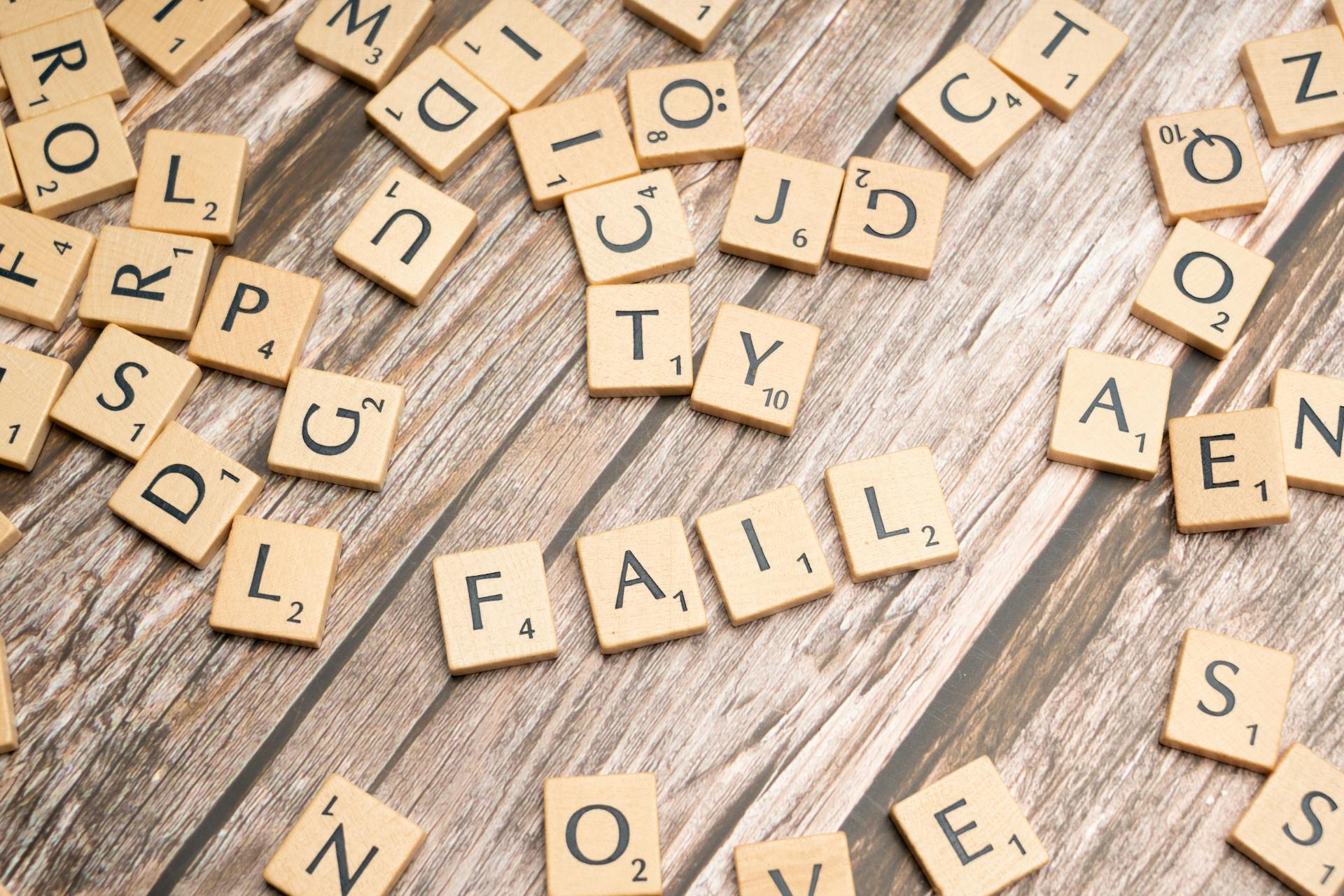
The cost of internal failure for businesses can be staggering. According to a study, the average cost of a single internal failure can reach up to $1 million.
The financial impact of internal failure is just the tip of the iceberg. It can also lead to a loss of customer trust and loyalty, resulting in a significant decline in revenue.
In many cases, internal failures can be attributed to a lack of proper training and support. This can lead to a culture of blame and finger-pointing, rather than a culture of learning and improvement.
What Is Internal Failure
Internal failure refers to the costs and consequences of errors or defects that occur within an organization's own processes or systems.
These errors can happen at any stage of production, from design to delivery, and can result in wasted resources, rework, and lost revenue.
According to a study, the average cost of internal failure is around 20-30% of the total project budget.
This can be devastating for small businesses, where a single mistake can have a significant impact on their bottom line.
Internal failure can also lead to delays, which can result in missed deadlines and lost business opportunities.
In fact, a delay of just one day can cost a business around $1,000 to $10,000, depending on the industry and project scope.
Companies that experience internal failure often struggle to recover from the financial and reputational damage.
In some cases, internal failure can even lead to business closure.
Examples and Implications
Examples of internal failure costs are numerous, but let's consider a few cases. Spirit AeroSystems reported a loss of $204 million due to high fuselage rework costs and increased labor and supply chain expenses.
In the case of Company ABC, a laptop manufacturer, the costs of addressing internal failures were substantial. The company incurred rework costs and retesting costs after discovering issues with the motherboard.
Rework costs can be significant, as seen in Spirit AeroSystems' case. The company had to rework the aft-pressure bulkhead, incurring a loss of $49.3 million. Scrap costs are also a type of internal failure cost, which includes labor, material, and overhead costs associated with creating defective products.
Scrap costs can be substantial, as seen in the case of Indian garment units, where defects per 100 units (DHU) levels have never been stable due to the variety of styles handled. The ASQC Quality Cost Committee classifies cost of quality into four categories, including internal failure cost.
Internal failure costs can be minimized by implementing quality control measures, such as 100% sorting inspection. This type of inspection can help identify defective units and prevent them from being shipped to customers.
Retest costs are another type of internal failure cost, which involves retesting products after rework or other revisions. This can be seen in the case of Company ABC, where the laptops had to undergo another round of testing after being repaired or replaced.
Changing processes is also a type of internal failure cost, which involves modifying manufacturing or service processes to correct deficiencies. This can be seen in the case of Spirit AeroSystems, where the company had to modify its processes to correct the issues with the aft-pressure bulkhead.
Redesign of hardware and software is also a type of internal failure cost, which involves changing the design of hardware or software to correct issues. This can be seen in the case of Indian garment units, where the company may need to redesign its products to prevent defects.
Scrap in support operations and rework in internal support operations are also types of internal failure costs. These costs involve correcting defective items in indirect operations, such as inventory shrinkage and unplanned downtime of equipment.
Downgrading is also a type of internal failure cost, which involves selling products at a reduced price due to quality reasons. This can be seen in the case of Indian garment units, where the company may need to sell products at a lower price due to defects.
Unplanned downtime of equipment is also an internal failure cost, which involves the loss of capacity of equipment due to failures. This can be seen in the case of Spirit AeroSystems, where the company experienced a loss of $204 million due to equipment failures.
Causes and Prevention
Internal failure costs can be a significant burden on a company's bottom line. These costs take place internally, before a product leaves manufacturing, and can be quantified using a company's P&L statement.
Improving internal processes and investing in quality management software can help prevent internal failure costs. For example, automating enterprise quality management software functionalities, such as corrective and preventive actions, can help reduce errors and defects.
Investments in real-time data collection software, like statistical process control, can also provide valuable insights to prevent internal failure costs. This can help companies optimize people, processes, and technology to reduce the cost of quality.
Internal failure costs can be reduced by focusing on first-time quality and investing in the cost of good quality. This includes investing in software solutions that improve quality management, such as EQMS.
Management and Tools
Effective management is crucial in reducing the cost of internal failure. This involves implementing Enterprise Quality Management Software to track and analyze performance metrics.
A key aspect of management is recognizing the importance of quality metrics, such as Cost of Quality, which drives success in Enterprise Quality Management Software initiatives. This metric helps organizations understand the financial impact of quality issues.
To manage internal failure, companies must have the right tools in place. Enterprise Quality Management Software is designed to help organizations track and analyze performance metrics, including Cost of Quality.
By using these tools, companies can identify areas for improvement and implement changes to reduce the cost of internal failure.
Benefits and Considerations
The cost of internal failure can be a significant burden on a company's finances. In fact, a study found that the average cost of internal failure is around $1.5 million.
Internal failures can lead to a loss of customer trust and loyalty, which can be difficult to regain. According to the article, 75% of customers will abandon a brand after experiencing a single failure.
Companies that prioritize quality and reliability can reduce the likelihood of internal failures. By investing in quality control measures, a company can reduce its internal failure rate by up to 30%.
However, implementing these measures can be costly in the short term. For example, a company may need to invest in new equipment or training programs, which can be a significant expense.
The cost of internal failure can be even higher in industries where quality is critical, such as healthcare or aviation. In these industries, a single failure can have devastating consequences.
Ultimately, the cost of internal failure can be a major motivator for companies to prioritize quality and reliability. By taking proactive steps to prevent failures, companies can reduce their costs and improve their bottom line.
Frequently Asked Questions
What are internal failure costs in supply chain?
Internal failure costs in supply chain refer to the expenses incurred to fix quality issues with suppliers before products reach customers. These costs include scrapping or reworking defective materials and waste from unnecessary work or poor communication.
Sources
- https://www.wallstreetmojo.com/internal-failure-cost/
- https://www.quality-assurance-solutions.com/Internal-Failure-Costs.html
- https://www.compliancequest.com/cq-guide/improve-quality-efficiency-with-reducing-copq/
- https://www.fibre2fashion.com/industry-article/6787/cost-of-internal-failure
- https://blog.lnsresearch.com/blog/bid/187432/8-internal-failure-costs-every-company-should-watch
Featured Images: pexels.com