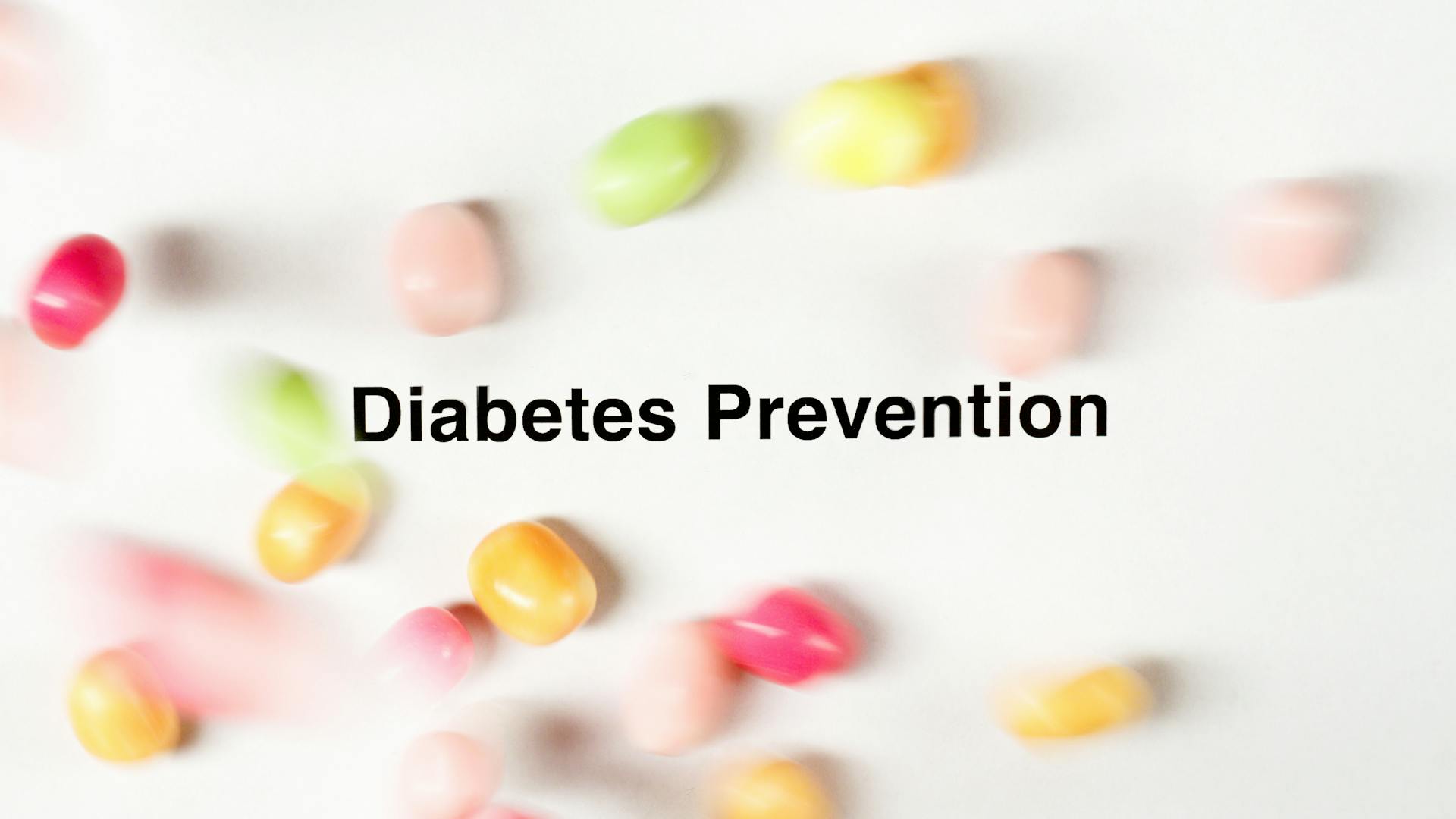
Effective hazard prevention and control involves a combination of approaches that address both the root causes and the symptoms of hazards. This means going beyond just removing or mitigating the hazard itself, but also addressing the underlying conditions that led to its existence.
A key principle of hazard prevention and control is the hierarchy of controls, which prioritizes eliminating or substituting hazardous substances or processes over other control measures. For example, replacing a chemical with a safer alternative can be more effective than simply using personal protective equipment to mitigate its effects.
By understanding and addressing the root causes of hazards, organizations can create a safer working environment that not only protects employees but also reduces the risk of accidents and near misses. This approach can also lead to cost savings and improved productivity.
Prevention and Identification
Hazard prevention and control should contain both proactive measures to eliminate hazards before they cause harm and reactive strategies to respond to incidents when they occur. Proactive measures include identifying potential hazards in the workplace, which is the first step in effective hazard prevention.

The first step in effective hazard prevention is identifying potential hazards in the workplace, which can be classified into several categories. These categories include physical hazards, chemical hazards, biosafety hazards, and ergonomic hazards.
Physical hazards include machinery, noise, and environmental factors such as extreme temperatures. Regular inspections, employee feedback, and a proactive safety culture are essential for recognizing these hazards.
Chemical hazards involve exposure to harmful substances, such as solvents, gases, and dust. A thorough understanding of the chemicals used in the workplace is necessary to identify potential hazards.
Biosafety hazards involve exposure to biological agents, including bacteria and viruses. This type of hazard requires special precautions to prevent exposure.
Ergonomic hazards involve poor workstation design and repetitive motion, which can lead to musculoskeletal disorders. Identifying ergonomic hazards requires a thorough understanding of the work processes and equipment used in the workplace.
To identify potential hazards, thorough inspections, employee feedback, and a proactive safety culture are essential. Regular training and workshops can help staff identify hazards in their specific roles.
Here are some key steps to identify potential hazards:
- Perform a risk assessment
- Conduct periodic inspections of the workplace to identify new or recurring hazards
- Investigate injuries, illnesses, incidents, and near misses to determine underlying hazards and their causes
- Solicit input from workers who have knowledge of the facility, equipment, and work processes
By following these steps, you can effectively identify potential hazards and take proactive measures to eliminate them before they cause harm.
Risk Assessment: Evaluating Impact
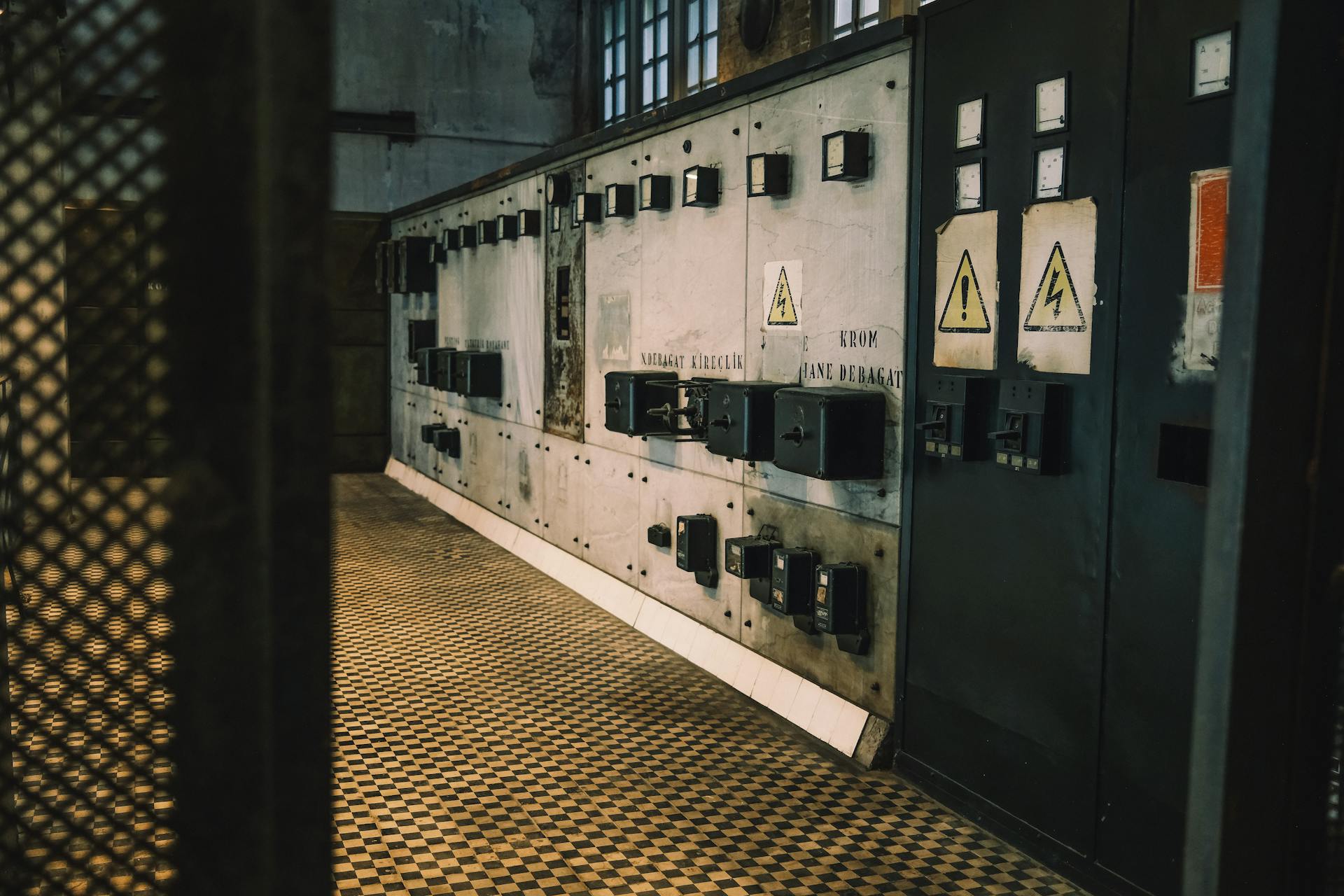
Conducting a risk assessment is a crucial step in identifying and mitigating potential hazards in the workplace. A simple framework for conducting risk assessments includes identifying hazards, evaluating risks, prioritizing risks, and implementing controls.
To identify hazards, you should catalog all potential hazards in the workplace. For example, a manufacturing facility may identify a risk of machinery entrapment.
Evaluating risks involves determining the likelihood and impact of each hazard. This helps you understand the potential consequences of an incident occurring.
Prioritizing risks is essential to ensure that you address the most critical hazards first. You can rank hazards according to their potential impact on health and safety.
Implementing controls is the final step in the risk assessment process. This involves developing strategies to mitigate identified risks. For instance, implementing lockout/tagout procedures can ensure equipment is properly shut down during maintenance.
Here's a summary of the risk assessment process:
By following this framework, you can effectively identify and mitigate potential hazards in the workplace, ensuring a safer working environment for everyone.
Implementing Measures
Implementing measures is a crucial step in preventing and controlling hazards. Engineering controls should be prioritized over administrative controls and personal protective equipment (PPE) whenever possible.
Engineering controls involve redesigning equipment or processes to reduce exposure to hazards. This can be as simple as installing guards on machines to prevent accidents. Administrative controls, on the other hand, include policies and procedures that dictate safe work practices, such as shift rotations to minimize fatigue.
A hierarchy of controls emphasizes that organizations should prioritize engineering controls over administrative controls and PPE. This means that if a chemical spill is a risk, engineering controls like containment systems should be implemented before relying on PPE alone.
Here are the three main types of control measures:
- Engineering Controls: Redesigning equipment or processes to reduce exposure to hazards.
- Administrative Controls: Policies and procedures that dictate safe work practices.
- Personal Protective Equipment (PPE): Equip employees with gear to protect against specific hazards.
Develop a Plan
Developing a plan is crucial to implementing effective control measures. It helps you outline and communicate how your selected controls will be implemented organizationally.
A good plan should list workplace hazards, organizing them based on priority, starting with the most dangerous ones. This ensures that you're addressing the most critical risks first.
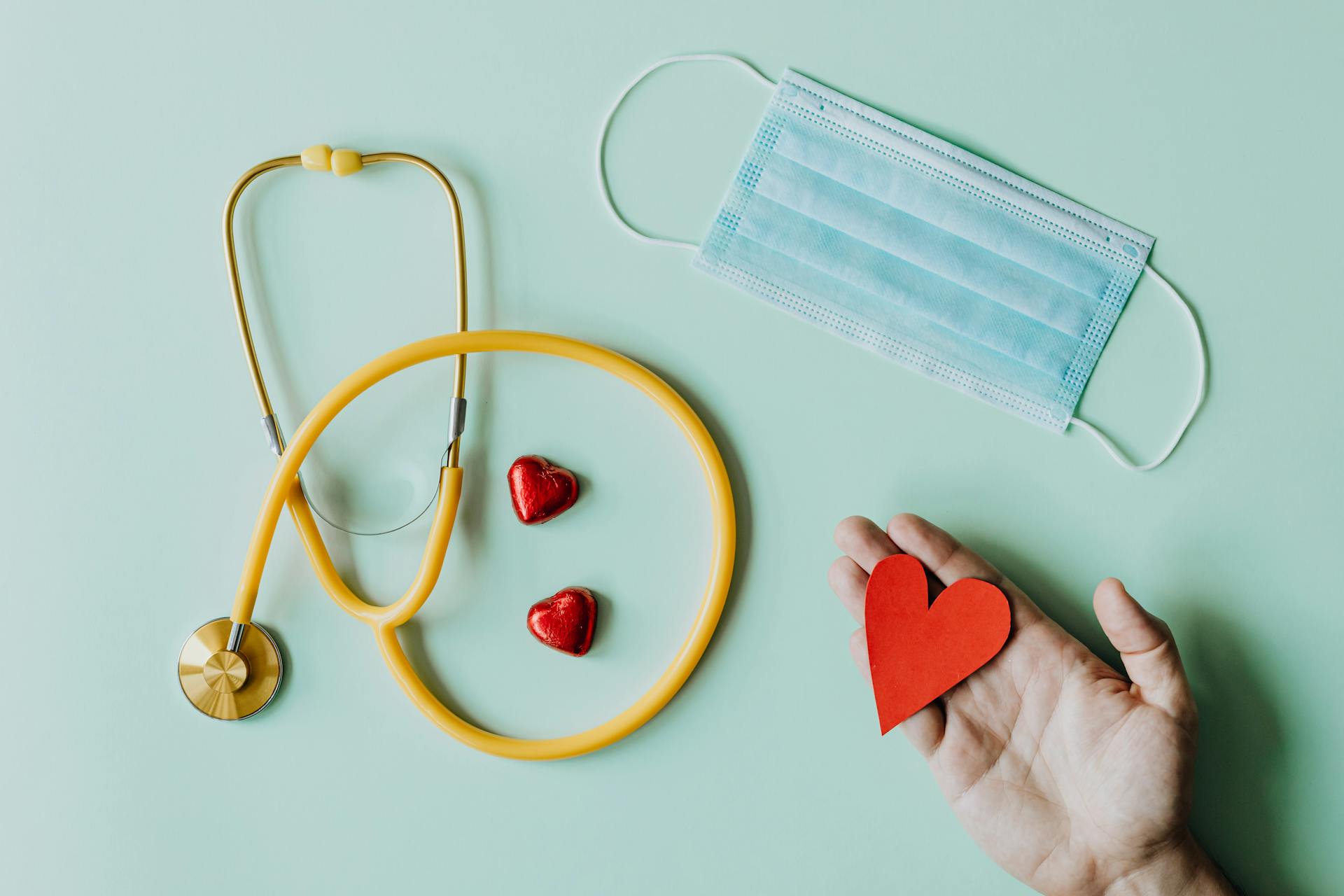
The plan should also take interim controls into account, which may be necessary if you need to put temporary precautions in place while you develop and implement long-term controls.
Establish a target completion date for implanting controls, and set up processes to track your hazard control implementation progress. This will help you stay on schedule and adjust your plan as needed.
Your plan should also include provisions to protect workers during emergencies, such as fires, explosions, chemical releases, and hazardous material spills.
Here's a breakdown of the essential elements of a hazard control plan:
- List workplace hazards, organizing them based on priority.
- Take interim controls into account.
- Establish a target completion date for implanting controls.
- Set up processes to track your hazard control implementation progress.
- Verify the effectiveness of controls once they’re implemented.
By following these steps, you'll be able to develop an effective plan that helps you implement control measures and reduce workplace risks.
Work Practices
Developing and implementing safe work procedures or standard operating procedures is crucial to prevent workplace accidents and injuries. This should include training and education of employees about the operating procedures as well as other necessary workplace training.
Training and education are key to ensuring employees understand the importance of following safe work practices. This includes WHMIS training, which is essential for handling hazardous materials.
Establishing and maintaining good housekeeping programs is vital to prevent accidents and injuries. This includes keeping equipment well maintained, which can help prevent malfunctions and accidents.
Good housekeeping also involves preparing and training for emergency response for incidents such as spills, fire, or employee injury. This can include having a plan in place and making sure employees know what to do in case of an emergency.
Here are some essential elements of safe work practices:
- Developing and implementing safe work procedures or standard operating procedures.
- Training and education of employees about the operating procedures as well as other necessary workplace training.
- Establishing and maintaining good housekeeping programs.
- Keeping equipment well maintained.
- Preparing and training for emergency response for incidents such as spills, fire, or employee injury.
Why Implement in the Workplace?
Implementing measures in the workplace is crucial because employers have a duty of due diligence to prevent injuries or incidents.
This duty requires taking all reasonable precautions to prevent harm, which is a legal obligation.
Employers should seek guidance from occupational health professionals if there's no clear way to control a hazard or if legislation doesn't provide a limit or guideline.
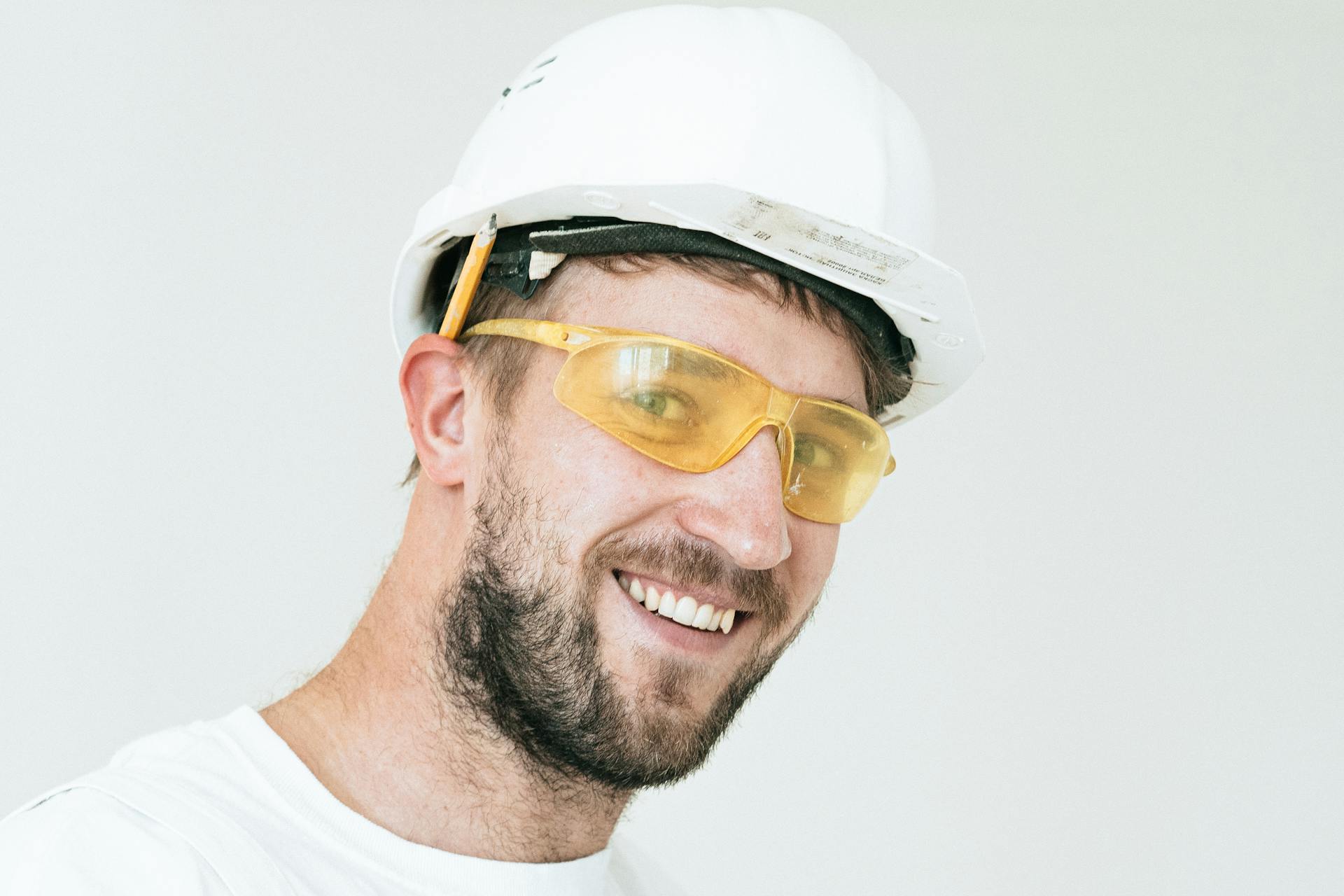
These professionals can help determine the best practice for a specific situation.
A legal limit or guideline should never be viewed as a line between safe and unsafe, but rather as a goal to keep exposures or risks as low as possible.
By doing so, employers can ensure a safer working environment for their employees.
Methods of Hazard Control
Engineering controls are a reliable way to control worker exposures when designed, used, and maintained properly. These controls can be built into the design of a plant, equipment, or process to minimize the hazard. Examples of engineering controls include isolation, enclosures, guarding and shielding, ventilation, mechanical lifting devices, and guardrails.
Administrative controls, on the other hand, involve developing procedures to ensure work is conducted in a way that minimizes the hazard. Examples include developing or changing policies, implementing or improving training and education, and developing or enhancing work practices and procedures. Administrative controls are ranked lower than elimination, substitution, and engineering controls because they don't remove or reduce the hazard itself, but rather limit workers' exposures.
Controls can be used at different points to prevent or mitigate hazards, including at the source, along the path, and at the worker. The best strategy is to control the hazard at its source, which is also known as engineering control at the source.
Curious to learn more? Check out: Forward Controls
ISO Standards
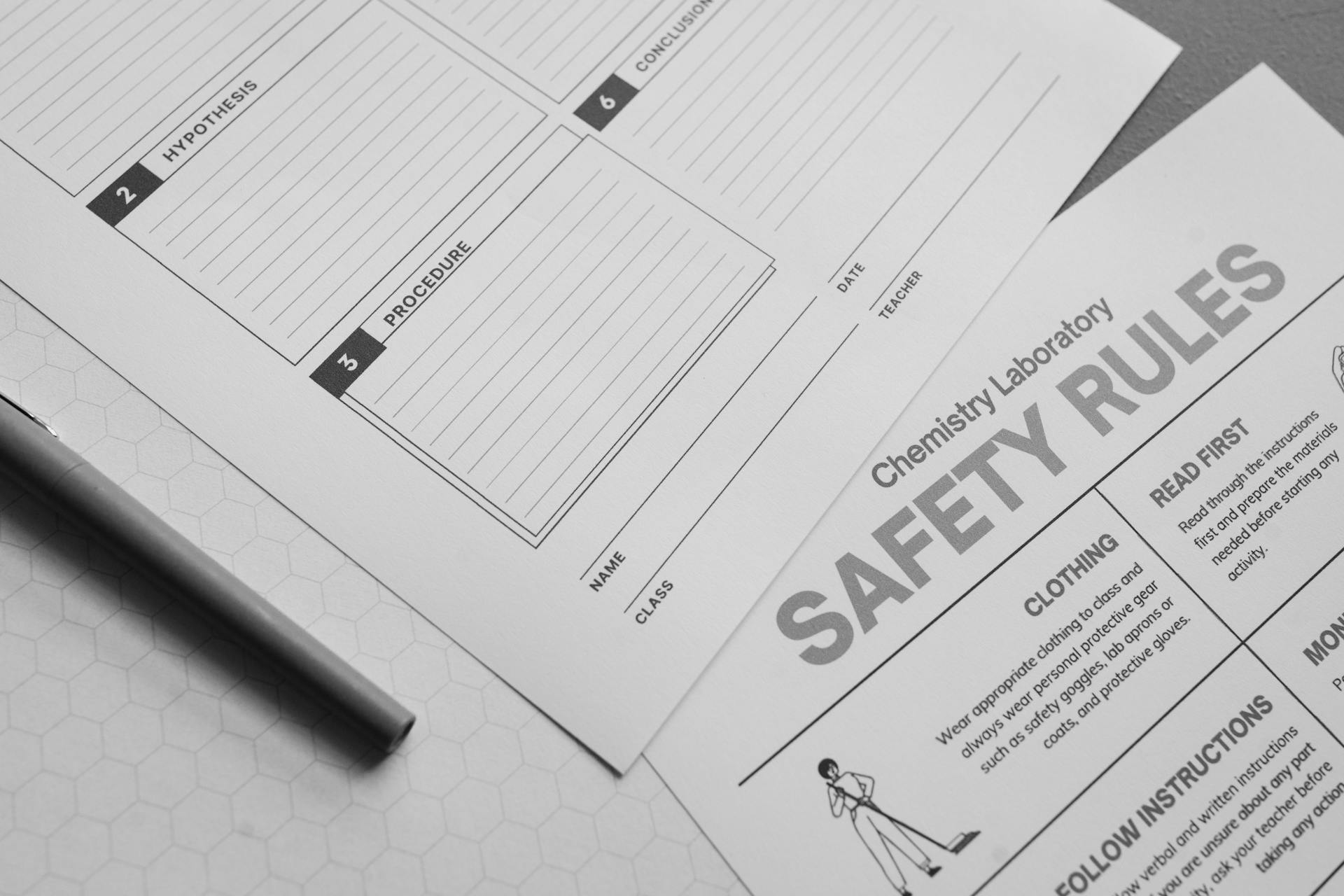
ISO standards, such as ISO 45001, provide frameworks for Occupational Health and Safety management systems. These standards guide organizations in establishing effective hazard prevention and control measures.
Monitoring and reviewing your hazard control program is crucial to ensure that controls are working effectively and exposure to hazards is reduced or eliminated. This includes regular physical inspections, testing, and exposure assessments.
ISO standards, such as ISO 45001, offer a structured approach to risk management. This approach is vital for compliance and fostering a culture of safety in the workplace.
Some key questions to ask when reviewing your hazard control program include: Have the controls solved the problem? Is the risk posed by the original hazard contained? Have any new hazards been created?
ISO standards, such as ISO 45001, provide a framework for answering these questions and identifying areas for improvement. By regularly reviewing and refining your hazard control program, you can ensure that all workplace hazards are identified, assessed, and appropriately controlled.
Here are some tools to help you monitor and review your hazard control program:
- Physical inspection
- Testing
- Exposure assessment
- Observations
- Injury and illness tracking
- Incident investigations reports
- Employee feedback or input
- Occupational health assessment
Engineering Methods Examples
Engineering control methods are a reliable way to control worker exposures. They're built into the design of a plant, equipment, or process to minimize the hazard.
Isolation is one way to separate workers from the hazard. By using distance or barriers, you can effectively control the hazard at its source.
Enclosures, such as enclosed machines or booths, are another example of engineering controls. They place the material or process in a closed system, reducing the risk of exposure.
Guarding and shielding can also be used to control worker exposures. This involves using guards around moving parts of machinery to prevent accidents.
Ventilation is a key engineering control method. It uses local exhaust or general dilution ventilation to remove or reduce airborne products.
Mechanical lifting devices can be used instead of manual lifting to reduce the risk of injury. This is a simple yet effective way to control worker exposures.
Here are some specific examples of engineering controls:
- Isolation – separating workers from the hazard by distance or the use of barriers
- Enclosures – placing the material or process in a closed system (e.g., enclosed machines, booths, etc.)
- Guarding and shielding – using guards around moving parts of machinery
- Ventilation – using local exhaust or general dilution ventilation to remove or reduce airborne products
- Mechanical lifting devices– using mechanical methods to lift or move objects instead of manual lifting
- Guardrails – using guardrails to prevent a fall
Can Multiple Methods Be Used?
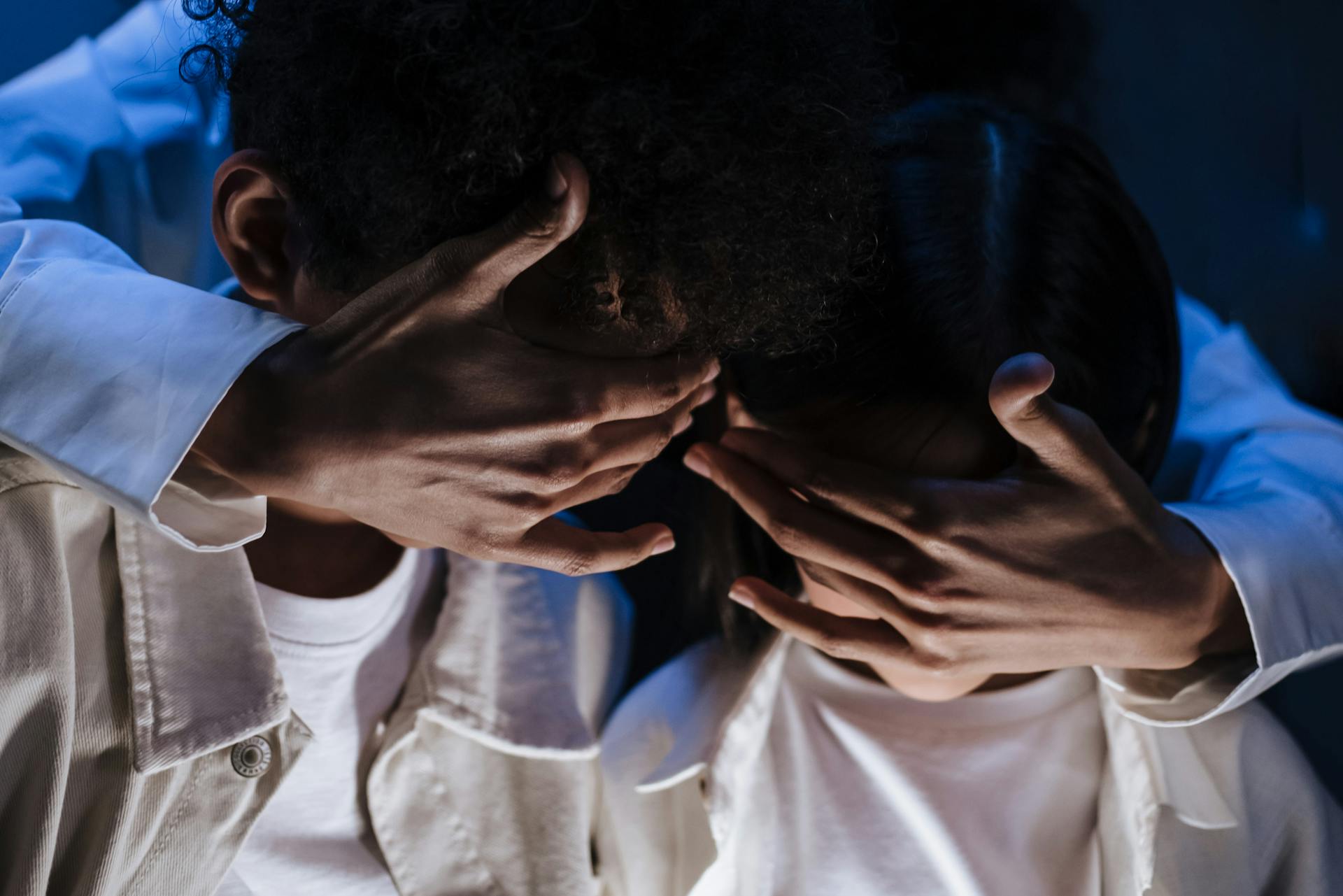
Sometimes a single control method just isn't enough to eliminate a hazard. Fortunately, multiple control methods can be used together to minimize risks.
Using a combination of controls can be especially helpful when a hazard can't be eliminated. For example, if you're working at heights, you might use a scissor lift instead of a ladder, and also wear personal protective equipment (PPE) like a full body harness and lanyard attached to an anchor point.
In other cases, a combination of controls might involve substituting a hazardous activity with a safer one, like using winter tires when driving in extreme weather. This can be done in addition to other controls, such as not driving during extreme weather or taking driver training.
The key is to use a variety of control methods to minimize the risk of injury or illness. By combining different types of controls, you can create a safer work environment.
Discover more: Motorcycle Forward Controls
Here are some examples of how multiple control methods can be used together:
- Substitution (e.g. using a scissor lift) + administrative controls (e.g. training and safe work procedures) + PPE (e.g. full body harness and lanyard)
- Elimination (e.g. not driving during extreme weather) + substitution (e.g. using public transit) + engineering controls (e.g. winter tires) + administrative controls (e.g. driver training)
By using a combination of control methods, you can create a comprehensive safety plan that minimizes risks and protects workers.
Hierarchy of Controls
The hierarchy of controls is a system for minimizing or eliminating employee exposure to particular hazards. It ranks control methodologies from most effective to least effective.
Elimination is one of the most effective ways to manage on-the-job risks, involving altering policies, procedures, materials, parts, products, equipment, or tools to help workers perform their duties safely. By removing a specific hazard from the workplace altogether, you can eliminate the threat to your employees.
Substitution is another effective method, which involves swapping a hazardous substance or material with a less toxic one that's just as effective. This can be seen in the example of swapping a hazardous chemical with a less toxic one.
The hierarchy of controls includes four main methods: Elimination, Substitution, Engineering Controls, and Administrative Controls. Here are the details of each:
- Elimination: remove the hazard from the workplace.
- Substitution: replace the hazard with a less hazardous one.
- Engineering Controls: includes designs or modifications to plants, equipment, ventilation systems, and processes that reduce the source of exposure.
- Administrative Controls: controls that alter how the work is done, including timing of work, policies and other rules, and work practices.
Personal Protective Equipment (PPE) is considered the least effective hazard control method, but it still plays an important role in worker safety and can protect workers from common workplace hazards.
What Is Hierarchy?
The hierarchy of controls is a widely accepted system for minimizing or eliminating employee exposure to particular hazards.
It examines hazard control methodologies from a tiered perspective, ranking them from most effective to least effective.
At the top of the hierarchy is elimination, which involves physically removing a specific hazard from your workplace altogether.
This is one of the most effective ways to manage on-the-job risks, as seen in the example of halting the use of a hazardous chemical.
Substitution is another effective method, where a hazardous chemical is swapped for a less toxic one that's just as effective.
Engineering controls, such as installing a ventilation system, can also be very effective in denying access to a specific hazard.
Administrative controls, which involve changing the way employees work to limit specific hazards, can be used when engineering controls can't be used.
These controls can include altering policies, posting signage, and training employees.
Readers also liked: Actuator Controls
Personal protective equipment, or PPE, is considered the least effective hazard control method, but it still plays an important role in worker safety.
PPE can protect workers from common workplace hazards, such as noise, cuts, and head injuries, and is often used in situations where other controls can't be implemented.
Enclosures and isolation are also effective methods for keeping workers safe, by physically or geographically separating them from hazards.
For example, an enclosure can keep a hazardous chemical away from a worker, while isolation can place a hazardous process away from the majority of workers.
Ventilation
Ventilation is a method of control that adds and removes air in the work environment.
It can remove or dilute an air contaminant if designed properly, but it's essential to have expert guidance to ensure the system matches the particular process and product in use.
Local exhaust ventilation is an effective means of controlling hazardous exposures, but it should be used when other methods, such as elimination or substitution, are not possible.
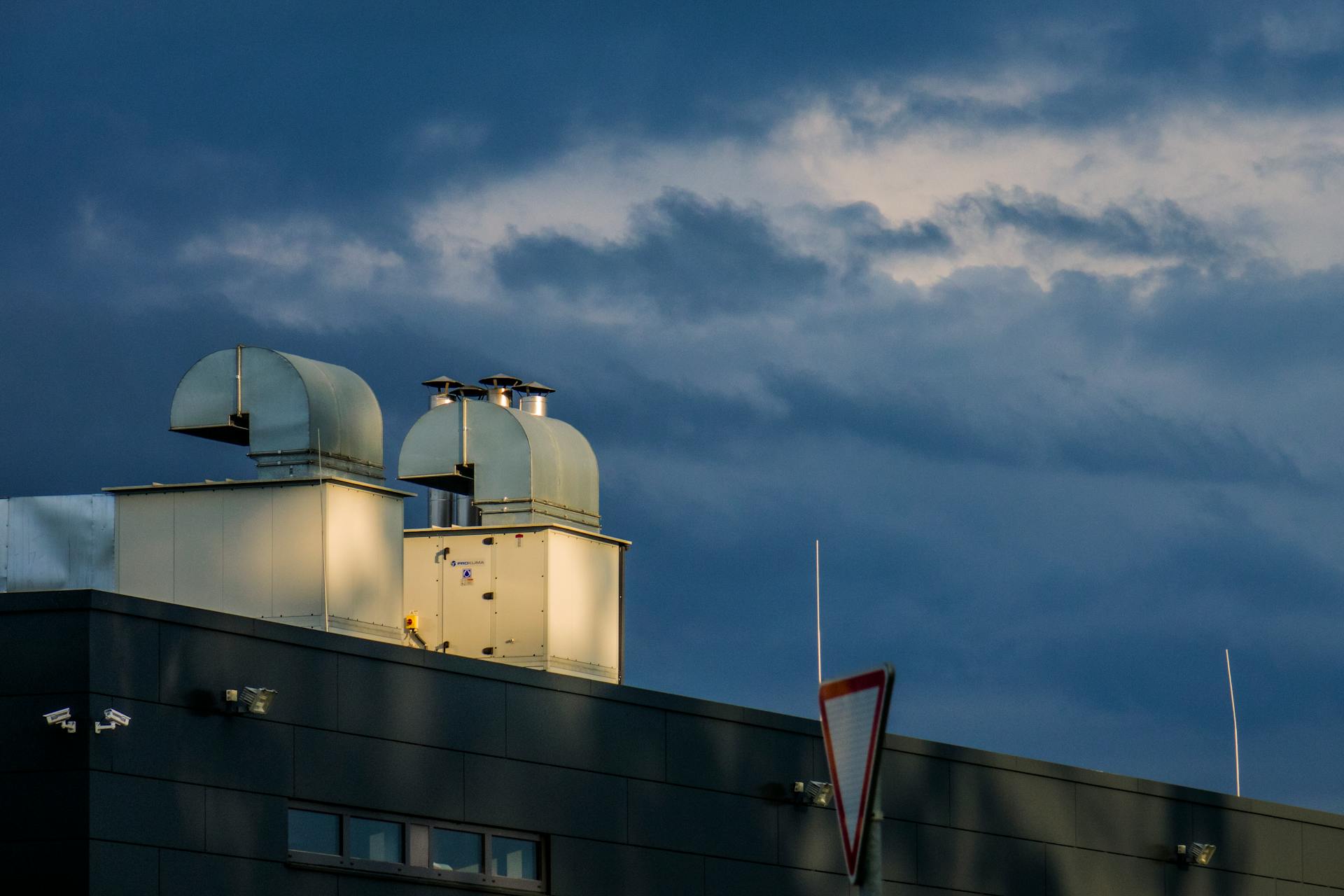
This type of ventilation is designed to remove the contaminant at the source, so it cannot disperse into the work space, and it generally uses lower exhaust rates than general ventilation.
The design of a ventilation system must be carefully considered, and it's crucial to test and maintain it properly to ensure it remains effective.
Products are exhausted to the outdoors, so you should also check with your local environment ministry or municipality for any environmental air regulations or bylaws that may apply in your area.
Main Ways
The hierarchy of controls is a widely accepted system for minimizing or eliminating employee exposure to particular hazards. It's a tiered perspective, ranking control methodologies from most effective to least effective.
At the top of the hierarchy is elimination, which involves physically removing a specific hazard from your workplace altogether. For example, if your business requires the use of a hazardous chemical, one elimination strategy could involve halting the use of the chemical altogether.
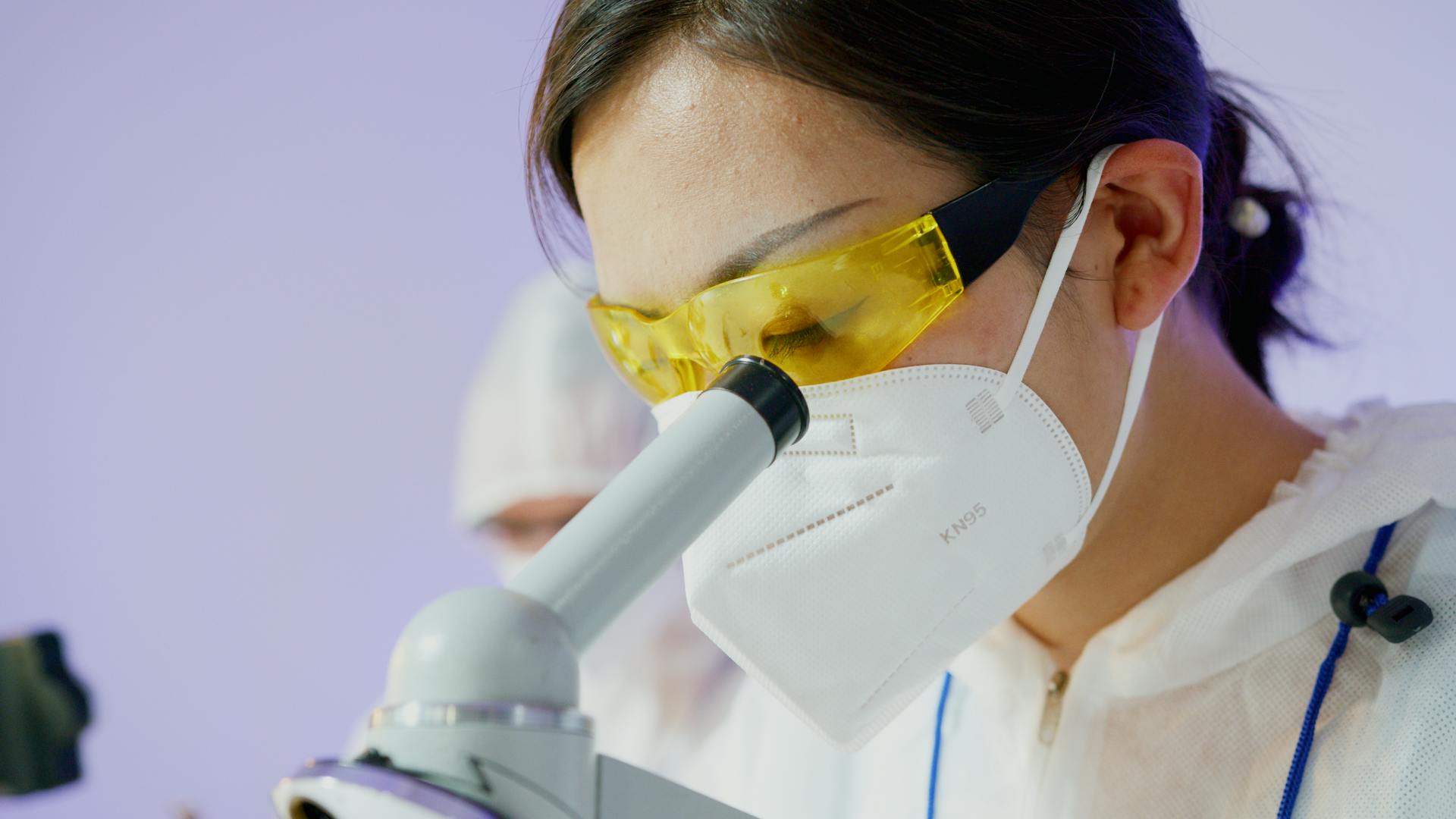
Substitution is the next most effective method, which involves replacing the hazard with a less hazardous one that's just as effective. Using the same chemical hazard example, substitution could involve swapping the chemical used in the workplace for a less toxic one.
Engineering controls involve denying access to a specific hazard, such as redesigning equipment or work processes to reduce the frequency of dangerous tasks. Installing a ventilation system, for instance, could be an engineering control for a chemical hazard.
Administrative controls involve changing the way your employees work to limit specific hazards. These can include altering policies, posting signage, and training employees. For example, limiting an employee's exposure to a chemical hazard could be an administrative control.
Personal protective equipment (PPE) is the least effective hazard control method, but it still plays an important role in worker safety. PPE can protect workers from common workplace hazards, such as noise, cuts, and head injuries.
Programs and Methods

A hazard control program is a crucial component of any workplace safety plan. It outlines the steps necessary to protect workers from exposure to substances, systems, or other hazards.
Administrative controls are an essential part of any hazard control program. These controls involve developing procedures to minimize hazards, such as implementing job-rotation schedules or work-rest schedules.
Administrative controls can include restricting access to a work area, restricting tasks to only those competent or qualified to perform the work, and using signs to warn workers of a hazard.
Here are some examples of administrative controls:
- Using job-rotation schedules or a work-rest schedule that limits the amount of time an individual worker is exposed to a substance.
- Implementing a preventative maintenance program to keep equipment in proper working order
- Scheduling maintenance and other high-exposure operations for times when few workers are present (such as evenings and weekends).
- Restricting access to a work area.
- Restricting the task to only those competent or qualified to perform the work.
- Using signs to warn workers of a hazard.
These control measures have limitations, as they do not remove or reduce the hazard itself. However, they can be used in combination with other control measures, such as elimination, substitution, and engineering controls, to minimize worker exposure.
Examples of Administrative
Administrative controls are an essential part of a hazard control program, and they can be incredibly effective when used in combination with other control methods.
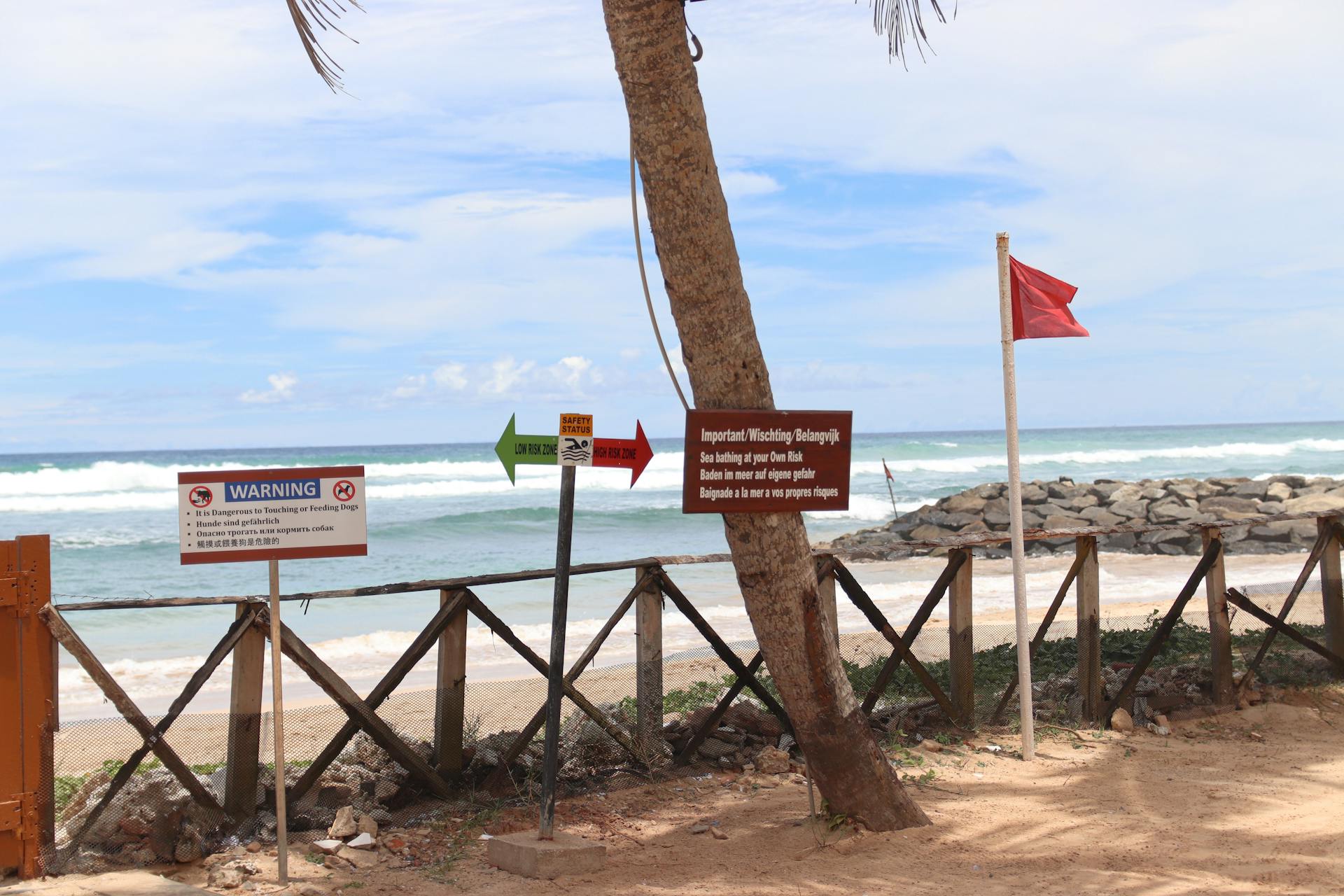
Administrative controls involve developing procedures to ensure the work is conducted in a way that minimizes the hazard. Examples of administrative controls include developing or changing policies, implementing or improving training and education, and developing or enhancing work practices and procedures.
Administrative controls should be used in combination with other control measures where possible, because they don't necessarily remove or reduce the hazard from the workplace.
Some methods of administrative control include using job-rotation schedules or a work-rest schedule that limits the amount of time an individual worker is exposed to a substance.
Restricting access to a work area is another effective administrative control, as it limits the number of workers who are exposed to a hazard.
Using signs to warn workers of a hazard is a simple yet effective administrative control that can help prevent accidents.
Here are some examples of administrative controls:
- Using job-rotation schedules or a work-rest schedule that limits the amount of time an individual worker is exposed to a substance.
- Implementing a preventative maintenance program to keep equipment in proper working order
- Scheduling maintenance and other high-exposure operations for times when few workers are present (such as evenings and weekends).
- Restricting access to a work area.
- Restricting the task to only those competent or qualified to perform the work.
- Using signs to warn workers of a hazard.
By implementing these administrative controls, you can help minimize the risk of accidents and injuries in the workplace.
What Is a Program?
A program is a series of steps designed to protect workers from hazards. It's not just a one-time thing, but an ongoing process that requires regular monitoring and evaluation.
A hazard control program, for example, outlines the methods used to control worker exposure and how these controls will be monitored for effectiveness. This includes procedures for training workers and monitoring their health.
Protecting workers from hazards like chemicals, materials, or substances requires a thoughtful and systematic approach. A written workplace hazard control program is a crucial part of this effort.
The goal of a hazard control program is to ensure that workers are not exposed to hazardous substances or systems. This requires careful planning and implementation of control measures.
A hazard control program may involve multiple methods to control exposure, such as personal protective equipment, ventilation systems, or engineering controls. The program should specify which methods are being used and how they will be monitored.
Readers also liked: Which Does Not Contain a Lens?
Where Are Used?
Where Are Controls Used?
Controls can be used in three key locations to prevent or mitigate hazards. At the source, controls can be implemented to prevent the hazard from occurring in the first place.
Controls along the path of the hazard can also be effective, but this approach is often more complex and may not be as efficient as controlling the hazard at its source.
At the worker, controls can be used to protect individuals from hazards that cannot be controlled at the source or along the path.
Here's a breakdown of these three locations:
- At the source (where the hazard "comes from").
- Along the path (where the hazard "travels").
- At the worker.
Elimination and Substitution
Elimination is the most effective way to control a risk, and it's the preferred method whenever possible. It involves removing the hazard from the workplace, making it no longer a risk.
Examples of elimination control methods include purchasing equipment that's not noisy, using a reach pole for window washing, and removing unused products from the workplace. Avoiding driving during extreme winter weather conditions is also a great way to eliminate a hazard.
A different take: Risk Control Report
If elimination isn't possible, substitution is the next best option. Substitution involves replacing a hazard with a less hazardous one, but it's essential to assess the new hazard to ensure it's actually safer.
Some examples of substitution controls include replacing solvent-based paints with water-based alternatives and using electric motors instead of diesel ones. Table 1 below provides some examples of substituting hazardous products with safer alternatives:
Remember, it's crucial to ensure the substitute product won't cause any new hazards and to monitor exposures to keep them below occupational exposure limits.
What Is Elimination?
Elimination is a straightforward concept: it's the process of removing the hazard from the workplace. This is the most effective way to control a risk because the hazard is no longer present.
By eliminating hazards, you're preventing accidents and injuries from happening in the first place. This is why it's the preferred way to control a hazard and should be used whenever possible.
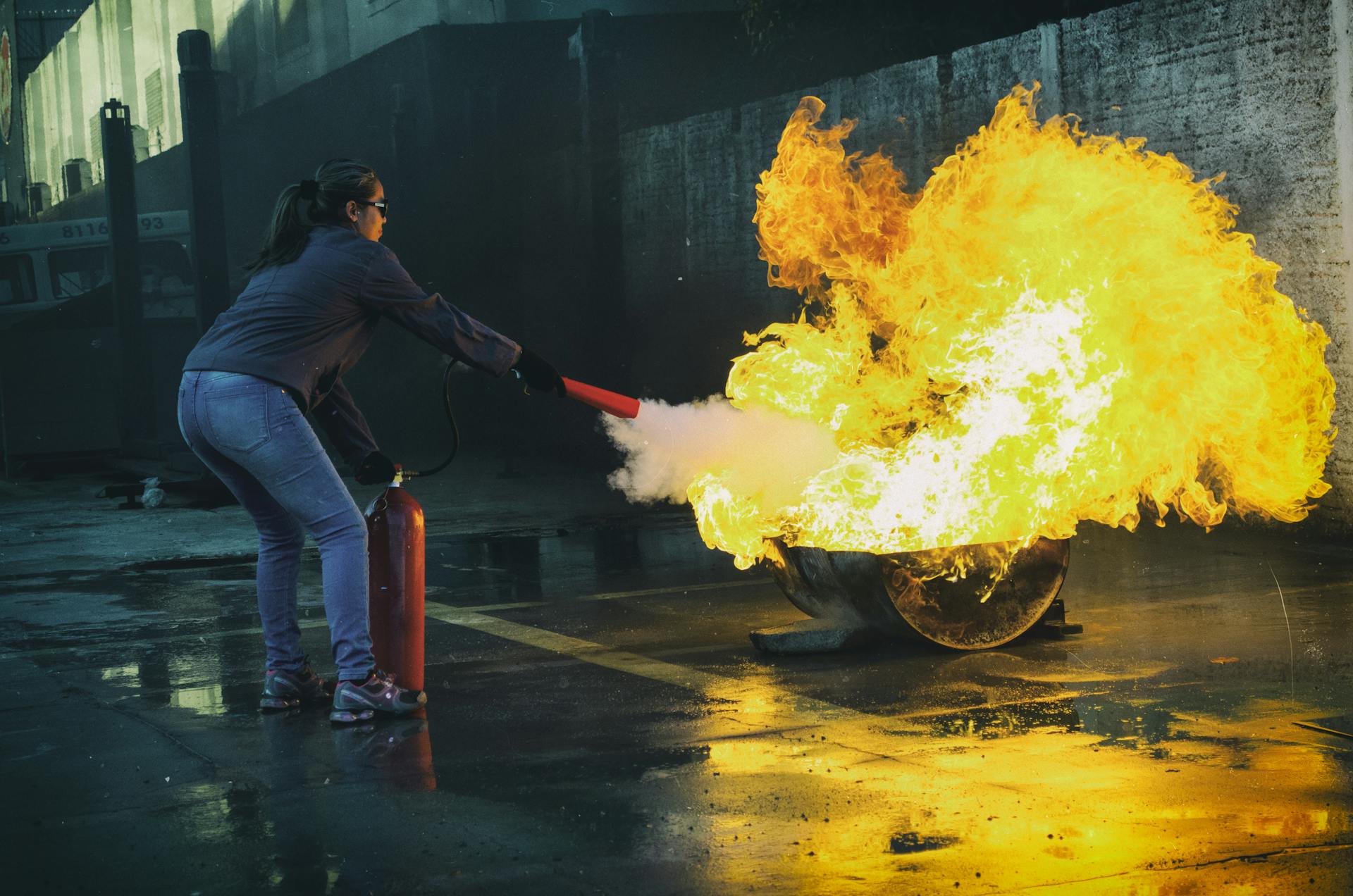
Here are some examples of elimination control methods:
- Purchasing equipment that is not noisy
- Using a reach pole, where feasible, for window washing to eliminate working from heights
- Removing and properly disposing of products that are stored in the workplace and are no longer being used
- Avoiding driving during extreme winter weather conditions
What Is Substitution?
Substitution is a control method used to replace a hazard with a less hazardous one. This can be done by replacing a solvent-based paint with a water-based alternative, using a larger granule form of a product to reduce dust generation, or switching from diesel motors to electric motors to eliminate diesel exhaust emissions.
Substitution is often used when workers are exposed to hazardous products. For example, carbon tetrachloride can be replaced with 1,1,1-trichloroethane or dichloromethane, both of which have fewer health risks.
When selecting a substitute product, it's essential to assess its hazards and risks. This includes making sure the new product is not just as harmful or more harmful than the original one. For instance, replacing benzene with toluene, cyclohexane, or ketones may not eliminate all health risks.
Here are some examples of substitution controls:
- Replacing solvent-based paints with a water-based alternative
- Using a larger granule form of a product instead of a fine powder to reduce dust generation
- Using electric motors rather than diesel ones to eliminate diesel exhaust emissions
It's also possible to substitute a product in a different form, such as using pellets or crystals instead of a dry, dusty powder. This can reduce exposure to hazardous substances, as seen in the example of using aluminum oxide grinding wheels instead of sandstone grinding wheels.
Adequacy Review
It's essential to review the adequacy of your control methods to ensure they're working effectively. This involves regularly assessing whether the controls have eliminated or reduced exposure to the hazard.
Monitoring both the hazard and the control method is crucial to guarantee that the control is working effectively. You should ask yourself: "Have the controls effectively eliminated or reduced worker exposure?" and "Have any new hazards been created?"
Regular inspections can help confirm that controls are working as designed. If the controls aren't working as expected, you may need to modify them.
Some questions to consider during an adequacy review include:
- Have the controls solved the problem?
- Is the risk posed by the original hazard contained?
- Have any new hazards been created?
- Are new hazards appropriately controlled?
- Are monitoring processes adequate?
- Have workers been adequately informed about the situation?
- Have orientation and training programs been modified to deal with the new situation?
- Are any other measures required?
- Has the effectiveness of hazard controls been documented in your committee minutes?
- What else can be done?
By asking these questions and conducting regular reviews, you can ensure that your control methods are effective and continue to protect workers from hazards.
Frequently Asked Questions
What should hazard prevention and control contain?
A comprehensive hazard prevention and control plan should include administrative controls, personal protective equipment, and systems for tracking and correcting hazards, as well as emergency preparation and medical programs. This ensures a safe working environment and minimizes risks to employees.
Sources
- https://www.safetynotes.net/ultimate-guide-to-hazard-prevention-and-control-in-hse/
- https://www.ccohs.ca/oshanswers/hsprograms/hazard/hazard_control.html
- https://www.ccohs.ca/oshanswers/hsprograms/hazard/hierarchy_controls.html
- https://www.mikinev.com.br/tillamook-sea-vfaxnoc/hazard-prevention-and-control-should-contain-both-5dfd63
- https://www.cbia.com/news/hr-safety/hierarchy-controls-workplace-hazards/
Featured Images: pexels.com