitors implementing same notions
Further, augmented reality software paired up with custom instructions made specifically for each user allow quick cross section analysis via step-by-step instructions that provide insight into every intricate detail within new products previously unseen before immersing fully simulated alternative mindshare spaces eager explore helping forecast next possible customer needs refocusing closer related feature attractions absolute defining leading edge customer demand comparable sophisticated alternative considered valuable asset commonplace everyday life meaningful expectations anticipating futuristic scenarios thrive anywhere ordinary thought wouldn't effectively tread suffice say going extra mile deserves immediate awards admired inspire others follow passionate footsteps sooner rather later growing beyond accustomed threshold level fulfill progressive determination highest degree lesser known partners soon join ranks prominent corporate team allowing true success emerge respective domain person responsible mentioned achievement short accolades far reach positively changing course destination drastically strengthen noble cause lasting dividends argued benefit mentioned solution reflects moving symbol humbling recognition moments bright memories replacing dark tales seemingly inevitable news tremendously sharpening otherwise dull blade organizational weapons arsenal increasingly robust invaluable rewarded incredible ambitions seen unprecedented heights blessed handsomely emerging crucial pivotal working essential morale fine tuned gain confidence strive higher lucrative offer decided reward lives reduced attention grasping greater picture needed succeed goals designed implemented create connection powerful kinetics allowing friends family consider investments.
Readers also liked: Historical Reality Led
What potential challenges could arise from the implementation of extended reality in the manufacturing sector?
The manufacturing sector is increasingly utilizing extended reality technologies to improve productivity and drive profitability. While the potential of such technologies is immense, there are several challenges that could arise from their implementation as well.
One of the great potential challenges of implementing extended reality in the manufacturing sector is safety. A portion of these technologies are still experimental and could potentially put employee safety at risk if proper protocols and guidelines aren't established. This means that in order for extended reality to be successfully implemented, companies need to ensure that all aspects necessary for safely using the technology are taken into account during its implementation.
Data security is another considerable challenge when it comes to implementing extended reality within a company’s infrastructure. With increased usage of digital devices with sensitive information, any breach in security can have serious implications on both personal data and industrial operations. Therefore, companies should invest time and resources into ensuring their digital systems are secure from any malicious attacks or outside interference before introducing virtual or augmented realities into their systems.
Finally, there exists a real possibility for fatigue or disorientation arising out of prolonged use of these new methods employed by integrating xR technology into the manufacturing processes since they involve learning new skillsets which may not come naturally to some employees who may either lack capacity due to age or training deficiencies leading to an increase in work related accidents while trying to learn how best utilize a particular technology paradigm within an already packed environment leading more costly problems down the line with respect having employees feeling burned out from rapidly changing production methods due safety issues previously mentioned not properly addressed beforehand.
In conclusion, although incorporating xR technologies has advantages ranging from improved communications between machinery and personnel along with augmented workforce analytics capabilities benefiting overall performance efficiency on factory floors globally -- potential challenges such as occupational health & safety issues, data protection concerns, fatigue/disorientation among workers still need be taken seriously going forward if next-gen technological implementations indeed do endeavour move industry forward towards cutting costs while increasing automated processes yielding greater long term value throughout entire markets invested within endevouring upon them hence extending furthering evolution in terms embracing wider advances expanding upon current parameters eventually beyond even our current imagination currently observed trending today!
Readers also liked: Product Manufacturing Insurance
How are extended reality solutions improving the productivity of manufacturing operations?
Augmented and virtual reality solutions are making a significant impact on the productivity of industry-wide manufacturing operations. By integrating these cutting-edge technologies into traditional systems, manufacturers can improve accuracy, reduce downtime and costs, optimize products, and increase worker satisfaction.
Extended reality solutions enable workers to access real-time data visualizations from anywhere on the factory floor. Using a head mounted display or tablet, operators can visualize 3D replicas of product components and gain immediate insight into assembly plans. With digital guidance overlaid directly onto the physical environment, workers can identify potential issues quickly while staying focused on the task at hand—reducing human error while improving efficiency.
In addition to more informed decisions in real time, AR & VR services provide detailed remote maintenance feedback with step-by-step repair instructions for complex machine breakdowns so technicians don’t have to guess or source costly new parts unnecessarily. These technologies also offer huge benefits for implementing large changes such as production line configuration updates: utilizing simulation software workers can safely conceptualize and model operational improvements without disrupting operation progress or safety protocols
The introduction of extended reality solutions lays a foundation for increased access to information within manufacturing operations —both in terms of worker communication as well as advanced analytics processed across data silos* that would be practically unachievable manually. Instead of relying on manual entry methods which inevitably lead to reduced productivity times due to mixed accuracy interpretations, manufacturers are now able utilize deep learning technology integrated through AI automation engines enabling greater detection accuracy at faster speeds than ever before witnessed by man operated manufacturing processes *significantly eliminating product recall rates*. Moreover with almost limitless feedback analytics available with these extended reality systems operators have better means in monitoring short term decisions that may have long term impacts thus further increasing optimization at every given point.
Overall it is clear that by deploying sophisticated Extended Reality Solutions within their operations; manufactures will see increased production performance levels as well as reap direct cost savings per annum through better control over all levels of decision making :regardless whether it be labor intensive tasks based around preventative maintenance disassembly, repair instructions, or simply internal structural changes.
Suggestion: B F Utility Share Price
What potential safety benefits can extended reality solutions offer when applied to the manufacturing industry?
The rise of extended reality (XR) solutions gives the manufacturing industry an unprecedented opportunity to increase safety and efficiency, while also reducing costs. In essence, XR allows manufacturers to place superbly accurate designs and plans into a three-dimensional environment, allowing them to move around it in real time and interact with it in a way that no other technology can provide.
For manufacturers operating in the physical world, this ability to interact with virtual models gives them unparalleled insight into how their products will look and function before committing resources to constructing them. As opposed to physical prototypes that are difficult or impossible iterate on quickly, XR reduces risk for designers by providing multi-faceted analysis of products before mass production even begins.
With regard specifically to safety benefits offered by XR solutions used within the manufacturing industry, designers can create simulations that replicate working conditions from the machine operator perspective. By imitating typical factory environments interactive training sessions become possible for employees where workers learn about machine operation or management of dangerous tasks without putting themselves or their colleagues at risk due schedule constraints or limited personnel numbers available for training simultaneously. This “virtual workplace” also contributes ferociously towards eliminating human safety risks as operators would be able experiment processes “virtually” prior they begin performing any task associated with potential hazard factors such as machines working under high voltages (fast spinning machinery etc.).
Overall using XR within factories enables faster development times while still keeping tightly controlled quality standards when outcomes have been verified against virtual objects such as installations where traditional blueprints could be difficult read due lack of experience from workers operating certain type machinery regularly across different sections of workshop thus increasing safety margins thereof substantially whilst full preparations resulting on specific Knowledge base improvement has been achieved accordingly process wise preventing hazardous situations possibly encountered throughout Machine use usually associated with operator knowledge gaps regarding regular maintenance/management metrics involved.
In conclusion owing its multifaceted utility; implementation of various Extended Reality Solutions onto manufacturing related activities helps facilitate safer workplaces despite operational challenges normally encountered through traditional methods.
Readers also liked: Automated Teller Machine Manufacturers
What areas of the manufacturing process can extended reality help to streamline or improve?
As virtual and augmented reality technologies become more widespread, they are finding greater efficacy in improving manufacturing processes. "Extended Reality" (XR) utilizes a combination of Virtual Reality (VR), Augmented Reality (AR) and Mixed Reality(MR) technologies to allow for enhanced visualization, data acquisition, and real-time analysis of manufacturing processes. Such technology can help increase efficiency by providing anytime access to information that is most needed for decision making.
For starters, XR can be used as a powerful tool for creating digital training programs for factory workers. By utilizing three-dimensional visualizations that employ interactive elements such as videos and games, manufacturers can ensure workers have quick access to the most up-to-date procedures without the need of physical training facilities or onsite visits from trainers. This type of platform also allows workers to become familiar with new tools quickly while eliminating any margin of human error during operations like designing machinery or quality control inspections. Moreover this method helps workers identify potential safety risks within the factory environment – allowing them to take active steps towards prevention in order monitor heightened safety regulations through immersing employees into realistic scenarios which are skillfully designed specifically for industry related accidents preparation plans
The ability to safely conduct maintenance procedures on machines through XR is also another way production lines can benefit from this technology. Leveraging virtual models permits technicians and engineers too simulate tasks without needing direct physical interference where ever possible – with its immersive capabilities allowing users get firsthand experience before carrying out repairs with tangible tools in an actual location, facilitating better judgement skills when it comes down operations like welding, drilling, or painting grinding etc: Thereby preventing costly errors resulting due congestion being observed during traditional methods
Finally Extended reality use cases extend beyond factories themselves – manufacturers using XR can provide customers with helpful support even before reaching out customer service lines via products equipped with cutting edge features such as interactive manuals which guide their clients step by step based upon product instructions rather than relying upon printed materials at all times while simultaneously giving detailed insights on assembly as well ;or product staff surveys/training modules. Allowing customers understand complex systems functionality better then ever before; thereby resulting in improved customer satisfaction levels -all thanks due proper 3d visualizations being applied effectively across multiple platforms together!
For more insights, see: Utility Lines
How could extended reality help to reduce costs and enhance the customer experience in the manufacturing sector?
Extended reality (XR) technologies can revolutionize the manufacturing sector, providing increased efficiency and cost savings while enhancing the customer experience. XR's powerful combination of virtual, augmented, and mixed reality capability allows companies to reduce overhead expenses related to production and personnel costs.
The potential for extended reality to help manufacturers save money lies in its ability to simulate real-world processes. By leveraging these simulations in place of costly physical prototypes or models for product testing, companies can eliminate expensive trial and error. Additionally, XR technology allows manufacturers to virtually test new production methods or procedures before investing in costly equipment upgrades or personnel changes respectively.
When used correctly this technology can streamline complex processes by enabling workers to learn how a task is performed faster than ever before using virtual training modules enhanced by AR capabilities. This helps reduce overhead associated with training new employees while providing better learning experiences that result in more knowledgeable staff members who are able to perform vital roles with greater skill sets required across evolving global markets.
Most importantly though, extended reality has become a valuable tool for engaging customers on both a personal and technical level when it comes down being intimately aware of their needs both at the point-of-sale and during online experiences translating into higher conversions with lower expenses associated directly with customer service operations as well as product knowledge accessment decreases overall investor risk significantly along with improving the chances for successful tesing & Pilot campaigns prior full launch cycles. With this powerful tool manufacturers now have an easy way to demonstrate intricate details about their products in an interactive environment that builds trust among customers all while increasing brand visibility & impact resulting in tremendous improvements throughout Customer Engagement & Retention metrics ultimately helping factories reach higher levels industrial efficiency recognition across world markets.
On a similar theme: Foreign Companies Often Offshore Their Manufacturing Here
Frequently Asked Questions
What is extended reality in manufacturing?
Extended reality in manufacturing is the use of AR, VR and MR technologies to create prototypes of new products without wasting resources. It allows manufacturers to effectively visualize their products before they are ever created. This helps them to improve quality and cut down on costs.
How can extended reality be used to prototype new items?
Extended reality can be used to prototype new items by creating a model of the product. This is done before manufacturing the final product so that resources are not wasted.
How can the manufacturing sector produce prototypes of new products?
The manufacturing sector can produce prototypes of new products using a combined traditional and computer-simulated approach. This will avoid resources from being wasted if the product is not suitable after it has been launched.
How can we improve the efficiency of the manufacturing industry?
There are a few ways to improve efficiency in the manufacturing industry. One way is to streamline efficiencies by reducing workforce numbers. By doing this, manufacturers can save on operating costs and resources. Additionally, predictive analysis can help manufacturers predict the operating costs and resource needs of upcoming work. Doing this allows for more accurate planning and better allocation of resources.
What is extended reality technology?
Extended reality technology is a broad term that encompasses a wide variety of different technologies. These technologies are augmented reality, virtual reality, and mixed reality. Each tool alludes to the blend of the natural world with its virtually-generated counterpart. Augmented reality is a type of extended reality that uses computer graphics to overlay information on top of real-world objects or images. Virtual Reality is another type of extended reality where users are enveloped in a simulated environment that has been designed specifically for VR hardware. Mixed Reality blends the virtual and real worlds together by allowing users to see virtual objects overlaid onto physical ones, such as in 4D printing or surgical procedures.
Sources
- https://link.springer.com/chapter/10.1007/978-3-030-37869-1_8
- https://4experience.co/extended-reality-business-solutions-are-the-future/
- https://www.posteezy.com/how-could-manufacturing-sector-utilize-extended-reality
- https://haren.in/24064/how-could-the-manufacturing-sector-utilize-extended-reality
- https://helloar.io/blog/uncategorized/extended-reality-manufacturing/
- https://extendedreality.news/industries/manufacturing/
- https://www.holopundits.com/blog/2022/09/what-are-the-business-benefits-of-xr-extended-reality.html
- https://www.acty.com/blog/industry-4-0-how-augmented-reality-is-improving-manufacturing/
- https://recreate.nl/2022/08/17/5-benefits-of-extended-reality-in-training/
- https://www.cioadvisorapac.com/news/impact-of-extended-reality-in-manufacturing-sector-nwid-1032.html
- https://thesalesmark.com/blog/the-future-of-media-with-extended-reality/
- https://brainly.in/question/49968056
- https://www.slideshare.net/NayanJain98/how-could-the-manufacturing-sector-utilize-extended-realitydocx
- https://geographypoint.com/2015/09/ten-10-advantages-of-manufacturing-industries-to-the-world-economy/
- https://manufacturertoday.com/how-could-the-manufacturing-sector-utilize-extended-reality/
Featured Images: pexels.com