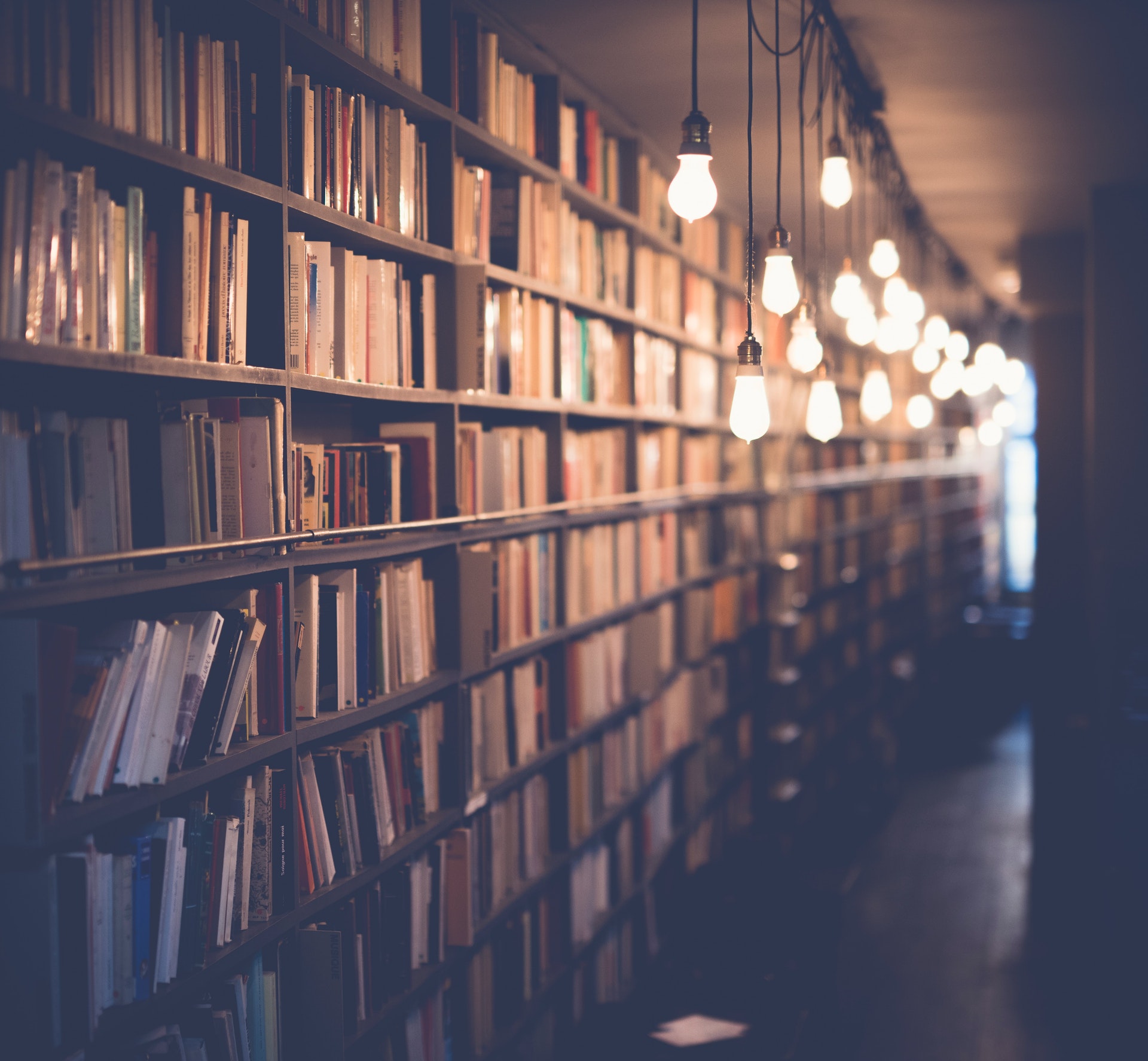
It is no secret that in transit inventory is a huge drain on company resources. It ties up valuable working capital, takes up valuable space, and causes a drag on company profits. So what can be done to encourage a reduction in in transit inventory?
One way to encourage a reduction in in transit inventory is to offer incentives to customers for ordering early. This could be in the form of a discount on the purchase price, or a free shipping offer. Either way, the goal is to encourage customers to place their orders earlier so that the goods can be shipped and received faster, thereby reducing the amount of time that the inventory is in transit.
Another way to reduce in transit inventory is to streamline the manufacturing and distribution process. This could involve investing in new technology or equipment that speeds up the production process, or revamping the distribution process to make it more efficient. By making the manufacturing and distribution process more efficient, companies can reduce the amount of time that goods spend in transit, thereby reducing in transit inventory levels.
Finally, companies can work with their suppliers to reduce in transit inventory levels. This could involve setting up a just-in-time delivery system, where goods are only ordered and shipped as they are needed. This way, there is no need to stock up on inventory, as it can be shipped directly to the customer as soon as it is needed. This can be a very effective way to reduce in transit inventory levels, as it eliminates the need to store excess inventory.
All of these strategies can be effective in reducing in transit inventory levels. By offering incentives to customers for ordering early, streamlining the manufacturing and distribution process, and working with suppliers to set up a just-in-time delivery system, companies can encourage a reduction in in transit inventory, which will free up valuable resources and improve company profits.
Check this out: Bond Reduction
How can lead times be shortened to reduce in transit inventory?
In many industries, raw materials must be shipped to manufacturing plants, where they undergo production processes before being shipped to retailers or other customers. The time required to transport raw materials to manufacturing plants and finished products to customers is known as the lead time. Reducing the lead time can help to reduce in-transit inventory and associated costs.
There are a number of ways to reduce lead times. One way is to shortened the distances between suppliers and manufacturing plants. This can be done by locating suppliers closer to manufacturing plants or by using faster transportation methods. Another way to reduce lead times is to improve coordination between suppliers and manufacturing plants. This can be done by implementing just-in-time production or by using Vendor Managed Inventory systems.
Just-in-time production is a manufacturing strategy that coordinates the arrival of raw materials with the production schedule. This minimizes the time raw materials spend in transit and in storage. Vendor Managed Inventory systems give suppliers real-time information about manufacturing schedules and inventory levels. This allows suppliers to ship raw material only when it is needed, further reducing in-transit inventory.
Lead times can also be shortened by reducing the time required for production processes. This can be done by streamlining manufacturing processes, investing in new technology, or training employees.
Reducing lead times can help to reduce in-transit inventory and costs associated with storing and shipping inventory. There are a number of ways to reduce lead times, including shortened distances between suppliers and manufacturing plants, improved coordination between suppliers and manufacturing plants, and reduced time required for production processes.
You might like: Why Inventory Should Be Digital?
What is the effect of in transit inventory on working capital?
Inventory that is in transit is considered to be part of a company's working capital. This is because the inventory has not yet been sold, and therefore, is still considered to be an asset of the company. The effect of in transit inventory on working capital is that it can tie up a significant amount of the company's money. This is because the inventory must be paid for, even though it has not yet been sold. In addition, in transit inventory can also increase the risk of a company's working capital, because if the inventory is damaged or stolen, the company will not be able to recoup the cost.
Suggestion: Inventory Provision Accounting
How can in transit inventory be managed to minimize its impact on working capital?
In most cases, in transit inventory is physical inventory that is being shipped from one location to another. This type of inventory is considered to be part of the company's working capital because it is inventory that is "in the process" of being sold.
There are a few different ways that companies can manage in transit inventory to minimize its impact on working capital. One way is to track the inventory closely and make sure that it is only shipped when it is absolutely necessary. This can be done by using a software system that tracks inventory levels and shipment dates.
Another way to minimize the impact of in transit inventory on working capital is to ship the inventory on consignment. This means that the company does not pay for the inventory until it is sold to the customer. This can be a good option for companies that have a lot of in transit inventory.
yet another way to reduce the impact of in transit inventory on working capital is to use a just in time (JIT) inventory system. With this system, inventory is only shipped when it is needed and not before. This can be a very effective way to reducing the amount of in transit inventory.
Ultimately, the best way to reduce the impact of in transit inventory on working capital is to have a good system in place that minimizes the amount of inventory that is shipped. By tracking inventory levels and shipping dates, shipping on consignment, and using a JIT system, companies can greatly reduce the amount of in transit inventory and the impact it has on working capital.
Curious to learn more? Check out: How Good It Can Be?
What are the risks associated with reducing in transit inventory?
In order to maintain efficient inventory levels, many companies have adopted the strategy of reducing in transit inventory. This involves reducing the level of inventory that is being held at any given time in order to reduce the associated costs. While this can be an effective strategy for reducing inventory costs, it also comes with a number of risks that need to be considered.
One of the biggest risks associated with reducing in transit inventory is the potential for stock outs. If inventory levels are not carefully monitored, it is possible that demand could exceed supply, resulting in a stock out. This could have a serious impact on the company, as it would be unable to meet customer demand. In addition, it could lead to lost sales and damage the company's reputation.
Another risk associated with reducing in transit inventory is the potential for disruptions in the supply chain. If inventory levels are too low, it could lead to disruptions in the supply chain, as suppliers may not be able to meet demand. This could have a knock-on effect on the company, as it may be unable to meet customer demand and could lose sales as a result.
Finally, reducing in transit inventory can also lead to a number of logistical challenges. For example, if inventory levels are too low, it may be difficult to coordinate shipments and ensure that products are delivered on time. This could lead to further disruptions in the supply chain and could have a negative impact on the company's profitability.
Reducing in transit inventory can be an effective way to reduce costs and improve efficiency. However, it is important to consider the risks associated with this strategy before implementing it. By understanding the risks and taking steps to mitigate them, companies can minimize the potential impact on their business.
What are the risks associated with holding excessive in transit inventory?
When a company holds too much inventory, it ties up cash that could be used for other purposes, such as investing in new products or expanding the business. Excessive inventory also exposes the company to the risk of obsolescence if the products it is holding become outdated before they can be sold. In addition, holding large amounts of inventory can create safety and security risks, as well as increase the likelihood of theft and damage.
The risks associated with holding excessive in transit inventory are mainly financial. Companies that carry large amounts of inventory can find themselves in a difficult financial position if they are unable to sell the inventory in a timely manner. When inventory remains unsold for extended periods of time, it can become outdated and lost its value. In some cases, obsolescence can happen quickly, such as with technology products that are quickly replaced by newer models. This can leave a company stuck with a large amount of inventory that is worth less than the original purchase price.
Another financial risk associated with holding excessive in transit inventory is the opportunity cost of tying up cash in inventory. Instead of using the cash to invest in new products or expand the business, the company is using the cash to pay for the inventory that is sitting in warehouses or in transit. This can limit the company's growth potential and make it difficult to compete against other firms that are investing their resources more wisely.
The safety and security of the inventory is another risk to consider. If a company is holding a large amount of inventory in a single location, there is a greater risk of theft or damage. For example, if there is a fire at the warehouse, the entire inventory could be destroyed. Similarly, if the inventory is stored in an insecure location, it could be subject to theft.
Finally, it is important to consider the environmental impact of holding excessive in transit inventory. If the inventory is being shipped by truck, there will be an increased amount of emissions from the trucks. In addition, the warehouse or storage facilities that are holding the inventory may not be designed for long-term storage, which could lead to environmental contamination.
In conclusion, there are a number of risks associated with holding excessive in transit inventory. These risks can be financial, safety and security, or environmental. Companies should carefully consider these risks before deciding to hold large amounts of inventory.
Intriguing read: Security Guards
How can in transit inventory be monitored to ensure that it is minimized?
Inventory that is in transit is often one of the most difficult to monitor and control. This is because it is not in the possession of the company and is oftentimes out of sight. However, there are a few ways that in transit inventory can be monitored to ensure that it is minimized.
One way to monitor in transit inventory is to track the shipments. This can be done using a shipment tracking system. This system can be used to track the location of the shipment and the status of the shipment. This information can be used to determine if the shipment is on schedule and if it is likely to arrive on time.
Another way to monitor in transit inventory is to contact the supplier on a regular basis. This can be done to check on the status of the shipment and to inquire about any delays. This communication can help to avoid any surprises when the shipment arrives.
A third way to monitor in transit inventory is to create a buffer. This buffer can be in the form of extra inventory that is available at the destination. This extra inventory can be used in the event that the shipment is delayed or if there are problems with the shipment. This buffer can help to minimize the impact of in transit inventory on the company.
In transit inventory can be a difficult thing to monitor and control. However, by tracking the shipments, contacting the supplier, and creating a buffer, companies can help to minimize the impact of in transit inventory.
What are the consequences of reducing in transit inventory too aggressively?
In the business world, the consequences of reducing in transit inventory too aggressively can be significant. By definition, "in transit inventory" refers to the inventory that is being shipped from one location to another, but has not yet arrived at its destination. In other words, it is the inventory that is in the process of being delivered. Reducing this type of inventory too aggressively can have a number of consequences for a business.
First, it can lead to production delays. If a business does not have enough inventory on hand to meet customer demand, then it will have to slow down or stop production in order to avoid running out of materials. This can lead to significant delays in fulfilling customer orders, which can damage the business's reputation and lead to lost sales.
Second, reducing in transit inventory too aggressively can lead to stock-outs. If a business doesn't have enough inventory on hand to meet customer demand, then it will eventually run out of stock entirely. This can be a major problem, as it can lead to unhappy customers and lost sales.
Third, reducing in transit inventory too aggressively can increase the risk of damage or theft. If there is less inventory in transit, then there is a greater chance that it will be damaged or stolen before it arrives at its destination. This can lead to additional costs for the business, as well as lost sales.
Fourth, reducing in transit inventory too aggressively can lead to higher shipping costs. If a business has to ship less inventory, then it will generally have to pay higher shipping rates. This can add to the overall costs of the business and make it more difficult to compete on price.
Finally, reducing in transit inventory too aggressively can lead to lower levels of customer service. If a business doesn't have enough inventory on hand to meet customer demand, then it will likely have to cut back on customer service in order to save costs. This can lead to unhappy customers and lost sales.
In summary, the consequences of reducing in transit inventory too aggressively can be significant. This can include production delays, stock-outs, increased shipping costs, and lower levels of customer service. businesses should be sure to carefully consider the potential consequences before reducing their in transit inventory levels too drastically.
For your interest: Who Says You Can T You Do?
How can in transit inventory be used to improve customer service levels?
Inventory that is in transit between suppliers and customers can often be overlooked as a source of potential customer service problems. In fact, in transit inventory can be a significant source of customer service issues if not managed properly. Here are some tips on how to use in transit inventory to improve customer service levels:
1. Keep track of in transit inventory levels and locations. Knowing where your in transit inventory is at all times is critical to being able to provide good customer service. Keep track of in transit inventory levels and locations using a software system or a manual process.
2. Make sure in transit inventory is visible to customer service representatives. Customer service representatives should be able to see in transit inventory levels and locations in the same system they use to track customer orders. This will help them to better understand the status of customer orders and make more informed decisions about how to best serve customers.
3. Use in transit inventory to improve order accuracy. In transit inventory can be used to improve order accuracy by ensuring that customer orders are shipped complete and on time. Use in transit inventory to cross-check customer orders against shipping manifests to make sure all items are accounted for.
4. Use in transit inventory to improve lead times. In transit inventory can also be used to improve lead times by ensuring that customer orders are shipped as soon as possible. Use in transit inventory to create shipping schedules and prioritize customer orders.
5. Communicate with customers about in transit inventory. Customer service representatives should be prepared to answer questions about in transit inventory levels and locations. They should also be aware of any potential delays that could impact customer orders.
6. Use in transit inventory to improve planning. In transit inventory can be used to improve planning by helping to predict future customer demand. Use in transit inventory data to create forecasts and plan for future customer orders.
7. Use in transit inventory to improve customer service levels. In transit inventory can be used to improve customer service levels by ensuring that customer orders are shipped complete and on time. Use in transit inventory to cross-check customer orders against shipping manifests to make sure all items are accounted for. Communicate with customers about in transit inventory levels and locations. Use in transit inventory to create shipping schedules and prioritize customer orders.
Frequently Asked Questions
Can be a strategy to reduce lead time of the operation?
Yes, but it increases the risk of errors.
How does lead time affect inventory?
When a company has a long lead time, it must hold more inventory in order to meet the demands of customers. This can make it difficult to predict future demand, and can affect profitability because the company needs to rely on forecasts in order to make sales.
Which tool is used to reduce the lead time for a product to reach from one assembly point to another?
There are a number of lean tools that can be used to help in reducing lead time for a product to reach from one assembly point to another. One popular tool used to reduce lead time is Single Minute Exchange of Dies (SMED).
What method can be used to reduce lead time?
There are many ways to reduce lead time, but one of the most effective is to use a domestic supplier. This can automatically reduce your lead time by two weeks or more — that's about how long it takes for parts to ship from many foreign countries. Adding to potential delays is the language barrier that often can complicate communications.
How does lead time affect inventory cost?
If you have a long lead time to procure inventory, your inventory costs will be higher because you'll need to stockpile more items. This increase in storage and maintenance costs can have a ripple effect on your company's bottom line, especially if demand for your products remains high.
Sources
- https://managementmcq.blogspot.com/2019/02/how-can-reduction-of-in-transit.html
- https://www.chegg.com/homework-help/questions-and-answers/reduction-transit-inventory-encouraged--use-trains-trucks-b-ship-large-quantities-c-lower--q46926130
- https://quizlet.com/56816912/supply-chain-exam-2-chapter-16-flash-cards/
- https://quizlet.com/207264682/isds-3115-final-flash-cards/
- https://mcqmate.com/discussion/143992/reduction-of-in-transit-inventory-encouraged-through-use-of
- https://www.coursehero.com/file/p434011/Reduction-of-in-transit-inventory-can-be-encouraged-through-use-of-a-supplier/
- https://cp.dhafi.link/reduction-of-in-transit-inventory-can-be-encouraged-through-the-use-of/
- https://quizplus.com/quiz/99835-quiz-16-jit-and-lean-operations/questions/8008408-reduction-of-in-transit-inventory-can-be-encouraged-through
- https://www.mcl.bz/blog/ways-to-reduce-supply-chain-lead-times
- https://www.seraitrade.com/blog/8-strategies-to-reduce-lead-times-in-your-supply-chain
- https://www.cgnglobal.com/blog/node/710
- https://www.dxpe.com/manufacturing-lead-time-reduction-methods-procurement/
- https://www.jbc-tech.com/blog/posts/how-to-reduce-supply-chain-lead-times/
- https://www.intellichief.com/reduce-your-lead-time/
- https://dearsystems.com/lead-time-reduction/
- https://www.interlakemecalux.com/blog/logistics-lead-time
- https://www.demandcaster.com/blog/5-ways-to-reduce-lead-times-in-your-supply-chain/
- https://www.investopedia.com/ask/answers/100515/does-working-capital-include-inventory.asp
- https://research-information.bris.ac.uk/en/publications/the-effects-of-in-transit-inventory-financing-on-the-capital-cons
- https://ideas.repec.org/a/eee/ejores/v296y2022i1p131-145.html
- https://www.diva-portal.org/smash/get/diva2:346166/FULLTEXT01.pdf
- https://www.shipbob.com/blog/goods-in-transit/
- https://www.alpegagroup.com/en/resources/blog/optimising-your-working-capital-in-the-supply-chain/
- https://arviem.com/working-capital-financing/
- https://www.researchgate.net/publication/306921483_Inventory_management_under_working_capital_constraints
- https://www.superbusinessmanager.com/all-you-need-to-know-about-working-capital/
- https://www2.deloitte.com/content/dam/Deloitte/ca/Documents/finance/ca-en-fa-working-capital-inventory-management.pdf
- https://www.zlc.edu.es/news/static-inventory-an-untapped-source-of-working-capital/
- https://enterslice.com/learning/manage-inventory-reduce-working-capital/
- https://www.logisticsbureau.com/reducing-working-capital-in-supply-chains/
- https://www.tompkinsinc.com/en-us/Insight/Articles/supply-chain-visibilitys-role-in-working-capital-reduction
- https://wakeo.co/blog/how-to-reduce-your-working-capital-requirement-with-real-time-visibility
- https://www.flexport.com/blog/for-explosive-growth-regain-control-of-your-inventory-and-working-capital/
- https://inchainge.com/knowledge/supply-chain/finance/
- https://www.slimstock.com/working-capital-management-success-factors/
- https://rmas.fad.harvard.edu/pages/goods-equipment-transit-risk-discussion
- https://zhenhub.com/blog/in-transit-inventory-management/
- https://www.connerindustries.com/whats-the-real-cost-of-in-transit-damage/
- https://www.fhwa.dot.gov/policy/otps/060320d/060320d.pdf
- https://www.business.org/finance/inventory-management/what-is-in-transit-inventory/
- https://sloanreview.mit.edu/article/reducing-the-risk-of-supply-chain-disruptions/
- https://www.inboundlogistics.com/cms/article/are-your-goods-in-transit-safeguarded/
- https://gimmenotes.co.za/wp-content/uploads/2017/08/TRL3707-study_unit_2_-_inventory_functionality_and_principles.pdf
- https://thesupplychainlab.blog/2007/10/21/10-ways-to-reduce-inventory-cost/
- https://accountlearning.com/risks-cost-holding-inventory-firm/
- https://www.planettogether.com/blog/excess-inventory-advantages-and-disadvantages
- https://www.planettogether.com/blog/holding-excess-inventory-pros-and-cons
- https://www.inturn.com/post/impact-too-much-inventory-on-hand/
- https://teci.com/5-negatives-effects-of-holding-too-much-inventory-on-hand/
- https://www.wisys.com/5-costs-of-having-too-much-inventory/
Featured Images: pexels.com