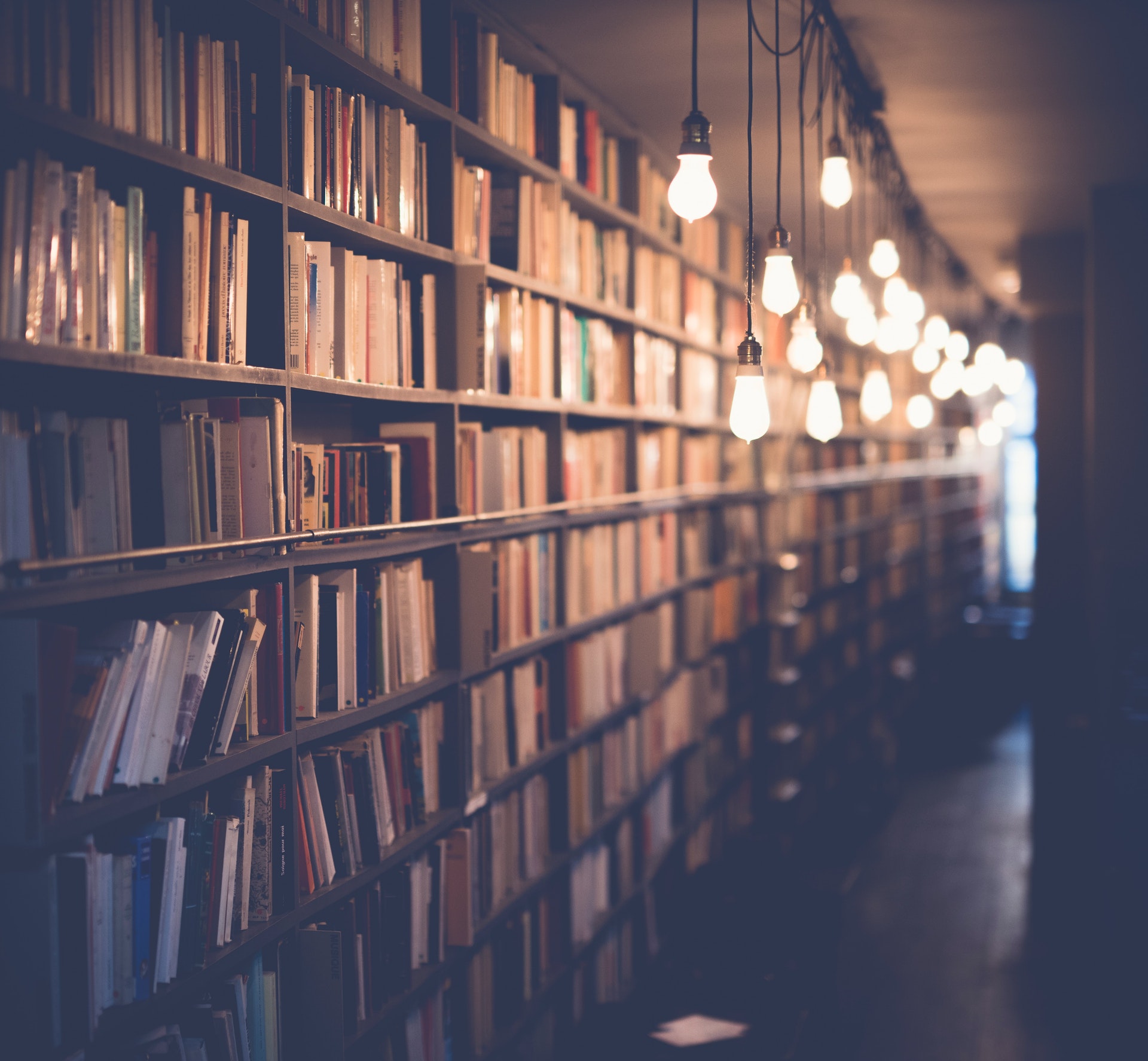
Delrin can be injection molded provided the proper equipment and conditions are used. The material is sensitive to moisture, so proper drying is essential. The melt temperature must be closely monitored, as Delrin has a narrow processing window. Injection pressure and speed must be carefully controlled to avoid sink marks and other defects.
Delrin is a versatile engineering thermoplastic used in a variety of applications requiring high strength and stiffness, good dimensional stability, and low friction. It is an ideal material for injection molding and is well suited for use in high precision applications. With proper care, injection molded Delrin parts can be highly accurate with smooth surface finishes.
The material is frequently used in the aerospace, automotive, and electrical industries. Injection molded Delrin has replacedmetal parts in many applications due to its superior strength and stiffness, light weight, and good fatigue resistance. The material is also used in a variety of consumer applications such as toys, sporting goods, and plumbing fixtures.
Delrin is a polyoxymethylene (POM) homopolymer resin. It is synthesized by ring-opening polymerization of the monomer propylene oxide. The resulting polymer has a wide range of properties that can be optimized by varying the molecular weight and degree of crystallinity.
The physical properties of injection molded Delrin are dependent on a number of factors including the molecular weight, degree of crystallinity, and additives used. In general, the material has high stiffness, good dimensional stability, and low friction. It is also resistant to a variety of chemicals and has a low moisture absorption rate.
The material can be molded into a variety of shapes and sizes. Injection molding is the most common method used to fabricate Delrin parts. The material can also be machined, blanked, or hot formed.
Injection molding is a manufacturing process for producing parts by injecting molten material into a mold. Delrin is well suited for injection molding and can be molded into complex shapes with high accuracy. The material has a relatively low melting temperature and can be injection molded at temperatures as low as 140°C (284°F).
The material must be properly dried prior to injection molding to prevent moisture related defects. Delrin is sensitive to moisture and must be dried to a moisture content of 0.04% or less. Proper drying can be accomplished using a desiccant dryer or oven.
The
Check this out: B12 Injection
What is delrin?
Delrin is an engineering thermoplastic used in precision parts requiring high stiffness, low friction, and excellent dimensional stability. As a semi-crystalline material, it also has good creep resistance. It can be used in machining processes similar to those used for metals, and it can be molded, extruded, or machined to produce intricate parts with very tight tolerances.
What are the challenges of injection molding delrin?
There are several challenges associated with injection molding Delrin. One challenge is that Delrin is a semi-crystalline material, meaning it has both crystalline and amorphous regions. The crystalline regions are less dense and more strong, while the amorphous regions are more dense and tougher. This makes injection molding Delrin somewhat more difficult than other materials because the resulting part will have different properties depending on the orientation of the crystalline regions. Additionally, Delrin has a relatively low melting temperature, so care must be taken to not overheat the material during the injection molding process. Finally, Delrin is an acetal resin, meaning it is susceptible to hydrolysis (degradation in the presence of water). Therefore, it is important to use appropriate drying conditions and resin storage practices to prevent degradation of the material.
You might enjoy: Cortisone Injection
What are the best practices for injection molding delrin?
Delrin is an acetal resin, a polyoxymethylene polymer, commonly abbreviated POM. It is also manufactured under the tradenames DuPontdelrin, Kepital and Celcon. Delrin is characterized by its high strength, stiffness, and resistance to moisture, wear, and chemicals. It is used in gears, bearings, bushings, valve seats, electric motors, light bulb bases, and many other applications requiring high levels of strength, toughness, and dimensional stability.
Best practices for injection molding delrin include:
1. Using a high quality delrin resin that meets or exceeds the specifications for your application.
2. Carefully controlling the injection molding parameters to ensure proper filling and consolidation of the delrin resin.
3. Using a well-designed and constructed injection mold that is properly cooled to avoid warping or deformation of the finished part.
4. Inspecting the finished parts for defects and ensuring that they meet all dimensional and cosmetic requirements.
5. Storing the finished parts in a controlled environment to prevent moisture absorption or other damage.
You might enjoy: Buy Lidocaine Injection
Frequently Asked Questions
What is Delrin made of?
Delrin is a polymer made from acetal, a synthetic thermoplastic that resists injection molding and heaturlization.
Why is Delrin so popular?
Among all the thermoplastic materials, Delrin is considered to be one of the most versatile and widely used due to its many qualities. These include its excellent strength, toughness and creep resistance as well as its reliability in fabrication.
What is the difference between delrin and acetal?
Delrin is a popular name for acetal homopolymer. Acetal is a more commonly known name for the PolyOxyMethylene (POM) family of thermoplastics. Acetal is available in two forms – homopolymer and copolymer.
What is the difference between the different grades of Delrin?
The different grades of Delrin offer a finer-tuned viscosity range over the standard toughened grades (Delrin® 100ST, 100T, and 500T). The availability of the Delrin® 300TE gives users even more flexibility when choosing a grade for a particular application.
What is Delrin (pom) plastic?
Delrin is a brand name for Dupont’s acetal polymer. It has two distinguishing factors when compared to other acetal plastics: Delrin is resistant to environmental acids, which means it can be used in harsh environments, and it maintains its shape under stress, making it ideal for applications where tamper-evident or impact-resistant characteristics are required.
Sources
- https://www.dupont.com/content/dam/dupont/amer/us/en/mobility/public/documents/en/Delrin%20Molding%20Guide.pdf
- https://www.comicsanscancer.com/can-you-injection-mold-delrin/
- https://www.protolabs.com/resources/blog/delrin-offers-strong-versatile-plastic-alternative-to-metal/
- https://globalizethis.org/can-you-injection-mold-delrin/
- https://www.hubs.com/knowledge-base/what-is-delrin/
- https://www.rapiddirect.com/blog/acetal-vs-delrin-what-are-their-differences/
- https://www.dupont.com/knowledge/grades-of-delrin.html
- https://www.youtube.com/watch
- https://www.xcentricmold.com/what-is-delrin/
- https://www.jwinjectionmold.com/what-are-the-benefits-of-injection-molding/
- https://www.xometry.com/resources/materials/acetal-vs-delrin/
- https://www.hubs.com/knowledge-base/injection-molding-applications-and-benefits/
- http://www.delrinproperties.com/
- https://globalizethis.org/can-delrin-be-injection-molded/
- http://www.complast.com/delrin/DelrinData.pdf
Featured Images: pexels.com