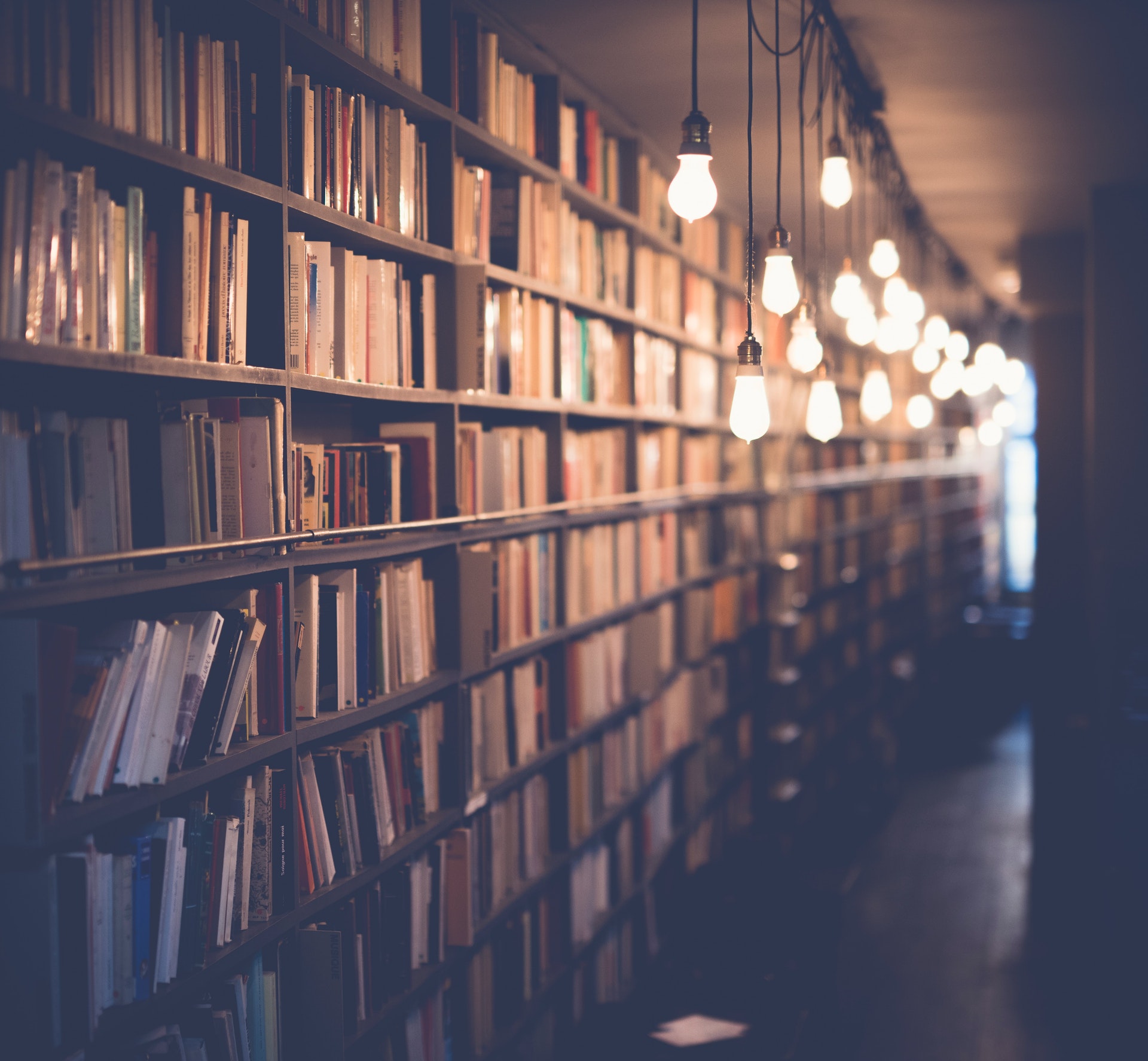
Aluminum welding is an important aspect of construction and the manufacture of many products. So the question is: can you spot weld aluminum? The answer is yes — however, it takes a certain skill level and welding equipment to do so.
Spot welding aluminum is different from other metals due to its lower resistance to electrical current and higher thermal conductivity. As a result, typical spot welding equipment will not be sufficient for the job — as a high-end welder adapted for aluminum spot welding must be used. It requires significantly higher amps or volts than for steel, for example, in order to penetrate and form a successful bond between metal sheets.
For those who are experienced in spot welding, many recommend double-sided spot welding if your aluminum material will stay exposed amidst the weather elements, since it helps to create a more secure connection than one-sided spot welds. Furthermore, take into account that some combinations of aluminum require specialized filler rods given the distinct properties found in specific grades (for example grade 5083 usually requires SLG type filler rod). In addition, when preparing your workpieces it is important to ensure cleaning supplies are used on both sides and that the surfaces being melted together are free of grease or other imperfections which may affect the strength and quality of your welded joints.
In conclusion — yes you can indeed spot weld aluminum! It does take skill and know-how plus specialized equipment and prepares but with these steps fulfilled you can ensure greater success with your welds.
A unique perspective: Can You Use Bleach on Your Areola?
What welding process is used to weld aluminum?
Welding aluminum is a common task that can be completed using the following welding processes: gas tungsten arc welding, gas metal arc welding, and shielded metal arc welding.
Gas Tungsten Arc Welding (GTAW), also known as TIG (Tungsten Inert Gas) is the most common and technically advanced process used for aluminum welding. GTAW is extremely reliable and provides a high level of accuracy to weld thin materials with minimal distortion. This process requires the use of a stable gas mixture such as pure Argon to form an inert atmosphere around the arcs making it possible to weld even the thinnest materials with extreme accuracy. This process uses direct current (DC) which creates interesting applications such as allowing users to reverse polarity in order to achieve maximum penetration on thicker materials while still providing excellent result on thin metals. The downside of this type of aluminum welding is the price of specialized equipment such as helium and argon tanks, flux cables and power supplies that increase over time due to oxidation from air contact with the electrodes.
Gas Metal Arc Welding (GMAW), also known as MIG (Metal Inert Gas) welding is also a popular choice for aluminum welding. GMAW is very simple in operation and does not require a skilled operator which makes it more economical for some applications. This process is characterized by continuous current, high efficiency and good bonding quality due to its low heat input compared to other types of welding processes. It also provides users with portability in comparison with GTAW since no gas tank or special cables are needed in order to start this type of welding process.
The last type of aluminum welding you might consider is Shielded Metal Arc Welding (SMAW) which is commonly referred to as "stick" or "arc" welding. SMAW has been around since the 1920s and is still used today for basic applications involving thick metals, such as heavy-duty equipment repairs and construction projects where materials must be joined quickly because of atmospheric conditions or lack of access for other options like GMAW/FCAW methods. Stick welding can be performed outdoors without any shielding gas which makes it very versatile in many circumstances where GMAW/FCAW can not be practical due to external factors like wind, exposure or high temperatures which can affect the fill quality of these processes respectively when working outdoors under certain circumstances above mentioned scenarios make this method ideal when dealing with thick materials like surface plates made out of thick steel plates or heavy duty equipment parts that must be joined quickly due to atmospheric conditions or simply lack of gaining access for other options than stick method usage on some specific projects like joining thick metals, hence Stick Welding process should be considered among few other alternatives while selecting appropriate typeof Aluminum alloy joining procedure depending on specifics associated with The Selected Applications
On a similar theme: What Is Friction?
How do you join aluminum components with welding?
Welding aluminum is a great way to join two components in order to create a strong and reliable bond. It’s a simple process that requires you to have the right welding tools, such as an aluminum MIG or TIG welder. Before beginning the joint, it’s important to properly prepare the aluminum for welding. This includes removing any grease and rust from the materials, as well as cleaning off any traces of paint or other foreign particles.
Once the components are appropriately prepped, you can start welding them together using a specific filler metal. For certain aluminum alloys, you’ll need a heat sink and backbone bar in order to avoid cracking while welding. When selecting your filler metal, it’s important that you look for one that has good properties when it comes to flowability and fatigue strength ratings. Once everything is ready, you can begin welding at very low temperatures and then heat up gradually as needed for effective fusion between the two pieces of aluminum. Take special care to keep your weld arc short in order to minimize porosity in the joint. Don't forget that when working with aluminum it's important to ensure adequate ventilation due to harmful fumes released during the process.
Aluminum welding is an easy process when done correctly. By following these steps, you can ensure that your weld joint will be strong and reliable without any difficulty!
Intriguing read: Which Ensure Is Best?
How can you weld aluminum to other metals?
Welding aluminum to other metals is an exciting way to add strength, beauty, and all-around stability to projects. With some knowledge and use of the right materials and techniques, you can create strong welded joints in these metals with relative ease such as joining on components. There are some very important steps you must take to ensure a successful weld, however.
First, it is essential that you use an aluminum-specific welding rod. A standard steel rod will not work with aluminum, no matter the welding process used. Plus, there is a higher heat needed for aluminum so it is important to use the correct rod type that can withstand the heat required by the weld; different types of od require different types of shielding — usually Argon.
Second, make sure there is enough cleaning before starting any welding of metals together. Dirt, grease or oil will eliminate any chance of ultra-strong bonds with either material as well as prevent an even flow for both materials during the process — so it’s important to make sure everything is clean before starting! The most common form of cleaning for these metals used for welding is sanding them down and deoxidizer treatments when necessary.
Thirdly, once the item has been cleaned off properly, you should then adjust your welder’s amperage appropriately according to what metal types you are welding together (aluminum needs a higher amperage than steel). The next step would be tacking in your pieces first before applying pressure and fully working on your metal joint — this allows space between each piece and also keeps them in position better while being welded together. Finally, when your joint has been tacked properly and the full weave has been made it will be complete!
With proper supplies and attention to detail while following steps in sequence, anyone can achieve satisfactory results when welding aluminum or other metals together. That said always make sure wear protective gear such as safety glasses and gloves during this process and follow safety precautions set forth by your equipment manufacturer for best results!
See what others are reading: What Metals Are Hypoallergenic?
Is it possible to weld aluminum at home?
Welding is an art, and crafting aluminum requires even more delicacy and precision. There have been advances in welding technology in the past few decades that have made a number of projects doable, even by amateur welders. So, is it possible to weld aluminum at home?
The answer is a resounding yes! Aluminum can be successfully welded at home with the right supplies and basic knowledge. Aluminum welding needs a specialized metal alloys as filler material, although it’s possible to use other materials if absolutely necessary. You’ll also need a specialized welder for aluminum that can work on metal pieces between 16 and 18 gauges with safety-approved gas or gasless wire feed. Investing into the proper tools like DC current stainless steel electrodes and sheet holders designed for aluminum will be key in getting great results.
Having the right tools is essential for successful welding, but knowledge is just as important. Just like skillful bakers who can create a delicious cake without proper ingredients, you can still do good work without all the right supplies by understanding how to apply pressure in the right way to prevent blowouts while also keeping an eye out on its integrity while working through each step of crafting your project. It’s always best to be well-informed on techniques before starting any project in order to reduce start-up time and money while boosting your safety during the process.
For your interest: Proper Lookout
What type of welding process is best for welding aluminum?
The welding process that is best for welding aluminum depends on factors related to the application and properties of the aluminum being welded. Some of the most popular aluminum welding processes include gas tungsten arc welding (GTAW or TIG), gas metal arc welding (GMAW or MIG), shielded metal arc welding (SMAW or stick) and oxy-fuel welding.
Gas tungsten arc welding produces heat that is generated through an electric arc created between a non-consumable tungsten electrode and the base material. This process is considered optimal when joining aluminum because it produces clean welds with minimal distortion and offers excellent control over heat input levels. It also offers higher travel speed capabilities in comparison to other processes which contributes to reduced joint preparation time.
Gas metal arc welding produces heat from an electric arc between a consumable wire electrode and the base material. It is often used for its high deposition rates, flexibility in operations and lower cost because it does not require as much equipment nor number of highly-skilled technicians as some other processes do. This method also allows more efficient use of filler metals than oxy-Fuel, though there may be build up within welds if excess filler material is present.
Shielded metal arc welding uses an electric current flowing through a flux-coated electrode to create heat both at the electrode tip as well as between the workpiece and electrode itself, forming a puddle out of which molten slag forms on top of which solidified weld pools originate after cooling down. This method is typically used on thicker materials since it can only produce high-quality fillet welds on pieces measuring up to 3/8 inch thick due to intrinsic low penetration levels, making it useful for basic repairs or in construction projects involving pipes made from thicker sheet metals like aluminum alloys.
Oxy-fuel recently became popular due to its cheaper equipment costs, however, this process can be difficult to manage owing to its high levels of heat input affecting distortion rates negatively in comparison with some other methods when dealing with aluminum materials. Additionally, this technique requires higher skillset from the operators due to its manual nature when cutting compared to automatic processes such as GMAW or GTAW which produce cleaner cuts offering higher precision levels while maintaining cheaper equipment costs overall in comparison with laser based systems used in fabrication shops worldwide on a daily basis.
Explore further: Aux Input
Are there special considerations for welding aluminum?
Welding aluminum is a difficult and different process compared to welding other metals. It presents several unique challenges for welders, so to properly answer the question, let us examine some of the most important special considerations for welding aluminum.
Heat is a major factor when it comes to welding aluminum. When working with aluminum, the welder must pay special attention to the heat generated by the weld area as well as the traveling bead of molten metal during GMAW (Gas Metal Arc Welding). The heat will cause the metal to react differently than when welding other metals. A good way to avoid overheating is to reduce the amperage while increasing travel speed; slower travel speed means higher amperage, resulting in more heat generated in the weld pool.
One of aluminum's natural attributes is its tendency to develop oxides on its surface when exposed to oxygen. This oxide layer needs be cleaned off prior to welding if you want your welds beads to look good and properly hold up over time - just as with other metals, proper cleaning is key for proper result and quality assurance. Aluminum can also warp slightly as it heats, so make sure you clamp your workpieces in place before beginning any work on them or you may find yourself dealing with incorrect fitment afterwards!
In short, yes there are indeed special considerations for welding aluminum that require care and attention from the welder if great results are desired. Quality assurance should always be a priority when it comes to this specialized craftsmanship – make sure you take every precaution necessary and adhere to safety regulations at all times!
Explore further: Welding Rod Oven
Sources
- https://www.materialwelding.com/can-you-weld-aluminum-to-steel-metals/
- https://weldingmagazine.com/what-gas-to-use-to-weld-aluminum/
- https://mydecorative.com/a-basic-guide-to-welding-aluminum-at-home/
- https://blog.red-d-arc.com/welding/aluminum-welding/aluminum-welding-challenges/
- https://weldingpros.net/welding-aluminum/
- https://www.millerwelds.com/resources/article-library/mig-welding-aluminum-important-questions-and-best-practices
- https://weldingtroop.com/how-to-weld-aluminum-at-home-a-beginners-guide/
- https://www.wikihow.com/Weld-Aluminum
Featured Images: pexels.com