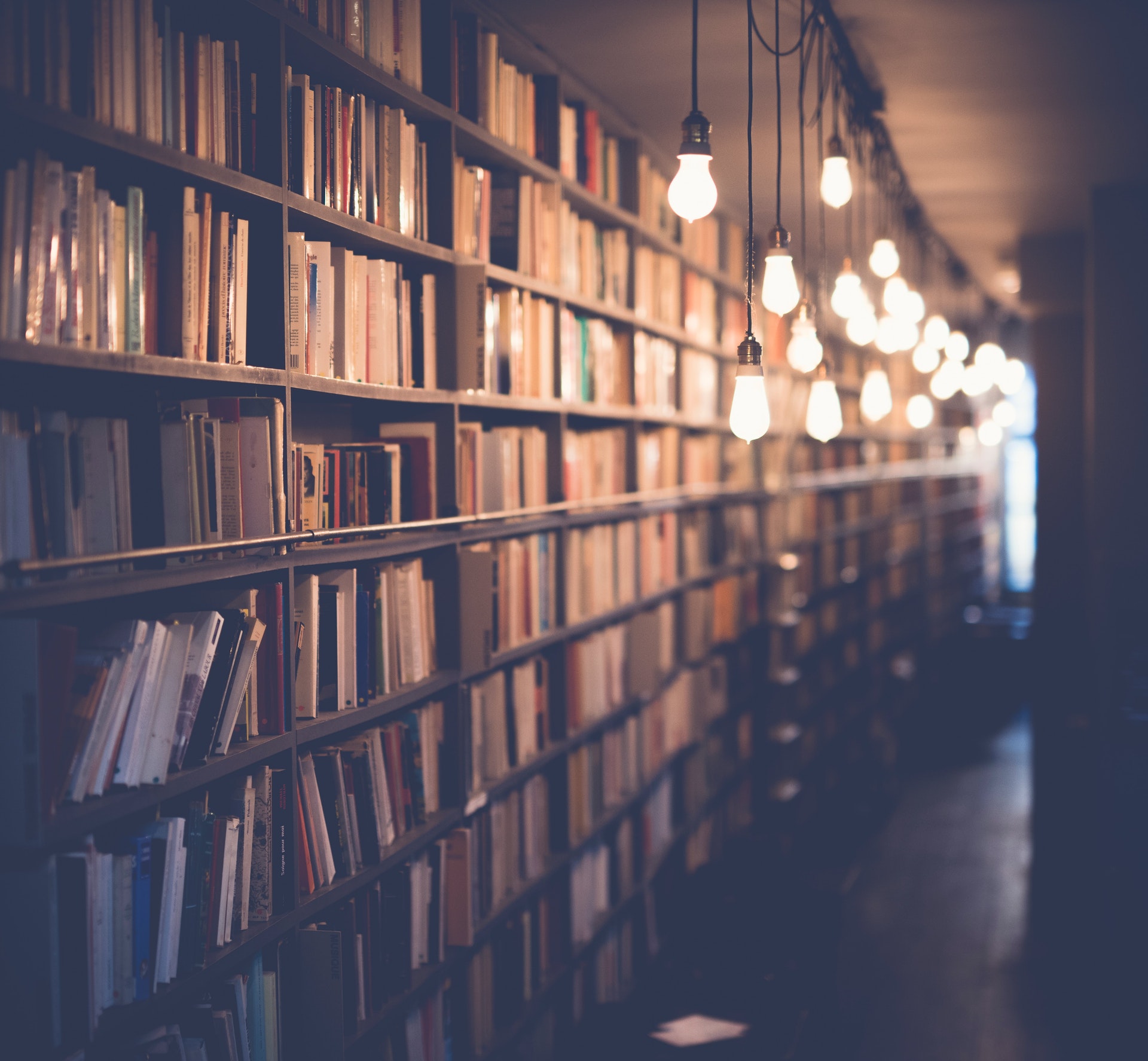
Mig welding is a popular welding process that can be used on a variety of materials, including cast iron. Cast iron is an alloy material, which is a combination of metals and nonmetals, and it has been used to manufacture items since ancient times.
Yes, it is possible to mig weld cast iron. Before attempting to do so, however, it is important to note that cast iron is harder than many other metals, and as such, you will need to use correct techniques when handling the material. Preparation of the surface before welding cast iron is very important. The metal must be clean and free of any rust or other debris that could impede the welds process. Additionally, surface oxidation should be removed with a grinder or wire brush. Be sure to use an appropriate shield gas such as an Argon/CO2 mix in order for your welds to adhere properly.
Once preparations have been adequately made and all necessary safety precautions are taken into account (i.e., safety mask/goggles/gloves), you are now ready for welding. As with any type of welding process, a steady hand and even speed at which you move the mig gun around the joint are critical for success - take your time! As with all welding processes, accuracy will determine whether your welds hold strong over time or not. Proper technique must also be used when adding filler metal in order for distortion to be minimized; too much filler can lead to cracking or other imperfections in the finished welds.
Enough heat needs to generated while welding otherwise it will likely cause porosity which weakens the joint; thus one needs experience not only in preparation but also when applying heat with their welder itself in order to correctly join two pieces of cast iron together through metals fusion alongside some form of filler metal to help maintain structure integrity.
Finally after completing each weld one should go ahead do visual inspection as well as probes if required just to make sure there’s no void present inside fillers material along with x-ray look if applicable so you can know if everything went according to plan or not plus feel free taking advantage of infrared ray while doing this inspection especially after recently done joints since they’ll give out more heat hence clearly conveying how great was heat application on joints, how well filler aid structural integrity & grain flow orientation plus gas penetration depth within joints along with numerous other factors thus let you know where exactly were problems created et cehtera.
In conclusion, yes it is possible to mig weld cast iron – but it takes proper preparation prior as well as accurate techniques while doing so in order ensure good results when attempting such processes alongside maintaining good safety approaches throughout entire duration present during entire work cycle.
For more insights, see: Underwater Welding
Can you braze cast iron?
Braze-cast iron is a unique way of joining two different metals, such as cast iron, together using an alloy of two other metals and heat. The process is often used for maintenance purposes instead of traditional welding, as the temperatures needed to join the two base metals don’t need to be as extreme. Braze-cast iron is especially effective when working with large or delicate pieces that can’t withstand traditional welding techniques.
The process starts with preparing the pieces to be joined by cleaning them thoroughly, removing any rust and dirt that could weaken the weld. Next, a cast iron alloy such as nickel-bronze or copper-silicon must be applied to both pieces in an even layer over the areas you wish to join together. Heat is then used throughout the area; this keeps melting away any rust or dirt particles that were left behind resulting in an incredibly strong joint. Eventually, once enough heat has been applied and the alloy has been pushed evenly between both pieces, the bond will become solidified and ready for use.
Braze-cast iron is a great tool for professionals who are looking to repair damaged wrought or cast iron pieces quickly while creating joints that won’t break down easily in the future. It offers a great way to combine materials without having to put too much pressure on them while still ensuring they remain securely bonded together. Cleaning up after use is also much easier than traditional welding due to its low temperature constraints. For those who are looking for an efficient and cost-effective way of joining two metals together, braze-cast iron might just be ideal solution!
See what others are reading: Can You Use Bleach on Your Areola?
Is it possible to weld stainless steel to cast iron?
Welding stainless steel to cast iron may sound like an impossible task, but depending on the application it is not only possible but can also be quite common.
The first step of this process is identifying the type of stainless and cast iron you will be working with. In some cases, different types of stainless steel or cast iron may be incompatible for welding. The key factor here is making sure the base metal of both materials has similar or equal amounts of nickel. Another key factor when considering these metals for welding is their designating tensile strength, as different levels can cause blending difficulties. Therefore, both base metals must have a similar tensile strength as well.
Once you have identified and verified that the two metals are compatible it is now time to move into cleaning up the edges and prepping them for welding. Using a power grinder may help smooth out any jagged surfaces that could create mismatching parts during welding, while wire brush cleaning can help remove any slag or other residue that would make creating a good weld even more difficult.
Finally, stainless steel to cast iron welding can be properly carried out using either stick, MIG or TIG methods. Of course, this will greatly depend on your skillset as well as your access to the correct tools for the job. For example, a professional welder who knows how to utilize all three methods might use stick welding for larger projects such as utility pipelines while smaller parts could possibly be welded together with a MIG welder. It all depends on your level of expertise and comfort when it comes time to choose what method you decide on.
To summarize: yes it is possible to weld stainless steel to cast iron when certain measures are taken into consideration such as matching nickel content and tensile strength in both base metals as well as having access to proper tools such as grinders and wire brushes needed prior to welding together with either stick, MIG or TIG methods.
Expand your knowledge: Primary Safeguarding Methods
Can you stick weld cast iron?
It is possible to stick weld cast iron and many find it to be a reliable and cost-effective technique. Stick welding cast iron requires more patience than regular steel, because of its maximum temperature that requires precise timing and control in order to prevent excessive heat input. It can also often require several passes.
For stick welding cast iron, it is best to use an E6011 or E6013 electrode as well as a TIG welder with a low amperage setting. The reason for this is because higher amperages will overwhelm the arc, leading to casting pitting. The edge of the cast iron should also be ground down so that it is flush before welding in order to prevent any gaps or cavities which may cause issues during the welding process. Additionally, using a neutral or slightly basic flux will help ensure better fusion and more effective welds with less spatter.
The best way to achieve optimal results with stick welding cast iron is by practicing on scrap pieces first until you are confident with the technique. As with most things in life, learning new techniques with patience will pay off in terms of successful results so don't give up if you don't get it right immediately!
A fresh viewpoint: What Are the Best Places to Elope in California?
Is it possible to TIG weld cast iron?
Yes, it is possible to TIG weld cast iron! TIG welding is a highly-specialized form of welding that can be used on a variety of different metals and materials, including steel and cast iron. While it is possible to weld both these materials together, different techniques are required for each, making the cast iron welding job a bit more difficult.
Cast iron is known for its especially brittle nature compared to other metals, so special attention must be taken in order to weld it successfully. TIG welding involves the use of a tungsten electrode which produces an electrical arc that melts the pieces of metal being joined together. Since cast iron can easily crack or become unsightly due to heat affected zones, special technique must be employed when working with it. This includes using appropriate filler rods made specifically for use with cast iron and proper preheating steps just before welding begins. Working slowly and in small batches can also help reduce distortion and imperfections in the final weldment.
The key benefit of TIG welding on cast iron is the ability to produce incredibly strong, uniform and reliable joints without excessive usage time or material costs. Moreover, since this process operates without any type of fluxes or shielding gases like other common welding processes require, there’s no additional cost associated with them either! With all this being mentioned, requiring more knowledge and skillfulness than ordinary stick or MIG process, TIG method indeed require special handling when dealing with cast iron components in order to get a flawless fusion quality at the end.
For more insights, see: Building Materials
Is it feasible to oxy-acetylene weld cast iron?
Yes, it is entirely possible to oxy-acetylene weld cast iron with the right skills, knowledge, and equipment. This form of welding is big business in industries such as plumbing and vehicle restoration; both adding value to the item being worked on and creating a cost effective solution when having to repair an otherwise expensive part.
Oxy-acetylene welding is one of the easiest forms of welding to learn, although it’s often viewed as a more dangerous technique due to the use of gases needed for the process. Welders must exercise caution and utilize all necessary safety protocols while using ignition equipment. Before any welding takes place on cast iron material, the surface must be inspected for cracks or weak spots which require patching or filling prior to welding. This is where oxy-acetylene welding comes into play; it’s a process that does not require additional materials like rod electrodes or electrode holders, making this form of welding ideal for working with already established pieces or large surfaces that need another level of protection rather than repair.
For cast iron in particular, this form of welding can provide an excellent long-lasting solution; practice makes perfect and consistency is key but with experience a well trained welder can produce results that rival most commercial products available for purchase at much higher costs. The key benefit lies in being able to customize existing pieces through joining two surfaces together without disassembling or replacing entire sections.
Explore further: What Is Friction?
Is laser welding a viable option for cast iron?
Laser welding has taken over many traditional welding methods in recent years, and one of the most popular questions in welding industries regards the use of laser welding for cast iron parts. Although it may seem unlikely, laser welding is indeed a viable option for this notoriously difficult material.
The reasons why laser welding is a good choice for cast iron are varied. For starters, due to its heightened energy concentration and increased controllability, laser welding can give you greater accuracy when compared to traditional welding methods. It also reduces oxidation and decarburization on the edges at a much faster rate than other techniques, meaning that heat-affected zones (HAZ) are kept to an absolute minimum. Additionally, because of how quickly and precisely a laser works, highly large parts can be joined without additional tools or clamps; and small intricate welds are just as easy to produce.
More and more manufacturers are turning to laser welding for cast iron components due to the improved strength it provides over traditional methods. Furthermore, because of its quick delivery time, parts can be ready for use in a much shorter time than before with no cracks or stress fractures present. With that said, it is important to keep in mind that this technique still requires proper operator knowledge and experience when dealing with cast iron - but performed correctly it is an incredibly useful option!
Consider reading: Welding Rod Oven
Sources
- https://www.twi-global.com/technical-knowledge/faqs/can-you-weld-cast-iron
- https://forums.iboats.com/threads/can-mapp-gas-braze-weld-cast-iron.9917/
- https://www.weldingandwelder.com/category/welding-equipment/oxy-acetylene-cutting-welding/oxy-acetylene-welding-rods/oxy-acetylene-welding-rods-cast-iron/
- https://waterwelders.com/can-you-mig-weld-cast-iron/
- https://thetigwelder.com/tig-welding-cast-iron-challenges-and-solutions/
- https://weldingpros.net/brazing-cast-iron/
- https://weldingpros.net/how-to-tig-weld-cast-iron/
- https://finemetalworking.com/welding-cast-iron
- https://www.weldpundit.com/tig-weld-cast-iron/
- https://welderslab.com/can-you-weld-cast-iron
- https://www.twi-global.com/technical-knowledge/job-knowledge/weldability-of-materials-cast-irons-025
- https://www.weldpundit.com/stick-welding-rod-aws-classification-guide/
Featured Images: pexels.com