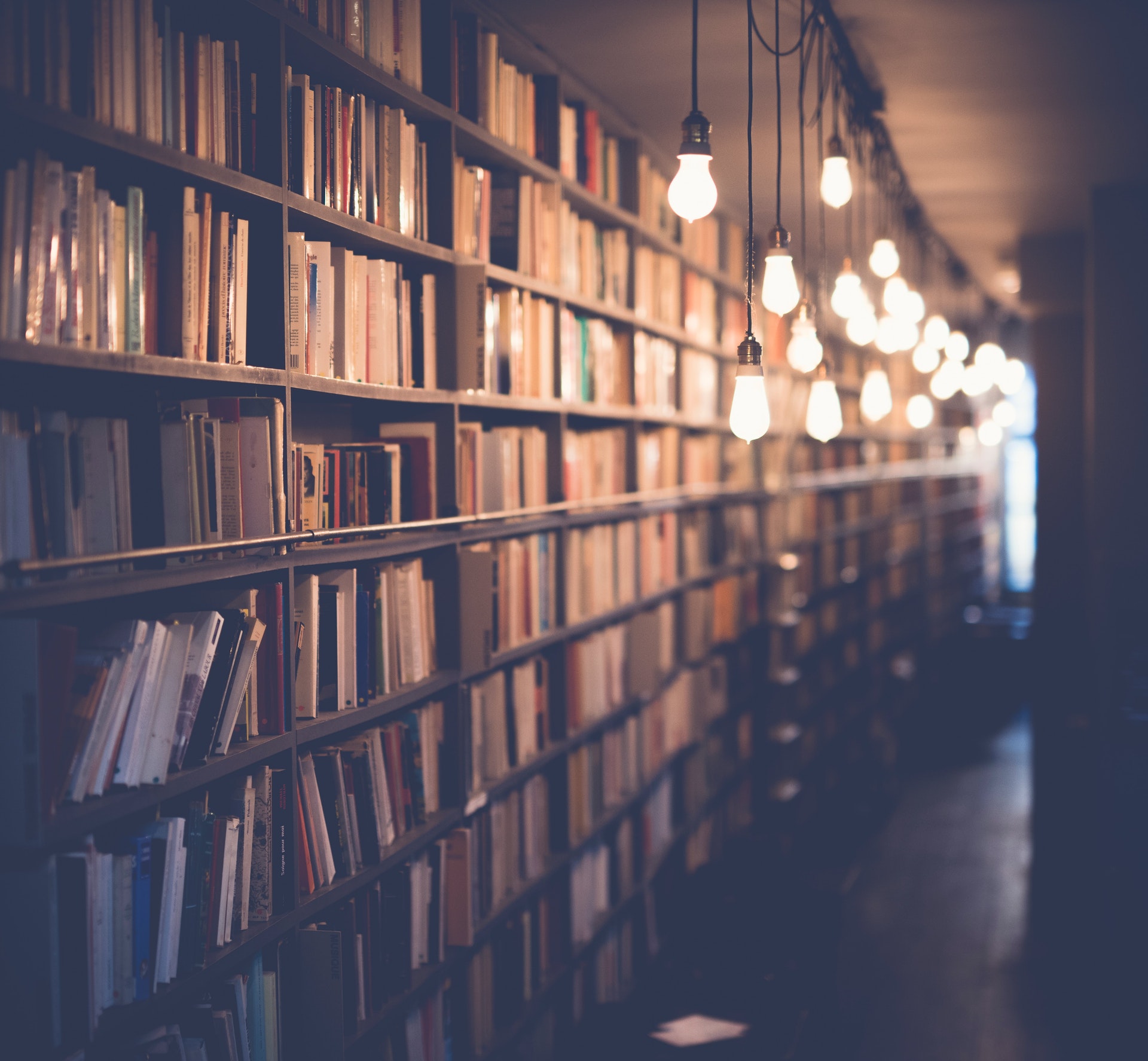
A bus cable connector is a type of electrical connector that is used to connect two or more cables together. It is also used to connect a cable to a device, such as a computer or a television. There are many different types of bus cable connectors, and they are available in a variety of different sizes and shapes. The most common type of bus cable connector is the pin header, which is a row of small metal pins that are used to connect the cables. Other types of bus cable connectors include the D-subminiature, the F-connector, and the mini-coaxial connector.
Additional reading: Can You Use Bleach on Your Areola?
What is a can bus cable connector?
A CAN bus is a type of computer network used in automobiles. It allows different electronic devices to communicate with each other, such as a car's engine control unit, brake system, and transmission. A CAN bus uses a standardised communication protocol, so different types of devices can work together. Each device has a controller area network (CAN) controller which manages the data flow on the bus.
A CAN bus connector is a type of connector used to connect two devices together on a CAN bus. There are various types of CAN bus connectors, but they all have two main parts: a male connector and a female connector. The male connector has a pin which is inserted into the female connector. The female connector has a socket which the pin sits in. Depending on the type of connector, there may be different numbers of pins and/or sockets.
The most common type of CAN bus connector is the D-subminiature connector. This type of connector has 9 pins in the male connector and 9 sockets in the female connector. The D-subminiature connector is typically used for low-speed CAN buses, such as those found in automobiles.
High-speed CAN buses use a different type of connector, such as the, which has fewer pins and sockets. The fewer pins and sockets allow for a higher data transfer rate.
Worth a look: What Is Friction?
What are the benefits of using a can bus cable connector?
The Controller Area Network (CAN bus) was developed in the 1980s by Robert Bosch GmbH. The CAN bus is a high-speed, twisted-pair data link that connects electronic control units (ECUs) in vehicles. ECUs are the electronic brains of vehicles that control functions such as engine management, transmission, traction control, and brakes. The CAN bus allows ECUs to communicate with each other without the need for a central computer.
The main benefits of using a CAN bus are:
1. reduced wiring harness complexity and weight 2. reduced installation time and cost 3. increased reliability 4. increased diagnostic capability
The reduced wiring harness complexity and weight is a major advantage of using a CAN bus. In a conventional vehicle with a central computer, each ECU is connected to the computer via a separate wiring harness. This can result in a large and heavy wiring harness. By using a CAN bus, the number of wires is reduced because all ECUs share a common data link. This can lead to a lighter and more compact wiring harness.
The reduced installation time and cost is another important benefit of using a CAN bus. In a vehicle with a central computer, the ECUs must be individually connected to the computer via their wiring harnesses. This can be a time-consuming and expensive process. By using a CAN bus, the ECUs can be connected together using a single cable, which can save both time and money.
The increased reliability is another benefit of using a CAN bus. When all ECUs are connected together using a single data link, there are fewer opportunities for wiring errors. This can lead to fewer vehicle breakdowns and increased customer satisfaction.
The increased diagnostic capability is the final benefit of using a CAN bus. When all ECUs are connected together, it is easier to diagnose problems because all data is available on the same data link. This can lead to faster repairs and reduced downtime.
For another approach, see: X3 4 Point Harness
What are the features of a can bus cable connector?
A can bus connector is a connector used to connect two or more can bus cables. Can bus connectors are used in a variety of applications, including automotive, industrial, and military. Can bus connectors can be used to connect can bus cables to each other, to an electronic device, or to a computer. Can bus connectors can be either male or female.
Can bus connectors are used in automotive applications to connect can bus cables to each other or to an electronic device. Can bus connectors are used in industrial applications to connect can bus cables to each other, to an electronic device, or to a computer. Can bus connectors can be used in military applications to connect can bus cables to each other, to an electronic device, or to a computer.
Can bus connectors can be either male or female. Male can bus connectors have a pin that mates with a socket on a female can bus connector. Female can bus connectors have a socket that mates with a pin on a male can bus connector. Can bus connectors can be either right-angle or straight.
Can bus connectors can be made from a variety of materials, including plastic, metal, and glass. The material used to make a can bus connector can affect the price, the durability, and the electrical properties of the connector. Can bus connectors can be made from a variety of metal alloys, including brass, bronze, and stainless steel.
Can bus connectors can be either solderless or soldered. Solderless can bus connectors have a metal spring that contacts the can bus cable to make the connection. Soldered can bus connectors have a solder joint that permanently connects the can bus connector to the can bus cable.
Can bus connectors can be either shielded or unshielded. Shielded can bus connectors have a metal shell that protects the connector from electromagnetic interference. Unshielded can bus connectors do not have a metal shell and are less resistant to electromagnetic interference.
Can bus connectors can be either waterproof or non-waterproof. Waterproof can bus connectors have a seal that prevents moisture from entering the connector. Non-waterproof can bus connectors do not have a seal and are not designed to be used in wet environments.
Can bus connectors can be eitherstraight or right-angle. Straight can bus connectors are designed to be used in applications where the can bus cable is running in a straight line. Right-angle can bus connectors are designed to be used in applications where the can
Suggestion: Automotive Aftermarket
What are the applications of a can bus cable connector?
The CAN bus is a flexible, scalable controller area network bus standard that was originally designed for the automotive industry. It has since been adopted by aerospace, industrial, and commercial applications. The CAN bus is available in a variety of configurations and can be customized to meet the specific needs of any application.
The most common applications for the CAN bus are in automotive systems, where the bus is used to connect the various electronic control units (ECUs) in a vehicle. The CAN bus can also be used in other types of transportation systems, such as buses, trains, and aircraft. In addition, the CAN bus is finding applications in industrial control systems and building automation systems.
One of the key advantages of the CAN bus is its flexibility. The bus can be configured to support a wide range of data rates, from a few kilobits per second to several megabits per second. This makes it possible to tailor the bus to the specific needs of each application.
The CAN bus is also scalable, meaning that it can be expanded to support more nodes or devices as needed. This makes it possible to use the bus in a wide range of applications, from small, stand-alone systems to large, complex networks.
The CAN bus is also well suited for applications that require high levels of reliability. The bus uses a robust data link layer that includes error detection and correction features. This helps to ensure that data is transmitted accurately and reliably between nodes on the bus.
In summary, the CAN bus is a flexible, scalable, and reliable bus standard that is well suited for a wide range of applications.
Worth a look: When Possible Pedestrians Should Walk?
What are the disadvantages of a can bus cable connector?
While the can bus cable connector is a very popular type of connector, it does have some disadvantages. One of the biggest disadvantages is that it is not very durable. This means that if you are using it in an application where it will be subject to a lot of wear and tear, it is likely that it will eventually break down. Additionally, it is not very flexible, so if you need to route it through a tight space, it may be difficult to do so. Additionally, the can bus cable connector is not very friendly to wireless signals, so if you are using it in an application where wireless communication is important, it is likely that you will experience interference.
Consider reading: What Are the Best Places to Elope in California?
What are the specifications of a can bus cable connector?
The Controller Area Network (CAN) bus is a two-wire, half-duplex, serial bus originally developed for the automotive industry by Robert Bosch GmbH. It is now used in many applications including industrial machinery, embedded systems, and consumer electronics. The CAN bus was designed to allow microcontrollers and devices to communicate with each other without the need for a host computer. Devices that are connected to the CAN bus are called nodes. A node can be a microcontroller, an input/output (I/O) device, or a sensor. The CANbus is a balanced (differential) 2-wire interface running over twisted pair (TP) cable. The bus uses a shielded twisted pair (STP), shielded CAT5, or optical fiber cable. The bus is terminated at each end with a 120Ω resistor.
The original CAN specification, ISO 11898-1, was released in 1993. It specified a maximum data rate of 1Mbps and a 7-bit identifier. An extended data frame format was added in 1995, which increased the maximum data rate to 8Mbps and allowed for a 8-byte payload. In 2003, the CAN bus was redesigned to support a media access control (MAC) layer. The new CAN FD specification, ISO 11898-2, was released in 2015. It increased the maximum data rate to 12Mbps and allowed for a 64-byte payload.
The CAN bus uses two wires, a CAN high and a CAN low. The CAN high wire is the dominant wire and the CAN low wire is the recessive wire. A node is only allowed to transmit when the bus is in an idle state. When a node wants to transmit, it first checks if the bus is idle. If the bus is idle, the node will assert the dominant state on the bus and wait for a certain amount of time. If no other node asserts the dominant state within that time, the first node can transmit its data. If another node does assert the dominant state, the first node must wait until the bus is idle again before it can transmit.
The data frame format consists of a start bit, a number of identifier bits, a number of data bits, and a CRC field. The start bit is always a dominant bit. The identifier field is used to identify the transmitting node and the receiving node. The data field is used to carry the data. The CRC field is used to error-check the data
For more insights, see: Display Ad Format Adjusts
What are the dimensions of a can bus cable connector?
The Controller Area Network (CAN) bus is a two-wire, half-duplex, asynchronous, serial bus originally developed for automotive applications. It has subsequently been made mandatory on all new passenger cars sold in the European Union (from 1 January 1998), and is now increasingly used in other embedded control systems. The CAN bus is a message-based protocol, designed specifically for automotive applications but now also used in other areas such as industrial automation and medical equipment.
The key feature of a CAN bus is its ability to send and receive messages on a network without a central controller. This means that each node on the network can act as both a transmitter and receiver of messages. This enables the network to be scalable and to support a large number of nodes. The CAN bus was originally designed for use in vehicles, where a large number of sensors and actuators are required to be connected together. The flexibility of the CAN bus means that it is now also used in a wide range of other applications including building automation, white goods, factory automation, and medical equipment.
The CAN bus is a broadcast medium, meaning that all nodes on the network receive every message that is sent. Each node can then decide whether or not to take any action in response to the message. This allows for a high level of flexibility, as each node can be programmed to respond in the most appropriate way to the messages it receives.
TheCAN bus uses a shielded twisted pair of wires for the data connection. Theshielding helps to protect the data from interference, while the twistedpair helps to reduce the effects of electromagnetic interference (EMI). Thedata is transmitted using differential signalling, where the voltage onone wire is compared to the voltage on the other wire. This allows thesignal to be transmitted over long distances with low levels ofnoise and interference.
The CAN bus uses a standardised connector for the data connection. This is typically a 9-pin or 15-pin D-sub connector. The pinout of the connector is standardised, so that any node can be connected to any other node on the network.
The message format of the CAN bus is based on the ISO 11898 standard. This defines the frame structure, bit timing, and electrical interface of the CAN bus. The message format consists of a start bit, an arbitration field, a control field, a data field, and a CRC field. The arbitration field is used to determine which node has
Related reading: Devices Connected
What is the weight of a can bus cable connector?
Assuming you are asking about the weight of a specific can bus cable connector, the answer may vary depending on the particular model. For example, the weight of a DIN 41612 Cables Crossover Plug with solder contacts is 12.4 grams.
What is the maximum voltage of a can bus cable connector?
A can bus is a message-based protocol used for networking electronic control units (ECUs) in automobiles. The need for a can bus arose out of the limitations of the existing automotive data bus systems at the time, which were designed for point-to-point communication and could not handle the increased number of ECUs being used in modern vehicles. The can bus was designed to be a versatile, scalable, and fault-tolerant network that could accommodate the ever-increasing amount of electronics in vehicles.
The can bus uses a twisted pair of wires for the data signal and a separate wire for the ground. The data signal is differential, meaning that there is a separate wire for the positive and negative sides of the signal. The can bus uses a voltage of 12V, with a maximum voltage of 7V. The can bus connector has two pins, one for the data signal and one for the ground.
The can bus is used in a variety of automotive applications, including engine control, transmission control, ABS braking, and airbag deployment. The can bus is also used in non-automotive applications, such as industrial control and avionics.
Related reading: Job Applications
Frequently Asked Questions
What type of CAN bus cable do I Need?
The simplest wiring is for pins 2 and 7 on the DB9 connectors to connect straight through. However, depending on your device, you may need a different type of CAN bus cable. For devices following the CANopen specification, the basic CAN bus cable is a length of single twisted pair cable with DB9 sockets (the female 9-pin D-sub connectors with the holes):
How do I connect to the CAN bus?
To connect to the CAN bus, use a 9-pin D-Sub Insulation Displacement Connector (IDC) fitted with a ribbon cable.
What is the CAN bus in networking?
The CAN bus is an interfacing standard used in many networking applications. CAN regulates communications between devices within a network by handling message transmission, detection of errors, and retransmission of lost packets.
What is a 9-pin D-sub CAN bus cable?
A 9-pin D-sub CAN bus cable is a length of single twisted pair cable with DB9 sockets (the female 9-pin D-sub connectors with the holes).
What is the physical layer of the CAN bus?
The physical layer of the CAN bus is responsible for transmitting and receiving electrical signals over a two wire bus.
Sources
- https://www.buenoptic.net/encyclopedia/item/537-maximum-cable-length-for-a-can-bus.html
- https://www.polytechnichub.com/applications-controller-area-network-can-bus/
- https://www.etas.com/fr/produits/cables_connectors_can_connection.php
- https://www.belden.com/products/cable/fieldbus-cable/can-bus-cable
- https://www.sab-cable.eu/cables-confection-technique-de-thermometrie/cables/cables-bus/cables-can-bus.html
- https://quizlet.com/516312645/connector-quiz-flash-cards/
- https://www.kvaser.com/about-can/the-can-protocol/can-connectors/
- http://www.zimo.at/web2010/products/can_EN.htm
- https://info.waytekwire.com/blog/what-to-look-for-in-can-bus-cables-and-connectors
- https://www.polytechnichub.com/advantages-disadvantages-controller-area-network-can-bus/
- https://copperhilltech.com/blog/can-bus-and-sae-j1939-bus-voltage/
- https://www.etas.com/en/products/cables_connectors_can_connection.php
- https://www.se.com/ww/en/faqs/FA339840/
- https://www.fscables.com/products/can-bus-cable.html
Featured Images: pexels.com