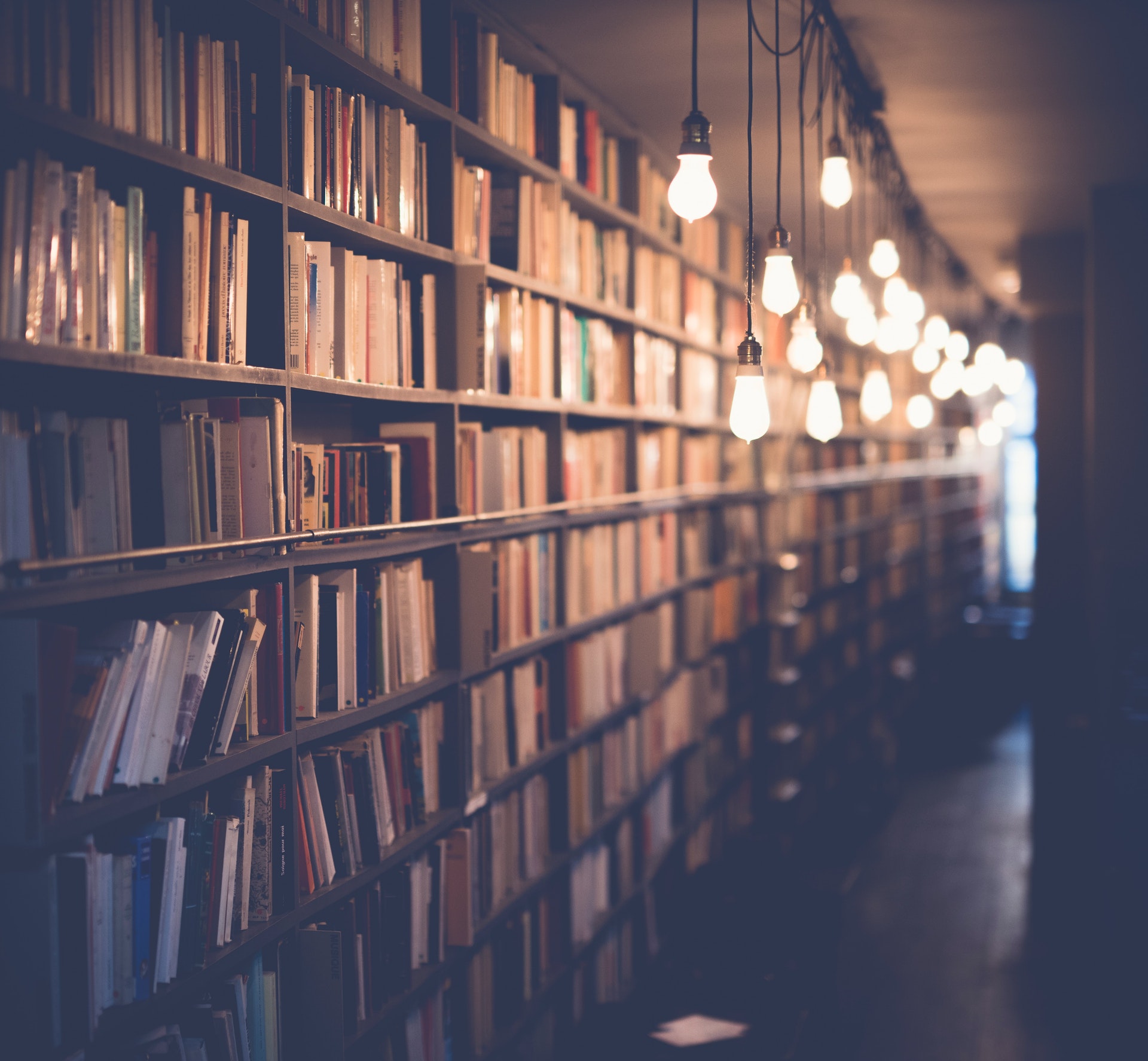
Can you plasma cut aluminum?
The answer to this question is yes, you can plasma cut aluminum. Plasma cutting is a process that uses a high-velocity stream of ionized gas to cut through metal. This ionized gas is created by using an electrical arc to ionize a gas, such as argon, that is flowing through a nozzle. The result is a plasma jet that can cut through metal.
One of the benefits of plasma cutting is that it can be used to cut through aluminum. Aluminum is a difficult material to cut through with traditional methods, such as saws and lasers. However, plasma cutting can easily cut through aluminum. Plasma cutting is also a very fast method of cutting, which can save time when cutting aluminum.
In order to plasma cut aluminum, you will need a plasma cutter. Plasma cutters are available in a variety of sizes and styles. You will also need to select the right type of nozzle for your plasma cutter. The nozzle is what determines the shape of the plasma jet. You will also need to select the right gas for your plasma cutter. Argon is a common gas that is used for plasma cutting, but other gases, such as nitrogen, can also be used.
Once you have all of the necessary equipment, you are ready to start plasma cutting aluminum. The first step is to set up your plasma cutter. You will need to connect the power supply to the plasma cutter and turn on the gas. Once the plasma cutter is turned on, you can begin cutting.
To cut aluminum with a plasma cutter, you will need to hold the tip of the cutter close to the aluminum. The plasma jet will cut through the aluminum at a high speed. You can move the plasma cutter around to cut through different thicknesses of aluminum.
If you are cutting through a large piece of aluminum, you may need to use a guide to help you keep the cutter in the right position. A guide can also help you cut through aluminum that is curved or irregular in shape.
Plasma cutting is a great way to cut through aluminum. It is fast, easy to use, and can save you time.
For another approach, see: Plasma Cutter Cut Aluminum
What is plasma cutting?
In welding and other industrial and construction applications, plasma cutting is a process where a gas is used to cut through electrically conductive materials. The gas is ionized to create plasma, which, in turn, heats the material and causes it to melt, vaporize, or ablate. Plasma cutting is an effective way to cut through materials such as stainless steel, aluminum, brass, and other metals.
While plasma cutting has many advantages, there are also some disadvantages to using this process. One disadvantage is that plasma cutting can produce dangerous UV radiation. Another disadvantage is that the process can create a lot of noise. Additionally, plasma cutting can produce hazardous fumes that can be harmful to both people and the environment.
Recommended read: Cutting Aluminum
What are the benefits of plasma cutting?
Plasma cutting is a process that uses a superheated jet of ionized gas to cut through metal. The process is very versatile and can be used to cut through a variety of materials, including stainless steel, aluminum, and even titanium. Plasma cutting is a very fast and efficient way to cut metal, and the process can be automated to produce very precise cuts.
There are many advantages to plasma cutting over traditional methods such as oxy-fuel cutting or machining. Plasma cutting is much faster than oxy-fuel cutting, and the process can be easily automated. Additionally, plasma cutting produces very little heat-affected zone (HAZ), which means that the material being cut is less likely to be damaged by the cutting process.
Another advantage of plasma cutting is that it can be used to cut very thin materials. This is because the plasma jet is very focused, and can be controlled very precisely. This means that plasma cutting can be used to cut very delicate materials, such as thin sheets of aluminum or titanium.
Overall, plasma cutting is a very versatile and efficient way to cut metal. The process is fast, precise, and can be easily automated. Additionally, plasma cutting produces very little heat-affected zone, making it ideal for cutting thin and delicate materials.
Take a look at this: 100w Co2 Laser Cut Metal
What are the disadvantages of plasma cutting?
Plasma cutting is a thermal cutting process that uses a plasma torch to cut through conductive materials. Plasma cutting is often used in industrial and metalworking applications, as it can cut through thick materials quickly and easily. However, there are some disadvantages to using plasma cutting, which include:
1. Plasma cutting can be a dangerous process if not properly done. The plasma torch produces a very hot and bright plasma arc, which can easily cause burns or blindness if someone is not careful.
2. Plasma cutting produces a lot of heat, which can distort or damage the material being cut.
3. Plasma cutting can produce hazardous fumes, which can be harmful to the operator and those nearby.
4. Plasma cutting produces a lot of noise, which can be a nuisance for those working nearby.
5. Plasma cutting can be a costly process, as it requires special equipment and training.
What are the best practices for plasma cutting?
There are a few best practices to follow when plasma cutting to ensure safe and optimal cut quality. Always wear proper personal protective equipment, including gloves, goggles, and a welding helmet with a dark filter. Make sure the area around the cutting zone is clear of any flammable materials, and always have a fire extinguisher on hand.
When setting up the plasma cutter, be sure to follow the manufacturer's instructions. Adjust the height of the torch so that the tip is just barely touching the metal surface. The plasma cutting process will create a lot of sparks and heat, so be sure to have proper ventilation in the work area.
Start the plasma cutter and slowly guide it along the cutting line. Keep the tip at a consistent distance from the metal surface, and don't move too quickly or the cut will be uneven. After completing the cut, turn off the plasma cutter and allow the metal to cool before handling.
You might enjoy: When Can You Cut a Puppy's Nails?
What are the different types of plasma cutting?
Plasma cutting is a process that uses a high-velocity stream of ionized gas to cut through conductive materials. The gas is typically composed of a mix of Argon and Hydrogen. Plasma cutting is often used in industrial applications, such as cutting metal plate, pipe, and other materials. There are two main types of plasma cutting systems: handheld and robotic.
Handheld plasma cutting systems are portable and can be used in a variety of settings, including construction sites, auto body shops, and fabrication shops. These systems typically use a trigger to start the flow of plasma, and the operator guides the torch along the cutting line.
Robotic plasma cutting systems are fixed in place and controlled by a computer. These systems are often used in industrial settings, such as metal fabrication shops and steel mills. Robotic plasma cutting systems can be programmed to cut specific shapes and patterns.
Plasma cutting is a versatile process that can be used to cut a variety of materials, including metals, plastics, and composites. Plasma cutting can be used to create straight, curved, or complex shapes. The process is relatively safe and can be performed quickly and easily.
If this caught your attention, see: How Often Can You Have Botox?
What is the difference between CNC and manual plasma cutting?
There are several important differences between CNC (computer numerical control) and manual plasma cutting. Perhaps the most important difference is that CNC plasma cutting is automated, while manual plasma cutting is not. This means that CNC plasma cutters can be operated with much less operator involvement than manual units.
CNC plasma cutters also have much higher accuracy than manual units. This is due to the fact that CNC units use computer-controlled movement to make cuts, while manual units do not. This means that CNC units can make very precise cuts, while manual units cannot.
Another difference between CNC and manual plasma cutters is the price. CNC plasma cutters are significantly more expensive than manual units. This is due to the fact that CNC units are more complex and require more expensive components.
Finally, CNC plasma cutters typically have a higher cutting speed than manual units. This is due to the fact that CNC units can move the cutting torch more quickly and precisely than manual units.
You might enjoy: Cnc Router Cut
What are the most common applications for plasma cutting?
Plasma cutting is a process that uses a stream of hot plasma to cut through electrically conductive materials. Plasma cutting is commonly used in a variety of industries, including automotive, aerospace, and shipbuilding. In addition, plasma cutting is often used in the fabrication of metal parts for a variety of applications.
Some of the most common applications for plasma cutting include cutting metal sheets, pipes, and tubes. plasma cutting can also be used to create openings in metal surfaces for the purpose of welding or other joining processes. Additionally, plasma cutting can be used to create holes for bolting or riveting.
Plasma cutting is a versatile process that can be used to cut a variety of materials, including steel, stainless steel, aluminum, copper, and brass. In addition, plasma cutting can be used on a variety of thicknesses, from thin sheet metal to thick plate.
If this caught your attention, see: Laser Cut Galvanized Steel
What are the most common materials that can be cut with plasma?
There is no definitive answer to this question as different materials can be cut with different types of plasma. However, some of the most common materials that can be cut with plasma include metals (such as steel and aluminum), as well as certain types of plastics. In general, plasma cutting is a very versatile tool and can be used to cut a wide variety of materials.
What are the most common sizes and thicknesses of plasma cutting?
When it comes to plasma cutting, size and thickness really do matter. There are three main types of plasma cutting machines: portable, hand-held and bench-top. Each one is designed to cut a different range of materials, so it's important to choose the right machine for the job.
The most common sizes of plasma cutting machines are the portable and hand-held varieties. These are great for cutting smaller pieces of material, such as sheet metal or thin plate. The portable machines are usually lighter and more compact, making them easy to transport and set up. Hand-held plasma cutters are a bit more powerful, so they can handle thicker materials.
Bench-top plasma cutters are the largest and most powerful type of machine. They're designed for cutting thicker materials, such as plate steel. They're not as portable as the other types of machines, but they can handle the toughest jobs.
When it comes to cutting material thickness, most plasma cutting machines can handle between 1/8 inch and 2 inches. Some machines can cut even thicker materials, but they're not as common. The thickness of the material you're cutting will determine the size and power of the machine you need.
No matter what size or thickness of materials you need to cut, there's a plasma cutting machine that's right for the job. With so many options on the market, it's important to do your research to find the best machine for your needs.
A different take: When Can I Retire
Frequently Asked Questions
What can I cut with a plasma cutter?
A plasma cutter can cut a variety of materials, including metals, plastics, and composites. Some of the most common uses for a plasma cutter include cutting metal sheets and plates, fabricating parts out of plastic or other materials, and crafting various composite materials.
What is the difference between plasma cutting and laser cutting?
Laser cutting is a cutting process using lasers to cut materials. The use of lasers greatly reduces the amount of heat and material required, making the process faster and more precise than other types of cutting. Plasma cutting uses high-energy arcs that create a hot gas, called plasma, which cuts the material.
What is the history of plasma cutting?
Plasma cutting typically grew out of plasma welding in the 1960s, where it proved to be an efficient way of cutting sheet metal and plate. The advantages of plasma cutting over traditional "metal against metal" cutting include that there is no production of metal chips, the cuts are accurate, and the edge left by the process is usually cleaner than what can be achieved with oxy-fuel cutting.
What is CNC Plasma cutting?
CNC plasma cutting is a process that cuts through electrically conductive materials by means of an accelerated jet of hot plasma. The cutting edge is heated to 2500 degrees Celsius and accelerated to a speed of up to 80,000 km/h (50,000 mph).
What materials can be cut with a plasma cutter?
Most plasma cutters can cut most metals, depending on the power and speed of the machine.
Sources
- https://unimig.com.au/9-tips-tricks-to-improve-your-plasma-cutting/
- https://weldinghelmetreviews.com/cut-aluminum-with-a-plasma-cutter/
- https://www.hypertherm.com/en-US/resources/spark-the-blog/plasma-cutting-aluminum/
- https://espritautomation.com/benefits-of-plasma-cutting/
- https://blog.glwengineering.co.uk/plasma-cutting-advantages-and-disadvantages
- https://www.chinaweldingmachines.com/news/advantages-and-disadvantages-of-plasma-cutting.html
- https://www.morntech.com/blog/fiber-laser-cutting-machine/difference-between-laser-cutting-machine-and-cnc-plasma-cutting-machine/
- https://plasmacutteradvisor.com/plasma-cutting-aluminum/
- https://plasmaadvisor.com/will-plasma-cutter-cut-aluminum/
- https://beginnerweldingguide.com/can-you-cut-aluminum-with-a-plasma-cutter/
- https://quickguidepro.com/plasma-cutting-tips-and-tricks/
- https://altpartsinc.wixsite.com/altpartsinc/single-post/top-3-safety-practices-for-plasma-cutting
- https://www.superwhat.org/what/what-is-difference-between-cnc-and-plasma/
- https://www.intselsteelwest.com/benefits-of-plasma-cutting/
- https://www.reforbes.com/benefits-of-plasma-cutting/
Featured Images: pexels.com